Free Airline High Lift Truck Operator course (6months)
Airline High Lift Truck Operator:
Brief Job Description: Preparing vehicle for airside use, maneuver the vehicle airside, maintain procedures and practices which contribute to the safety of airside traffic and apron operations. Servicing of aircraft for arrival/departure in the given time frame along with the required responsibilities.
Personal Attributes: The individual should have basic communication ability and should be responsible in order to maintain procedures. He should have the ability to work for long hours and be cautious to avoid any accidents.
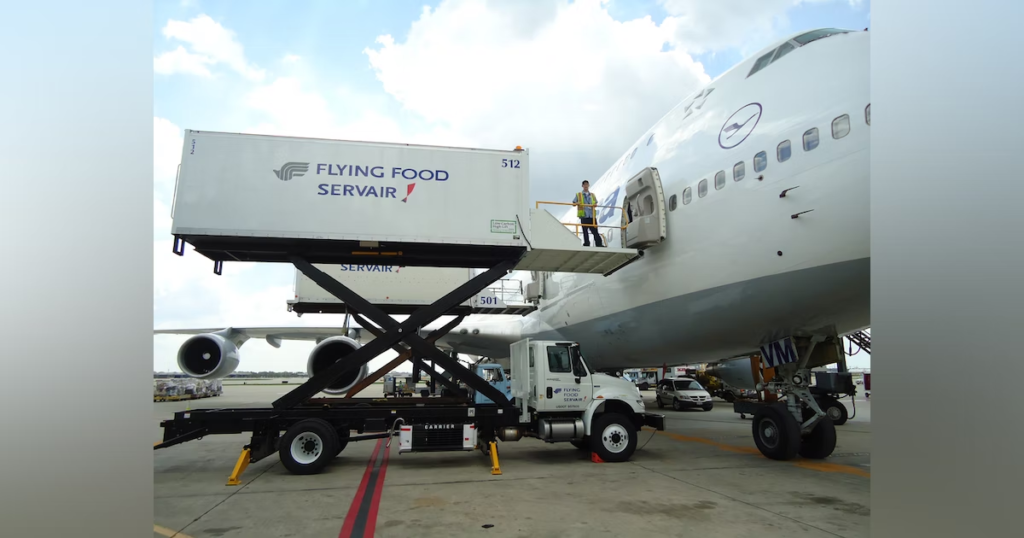
Safety and security procedures:-
Comprehending the safety and security procedures
PC1. comply with the organisation’s safety and security policies and procedures
PC2. comply with the regulatory guidelines on safe conduct of operations and maintenance of conditions to thwart any acts of unlawful interference
PC3. report any identified breaches of safety, and security policies and procedures to the designated person
PC4. coordinate with other resources at the workplace (within and outside the organisation) to achieve safe and secure environment
PC5. identify and mitigate any safety and security hazards like illness, accidents, fires or acts of unlawful interference if it falls within the limits of individual’s authority
PC6. report any hazards outside the individual’s authority to the relevant person in line with organisational procedures and regulatory guidelines
PC7. follow organisation’s emergency procedures for accidents, fires or acts of unlawful interference
PC8. identify and recommend opportunities for improving health, safety, and security to the designated person
PC9. ensure completion of all health and safety records are updated and procedures well defined
Knowledge and Understanding
Organisational Context
KA1. hazard identification and risk management as defined within the organisational policy and procedures
KA2. regulatory requirements and organisation’s procedures for maintenance of safety and security standards and individual’s role and responsibilities in relation to this
KA3. how and when to report hazards KA4. the limits of responsibility for dealing with hazards
KA5. the organisation’s emergency procedures for different emergency situations and the importance of following these
KA6. importance of maintaining high standards of safety and security kA7. implications that any non-compliance with safety and security may
have on individuals and the organisation
Technical Knowledge
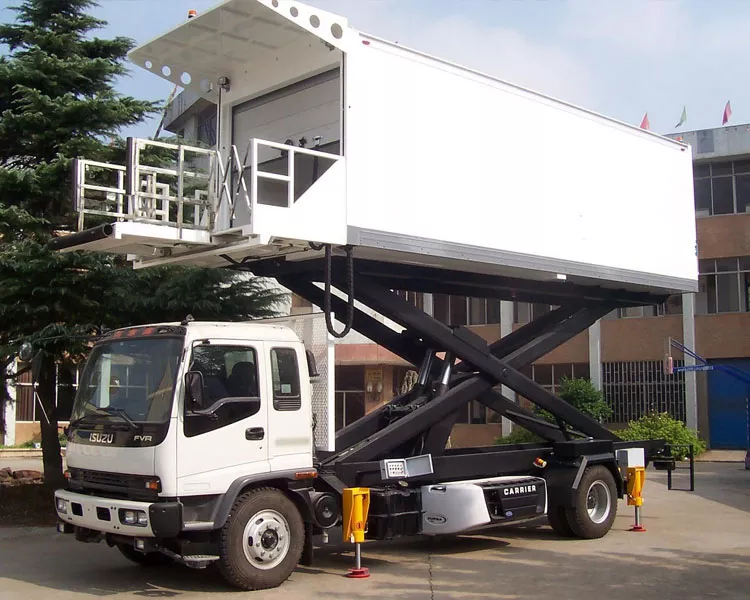
KB1. different types of breaches of safety and security and how and when to report these
KB2. evacuation procedures for workers and passengers
KB3. how to summon medical assistance and the emergency services, where necessary
KB4. how to use the health, safety and accident reporting procedures and the importance of these
KB5. regulatory guidelines on dealing with safety and security emergencies
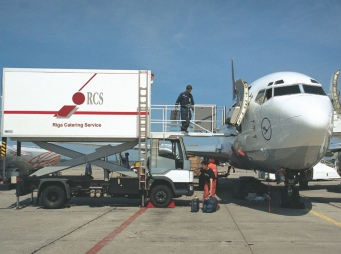
Core Skills/ Generic Skills
Writing Skills |
The user/individual on the job needs to know and understand how to: SA1. complete accurately a well written report in English language detailing the situations of emergency with attention to detail |
Reading Skills |
The user/individual on the job needs to know and understand how to: SA2. read instructions/guidelines/procedures/rules |
Oral Communication (Listening and Speaking skills) |
The user/individual on the job needs to know and understand how to: SA3. listen to and orally communicate information with all concerned |
Professional Skills
Decision Making |
The user/individual on the job needs to know and understand how to: SB1. make decisions on a suitable course of action or response if permitted by the authority matrix |
Plan and Organise |
The user/individual on the job needs to know and understand how to: SB2. monitor efficient functioning of all activities SB3. plan and organise work to achieve targets and deadlines |
Customer Centricity |
The user/individual on the job needs to know and understand how to: SB4. communicate with passengers and other stakeholders in a courteous manner SB5. maintain effective work relationship |
Problem Solving |
The user/individual on the job needs to know and understand how to: SB6. identify trends/common causes for errors and suggest possible solutions to the supervisor / management SB7. identify and correct errors |
Analytical Thinking |
The user/individual on the job needs to know and understand how to: SB8. analyse best possible solutions (cost, time, effort, etc.) suited for operations |
Critical Thinking |
The user/individual on the job needs to know and understand how to: SB9. concentrate on task at hand and complete it without errors SB10. apply balanced judgments to different situations Unloading an aircraft load: Approaching an aircraft PC1. understand the signs which indicate that it is safe to approach the aircraft PC2. identify the personal protective equipment (PPE) required to perform the function PC3. ensure that the equipment or personnel approach the aircraft from the right direction and as per the operational guidelines set forth by the organisation or regulators PC4. ensure that the equipment is parked at the designated location to perform its function PC5. ensure that the equipment is secured and no movement of equipment can take place which can damage the aircraft as per instructions from the supervisor Opening of cargo doors on the aircraft PC6. identify the location of the cargo door controls PC7. ensure that the equipment is in a safe configuration and shall not restrict or damage the cargo door in the process of its opening PC8. ensure that no external force is applied to the cargo doors in case of any fault in the process of cargo door opening PC9. ensure that the cargo door is opened only by individuals who are authorized as per organisational policy or by regulatory guidelines PC10. ensure that any visual defect observed on the cargo door is immediately escalated to appropriate personnel without any delay Initiate unloading of the aircraft load PC11. align the unloading equipment in line with the cargo door sill as per guidelines and instructions of the supervisor PC12. ensure that the load can be transferred under the supervision of the supervisor from the aircraft cargo compartment onto the equipment without any damage to cargo, equipment or aircraft. PC13. ensure that the unloading sequence is in line with the offloading instructions from the loading supervisor and as per organisation policies. PC14. ensure that the person is physically fit to enter into confined space and move or lift cargo in a sitting or kneeling position, if the space is not enough for the personnel to stand. PC15. ensure that during the process of moving the cargo in the cargo compartment there is no damage to the cargo or the aircraft. PC16. escalate to the appropriate personnel if any cargo is found damaged or in case of any issue observed which can impact the security or safety of aircraft. Knowledge and Understanding Organisational Context KA1. organisation safety policy and procedures, basic compliance to technical requirements and standards; safety and hazards, PPE KA2. organisation structure KA3. escalation procedure Technical knowledge KB1. types of aircraft and the location of cargo doors on the aircraft KB2. the opening mechanism of cargo doors on different types of aircraft KB3. the location reference or design of location numbers within the cargo compartment of different types of aircraft KB4. the operation of power drive unit KB5. self-evaluation of health concerns like back pain or injury KB6. basic first aid procedures KB7. airside safety regulations KB8. aviation security regulations Writing Skills The user/individual on the job needs to know and understand how to: SA1. write either in English or in the preferred local language events that took place on a flight if required due to any circumstances. Reading Skills The user/individual on the job needs to know and understand how to: SA2. read the details of any instructions SA3. read and understand the organisation policies & procedures Oral Communication (Listening and Speaking skills) The user/individual on the job needs to know and understand how to: SA4. communicate clearly with supervisors and peers SA5. regularly communicate with all employees in the chain of activities to ensure activities are running smoothly SA6. share best practices with peers and subordinates Professional Skills Decision Making The user/individual on the job needs to know and understand how to: SB1. make decisions on a suitable course of action or response if permitted by the authority matrix Plan and Organise The user/individual on the job needs to know and understand how to: SB2. monitor efficient functioning of all activities SB3. plan and organise work to achieve targets and deadlines Customer Centricity Not applicable Problem Solving The user/individual on the job needs to know and understand how to: SB4. identify trends/common causes for errors and suggest possible solutions to the supervisor / management SB5. identify and correct errors Analytical Thinking Not applicable Critical Thinking The user/individual on the job needs to know and understand how to: SB6. concentrate on task at hand and complete it without errors SB7. apply balanced judgments to different situations ![]() Loading an aircraft load Performance Criteria Approaching the aircraft PC1. understand the signs which indicate that it is safe to approach the aircraft PC2. ensure that the equipment or personnel are approaching the aircraft from the right direction and as per the operational guidelines set forth by the organisation or regulators PC3. identify the personal protective equipment (PPE) required to perform the function PC4. ensure that the equipment is parked at the designated location to perform its function PC5. ensure that the equipment is secured and no movement of equipment can take place which can damage the aircraft Opening of cargo doors on the aircraft PC6. identify the location of the cargo door controlsPC7. ensure that the equipment is in a safe configuration and shall not restrict or damage the cargo door in the process of its opening PC8. ensure that no external force is applied to the cargo doors in case of any fault in the process of cargo door opening PC9. ensure that the cargo door is opened only by individuals who are authorized as per organisation policy or by regulatory guidelines PC10. ensure that any visual defect observed on the cargo door is immediately escalated to appropriate personnel without any delay. Initiate loading of the aircraft load PC11. perform visual check of the aircraft compartment to ensure there is no unauthorized cargo or item left inside the cargo compartment. PC12. escalate any findings to the appropriate personnel immediately before commencing loading. PC13. align the loading equipment in line with the cargo door sill PC14. ensure that the load can be transferred from the equipment into the aircraft cargo compartment without any damage to cargo, equipment or aircraft. PC15. ensure that the loading sequence is in line with the instructions from the loading supervisor and organisation policies. PC16. ensure that the person is physically fit to enter into confined space and move or lift cargo in a sitting or kneeling position, if the space is not enough for the personnel to stand. PC17. ensure that during the process of moving the cargo in the cargo compartment there is no damage to the cargo or the aircraft. PC18. ensure that the cargo is secured in accordance to organisational procedures. PC19. escalate to the appropriate personnel if any cargo is found damaged or in case of any issue observed which can impact the security or safety of aircraft. Knowledge and Understanding Organisational Context KA1. organisation safety policy and procedures, basic compliance to technical requirements and standards; safety and hazards, PPE KA2. organisation structure KA3. escalation procedure Technical knowledge KB1. types of aircraft and the location of cargo doors on the aircraft KB2. the opening mechanism of cargo doors on different types of aircraft KB3. the location reference or design of location numbers within the cargo compartment of different types of aircraft KB4. the operation of power drive unit KB5. self-evaluation of health concerns like back pain or injury KB6. basic first aid procedures KB7. airside safety regulations KB8. aviation security regulations Core Skills/ Generic Skills Writing Skills The user/individual on the job needs to know and understand how to: SA1. write either in English or in the preferred local language events that took place on a flight if required due to any circumstances. Reading Skills The user/individual on the job needs to know and understand how to: SA2. read the details of any instructions SA3. read and understand the organisation policies & procedures Oral Communication (Listening and Speaking skills) The user/individual on the job needs to know and understand how to: SA4. communicate clearly with supervisors and peers SA5. regularly communicate with all employees in the chain of activities to ensure activities are running smoothly SA6. share best practices with peers and juniors Professional Skills Decision Making The user/individual on the job needs to know and understand how to: SB1. make decisions on a suitable course of action or response if permitted by the authority matrix Plan and Organise The user/individual on the job needs to know and understand how to: SB2. monitor efficient functioning of all activities SB3. plan and organise work to achieve targets and deadlines Customer Centricity Not applicable Problem Solving The user/individual on the job needs to know and understand how to: SB4. identify trends/common causes for errors and suggest possible solutions to the supervisor / management SB5. identify and correct errors Analytical Thinking Not applicable Critical Thinking The user/individual on the job needs to know and understand how to: SB6. concentrate on task at hand and complete it without errors SB7. apply balanced judgments to different situations ![]() Prestart inspection of equipment/ vehicle Performance Criteria Reviewing prestart inspection checklist PC1. identify the appropriate prestart inspection checklist for the respective equipment/vehicle PC2. perform the prestart inspection on the respective equipment/vehicle as per the checklist and the guidelines of the supervisor PC3. identify any defects on the equipment/vehicle and determine if the same can impact the operations of the equipment/vehicle Recording of inspection findings PC4. ensure that all the findings against the prestart inspection checklist are duly filled in the appropriate checklist forms PC5. record any additional defects found beyond the prestart inspection checklist in the appropriate form in relevant detail PC6. file the duly filled form in the manner as defined by the organisation or regulatory policies and procedures Knowledge and Understanding Organisational Context KA1. organisation safety policy and procedures; basic compliance to technical requirements and standards; safety and hazards KA2. organisation structure KA3. escalation procedure Technical knowledge KB1. types of equipment/vehicles in use KB2. basic knowledge of the various operating parts of an equipment/vehicle KB3. basic knowledge of the kinds of defects that can be observed on an equipment/vehicle KB4. airside safety regulations KB5. airside driving regulations KB6. aviation security regulations Core Skills/ Generic Skills Writing Skills The user/individual on the job needs to know and understand how to: SA1. write in English language the inspection findings and defects observed on the equipment / vehicle Reading Skills The user/individual on the job needs to know and understand how to: SA2. read the details of any instructions SA3. read and understand the organisation policy & procedures SA4. read the equipment/vehicle maintenance manual Oral Communication (Listening and Speaking skills) The user/individual on the job needs to know and understand how to: SA5. communicate clearly with supervisors and peers SA6. regularly communicate with all employees in the chain of activities to ensure efficient operations SA7. share best practices with peers and subordinates Professional Skills Decision Making The user/individual on the job needs to know and understand how to: SB1. make decisions on a suitable course of action or response if permitted by the authority matrix Plan and Organise The user/individual on the job needs to know and understand how to: SB2. monitor efficient functioning of all activities SB3. plan and organise work to achieve targets and deadlines Customer Centricity Not applicable Problem Solving The user/individual on the job needs to know and understand how to: SB4. identify trends/common causes for errors and suggest possible solutions to the supervisor / management SB5. identify and correct errors Analytical Thinking Not applicable Critical Thi nking The user/individual on the job needs to know and understand how to: SB6. concentrate on task at hand and complete it without errors SB7. apply balanced judgments to different situations Operate a vehicle airside Performance Criteria Prepare a vehicle for airside use PC1. make sure that airside driving authorization/license is appropriate and valid to the vehicle PC2. confirm that the vehicle is lit and marked according to airside driving requirements PC3. complete documents relating to using the vehicle in line with the organisation procedures Manoeuvre a vehicle airside PC4. manoeuvre the vehicle in a controlled manner in all conditions PC5. park the vehicle safely in appropriate areas in line with organisation procedures PC6. follow airside signage/markings PC7. give priority to moving aircraft at all times PC8. maintain a safe distance between the vehicle and aircraft at all times as defined by regulatory guidelines PC9. make sure that all doors and shutters (where relevant) are closed while driving the vehicle PC10. reverse the vehicle according to organisational and regulatory guidelines PC11. be constantly vigilant when driving Maintain procedures and practices which contribute to safety of airside traffic and PC12. wear appropriate Personal Protective Equipment (PPE) while driving PC13. secure vehicle loads in line with the organisation procedures PC14. carry an airside driving license in line with the organisation procedures and regulatory guidelines PC15. take appropriate remedial action when foreign object debris (FOD) or spillage is seen on the airfield/apron PC16. report dangerous or unsafe practices to appropriate authority PC17. get rid of all waste products in line with the organisation procedures and regulatory guidelines PC18. provide unhindered access for emergency services at all times Comply with airside accident, hazard and emergency procedures PC19. report all airside incidents, accidents and emergencies in line with organisation procedures and regulatory guidelines PC20. respond to airside incidents, accidents and emergencies in line with organisation procedures and regulatory guidelines Knowledge and Understanding Organisational Context KA1. organisation safety policy and procedures; basic compliance to technical requirements and standards; safety and hazards KA2. organisation structure KA3. escalation procedure Technical knowledge KB1. organisation and regulatory procedures as they may apply to airside operations KB2. airside safety instructions KB3. airside safety areas (roads, manoeuvring areas, stands) in relation to license categories KB4. airside signs and markings KB5. aircraft crossing points KB6. airport and stand layout KB7. speed limits KB8. airside parking regulations KB9. regulations concerning reversing KB10. low visibility notification and operating procedures KB11. the effect that poor weather conditions including snow and ice, high winds, rain/surface water, lightning and heat on driving airside Core Skills/ Generic Skills Writing Skills The user/ individual on the job needs to know and understand how to: SA1. complete documents related to use of vehicle Reading Skills The user/individual on the job needs to know and understand how to: SA2. interpret airport and stand layout SA3. read airside safety instructions SA4. read airside parking regulations Oral Communication (Listening and Speaking skills) The user/individual on the job needs to know and understand how to: SA5. communicate clearly with supervisors and peers SA6. regularly communicate with all employees in the chain of activities to ensure efficient operations SA7. share best practices with peers and subordinates Professional Skills Decision Making The user/individual on the job needs to know and understand how to: SB1. understand types of faults occurring and how to deal with it Plan and Organise The user/individual on the job needs to know and understand how to: SB2. monitor efficient functioning of all activities SB3. prioritize and execute tasks in within the scheduled time limits Customer Centricity Not applicable Problem Solving The user/individual on the job needs to know and understand how to: SB4. identi fy trends/common causes for errors and suggest possible solutions to the supervisor / management SB5. identify and correct errors Analytical Thinking The user/individual on the job needs to know and understand how to: SB6. take the most appropriate remedial action when hazards are identified on the airfield Critical Thinking The user/individual on the job needs to know and understand how to: SB7. concentrate on the task at hand and complete it without errors Post operations inspection of equipment/vehicle Performance Criteria Reviewing post operations inspection checklist To be competent, the user/individual on the job must be able to: PC1. identify appropriate post operations inspection checklist for the respective equipment /vehicle PC2. perform the post operations inspection on the respective equipment /vehicle as per the checklist PC3. identify any defects with the equipment/vehicle and determine if the same can impact the operations of the respective equipment/ vehicle Recording of inspection findings PC4. ensure that all the findings against the post operations inspection checklist are duly filled in the appropriate checklist forms PC5. record any additional defects found or caused during operations or in the appropriate form in relevant detail PC6. file the duly filled form in the manner as defined by the organisation or regulatory policies and procedures Knowledge and Understanding Organisational Context KA1. organisation safety policy and procedures; basic compliance to technical requirements and standards; safety and hazards KA2. organisation structure KA3. escalation procedure Technical knowledge KB1. types of equipment / vehicles in use KB2. basic knowledge of the various operating parts of an equipment / vehicle KB3. basic knowledge of the kinds of defects that can be observed on an equipment/vehicle KB4. airside safety regulations KB5. aviation security Core Skills/ Generic Skills Writing Skills The user/individual on the job needs to know and understand how to: SA1. write in English language the inspection findings and defects observed on the respective equipment / vehicle Reading Skills The user/individual on the job needs to know and understand how to: SA2. read the details of any instructions SA3. read and understand the organisation policies & procedures SA4. read the equipment maintenance manual Oral Communication (Listening and Speaking skills) The user/individual on the job needs to know and understand how to: SA5. communicate clearly with supervisors and peers SA6. regularly communicate with all employees in the chain of activities to ensure efficient operations SA7. share best practices with peers and subordinates Professional Skills Decision Making The user/individual on the job needs to know and understand how to: SB1. understand types of faults occurring and how to deal with it Plan and Organise The user/individual on the job needs to know and understand how to: SB2. monitor efficient f unctioning of all activities SB3. prioritise and execute tasks in within the scheduled time limits Customer Centricity Not applicable Problem Solving The user/individual on the job needs to know and understand how to: SB4. identify trends/common causes for errors and suggest possible solutions to the supervisor / management SB5. identify and correct errors Analytical Thinking The user/individual on the job needs to know and understand how to: SB6. take the most appropriate remedial action when hazards are identified on the airfield Critical Thinking The user/individual on the job needs to know and understand how to: SB7. concentrate on the task at hand and complete it without errors. Work Effectively in a Team: Performance Criteria Support the work team PC1. display courteous and helpful behaviour at all times. PC2. take opportunities to enhance the level of assistance offered to colleagues. PC3. meet all reasonable requests for assistance within acceptable workplace timeframes. PC4. complete allocated tasks as required. PC5. seek assistance when difficulties arise. PC6. use questioning techniques to clarify instructions or responsibilities. PC7. identify and display a non discriminatory attitude in all contacts with customers and other staff members. Maintain personal presentation PC8. observe appropriate dress code and presentation as required by the workplace, job role and level of customer contact. PC9. follow personal hygiene procedures according to organisational policy and relevant legislation. Develop effective work habits PC10. interpret, confirm and act on workplace information, instructions and procedures relevant to the particular task. PC11. interpret, confirm and act on legal requirements in regard to anti- discrimination, sexual harassment and bullying. PC12. ask questions to seek and clarify workplace information. PC13. plan and organise daily work routine within the scope of the job role. PC14. prioritise and complete tasks according to required timeframes. PC15. identify work and personal priorities and achieve a balance between competing priorities Knowledge and Understanding Organisational Context KA1. The policies and procedures relating to the job role. KA2. The value system of the organisation. KA3. Employee rights and obligations. KA4. The reporting hierarchy and escalation matrix. Technical Knowledge KB1. ask questions to identify and confirm requirements. KB2. follow routine instructions through clear and direct communication. KB3. use language and concepts appropriate to cultural differences. KB4. use and interpret non-verbal communication. KB5. the scope of information or materials required within the parameters of the job role. KB6. consequences of poor team participation on job outcomes. KB7. work health and safety requirements. Core Skills/ Generic Skills Writing Skills, On the job the individual needs to be able to: SA1. complete documentation accurately. SA2. write simple reports when required. Reading Skills On the job the individual needs to be able to: SA3. read information accurately. SA4. read and interpret data sheets. Oral Communication (Listening and Speaking skills) The user/individual on the job needs to know and understand how to: SA5. listen to and orally communicate information with all concerned Professional Skills Decision Making On the job the individual needs to be able to: SB1. make appropriate decisions regarding the responsibilities of the job role. Plan and Organise The user/individual on the job needs to know and understand how to: SB2. monitor efficient functioning of all activities SB3. plan and organise work to achieve targets and deadlines Customer Centricity The user/individual on the job needs to know and understand how to: SB4. communicate with passengers and other stakeholders in a courteous manner SB5. maintain effective work relationship Problem Solving The user/individual on the job needs to know and understand how to: SB6. identify trends/common causes for errors and suggest possible solutions to the supervisor / management SB7. identify and correct errors Analytical Thinking The user/individual on the job needs to know and understand how to: SB8. analyse best poss ible solutions (cost, time, effort, etc.) suited for operations Critical Thinking The user/individual on the job needs to know and understand how to: SB9. concentrate on task at hand and complete it without errors SB10. apply balanced judgments to different situations Model Curriculum Airline High Lift Truck Operator Follow safety and security procedures · comprehend the organisation’s safety and security policies and procedures comprehend the regulatory guidelines on safe conduct of operations and maintenance of conditions to thwart any acts of unlawful interference report any identified breaches of safety, and security policies and procedures to the designated person coordinate with other resources at the workplace (within and outside the organisation) to achieve safe and secure environment identify and mitigate any safety and security hazards like illness, accidents, fires or acts of unlawful interference if it falls within the limits of individual’s authority report any hazards outside the individual’s authority to the relevant person in line with organisational procedures and regulatory guidelines follow organisation’s emergency procedures for incidents or accidents, fires or acts of unlawful interference identify and recommend opportunities for improving health, safety, and security to the designated person ensure completion of all health and safety records are updates and procedures well defined Unloading of aircraft load · understand the signs which indicate that it is safe to approach the aircraft identify the personal protective equipment (PPE) required to perform the function ensure that the equipment or personnel approach the aircraft from the right direction and as per the operational guidelines set forth by the organisation or regulators ensure that the equipment is parked at the designated location to perform its function ensure that the equipment is secured and no movement of equipment can take place which can damage the aircraft identify the location of the cargo door controls · ensure that the equipment is in a safe configuration and shall not restrict or damage the cargo door in the process of its opening ensure that no external force is applied to the cargo doors in case of any fault in the process of cargo door opening ensure that the cargo door is opened only by individuals who are authorized as per organisational policy or by regulatory guidelines ensure that any visual defect observed on the cargo door is immediately escalated to appropriate personnel without any delay align the unloading equipment in line with the cargo door sill ensure that the load can be transferred from the aircraft cargo compartment onto the equipment without any damage to cargo, equipment or aircraft. ensure that the unloading sequence is in line with the offloading instructions from the loading supervisor and as per organisation policies. ensure that the person is physically fit to enter into confined space and move or lift cargo in a sitting or kneeling position, if the space is not enough for the personnel to stand. ensure that during the process of moving the cargo in the cargo compartment there is no damage to the cargo or the aircraft. escalate to the appropriate personnel if any cargo is found damaged or in case of any issue observed which can impact the security or safety of aircraft. Loading an aircraft load understand the signs which indicate that it is safe to approach the aircraft ensure that the equipment or personnel are approaching the aircraft from the right direction and as per the operational guidelines set forth by the organisation or regulators identify the personal protective equipment (PPE) required to perform the function ensure that the equipment is parked at the designated location to perform its function ensure that the equipment is secured and no movement of equipment can take place which can damage the aircraft identify the location of the cargo door controls ensure that the equipment is in a safe configuration and shall not restrict or damage the cargo door in the process of its opening ensure that no external force is applied to the cargo doors in case of any fault in the process of cargo door opening ensure that the cargo door is opened only by individuals who are authorized as per organisation policy or by regulatory guidelines ensure that any visual defect observed on the cargo door is immediately escalated to appropriate personnel without any delay perform visual check of the aircraft compartment to ensure there is no unauthorized cargo or item left inside the cargo compartment. escalate any findings to the appropriate personnel immediately before commencing loading. align the loading equipment in line with the cargo door sill ensure that the load can be transferred from the equipment into the aircraft cargo compartment without any damage to cargo, equipment or aircraft. ensure that the loading sequence is in line with the instructions from the loading supervisor and organisation policies. ensure that the person is physically fit to enter into confined space and move or lift cargo in a sitting or kneeling position, if the space is not enough for the personnel to stand. ensure that during the process of moving the cargo in the cargo compartment there is no damage to the cargo or the aircraft. ensure that the cargo is secured in accordance to organisational procedures. escalate to the appropriate personnel if any cargo is found damaged or in case of any issue observed which can impact the security or safety of aircraft. Prestart inspection of equipment/ vehicle · identify the appropriate prestart inspection checklist for the respective equipment/vehicle · perform the prestart inspection on the respective equipment/vehicle as per the checklist identify any defects on the equipment/vehicle and determine if the same can impact the operations of the equipment/vehicle ensure that all the findings against the prestart inspection checklist are duly filled in the appropriate checklist forms record any additional defects found beyond the prestart inspection checklist in the appropriate form in relevant detail file the duly filled form in the manner as defined by the organisation or regulatory policies and procedures Operating a vehicle airside · make sure that airside driving authorization/license is appropriate and valid to the vehicle confirm that the vehicle is lit and marked according to airside driving requirements complete documents relating to using the vehicle in line with the organisation procedures manoeuvre the vehicle in a controlled manner in all conditions park the vehicle safely in appropriate areas in line with organisation procedures follow airside signage/markings give priority to moving aircraft at all times maintain a safe distance between the vehicle and aircraft at all times as defined by regulatory guidelines make sure that all doors and shutters (where relevant) are closed while driving the vehicle reverse the vehicle according to organisational and regulatory guidelines be constantly vigilant when driving wear appropriate Personal Protective Equipment (PPE) while driving secure vehicle loads in line with the organisation procedures carry an airside driving license in line with the organisation procedures and regulatory guidelines take appropriate remedial action when foreign object debris (FOD) or spillage is seen on the airfield/apron report dangerous or unsafe practices to appropriate authority · get rid of all waste products in line with the organisation procedures and regulatory guidelines provide unhindered access for emergency services at all times report all airside incidents, accidents and emergencies in line with organisation procedures and regulatory guidelines respond to airside incidents, accidents and emergencies in line with organisation procedures and regulatory guidelines Post operations inspection of equipment / vehicle · identify appropriate post operations inspection checklist for the respective equipment /vehicle perform the post operations inspection on the respective equipment /vehicle as per the checklist identify any defects with the equipment/vehicle and determine if the same can impact the operations of the respective equipment/ vehicle ensure that all the findings against the post operations inspection checklist are duly filled in the appropriate checklist forms record any additional defects found or caused during operations or in the appropriate form in relevant detail file the duly filled form in the manner as defined by the organisation or regulatory policies and procedures Work Effectively in a Team · display courteous and helpful behaviour at all times. take opportunities to enhance the level of assistance offered to colleagues. meet all reasonable requests for assistance within acceptable workplace timeframes. complete allocated tasks as required. seek assistance when difficulties arise. use questioning techniques to clarify instructions or responsibilities. identify and display a non-discriminatory attitude in all contacts with customers and other staff members. follow appropriate dress code and presentation as required by the workplace, job role and level of customer contact. follow personal hygiene procedures according to organisational policy and relevant legislation. interpret, confirm and act on workplace information, instructions and procedures relevant to the particular task interpret, confirm and act on legal requirements in regard to antidiscrimination, sexual harassment and bullying. ask questions to seek and clarify workplace information. plan and organise daily work routine within the scope of the job role prioritise and complete tasks according to required timeframes identify work and personal priorities and achieve a balance between competing priorities Guidelines for Assessment 1. Criteria for assessment for each Qualification Pack will be created by the Sector Skill Council. Each Performance Criteria (PC) will be assigned marks proportional to its importance in NOS. SSC will also lay down proportion of marks for Theory and Skills Practical for each PC 2. The assessment for the theory part will be based on knowledge bank of questions created by the SSC 3. Individual assessment agencies will create unique question papers for theory part for each candidate at each examination/training center (as per assessment criteria below) 4. Individual assessment agencies will create unique evaluations for skill practical for every student at each examination/training center based on this criteria 5. To pass the Qualification Pack, every trainee should sco re a minimum of 50% in aggregate |