Free Computer Aided Test Executive Course (6Months)
Computer Aided Test Executive:
Brief Job Description
This role is responsible for organizing various tests on automobile aggregates prototypes in a simulated laboratory environment and presenting first level analysis report to the Engineering Management.
Personal Attributes
The individual should have passions for automobiles and the phenomena connected . The individual should possess coordination and interpersonal skills, demonstrate analytical reasoning, be technology savvy, oral and written communication skills, observations skills, ability to plan and prioritize work, quality consciousness, sensitivity to problem solving, quick decision making, safety orientation and high precision.
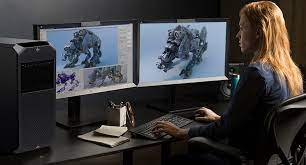
Maintain a safe and healthy working environment:
Elements and Performance Criteria
Identify and report the risks identified
To be competent, the user/individual on the job must be able to:
PC1.. Identify activities which can cause potential injury through sharp objects, burns, fall, electricity, gas leakages, radiation, poisonous fumes, chemicals ,loud noise
PC2. Inform the concerned authorities about the potential risks identified in the processes, workplace area/ layout, materials used etc
PC3. Inform the concerned authorities about machine breakdowns, damages which can potentially harm man/ machine during operations
PC4. Create awareness amongst other by sharing information on the identified risks
Create and sustain a Safe, clean and environment friendly work place
To be competent, the user/individual on the job must be able to:
PC5.. Follow the instructions given on the equipment manual describing the operating process of the equipments
PC6.. Follow the Safety, Health and Environment related practices developed by the organization
PC7. Operate the machine using the recommended Personal Protective Equipments (PPE)
PC8. . Maintain a clean and safe working environment near the work place and ensure there is no spillage of chemicals, production waste, oil, solvents etc
PC9. Maintain high standards of personal hygiene at the work place
PC10. Ensure that the waste disposal is done in the designated area and manner as per organization SOP.
PC11. Inform appropriately the medical officer/ HR in case of self or an employees illness of contagious nature so that preventive actions can be planned for others
Knowledge and Understanding (KU)
The individual on the job needs to know and understand:
KU1. relevant standards, procedures and policies related to Health, Safety and Environment followed in the company
KU2. basic knowledge of Safety procedures( fire fighting, first aid) within the organization
KU3. knowledge of various types of PPEs and their usage
KU4. basic knowledge of risks/hazards associated with each occupation in the organization
KU5. how to safely operate various tools and machines and risksassociated with the tools/ equipment
KU6. knowledge of personal hygiene and how an individual an contribute towards creating a highly safe and clean working environment
Generic Skills (GS)
User/individual on the job needs to know how to:
GS1. write basic level notes and observations
GS2. read safety instructions put up across the plant premises
GS3. read safety precautions mentioned in equipment manuals and panels to understand the potential risks associated
GS4. effectively communicate information to team members
GS5. informemployees in the plant and concerned functions about events, incidents & potential risks observed related to Safety, Health and Environment.
GS6. question operator/ supervisor in order to understand the safety related issues
GS7. attentively listen with full attention and comprehend the information given by the speaker during safety drills and training programs
GS8. use common sense and make judgments during day to day basis
GS9. use reasoning skills to identify and resolve basic problems
GS10. use common sense and make judgments during day to day basis
GS11. use reasoning skills to identify and resolve basic problems

Ensure implementation of 5S activities at the shop floor & the office area:
Elements and Performance Criteria
Ensure proper sorting of items at the work place
To be competent, the user/individual on the job must be able to:
PC1.. ensure all recyclable materials are put in designated containers
PC2. ensure no tools, fixtures & jigs are lying on workstations unless in use and no un-necessary items is lying on workbenches or work surfaces unless in use
PC3. ensure that the operators and other team members are segregating the waste in hazardous/ non hazardous waste as per the sorting work instructions
PC4. ensure that all the operators are following the technique of waste disposal and waste storage in the designated bins
PC5.. segregate the items which are labelled at red tag items for the process area and keep them in the correct places
PC6.. ensure that all the tools/ equipment/ fasteners/ spare parts are arranged as per specifications/ utility into proper trays, cabinets, lockers as mentioned in the 5s guidelines/ work instructions
PC7. check for return of any type of extra material and tools to the designated sections and make sure that no additional material/ tool is lying near the work area
PC8. . oversee removal of unnecessary equipment, storage, furniture, unneeded inventory, supplies, parts and material
PC9. ensure that areas of material storage areas are not overflowing
PC10. ensure proper stacking and storage of the various types of boxes and containers as per the size/ utility to avoid any fall of items/ breakage and also enable easy sorting when required
Ensure proper documentation and storage – streamlining & organizing the workplace
To be competent, the user/individual on the job must be able to:
PC11. ensure that the team follows the given instructions and checks for labelling of fluids, oils lubricants, solvents, chemicals etc and proper storage of the same to avoid spillage, leakage, fire etc
PC12. make sure that all material and tools are stored in the designated places and in the manner indicated in the 5s instructions
PC13. ensure that organizing the workplace takes place with due considerations to the principles of wasted motions, ergonomics, work & method study .
Ensure cleaning of self and the work place
To be competent, the user/individual on the job must be able to:
PC14. ensure that the area has floors swept, machinery clean and is generally neat and tidy in case of cleaning, ensure that correct displays are maintained on the floor which indicate potential safety hazards
PC15.. ensure workbenches and work surfaces are clean and in good condition
PC16.. ensure adherence to the cleaning schedule for the lighting system to ensure proper illumination
PC17.. ensure all recyclable materials are put in designated containers
Ensure standardization
To be competent, the user/individual on the job must be able to:
PC18. ensure that daily cleaning standards and schedules to create a clean working environment are followed across the plant
PC19.. ensure all recyclable materials are put in designated containers
PC20. . ensure logical and user friendly documentation and file management for all activities across the plant and create guidelines around standardization of processes
PC21. ensure timely creation and sharing of the 5s checklists
PC22. ensure that the 5s manual are available as per the timelines Ensure sustenance
To be competent, the user/individual on the job must be able to:
PC23. ensure team cooperation during the audit of 5 s activities
PC24. ensure that workmen are periodically trained to address challenges related to 5s
PC25.. participate actively in employee work groups on 5s and encourage team members for active participation
PC26.. oversee that the staff/operators are trained and fully understand 5s procedures
PC27. . ensure that all the guidelines for what to do and what not to do to build sustainability in 5s are mentioned in the 5s check lists/ work instructions and are easily searchable
PC28. ensure continuous training of the team members on 5s in order to increase their awareness and support implementation
PC29. ensure that all visual controls, notice boards, symbols etc at the manufacturing place are created, working and are put up as per the requirement
Knowledge and Understanding (KU)
The individual on the job needs to know and understand:
KU1. relevant standards, procedures and policies related to 5Sfollowed in the company
KU2. have basic knowledge of 5S procedures
KU3. know various types 5s practices followed in various areas
KU4. understand the 5S checklists provided in the department/ team
KU5. have skills to identify useful & non useful items
KU6. have knowledge of labels , signs & colours used as indicators
KU7. Have knowledge on how to sort and store various types of tools,equipment, material etc
KU8. know , how to identify various types of waste products
KU9. understand the impact of waste/ dirt/ dust/unwantedsubstances on the process/ environment/ machinery/ humanbody
KU10. have knowledge of best and environment protective ways ofcleaning & waste disposal
KU11. understand the importance of standardization in processes
KU12. understand the importance of sustainability in 5S
KU13. have knowledge of TQM process
KU14. have knowledge of various materials and storage norms
KU15. understand visual controls, symbols, graphs etc

Generic Skills (GS)
User/individual on the job needs to know how to:
GS1. write basic level notes and observations
GS2. note down observations (if any) related to the process
GS3. write information documents to internal departments/ internal teams
GS4. read 5S instructions put up across the plant premises
GS5. effectively communicate information to team members inform employees in the plant and concerned functions about 5S
GS6. question the process head in order to understand the 5S related issues
GS7. attentively listen with full attention and comprehend the information given by the speaker during 5S training programs
GS8. use common sense and make judgments during day to day basis
GS9. use reasoning skills to identify and resolve basic problems using 5S
GS10. persuade team members to follow 5 S
GS11. ensure that the team members understand the importance of using 5 S tool
GS12. use innovative skills to perform and manage 5 S activities at the work desk and the shop floor
GS13. exhibit inquisitive behaviour to seek feedback and question on the existing set patterns of work emerge, techniques in CA/CI around 5 S work practices
GS14. do what is right, not what is a popular practice
GS15. follow shop floor rules& regulations and avoid deviations
GS16. lead by example in the plant premises while performing activities related to 5S
GS17. ensure self-cleanliness on a daily basis
GS18. demonstrate the will to keep the work area in a clean and orderly manner
GS19. accept additional responsibility for self and the team
GS20. encourage self and other to take greater responsibilities for managing 5S
GS21. identify obstacles and bottlenecks in the process and find basic level solutions for removing these obstacles
GS22. use previous experience in resolving problems and taking decisions
GS23. make timely and independent decisions on the line/ shift within the boundaries of the delegation matrix of the organization
Conduct testing of vehicles and aggregates using Computer Aided Engineering Aids:
Elements and Performance Criteria
Understanding the testing requirement and the process and establish parameters for comparison
To be competent, the user/individual on the job must be able to:
PC1.. understand the type of vehicle under test along with detailed understanding of the vehicle specifications
PC2.. understand the various organizational, domestic and international regulations impacting the performance of the vehicle under test
PC3.. understand the type of tests to be performed in the computer simulated environment by using the test checklist provided by the cross functional team
PC4.. understand various types of software modules like pro mechanics, nast ran, matlab, simi link etc. and their utility to conduct various cae based component and vehicle tests
PC5.. understand the testing methodology, process and test parameters required as per the work instructions/standard operating procedures. establish various data parameters for test results to enable comparison / simulation of performance.
Conduct CAE tests for assessing vehicle performance and durability
To be competent, the user/individual on the job must be able to:
PC6.. ensure selection of specified software program for testing the given component/ vehicle
PC7.. ensure selection of correct testing and simulation parameters as per the testing instruction manual provided by the team
PC8.. conduct the structural analysis of the test prototype and measure fatigue strength, body structure strength, chassis strength, vehicle door and window framework strength and metal fatigue analysis by selecting the correct testing parameters in the structural analysis program
PC9.. calculate the bending stiffness and torsional stiffness values for the vehicle components under testing
PC10.. conduct cae enabled motion tests for checking complex mechanical systems as engine, gearbox, powertrain and note down observations
PC11.. conduct cae simulated time motion based vehicle crash tests as per the testing instructions mentioned in the testing manual and note observations
PC12.. conduct front, side and rear crash impact testing and note observations of crash impact on vehicle structure and vehicle inhabitants ( through biomechanics and cae dummies)
PC13.. plot graphs for force vs. deformation and time vs. deformation and conduct first level analysis of impact
PC14.. using the recommended software programs, conduct the metal fatigue and stress strain analysis on vehicles and components
PC15.. conduct the cae simulated drop test to understand stress and shock bearing strength of the vehicle and the components
PC16.. conduct cfd ( computational fluid dynamics) to test the flow of fuel, lubricants, oil and water in the vehicle piping system
PC17.. ensure testing of thermal flow including exhaust gases through the thermal flow analysis module
PC18.. conduct non-linear analysis of rubber, plastic and metallic components to understand denting impact, cross movement, compression and expansion of components
PC19.. using cae enabled modules, test the outer body of vehicles to understand the vibrational behaviour of vehicle body and frames
PC20.. using digital electrical and electronic simulation program, test the working and performance of the vehicle electrical, electronics, telematics, instrumentation and navigation systems to ensure error free communication and decision making
PC21.. carry transfer path analysis, acoustic testing and component frequency analysis using relevant nvh testing modules
PC22.. conduct ergonomics testing using cae enabled modules to test vehicle design, rider comfort, seating comfort, braking process, steering movement process and overall vehicle dimensions
PC23.. carry out the vehicle dynamics tests as per the testing instruction to validate the vehicle manoeuvrability and vehicle performance through simulated obstacle testing tracks and proving tracks
PC24.. conduct cae enabled virtual driving test to validate the vehicle performance from a drivers point of view and measure driving comfort, manoeuvrability, vehicle handling and comfort level similar to an on road condition
PC25.. collate the test results and compare them with the internal/ external benchmarking standards and actual testing data parameters shared by the cross functional design team.
PC26.. prepare simulation & test result comparison for engineering cft /management team.
Knowledge and Understanding (KU)
The individual on the job needs to know and understand:
KU1. relevant manufacturing and testing standards and procedures followed in the company
KU2. new products manufactured by the company
KU3. internal product standards finalized within the organization
KU4. functional processes like Procurement, Store management, inventory management, quality management and key contact points for query resolution
KU5. quality norms and standards prescribed in the Quality Manual by the organization
KU6. 5S and Safety norms practiced in the organization
KU7. the working of various automobile components
KU8. general working of automobiles and linkage & impact of one parameter to another
KU9. various types of software testing programs like Pro Mechanical, Nast ran, Mat lab, Similinketc available in the market
KU10. impact of wind, water flow, hot & cold conditions, pressure on the performance of the vehicle
KU11. impact of various mechanical and thermal stresses on the external frame of the vehicle and overall vehicle performance
KU12. various national and international regulations, norms and standards on vehicles and engine performance regulations related to noise, vibrations, durability, reliability factors for 2 wheeler, 3 wheeler and 4 wheelers under normal and difficult environmental conditions
KU13. various defects related to reliability and durability of the component and impact of the defect on the final component and vehicle performance
KU14. probable sources of vehicle noise and possible impacts
KU15. analytical tools like Histogram analysis, Pareto Analysis, Why analysis, Process Mapping, Ishikawa ( Fishbone) analysis
KU16. basic human anatomy and impact of vehicle performance on human body
KU17. basic laws of physics, chemistry. metallurgy and mathematics
KU18. basic laws of geometry and product design
KU19. the methods of using instruments like Vernier callipers,micrometres, rulers and other inspection tools
KU20. how to read and interpret sketches and engineering drawings
KU21. potential health and safety hazards and related safety precautions during driving
Generic Skills (GS)
User/individual on the job needs to know how to:
GS1. document information from the manuals,discussion notes, process charts etc
GS2. create small notes/ work documents/ diagrams for operators and helpers to help them understand the process
GS3. write inter departmental notes/ memos or make suitable entries in the online system
GS4. use emails and other business correspondence methods ( internal memos, circular etc. ) for communicating with other team members/ vendors/ suppliers etc.
GS5. read equipment manuals and process documents to understand the equipment and processes better
GS6. read internal information memos send by internal customers ( other functions within the organization)
GS7. discuss task lists, schedules, and work-loads with the operative team members
GS8. answer the queries raised by the operative team as well as intercompany departments
GS9. effectively communicate with the operators and helpers and make them aware of work expectations, targets, policies, processes etc
GS10. attentively listen with full attention the queries and grievances raised by the operative team and comprehend the information given by the speaker
GS11. communicate effectively to the team members
GS12. identify conflicts in the team and try to resolve them at the earliest
GS13. interact and engage with the team members on a day to day basis
GS14. counsel and coach the operators and help them resolve issues
GS15. timely highlight to the management about any good work/ achievement by the operators and helpers
GS16. break the problem into smaller issues and tasks to arrive at a solution
GS17. understand inter process relationship and establish relationship between various parts of the problem
GS18. leverage experience to find effective solutions to problems
GS19. use basic analytical tools to arrive at solutions
GS20. plan, organize and prioritize the work order and jobs received from the production manager
GS21. manage the schedule plan for the operators and helpers on the line/shift
GS22. validate all process/ equipment manuals so that the final process selected is correct
GS23. organize information, tools, manuals etc. on the shop floor so that sorting becomes easy
GS24. reorganize resources on the line/ shift in case of change of plans
GS25. use common sense and make judgments during day to day basis
GS26. use reasoning skills to identify and resolve problems
GS27. use intuition to detect any potential problems which could arise during operations
GS28. accept additional responsibility for self and the team
GS29. encourage self and other to take greater responsibilities
GS30. ensure that the work allocated to the team is completed as per timelines and quality norms
GS31. identify obstacles and bottlenecks in the process and on own find basic level solutions for removing these obstacles
GS32. motivate and provide support for the team on the shop floor
GS33. encourage collaboration between team members
GS34. resolve team issues and grievances to manage conflicts within the team
GS35. create an environment of approachability, trust and openness within the team
GS36. ensure role clarity for all operators and helpers on the line/ shift
GS37. escalate any team related issues to the concerned person at the right time
GS38. identify defective parts in the manufacturing line by comparing manufactured pieces with the work standard
GS39. link the defect observed with the overall impact on the performance of the component/ automobile
GS40. support and contribute in monitoring and delivering high quality output from self and others
GS41. train team members on maintaining quality standards set by the organization
GS42. gather information skilfully from multiple sources
GS43. analyse information in depth and identifies the problem in a timely manner
GS44. develop alternate solutions and resolves problems in early stages
GS45. work tireless in spite of repeat activities in a diligent manner to resolve problems on a day to day basis
GS46. use previous experience in resolving problems and taking decisions
GS47. make timely and independent decisions on the line/ shift within the boundaries of the delegation matrix of the organization
GS48. exhibit objectivity & openness to others views
GS49. collaborate with stakeholders to achieve the desired state of final result
GS50. familiarise with leading practices available in the market
GS51. think independently on new approaches to manufacturing process, material management, data management and team management
GS52. represent any new ideas/ approaches on process improvement and productivity improvement to the seniors in the team
Ensure documentation and analysis of various tests conducted:
Elements and Performance Criteria
Understanding the testing requirement and the process
To be competent, the user/individual on the job must be able to:
PC1.. understand the vehicle testing requirements (based on the type of vehicle to be tested) as mentioned in the testing instructions sheets/ work instructions/ testing control plan
PC2.. understand the testing methodology, equipment and process required as per the process manuals/ work instructions/standard operating procedures
PC3.. ensure that the correct testing document containing the specified setup drawing, testing schedules, testing parameters, test specifications and test outcome ranges are mentioned
Documentation of the test outcomes
To be competent, the user/individual on the job must be able to:
PC4.. ensure observation of the various digital and graphical displays of the testing equipment
PC5.. note down the observations in the hard copy/ soft copy format as provided by the organization
PC6.. maintain records of all versions of testing conducted for a particular component/ vehicle along with the date, time, testing setup and testing environment information
PC7.. maintain records of any previous remarks mentioned by the testing team for a particular component/vehicle
PC8.. maintain records of comparison between the test outcomes and internal/ external benchmarks and government regulations
Analysis of test outcomes and modifications to the prototype
To be competent, the user/individual on the job must be able to:
PC9.. conduct a first level analysis of the test outcomes
PC10.. ensure reference to previous test results and benchmarks during the analysis phase
PC11.. use analytical tools like why analysis, 7 qc tools, brain storming and other methodology to systematically analyse the observations of the test results
PC12.. check for any gaps in design of the component/ vehicle prototype leading to the test failures
PC13.. share the first level draft test assessment report with the testing manager
PC14.. in case need arises, conduct required tests similar to the one already conducted in the presence of the testing manager to confirm the test results
PC15.. support the test manager in creating presentations and dockets for cross functional team meeting
PC16.. collaborate with the cross functional design team, prototyping team and manufacturing team and ensure required modification in vehicle and aggregate design take place
PC17.. conduct tests on the modified version of the prototype based on the testing results shared in the version 1 of the testing process
PC18.. maintain records/ version control documents of all changes done during testing of each version of the prototype in the format shared by the cross functional team
Knowledge and Understanding (KU)
The individual on the job needs to know and understand:
KU1. relevant manufacturing and testing standards and procedures followed in the company
KU2. new products manufactured by the company
KU3. internal product standards finalized within the organization
KU4. functional processes like Procurement, Store management, inventory management, quality management and key contact points for query resolution
KU5. quality norms and standards prescribed in the Quality Manual by the organization
KU6. 5S and Safety norms practiced in the organization
KU7. the working of various automobile components
KU8. general working of automobiles and linkage & impact of one parameter to another
KU9. various national and international regulations, norms and standards on vehicles and engine performance regulations related to noise, vibrations, durability, reliability factors for 2 wheeler, 3 wheeler and 4 wheelers under normal and difficult environmental conditions
KU10. various defects related to reliability and durability of the component and impact of the defect on the final component and vehicle performance
KU11. analytical tools like Histogram analysis, Pareto Analysis, Why Why analysis, Process Mapping, Ishikawa ( Fishbone) analysis
KU12. basic laws of physics, chemistry. metallurgy and mathematics
KU13. basic laws of geometry and product design
KU14. how to read and interpret sketches and engineering drawings
KU15. basic documentation rules and procedures
KU16. usage of graphs and pictorial data representation techniques for presentations
KU17. process for filing and storage of reports
Generic Skills (GS)
User/individual on the job needs to know how to:
GS1. document information from the manuals,discussion notes, process charts etc.
GS2. create small notes/ work documents/ diagrams for operators and helpers to help them understand the process
GS3. write inter departmental notes/ memos or make suitable entries in the online system
GS4. read equipment manuals and process documents to understand the equipment and processes better
GS5. read internal information memos send by internal customers ( other functions within the organization)
GS6. discuss task lists, schedules, and work-loads with the operative team members
GS7. answer the queries raised by the operative team as well as intercompany departments
GS8. effectively communicate with the operators and helpers and make them aware of work expectations, targets, policies, processes etc.
GS9. attentively listen with full attention the queries and grievances raised by the operative team and comprehend the information given by the speaker
GS10. communicate effectively to the team members
GS11. identify conflicts in the team and try to resolve them at the earliest
GS12. interact and engage with the team members on a day to day basis
GS13. counsel and coach the operators and help them resolve issues
GS14. timely highlight to the management about any good work/ achievement by the operators and helpers
GS15. break the problem into smaller issues and tasks to arrive at a solution
GS16. understand inter process relationship and establish relationship between various parts of the problem
GS17. leverage experience to find effective solutions to problems
GS18. use basic analytical tools to arrive at solutions
GS19. plan, organize and prioritize the work order and jobs received from the production manager
GS20. manage the schedule plan for the operators and helpers on the line/shift
GS21. validate all process/ equipment manuals so that the final process selected is correct
GS22. organize information, tools, manuals etc. on the shop floor so that sorting becomes easy
GS23. reorganize resources on the line/ shift in case of change of plans
GS24. use common sense and make judgments during day to day basis
GS25. use reasoning skills to identify and resolve problems
GS26. use intuition to detect any potential problems which could arise during operations
GS27. accept additional responsibility for self and the team
GS28. encourage self and other to take greater responsibilities
GS29. ensure that the work allocated to the team is completed as per timelines and quality norms
GS30. identify obstacles and bottlenecks in the process and on own find basic level solutions for removing these obstacles
GS31. motivate and provide support for the team on the shop floor
GS32. encourage collaboration between team members
GS33. resolve team issues and grievances to manage conflicts within the team
GS34. create an environment of approachability, trust and openness within the team
GS35. ensure role clarity for all operators and helpers on the line/ shift
GS36. escalate any team related issues to the concerned person at the right time
GS37. identify defective parts in the manufacturing line by comparing manufactured pieces with the work standard
GS38. link the defect observed with the overall impact on the performance of the component/ automobile
GS39. support and contribute in monitoring and delivering high quality output from self and others
GS40. train team members on maintaining quality standards set by the organization
GS41. exhibit objectivity & openness to others views
GS42. collaborate with stakeholders to achieve the desired state of final result
Assessment Guidelines
- Criteria for assessment for each Qualification Pack will be created by the Sector Skill Council. Each Element/ Performance Criteria (PC) will be assigned marks proportional to its importance in NOS. SSC will also lay down proportion of marks for Theory and Skills Practical for each Element/ PC.
- The assessment for the theory part will be based on knowledge bank of questions created by the SSC.
- Assessment will be conducted for all compulsory NOS, and where applicable, on the selected elective/option NOS/set of NOS.
- Individual assessment agencies will create unique question papers for theory part for each candidate at each examination/training center (as per assessment criteria below).
- Individual assessment agencies will create unique evaluations for skill practical for every student at each examination/ training center based on these criteria.
- To pass the Qualification Pack assessment, every trainee should score the Recommended Pass % aggregate for the QP.
- In case of unsuccessful completion, the trainee may seek reassessment on the Qualification Pack.