Free Service Technician Level 6 Course (6Months)
Service Technician Level 6:
Brief Job Description
An Auto Service Technician Level 6 is responsible for managing advanced diagnosis and repairs. The individual carries out all types of diagnosis of faults and repairs and is responsible for supervising work of other technicians/senior technicians.
Personal Attributes
An individual on this job must have good communication and interpersonal skills in addition to being a team player, as the job requires coordination with other technicians during diagnosis. The individual must have a technical bend of mind to understand the technical aspects related to various aggregates in a vehicle, to assist in the fault diagnosis. The individual should be proactive, process and customer centric with ability to guide junior technicians. Keeping oneself abreast of the latest developments and newer technologies used in the various systems of the vehicle and its aggregates is highly desirable.
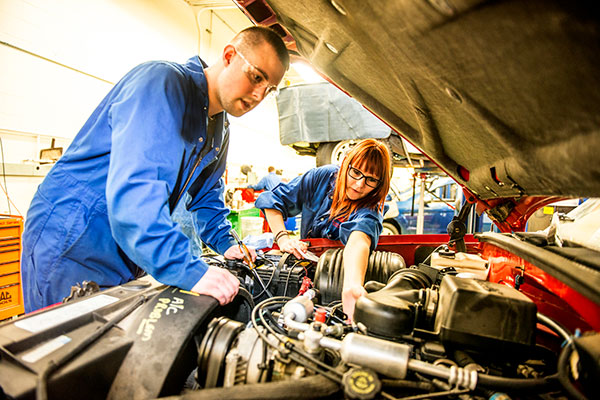
Plan and organise work to meet expected outcomes:
Elements and Performance Criteria
Work requirements including various activities within the given time and set quality standards
To be competent, the user/individual on the job must be able to:
PC1. keep immediate work area clean and tidy
PC2. treat confidential information as per the organisations guidelines
PC3. work in line with organisations policies and procedures
PC4. work within the limits of job role
PC5. obtain guidance from appropriate people, where necessary
PC6. ensure work meets the agreed requirements
Appropriate use of resources
To be competent, the user/individual on the job must be able to:
PC7. establish and agree on work requirements with appropriate people
PC8. manage time, materials and cost effectively
PC9. use resources in a responsible manner
Knowledge and Understanding (KU)
The individual on the job needs to know and understand:
KU1. the organisations policies, procedures and priorities for area of work, role and responsibilities in carrying out that work
KU2. the limits of responsibilities and when to involve others
KU3. specific work requirements and who these must be agreed with
KU4. the importance of having a tidy work area and how to do this
KU5. how to prioritize workload according to urgency and importance and the benefits of this
KU6. the organisations policies and procedures for dealing with confidential information and the importance of complying with these
KU7. the purpose of keeping others updated with the progress of work
KU8. who to obtain guidance from and the typical circumstances when this may be required
KU9. the purpose and value of being flexible and adapting work plans
KU10. how to complete tasks accurately by following standard procedures
KU11. technical resources needed for work and how to obtain and use these
Generic Skills (GS)
User/individual on the job needs to know how to:
GS1. write in at least one language
GS2. read instructions, guidelines/procedures
GS3. ask for clarification and advice from appropriate persons
GS4. communicate orally with colleagues
GS5. make a decision on a suitable course of action appropriate for accurately completing the task within resources
GS6. agree objectives and work requirements
GS7. plan and organise work to achieve targets and deadlines
GS8. deliver consistent and reliable service to customers
GS9. check own work and ensure it meets customer requirements
GS10. anomalies to the concerned persons
GS11. analyse problems and identify work-arounds taking help from
GS12. apply own judgement to identify solutions in different situations
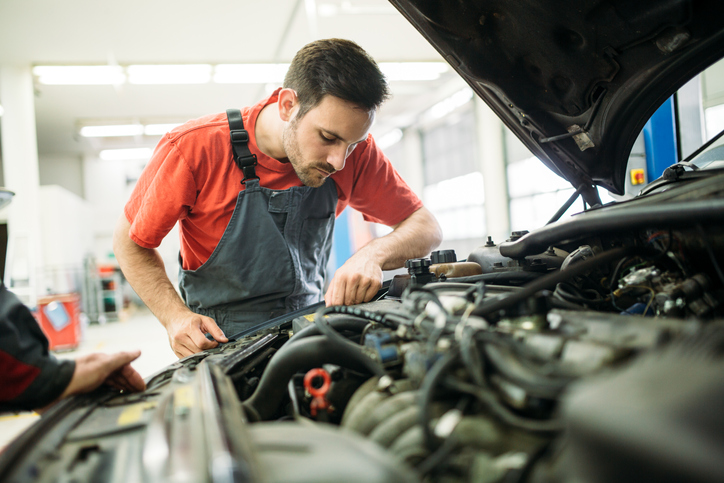
Work effectively in a team:
Elements and Performance Criteria
Effective communication
To be competent, the user/individual on the job must be able to:
PC1. maintain clear communication with colleagues
PC2. work with colleagues
PC3. pass on information to colleagues in line with organisational requirements
PC4.. work in ways that show respect for colleagues
PC5. carry out commitments made to colleagues
PC6. let colleagues know in good time if cannot carry out commitments, explaining the reasons
PC7. identify problems in working with colleagues and take the initiative to solve these problems
PC8. follow the organisations policies and procedures for working with colleagues
PC9. ability to share resources with other members as per priority of tasks
Knowledge and Understanding (KU)
The individual on the job needs to know and understand:
KU1. the organisations policies and procedures for working withcolleagues, role and responsibilities in relation to this
KU2. the importance of effective communication and establishing goodworking relationships with colleagues
KU3. different methods of communication and the circumstances inwhich it is appropriate to use these
KU4. benefits of developing productive working relationships withcolleagues
KU5. the importance of creating an environment of trust and mutualrespect
KU6. whether not meeting commitments, will have implications onindividuals and the organisation
KU7. different types of information that colleagues might need and theimportance of providing this information when it is required
KU8. the importance of problems, from colleagues perspective andhow to provide support, where necessary, to resolve these
Generic Skills (GS)
User/individual on the job needs to know how to:
GS1. complete well written work with attention to detail
GS2. read instructions, guidelines/procedures
GS3. listen effectively and orally communicate information
GS4. make decisions on a suitable course of action or response
GS5. plan and organise work to achieve targets and deadlines
GS6. check that the work meets customer requirements
GS7. deliver consistent and reliable service to customers
GS8. apply problem solving approaches in different situations
GS9. apply balanced judgements to different situations
GS10. apply good attention to detail
GS11. check that the work is complete and free from errors
GS12. get work checked by peers
GS13. work effectively in a team environment
Maintain a healthy,safe and secure working environment:
Elements and Performance Criteria
Resources needed to maintain a safe, secure working environment
To be competent, the user/individual on the job must be able to:
PC1. comply with organisations current health,safety and security policies and procedures
PC2. report any identified breaches in health,safety, and security policies and procedures to the designated person
PC3.. Coordinate with other resources at the workplace to achieve the healthy, safe and secure environment for all incorporating all government norms esp. for emergency situations like fires,earthquakes etc.
PC4. identify and correct any hazards like illness, accidents, fires or any other natural calamity safely and within the limits of individuals authority
PC5. report any hazards outside the individuals authority to the relevant person in line with organisational procedures and warn other people who may be affected
PC6. follow organisations emergency procedures for accidents, fires or any other natural calamity
PC7. identify and recommend opportunities for improving health,safety, and security to the designated person
PC8. complete all health and safety records are updates and procedures well defined
Knowledge and Understanding (KU)
The individual on the job needs to know and understand:
KU1. legislative requirements and organisations procedures for health, safety and security and individuals role and responsibilities in relation to this
KU2. what is meant by a hazard, including the different types of health and safety hazards that can be found in the workplace
KU3. how and when to report hazards
KU4. the limits of responsibility for dealing with hazards
KU5. the organisations emergency procedures for different emergency situations and the importance of following these
KU6. the importance of maintaining high standards of health, safety and security
KU7. implications that any non-compliance with health, safety and security may have on individuals and the organisation
KU8. different types of breaches in health, safety and security and how and when to report these
KU9. evacuation procedures for workers and visitors
KU10. how to summon medical assistance and the emergency services,where necessary
KU11. how to use the health, safety and accident reporting procedures and the importance of these
Generic Skills (GS)
User/individual on the job needs to know how to:
GS1. complete accurate, well written work with attention to detail
GS2. read instructions, guidelines/procedures/rules
GS3. listen and orally communicate information
GS4. make decisions on a suitable course of action or response
GS5. plan and organise work to achieve targets and deadlines
GS6. build and maintain positive and effective relationships withcolleagues and customers
GS7. apply problem solving approaches in different situations
GS8. analyse data and activities
GS9. apply balanced judgements to different situations
GS10. apply good attention to detail
GS11. check that the work is complete and free from errors
GS12. get work checked by peers
GS13. work effectively in a team environment
Carry out advanced diagnosis of vehicle for engine:
Elements and Performance Criteria
Carry out advance diagnosis for operational faults in the mechanical aggregates
To be competent, the user/individual on the job must be able to:
PC1.. identify and explain the functioning of each system, component and aggregate of a vehicle
PC2. . obtain sufficient information from the job card and customer/ service advisor to make an assessment of service and repair needs of the vehicle
PC3. . review the job card and develop clear and complete understanding of customer complaints
PC4. . use checklists and standard OEM operating procedures as per the vehicle service manual to confirm need for servicing, replacement of oils, filters and other parts etc.
PC5.. conduct routine and non-routine inspections for vehicle fitness assessment, emission testing, safety assessment, post-accident diagnostic assessment, postrepairserviceability assessment and manufacturer recall assessment
PC6. . ensure any additional malfunctions or repair requirements observed in the vehicle are reported to the service advisor and discussed with the customer
PC7.. follow standard operating procedures as prescribed by the suppliers in the user manuals of workshop tools and equipment
PC8. . ensure all workshop tools, equipment and workstations are adequately maintained by carrying out scheduled checks, calibration and timely repairs where necessary
PC9.. ensure any malfunctions observed in tools and equipment are reported to the concerned persons
PC10. . conduct inspection of the engine and all other mechanical parts & aggregates to diagnose need for repairs or adjustment
PC11. . conduct test drives to assess need for repairs, calibration or adjustment
PC12.. supervise dismantling and reassembly of aggregates of a vehicle for the purpose of diagnosing faults
PC13. . compare results of diagnostic inspections and tests against vehicle specifications and any regulatory requirements
PC14. . utilise various tools including computer-based diagnostic tools for accurate assessment of vehicles operating parts and systems
PC15.. prepare a list of all the service, repair and replacement requirements of the vehicle
PC16. . finalise the list of all the service, repair and replacement requirements of the vehicle in consultation with service advisor
PC17.. ensure safe movement and parking of the vehicle in the workshop
PC18.. supervise junior technicians in their work
PC19. . ensure that trainings organized by the OEM from time-to-time are attended and knowledge levels are upgraded (esp. in case of newly launched products, product refreshes)
PC20. . drive a relevant 2/3/4 wheeler vehicle which is an important part of the diagnosis of the type of vehicle that is dealt by the relevant OEM
Knowledge and Understanding (KU)
The individual on the job needs to know and understand:
KU1. standard operating procedures of the organisation/ dealership for inspection and diagnosis of faults in a vehicle
KU2. standard operating procedures recommended by the dealership/ suppliers/OEM for using tools and equipment
KU3. safety requirements for equipment and components (e.g. preventing/ dealing with oil spillage and inflammable materials)
KU4. documentation requirements for each procedure carried out
KU5. organizational and professional code of ethics and standards of practice
KU6. safety, health, environmental policies and regulations for the workplace as well as for automotive trade in general (e.g. safe practices while working in pits/ under vehicles)
KU7. the basic technology used in and functioning of various components and aggregates of the vehicle including: engine and fuel system (diesel, petrol, electrical, gas, hybrid etc.) cooling system air supply systems emission and exhaust system ignition systems clutch assembly clutch operating system gearbox (manual and automatic) drivelines and hubs drive-train assembly and transmission systems (manual, automatic etc.) steering system suspension system brake system (including regenerative braking systems) tyres and wheels (including wheel alignment) radiator batteries and power storage system power-generating systems (including charging systems especially for electrical and hybrid vehicles) electrical wire harness, lighting, ignition, electronic and air-conditioning systems etc. energy recuperation systems, if applicable (e.g. in electric, gas and hybrid vehicles) electronic active and passive safety, media, comfort and convenience, supplementary restraint systems (SRS), networking and other systems electronic control unit hydraulic and pneumatic system various lubrication systems
KU8. the tools used to assess and confirm technical faults that cannot be determined through a visual inspection, including use of: organic light emitting displays anti-lock braking system abs/air bag scan tools, automotive scanners, graphing scanners, modular diagnostic information systems pressure indicators: fuel pressure testers, manifold gauge sets, oil pressure gauges, tire pressure gauges measuring equipment: Vernier callipers, micrometre, feeler gauges, spanner, compression gauge, brake fluid tester, brake fluid bleeding equipment, refractometer, radiator pressure gauge, hydrometer, thermometer, strut compressor, bearing installer, installer and puller for bearings, oil seal installer and mandrel, AC manifold gauge, multi-metre, flow metre, temp gauge, dial gauge etc. other tools: laptops
KU9. the various sources of information available for assessing service and repair requirements of the vehicle including: diagnostic displays visual inspections test drives vehicle/equipment manufacturer specifications standard operating procedures for diagnosis
KU10. typical symptoms of common technical faults in a vehicle including fluid levels, leaks, wear and tear, damage to a part/ aggregate and need for adjustments
KU11. basic computer skills including the following: OEM specific computer applications basic computer based tasks (e.g. use of productivity tools such as word, excel etc.) basic internet based tasks (e.g. accessing and responding to emails etc.)
Generic Skills (GS)
User/individual on the job needs to know how to:
GS1. complete and maintain workplace record son inspection, diagnosis and repair activities
GS2. maintain all office records required on the job (e.g. stock records, job cards, repair quotations, personnel records, time sheets, meeting notes etc.)
GS3. record all diagnostic inspections and tests carried out on a vehicle
GS4. write in at least one language
GS5. read and interpret workplace related documentation
GS6. clearly communicate workplace information and ideas with workplace colleagues (verbal and non-verbal)
GS7. use terms, names, grades, and other nomenclature pertaining to the automotive trade, tools, specific workshop equipment etc.
GS8. communicate with colleagues to handle verbal enquiries, such as clarifying instructions and responding to requests for information
GS9. determine the nature and objective of the analysis and evaluation required and decide on the diagnostic techniques to be applied
GS10. plan work assigned on a daily basis and provide estimates of time required for each piece of work(e.g. by evaluating work assigned on a job card and providing time estimates for each service/ repair activity)
GS11. organise the workplace and work according to the principles of 5S
GS12. prioritise actions to achieve required outcomes
GS13. interpret the needs of customers by evaluating job cards and talking to service advisor and superiors
GS14. ensure that customer needs are assessed and satisfactory service is provided
GS15. follow up with the service advisor on any unfavourable feedback received from customer
GS16. recognise a workplace problem or a potential problem and take action
GS17. determine problems needing priority action
GS18. refer problems outside area of responsibility to concerned person(e.g. unavailability of required spare parts or materials in the workshop)
GS19. gather information and provide assistance as required to solve problems
GS20. analyse the complexity of work to determine if it can be successfully carried out
GS21. analyse, evaluate and apply the information gathered from observation, experience, reasoning, or communication to act efficiently
Carry out complete and advanced level diagnosis of vehicle for electrical:
Elements and Performance Criteria
Carry out advance diagnosis for faults in the electrical and electronic aggregates
To be competent, the user/individual on the job must be able to:
PC1.. identify and explain the functioning of various electrical systems, components and aggregates of a vehicle
PC2.. obtain sufficient information from customer/ service advisor to make an assessment of service and repair needs of the vehicle
PC3.. review the job card and understand customer complaints
PC4. . use checklists and standard OEM operating procedures to confirm need for servicing, replacement of oils, filters and other parts etc.
PC5. . follow standard operating procedures for using workshop tools and equipment
PC6. . ensure all workshop tools, equipment and workstations are adequately maintained by carrying out scheduled checks, calibration and timely repairs where necessary
PC7. . ensure any additional malfunctions or repair requirements observed in are reported to the service advisor and discussed with the customer
PC8. . ensure any malfunctions observed in tools and equipment are reported to the concerned persons
PC9. . conduct routine and non-routine inspections for pre-purchase assessment, vehicle fitness assessment, emission testing, safety assessment, post-accident diagnostic assessment, post-repair serviceability assessment and manufacturer recall assessment
PC10. . select the most appropriate analytical and evaluative methodology including diagnostic process, sequence, tests and testing equipment
PC11.. identify, select and prepare tools and material required for the specific diagnostic process
PC12.. prepare system components for the diagnostic process including park-up, isolation and cleaning requirements
PC13. . conduct inspection of electrical and electronic systems including: stability/steering/ suspension systems (including electronic stability systems, vehicle dynamic control, closed loop electronic steering and multi-class Bus systems) electric over hydraulic systems (including garbage compactors, crane rams, steering control, excavator bucket control, steering rudder control etc.) engine management systems (including fuel cell technology/hydrogen, on line maintenance and remote diagnostics, common rail diesel direct injection, drive by wire, multi-class Bus systems and closed loop diesel engine management systems) transmission/driveline systems (including clutches, torque converters, mechanical and automatic transmissions, drive and power take-off shafts and differentials, mechatronic modules and multi-class Bus systems) braking systems (including ABS, engine brakes, electric retarders, electric trailer brakes, brake by wire and multi-class Bus systems) safety systems (including fire suppressing, work load detecting, tyre pressure control, speed/load limiting, traction control, seat belt pre-tensioning, roll over protection, object detection, navigation aids, intelligent transport systems, intelligent SRS systems, adaptive cruise control, multi-class Bus systems, active and passive collision avoidance, infrared vision, lighting and windscreen wipers control) monitoring/protection systems (including display types such as LCD, VFD, CRT, HUD, re-configurable systems, electronic analogue display, on board diagnostics, remote/wireless monitoring systems and multi- class Bus systems) convenience and entertainment systems (including audio and visual units, compact disks, analogue tapes, radio, speaker types, amplifiers, crossovers, balancers, aerials and multi-class Bus systems) theft deterrent systems (including remote keyless entry (RKE), immobiliser system design, passive entry systems, two way RKE, fingerprint technologies, rolling codes, transmitter and receiver operation, satellite systems) electric and hybrid vehicle systems (including battery technology, motor drive systems, motor controllers, air conditioning systems, electronic protection systems and multi-class Bus systems) climate control systems (including air conditioning, heating, blending systems and multi-class Bus systems)
PC14. diagnose need for repairs, adjustment or part replacement in electrical and electronic systems
PC15. conduct test drives to assess need for repairs, calibration or adjustment
PC16. compare results of diagnostic inspections and tests against vehicle specifications and any regulatory requirements
PC17. prepare a list of all the service, repair and replacement requirements of the vehicle
PC18. finalise the list of all the service, repair and replacement requirements of the vehicle in consultation with service advisor
PC19. ensure safe movement and parking of the vehicle in the workshop
PC20. assist junior technicians in their work
PC21. utilise any computer-based diagnostic applications
PC22. ensure that trainings organized by the OEM from time-to-time are attended and knowledge levels are upgraded (esp. in case of newly launched products, product refreshes)
PC23. drive a relevant 2/3/4 wheeler vehicle which is an important part of the diagnosis of the type of vehicle that is dealt by the relevant OEM
Knowledge and Understanding (KU)
The individual on the job needs to know and understand:
KU1. standard operating procedures of the organization/ dealership for inspection and diagnosis of faults in a vehicle
KU2. standard operating procedures recommended by the dealership/ suppliers/OEM for using tools and equipment
KU3. safety requirements for equipment and components (e.g. preventing/ dealing with oil spillage and inflammable materials)
KU4. documentation requirements for each procedure carried out
KU5. organisational and professional code of ethics and standards of practice
KU6. safety, health, environmental policies and regulations for the workplace as well as for automotive trade in general (e.g. safe practices while working in pits/ under vehicles)
KU7. the basic technology used in and functioning of various components and aggregates of the vehicle including: engines and fuel system (diesel, petrol, electrical, gas, hybrid etc.) cooling system air supply systems emission and exhaust system ignition systems clutch assembly clutch operating system gearbox (manual and automatic) drivelines and hubs drive-train assembly and transmission systems (manual, automatic etc.) steering system suspension system brake system (including regenerative braking systems) tyres and wheels (including wheel alignment) radiator batteries and power storage system power-generating systems (including charging systems especially for electrical and hybrid vehicles) electrical wire harness, lighting, ignition, electronic and air-conditioning systems etc. energy recuperation systems, if applicable (e.g. in electric, gas and hybrid vehicles) electronic active and passive safety, media, comfort and convenience,supplementary restraint systems (SRS), networking and other systems electronic control unit hydraulic and pneumatic system various lubrication systems
KU8. basic principles of: ohms Law, voltage, power, current (AC/DC) resistance, magnetism, electromagnetism and electromagnetic induction etc. vehicle earthing and earthing methods vehicle engine systems (e.g. types, applications and operation of sensors, actuators, etc.) types of circuit protection and their use electrical safety procedures the operation of warning, charging and starter circuits symbols, units and terms associated with electric systems and components battery charging electrical/electronic control systems operation of electronic and electric engine systems (including electrical component function, electrical inputs, outputs, voltages and oscilloscope patterns, digital and fiber optics principles) electrical theory and operation covering automotive digital computers, networked vehicles, voltage, current, resistance, power, capacitance, electrostatics, magnetics, inductance, discrete electronic components, logic families, and radio frequency
KU9. the tools used to assess and confirm technical faults that cannot be determined through a visual inspection, including use of: measuring equipment: analogue and digital multi-meters, lab oscilloscopes, data scanners, test lights, test LEDs, pulse generators etc. electrical and electronic testing equipment: voltmeters, ammeters, ohmmeters, battery testing equipment, dedicated and computer based diagnostic equipment, oscilloscopes, scanner, battery tester, cell discharge tester, hydrometer, multimeter etc. other tools: laptops
KU10. the theory of diagnosis including concept, design and planning
KU11. types, functions, operations and limitations of diagnostic testing equipment
KU12. methods and processes for recording and reporting diagnostic findings and recommendations
KU13. the tests used to assess and confirm technical faults that cannot be determined through a visual inspection, including testing: wiring and connector integrity operator and specification of input and output devices controlling electronic components and computers readings related to direct, indirect and intermittent causes
KU14. the various sources of information available for assessing service and repair requirements of the vehicle including: diagnostic displays visual inspections test drives vehicle/equipment manufacturer specifications standard operating procedures for diagnosis
KU15. typical symptoms of common technical faults in a vehicle including fluid levels, leaks, wear and tear, damage to a part/ aggregate and need for adjustments
KU16. basic computer skills including the following: OEM specific computer applications basic computer based tasks (e.g. use of productivity tools such as word, excel etc.) basic internet based tasks (e.g. accessing and responding to emails etc.)
Generic Skills (GS)
User/individual on the job needs to know how to:
GS1. complete and maintain workplace record son inspection, diagnosis and repair activities
GS2. maintain all office records required on the job (e.g. stock records, job cards, repair quotations, personnel records, time sheets, meeting notes etc.)
GS3. record all diagnostic inspections and tests carried out on a vehicle
GS4. write in at least one language
GS5. read and interpret workplace related documentation (e.g. stock records, job cards, repair quotations, personnel records, time sheets, meeting notes etc.)
GS6. clearly communicate workplace information and ideas with workplace colleagues (verbal and non-verbal)
GS7. use terms, names, grades, and other nomenclature pertaining to the automotive trade, tools, specific workshop equipment etc.
GS8. communicate with colleagues to handle verbal enquiries, such as clarifying instructions and responding to requests for information
GS9. determine the nature and objective of the analysis and evaluation required and decide on the diagnostic techniques to be applied
GS10. plan work assigned on a daily basis and provide estimates of time required for each piece of work(e.g. by evaluating work assigned on a job card and providing time estimates for each service/ repair activity)
GS11. organise the workplace and work according to the principles of 5S
GS12. prioritise actions to achieve required outcomes
GS13. interpret the needs of customers
GS14. ensure that customer needs are assessed and every effort is made to provide satisfactory service
GS15. recognise a workplace problem or a potential problem and take action
GS16. determine problems needing priority action
GS17. refer problems outside area of responsibility to concerned person(e.g. unavailability of required spare parts or materials in the workshop)
GS18. gather information and provide assistance as required to solve problems
GS19. analyse the complexity of work to determine if it can be successfully carried out
GS20. analyse, evaluate and apply the information gathered from observation, experience, reasoning, or communication to act efficiently
Assessment Guidelines
- Criteria for assessment for each Qualification Pack will be created by the Sector Skill Council. Each Element/ Performance Criteria (PC) will be assigned marks proportional to its importance in NOS. SSC will also lay down proportion of marks for Theory and Skills Practical for each Element/ PC.
- The assessment for the theory part will be based on knowledge bank of questions created by the SSC.
- Assessment will be conducted for all compulsory NOS, and where applicable, on the selected elective/option NOS/set of NOS.
- Individual assessment agencies will create unique question papers for theory part for each candidate at each examination/training center (as per assessment criteria below).
- Individual assessment agencies will create unique evaluations for skill practical for every student at each examination/ training center based on these criteria.
- To pass the Qualification Pack assessment, every trainee should score the Recommended Pass % aggregate for the QP.