Free Aircraft Powerplant Technician course (6months)
Aircraft Powerplant Technician:
Brief Job Description: Aircraft Powerplant Technician is responsible for assembly of engine modules, complete engine, engine accessories and LRU’s.
Personal Attributes: Key attributes for Aircraft Powerplant Technician would include good communication skills, excellent written communication skills and good interpersonal skills with a keen eye for details.
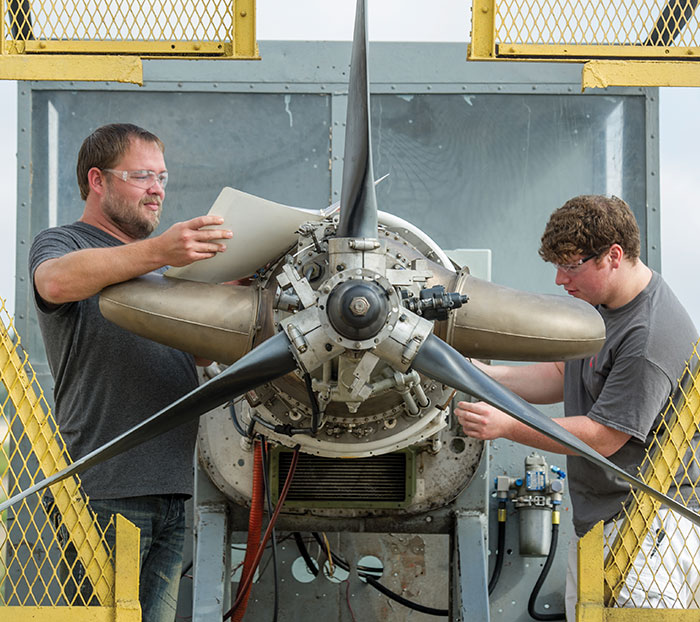
Safety and security procedures:-
Comprehending the safety and security procedures
PC1. comply with the organisation’s safety and security policies and procedures
PC2. comply with the regulatory guidelines on safe conduct of operations and maintenance of conditions to thwart any acts of unlawful interference
PC3. report any identified breaches of safety, and security policies and procedures to the designated person
PC4. coordinate with other resources at the workplace (within and outside the organisation) to achieve safe and secure environment
PC5. identify and mitigate any safety and security hazards like illness, accidents, fires or acts of unlawful interference if it falls within the limits of individual’s authority
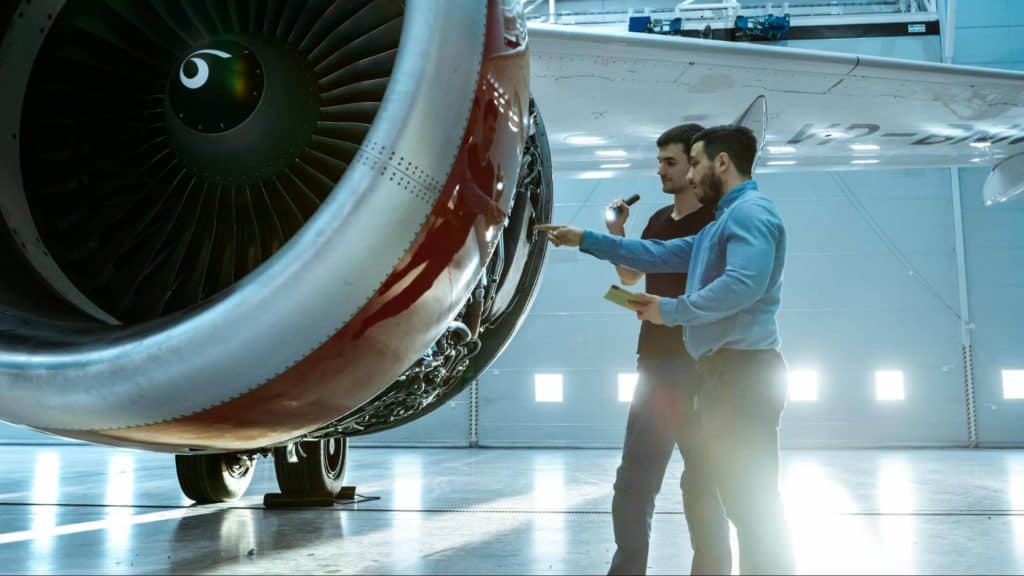
PC6. report any hazards outside the individual’s authority to the relevant person in line with organisational procedures and regulatory guidelines
PC7. follow organisation’s emergency procedures for accidents, fires or acts of unlawful interference
PC8. identify and recommend opportunities for improving health, safety, and security to the designated person
PC9. ensure all health and safety records are updated and procedures are well defined.
Organisational Context:

KA1. hazard identification and risk management as defined within the organisational policy and procedures
KA2. regulatory requirements and organisation’s procedures for maintenance of safety and security standards and individual’s role and responsibilities in relation to this
KA3. how and when to report hazards
KA4. the limits of responsibility for dealing with hazards
KA5. the organisation’s emergency procedures for different emergency situations and the importance of following these
KA6. importance of maintaining high standards of safety and security
KA7. implications that any non-compliance with safety and security may have on individuals and the organisation.
Technical
Knowledge
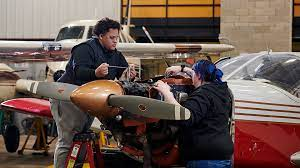
KB1. different types of breaches of safety and security and how and when to report these
KB2. evacuation procedures for workers and passengers
KB3. how to summon medical assistance and the emergency services, where necessary
KB4. how to use the health, safety and accident reporting procedures and the importance of these
KB5. regulatory guidelines on dealing with safety and security emergencies.
Core Skills/ Generic Skills
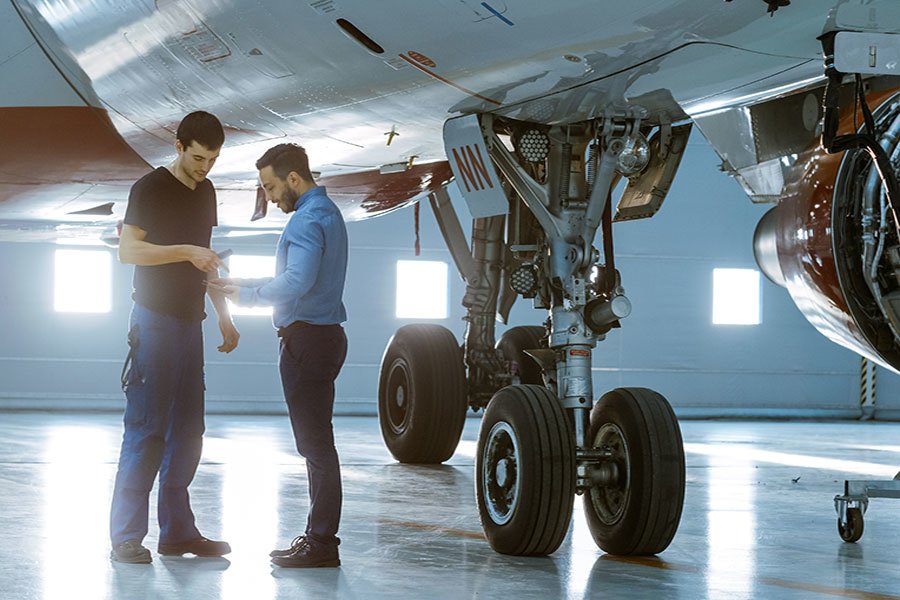
writing Skills |
The user/ individual on the job needs to know and understand how to: SA1. complete accurately a well written report in English language detailing the situations of emergency with attention to detail |
Reading Skills |
The user/individual on the job needs to know and understand how to: SA2. read instructions/guidelines/procedures/rules |
Oral Communication (Listening and Speaking skills) |
The user/individual on the job needs to know and understand how to: SA3. listen to and orally communicate information with all concerned |
Professional Skills |
Decision Making |
The user/individual on the job needs to know and understand how to: SB1. make decisions on a suitable course of action or response if permitted by the authority matrix. Plan and Organize The user/individual on the job needs to know and understand: SB2. monitor efficient functioning of all activities SB3. plan and organize work to achieve targets and deadlines Customer Centricity The user/individual on the job needs to know and understand how to: SB4. communicate with customers and other stakeholders in a courteous manner SB5. maintain cordial work relationship Problem Solving The user/individual on the job needs to know and understand how to: SB6. identify trends/common causes for errors and suggest possible solutions to the supervisor / management SB7. identify and correct errors Analytical Thinking The user/individual on the job needs to know and understand how to: SB8. analyse best possible solutions (cost, time, effort, etc.) suited for operations Critical Thinking The user/individual on the job needs to know and understand how to: SB9. concentrate on task at hand and complete it without errors SB10. apply balanced judgments to different situations. The process of aero-engine assembly/disassembly: Understanding the assembly/disassembly process PC1. understand all types of drawings, sketches and work instructions at the beginning of the assembly/disassembly PC2. understand of geometric dimensions and tolerances PC3. understand the rigs, gauges, standard tools, torque wrenches etc. PC4. understand the basics of aero engine and its parts PC5. understand the various materials, parts and consumables used during assembly/disassembly process PC6. understand the criticality of sub-assemblies of an aero engine. PC7. understand the right assembly/disassembly methodology and various process parameters like torque application, fitting tolerances, bolting and fastening as mentioned in the work instruction/organisation maintenance manuals PC8. understand 5 S related to the work area PC9. while understanding the drawings and sketches,he/she must ensure that the observed problems are highlighted to concerned supervisor PC10. understand the changes which may happen from time to time in assembly/disassembly process based on the approved engine configuration PC11. red flagging of the deviations during the assembly of engine and raising it to concerned supervisor/Quality Inspectors. Organisational Context KA1. relevant standards and procedures followed in the organisation KA2. different types of aero-engines KA3. different types of manuals containing work related information KA4. 5S and safety norms practiced in the organisation Technical Knowledge KB1. how to read engineering drawings, sketches, process sheet etc. KB2. geometrical dimensioning and tolerance limits KB3. use of standard tools like torque wrenches, spanners, sockets etc. KB4. use of standard measuring instruments like dial gauges, comparators, bore gauges, passometers, vernier callipers, slip gauges etc KB5. different types of assembling processes like fitting, bolting, torquing, tightening etc. KB6. basic computer knowledge for verifying the drawings KB7. basic knowledge regarding quality management KB8. basic principles of 5S manufacturing-cleaning, sorting, scrap handling etc. Core Skills/ Generic Skills Writing Skills The user/ individual on the job needs to know and understand how to: SA1. document the available information SA2. note down observations in the given format SA3. write information documents to concerned departments/teams under guidance of supervisor SA4. enter the information in Inspection record sheets, relevant registers etc. Reading Skills The user/individual on the job needs to know and understand how to: SA5. read and interpret engineering drawings, sketches and symbols used SA6. read the organisation/manufacturer manuals and process documents Oral Communication (Listening and Speaking skills) The user/individual on the job needs to know and understand how to: SA7. effectively discuss and communicate regarding targets, activities, processes etc with supervisor and co-workers SA8. question supervisor in order to understand the nature of problem Professional Skills Decision Making The user/individual on the job needs to know and understand how to: SB1. make decisions on a suitable course of action or response if permitted by the authority matrix Plan and Organize The user/individual on the job needs to know and understand how to: SB2. plan, organise and prioritise the job received from the production manager SB3. validate all the process/equipment manuals so that the final process selection is correct SB4. support the supervisor in scheduling tasks for timely completion of the job Customer Centricity The user/individual on the job needs to know and understand how to: SB5. communicate with stakeholders in a courteous manner SB6. maintain cordial working relationship Problem Solving The user/individual on the job needs to know and understand how to: SB7. recognise a work place problem or a potential problem and take action SB8. determine problems needing priority action SB9. gather information and provide assistance as required to solve problems SB10. refer problems outside area of responsibility to approach person SB11. make decision in emergency conditions in case supervisor is not available Analytical Skills The user/individual on the job needs to know and understand how to: SB12. analyse best possible solutions (cost, time, effort, etc.) suited for operations Critical Thinking The user/individual on the job needs to know and understand how to: SB13. analyse, evaluate and apply information gathered from observation, experience, reasoning or communication to act efficiently Assembly/disassembly of aero-engine Performance Criteria Disas semble aero-engine modules into piece parts PC1. receive the modules at the workshop area and perform visual inspection of the modules to identify defects PC2. receive the documentation received with the modules to ensure that all relevant deta ils are filled in the documents as per regulatory/organisational policies and procedures PC3. install the modules on the disassembly rig and perform diassembly of the modules into piece parts PC4. visually inspect the disassembled piece parts and record the defects observed on the piece parts to ascertain if the defects are within acceptable limits to certify airworthiness of the piece parts PC5. tag the piece parts with the appropriate tags and ensure all relevant information is filled as per regulatory/organisation policy and procedures PC6. dispatch the piece parts to the relevant component shops for inspection and repair as deemed necessary Perform assembly of aero engine modules PC7. receive the components and piece parts from the component shops and perform visual inspection to ensure no defects on the received parts PC8. ensure that defects, if any , are within the airworthiness limits for module assembly PC9. inspect and verify the airworthiness tags issued by the component shops and ensure that the tags are in line with regulatory/organisational policies and procedures PC10. install the components and piece parts on the module assembly rig PC11. perform assembly of the module PC12. visually inspect the module post assembly to ensure that there are no defects on the module beyond the airworthiness requirements PC13. issue the documentation and relavent tags for the module and dispatch the module for final engine assembly Knowledge and Understanding Organisational Context KA1. relevant standards and procedures followed in the organisation KA2. different types of aero-engines KA3. different types of manuals containing work related information KA4. 5S and safety norms practiced in the organisation Technical Knowledge KB1. how to read engineering drawings, sketches, process sheet etc. KB2. geometrical dimensioning and tolerance limits KB3. use of standard tools like torque wrenches, spanners, sockets etc. KB4. use of standard measuring instruments like dial gauges, comparators, bore gauges, passometers, vernier callipers, slip gauges etc. KB5. different types of assembling processes like fitting, bolting, torquing, tightening etc. KB6. basic computer knowledge for verifying the drawings KB7. basic knowledge regarding quality management KB8. basic principles of 5S manufacturing-cleaning, sorting, scrap handling etc Core Skills/ Generic Skills Writing Skills The user/ individual on the job needs to know and understand how to: SA1. document the available information SA2. note down observations in the given format SA3. write information documents to concerned departments/teams under guidance of supervisor SA4. enter the information in Inspection record sheets, relevant registers etc. Reading Skills The user/individual on the job needs to know and understand how to: SA5. read and interpret engineering drawings, sketches and symbols used SA6. read the organisation/manufacturer manuals and process documents Oral Communication (Listening and Speaking skills) The user/individual on the job needs to know and understand how to: SA7. effectively discuss and communicate regarding targets, activities, processes etc with supervisor and co-workers SA8. question supervisor in order to understand the nature of problem Professional Skills Decision Making The user/individual on the job needs to know and understand how to: SB1. make decisions on a suitable course of action or response if permitted by the authority matrix Plan and Organize The user/individual on the job needs to know and understand how to: SB2. plan, organise and prioritise the job received from the production manager SB3. validate all the process/equipment manuals so that the final process selection is correct SB4. support the supervisor in scheduling tasks for timely completion of the job Customer Centricity The user/individual on the job needs to know and understand how to: SB5. communicate with stakeholders in a courteous manner SB6. maintain cordial working relationship Problem Solving The user/individual on the job needs to know and understand how to: SB7. recognize a work place problem or a potential problem and take action SB8. determine problems needing priority action SB9. gather information and provide assistance as required to solve problems SB10. refer problems outside area of responsibility to approach person SB11. make decision in emergency conditions in case supervisor is not available Analytical Skills The user/individual on the job needs to know and understand how to: SB12. analyse best possible solutions (cost, time, effort, etc.) suited for operations Critical Thinking The user/individual on the job needs to know and understand how to: SB13. analyse, evaluate and apply information gathered from observation, experience, reasoning or communication to act efficiently Aero engine module disassembly/assembly Performance Criteria Disassemble aero-engine into modules PC1. perform visual inspection of the bare assembled engine and record the visual findings on the engine PC2. perform fuel and oil draining procedure on the engine prior to disassembly as per the procedures detailed in the job cards/manufacturer manuals/organisation maintenance manuals PC3. remove the engine accessories installed on the engine cases as per the procedures detailed in the job cards/manfacturer manuals/organisation maintenance manuals PC4. perform disassembly of the engine into its modules as per manufacturer manuals and organisation maintenance manuals PC5. ensure blanking is performed on all required areas to prevent an foreign object entering the modules, accessories and LRU’s PC6. perform visual inspection of the modules and record the visual findings on the modules PC7. tag the modules with the relevant information as required under regulatory/organisational policies and procedures PC8. dispatch the modules to the appropriate module shops for further disassembly PC9. dispatch the accessories and other LRU’s to the respective component shops for testing and repair with appropriate tags Perform assembly of aero engine, accessories and LRU’s PC10. receive the modules from the respective modular shops and perform visual inspection on the modules to certify airworthiness of the modules PC11. inspect the documentation received along with the modules to ensure completeness of the documentation in respect to airworthiness requirements set forth by regulator/organisational policy and procedures PC12. assemble the modules in sequence as detailed in the job card/manufacturer manuals/organisation maintenance manuals PC13. visually inspect the assembled modules to ensure no damage has occurred during assembly. PC14. inspect and verify if any damage found is acceptable withint the airworthiness limits for engine operations PC15. receive engine acessories and LRU’s from the component shops and inspect and verify that the accessories and LRU’s are airworthy to be installed on the engine PC16. inspect the documentation received along with the modules to ensure completeness of the documentation in respect to airworthiness requirements set forth by regulator/organisational policy and procedures PC17. install the accessories and LRU’s in sequence as detailed in the job card/manufacturer manuals/organisa tion maintenance manuals PC18. visually inspect the installed accessories and LRU’s to ensure no damage has occurred during installation. PC19. inspect and verify if any damage found is acceptable withint the airworthiness limits for engine operations PC20. dispatch the assembled engine to the engine test cell Knowledge and Understanding Organisational Context KA1. relevant standards and procedures followed in the organisation KA2. different types of aero-engines KA3. different types of manuals containing work related information KA4. 5S and safety norms practiced in the organisation Technical Knowledge KB1. how to read engineering drawings, sketches, process sheet etc. KB2. geometrical dimensioning and tolerance limits KB3. use of standard tools like torque wrenches, spanners, sockets etc. KB4. use of standard measuring instruments like dial gauges, comparators, bore gauges, passometers, vernier callipers, slip gauges etc. KB5. different types of assembling processes like fitting, bolting, torquing, tightening etc. KB6. basic computer knowledge for verifying the drawings KB7. basic knowledge regarding quality management KB8. basic principles of 5S manufacturing-cleaning, sorting, scrap handling etc. Core Skills/ Generic Skills Writing Skills The user/ individual on the job needs to know and understand how to: SA1. document the available information SA2. note down observations in the given format SA3. write information documents to concerned departments/teams under guidance of supervisor SA4. enter the information in Inspection record sheets, relevant registers etc. Reading Skills The user/individual on the job needs to know and understand how to: SA5. read and interpret engineering drawings, sketches and symbols used SA6. read the organisation/manufacturer manuals and process documents Oral Communication (Listening and Speaking skills) The user/individual on the job needs to know and understand how to: SA7. effectively discuss and communicate regarding targets, activities, processes etc with supervisor and co-workers SA8. question supervisor in order to understand the nature of problem Professional Skills Decision Making The user/individual on the job needs to know and understand how to: SB1. make decisions on a suitable course of action or response if permitted by the authority matrix Plan and Organize The user/individual on the job needs to know and understand how to: SB2. plan, organise and prioritise the job received from the production manager SB3. validate all the process/equipment manuals so that the final process selection is correct SB4. support the supervisor in scheduling tasks for timely completion of the job Customer Centricity The user/individual on the job needs to know and understand how to: SB5. communicate with stakeholders in a courteous manner SB6. maintain cordial working relationship Problem Solving The user/individual on the job needs to know and understand how to: SB7. recognize a work place problem or a potential problem and take action SB8. determine problems needing priority action SB9. gather information and provide assistance as required to solve problems SB10. refer problems outside area of responsibility to approach person SB11. make decision in emergency conditions in case supervisor is not available Analytical Skills The user/individual on the job needs to know and understand how to: SB12. analyse best possible solutions (cost, time, effort, etc.) suited for operations Critical Thinking The user/individual on the job needs to know and understand how to: SB13. analyse, evaluate and apply information gathered from observation, experience, reasoning or communication to act efficiently Prevent FOD during engine assembly/disassembly Performance Criteria Prevent FOD during assembly/disassembly PC1. ensure the availability of blanking, cover etc. at the work place PC2. ensure that no FOD is available near the assembly/disassembly area PC3. ensure proper availability of tools, fixtures and parts PC4. ensure proper accounting of material and tools used during assembly/diassembly PC5. ensure all the open cavities are properly blanked/ covered after the completion of work Knowledge and Understanding Organisational Context KA1. relevant standards and procedures followed in the Company KA2. different types of aero-engines KA3. different types of assembly/disassembly processes KA4. quality management practices of the organisation KA5. 5S and Safety norms practiced in the organization Technical Knowledge KB1. how to read and interpret engineering drawings, sketches, process sheet etc. KB2. different types of FOD’s that can occur at the workplace KB3. how to use machine manuals and the standard measuring instruments and gauges KB4. how to read and interpret the standard measuring instruments and gauges KB5. how to use lifting tools like hoists, cranes, clamps etc. KB6. basic computer knowledge for verifying the Drawings KB7. basic knowledge regarding quality management KB8. basic principles of 5S manufacturing-cleaning, sorting, scrap handling etc. Core Skills/ Generic Skills Writing Skills The user/ individual on the job needs to know and understand how to: SA1. document the available information SA2. note down observations (if any) in the given format SA3. write information documents to concerned departments/teams under guidance of supervisor SA4. enter the information in online ERP systems under guidance of the supervisor Reading Skills The user/individual on the job needs to know and understand how to: SA5. read and interpret engineering drawings, sketches and symbols used in both SA6. read and understand various tolerances and technical specifications of the product SA7. read the equipment manuals and process documents SA8. read and interpret technical customer drawings Oral Communication (Listening and Speaking skills) The user/individual on the job needs to know and understand how to: SA9. effectively discuss and communicate regarding Targets, activities, processes etc. with supervisor and co-workers SA10. question supervisor in order to understand the nature of problem Professional Skills Decision Making The user/individual on the job needs to know and understand: SB1. make decisions on a suitable course of action or response if permitted by the authority matrix Plan and Organize The user/individual on the job needs to know and understand: SB2. plan, organise and prioritise the job received from the Production Manager SB3. validate all the process/equipment manuals so that the final process selected is correct SB4. support the supervisor in scheduling tasks for tool and die making Customer Centricity The user/individual on the job needs to know and understand:SB5. communicate with stakeholders in a courteous manner SB6. maintain cordial work relationship Problem Solving The user/individual on the job needs to know and understand how to: SB5. recognise a work place problem or a potential problem and take action SB6. determine problems needing priority action SB7. gather information and provide assistance as required to solve problems SB8. refer problems outside area of responsibility to approach person SB9. make decision in emergency conditions in case of supervisor are not available Analytical Thinking The user/individual on the job needs to know and understand how to: SB10. analyse best possible solutions (cost, time, effort, etc.) suited for operations Critical Thinking The user/individual on the job needs to know and understand how to: SB11. analyse, evaluate and apply information gathered from observation, experience, reasoning or communication to act efficiently Maintain 5S at the work premises Performance Criteria Ensure sorting PC1. follow the sorting process and check that the tools, fixtures and jigs that are lying on workstations are the ones in use and un- necessary items are not cluttering the workbenches or work surfaces. PC2. ensure segregation of waste in hazardous/ non Hazardous waste as per the sorting work instructions PC3. follow the technique of waste disposal and waste storage in the proper bins as per SOP PC4. segregate the items which are labeled as red tag items for the process area and keep them in the correct places PC5. sort the tools/ equipment/ fasteners/ spare parts as per specifications/ utility into proper trays, cabinets, lockers as mentioned in the 5S guidelines/ work instructions PC6. ensure that areas of material storage areas are not overflowing PC7. properly stack the various types of boxes and containers as per the size/ utility to avoid any fall of items/ breakage and also enable easy sorting when required PC8. return the extra material and tools to the designated sections and make sure that no additional material/ tool is lying near the work area PC9. follow the floor markings/ area markings used for demarcating the various sections in the plant as per the prescribed instructions and standards Ensure proper documentation and storage (organizing, streamlining PC10. follow the proper labeling mechanism of instruments/ boxes/ containers and maintaining reference files/ documents with the codes and the lists PC11. check that the items in the respective areas have been identified as broken or damaged PC12. follow the given instructions and check for labeling of fluids, oils. Lubricants, solvents, chemicals etc. and proper storage of the same to avoid spillage, leakage, fire etc. PC13. make sure that all material and tools are stored in the designated places and in the manner indicated in the 5S instructions Ensure cleaning of self and the work place PC14. check whether safety glasses are clean and in good condition PC15. keep all outside surfaces of recycling containers are clean PC16. ensure that the area has floors swept, machinery clean and generally clean. In case of cleaning, ensure that proper displays are maintained on the floor which indicate potential safety hazards PC17. check whether all hoses, cabling & wires are clean, in good condition and clamped to avoid any mishap or mix up PC18. ensure workbenches and work surfaces are clean and in good condition PC19. follow the cleaning schedule for the lighting system to ensure proper illumination PC20. store the cleaning material and equipment in the correct location and in good condition PC21. ensure self-cleanliness – clean uniform, clean shoes, clean gloves, clean helmets, personal hygiene Ensure sustenance PC22. follow the daily cleaning standards and schedules to create a clean working environment PC23. attend all training programs for employees on 5S PC24. support the team during the audit of 5S PC25. participate actively in employee work groups on 5S and encourage team members for active participation PC26. follow the guidelines for What to do and What not to do to build sustainability in 5S as mentioned in the 5S check lists/ work instructions Knowledge and Understanding Organisational Context KA1. relevant standards, procedures and policies related to 5S followed in the company Technical Knowledge KB1. have basic knowledge of 5S procedures KB2. know various types 5S practices followed in various areas KB3. understand the 5S checklists provided in the department/ team KB4. have skills to identify useful & non useful items KB5. have knowledge of labels , signs & colours used as indicators KB6. have knowledge on how to sort and store various types of tools, equipment, material etc. KB7. how to identify various types of waste products KB8. understand the impact of waste/ dirt/ dust/unwanted KB9. substances on the process/ environment/ machinery/ human body KB10. have knowledge of best ways of cleaning & waste disposal KB11. understand the importance of standardization in processes KB12. understand the importance of sustainability in 5S KB13. have knowledge of TQM process KB14. have knowledge of various materials and storage norms KB15. understand visual controls, symbols, graphs etc. Core Skills/ Generic Skills Writing Skills The user/ individual on the job needs to know and understand how to: SA1. write basic level notes and observations SA2. note down observations (if any) related to the process SA3. write information documents to internal departments/ internal teams Reading Skills The user/individual on the job needs to know and understand how to: SA4. read 5S instructions put up across the plant premises Oral Communication (Listening and Speaking skills) The user/individual on the job needs to know and understand how to: SA5. effectively communicate information to team members inform employees in the plant and concerned functions about 5S SA6. question the process head in order to understand the 5S related issues SA7. attentively listen with full attention and comply with the information given by the speaker during 5S training programs Professional Skills Thinking The user/individual on the job needs to know and understand how to: SB1. use common sense and make judgments during day to day basis SB2. use reasoning skills to identify and resolve basic problems using 5S Persuasion The user/individual on the job needs to know and understand: SB3. persuade co-team members to follow 5S SB4. ensure that the co team members understand the importance of using 5S tool Creativity The user/individual on the job needs to know and understand: SB5. use innovative skills to perform and manage 5S activities at the work desk and the shop floor SB6. exhibit inquisitive behavior to seek feedback and question on the existing set patterns of work Self-Discipline The user/individual on the job needs to know and understand how to: SB7. do what is right, not what is a popular practices SB8. follow shop floor rules& regulations and avoid deviations; make 5S an integral way of life SB9. ensure self-cleanliness on a daily basis SB10. demonstrate the will to keep the work area in a clean and orderly manner Model Curriculum Aircraft Powerplant T echnician: Follow safety and security procedures comprehend the organisation’s safety and security policies and procedures comprehend the regulatory guidelines on safe conduct of operations and main tenance of conditions to thwart any acts of unlawful interference report any identified breaches of safety, and security policies and procedures to the designated person coordinate with other resources at the workplace (within and outside the organization) to achieve safe and secure environment identify and mitigate any safety and security hazards like illness, accidents, fires or acts of unlawful interference if it falls within the limits of individual’s authority report any hazards outside the individual’s authority to the relevant person in line with organisational procedures and regulatory guidelines follow organisation’s emergency procedures for accidents, fires or acts of unlawful interference identify and recommend opportunities for improving health, safety, and security to the designated person complete all health and safety records are updates and procedures well defined Understand the process of aero engine assembly understand all types of drawings, sketches and work instructions at the beginning of the assembly/disassembly understand of geometric dimensions and tolerances understand the rigs, gauges, standard tools, torque wrenches etc. understand the basics of aero engine and its parts understand the various materials, parts and consumables used during assembly/disassembly process understand the criticality of sub-assemblies of an aero engine understand the right assembly/disassembly methodology and various process parameters like torque application, fitting tolerances, bolting and fastening as mentioned in the work instruction/organisation maintenance manuals understand 5 S related to the work area while understanding the drawings and sketches,he/she must ensure that the observed problems are highlighted to concerned supervisor understand the changes which may happen from time to time in assembly/disassembly process based on the approved engine configuration red flagging of the deviations during the assembly of engine and raising it to concerned supervisor/Quality Inspectors Assembly/disassembly of aero-engine receive the modules at the workshop area and perform visual inspection of the modules to identify defects receive the documentation received with the modules to ensure that all relevant details are filled in the documents as per regulatory/organisational policies and procedures install the modules on the dis-assembly rig and perform dis-assembly of the modules into piece parts visually inspect the disassembled piece parts and record the defects observed on the piece parts to ascertain if the defects are within acceptable limits to certify airworthiness of the piece parts tag the piece parts with the appropriate tags and ensure all relevant information is filled as per regulatory/organisation policy and procedures dispatch the piece parts to the relevant component shops for inspection and repair as deemed necessary To be competent, the user/individual on the job must be able to: receive the components and piece parts from the component shops and perform visual inspection to ensure no defects on the received parts if any defects found, ensure that the defects are within the airworthiness limits for module assembly inspect and verify the airworthiness tags issued by the component shops and ensure that the tags are in line with regulatory/organisational policies and procedures install the components and piece parts on the module assembly rig perform assembly of the module visually inspect the module post assembly to ensure that there are no defects on the module beyond the airworthiness requirements issue the documentation and relevant tags for the module and dispatch the module for final engine assembly Perform aero-engine module disassembly/assembly perform visual inspection of the bare assembled engine and record the visual findings on the engine perform fuel and oil draining procedure on the engine prior to disassembly as per the procedures detailed in the job cards/manufacturer manuals/organisation maintenance manuals remove the engine accessories installed on the engine cases as per the procedures detailed in the job cards/manfacturer manuals/organisation maintenance manuals perform disassembly of the engine into its modules as per manufacturer manuals and organisation maintenance manuals ensure blanking is performed on all required areas to prevent an foreign object entering the modules, accessories and LRU’s perform visual inspection of the modules and record the visual findings on the modules tag the modules with the relevant information as required under regulatory/organisational policies and procedures dispatch the modules to the appropriate module shops for further disassembly dispatch the accessories and other LRU’s to the respective component shops for testing and repair with appropriate tags To be competent, the user/individual on the job must be able to: receive the modules from the respective modular shops and perform visual inspection on the modules to certify airworthiness of the modules inspect the documentation received along with the modules to ensure completeness of the documentation in respect to airworthiness requirements set forth by regulator/organisational policy and procedures assemble the modules in sequence as detailed in the job card/manufacturer manuals/organisation maintenance manuals visually inspect the assembled modules to ensure no damage has occurred during assembly. If any damage found, inspect and verify if the damage is acceptable within the airworthiness limits for engine operations receive engine accessories and LRU’s from the component shops and inspect and verify that the accessories and LRU’s are airworthy to be installed on the engine inspect the documentation received along with the modules to ensure completeness of the documentation in respect to airworthiness requirements set forth by regulator/organisational policy and procedures install the accessories and LRU’s in sequence as detailed in the job card/manufacturer manuals/organisation maintenance manuals visually inspect the installed accessories and LRU’s to ensure no damage has occurred during installation. If any damage found, inspect and verify if the damage is acceptable within the airworthiness limits for engine operations dispatch the assembled engine to the engine test cell Prevention of FOD during engine assembly/disassembly ensure the availability of blanking, cover etc. at the work place ensure that no FOD is available near the assembly/disassembly area ensure proper availability of tools, fixtures and parts ensure proper accounting of material and tools used during assembly/disassembly ensure all the open cavities are properly blanked/ covered after the completion of work Maintain 5S at the work premises follow the sorting process and check that the tools, fixtures & jigs that are lying on workstations are the ones in use and un- necessary items are not cluttering the workbenches or work surfaces. ensure segregation of waste in hazardous/ non Hazardous waste as per the sorting work instructions follow the technique of waste disposal and waste storage in the proper bins as per SOP segregate the items which are labeled as red tag items for the process area and keep them in the correct places sort the tools/ equipment/ fasteners/ spare parts as per specifications/ utility into proper trays, cabinets, lockers as mentioned in the 5S guidelines/ work instructions ensure that areas of material storage areas are not overflowing properly stack the various types of boxes and containe rs as per the size/ utility to avoid any fall of items/ breakage and also enable easy sorting when required return the extra material and tools to the designated sections and make sure that no additional material/ tool is lying near the work area follow the floor markings/ area markings used for demarcating the various sections in the plant as per the prescribed instructions and standards follow the proper labeling mechanism of instruments/ boxes/ containers and maintaining reference files/ documents with the codes and the lists check that the items in the respective areas have been identified as broken or damaged follow the given instructions and check for labeling of fluids, oils, lubricants, solvents, chemicals etc. and proper storage of the same to avoid spillage, leakage, fire etc. make sure that all material and tools are stored in the designated places and in the manner indicated in the 5S instructions check whether safety glasses are clean and in good condition keep all outside surfaces of recycling containers are clean ensure that the area has floors swept, machinery clean and generally clean. In case of cleaning, ensure that proper displays are maintained on the floor which indicate potential safety hazards check whether all hoses, cabling & wires are clean, in good condition and clamped to avoid any mishap or mix up ensure workbenches and work surfaces are clean and in good condition follow the cleaning schedule for the lighting system to ensure proper illumination store the cleaning material and equipment in the correct location and in good condition ensure self-cleanliness – clean uniform, clean shoes, clean gloves, clean helmets, personal hygiene follow the daily cleaning standards and schedules to create a clean working environment attend all training programs for employees on 5S support the team during the audit of 5 S participate actively in employee work groups on 5S and encourage team members for active participation follow the guidelines for What to do and What not to do to build sustainability in 5S as mentioned in the 5S check lists/ work instructions Unique equipment used; Cut-out model of a typical aero engine Ground Power Unit (GPU) Fire extinguisher Aircraft engine hoists Performing aerospace welding operations ensure wearing of Personnel Protective Equipment (PPE) that suits the task such as flame-resistant aprons, safety helmet & hand shields, ear plugs, footwear, safety goggles etc. comply with organisations Occupational Health & Safety (OHS) standards ensure that work area around the welding transformer, gas discharge unit, flux wire are clean as mentioned in the work instruction / Standard Operating Procedure (SOP) of organisation ensure that the welding work area is not around explosives or ignitable material and adequate ventilation is available for exhaust of fumes and gases check for correctness of power, coolant and operating parts of the machine escalate any queries to the supervisor ensure that the required welding material (electrodes, flux wire etc) is issued from the stores setup welding equipment as per selected welding process or approved Welding Procedure Specification (WPS) and Procedure Qualification Records (PQR) ensure work piece / test piece are clean from burrs prepare the edge of work piece / test piece as per the approved drawing specification and welding procedures ensure appropriate clamps, jigs and fixtures are available to hold the work piece / test piece to be welded select appropriate wire / electrode as per engineering drawings, type of welding joints or approved WPS & PQR select appropriate gas, pressure, amperage and voltage as per approved WPS & PQR perform the required welding process / technique on a test coupon as per approved WPS and PQR in the presence of supervisor, client or under supervision of third party approver get the test coupon approval for welding positions from supervisor, client or by third party approver assist supervisor in maintaining a log book with name, approved certificate no., approved welding position etc. select appropriate wire / electrode as per engineering drawings, type of welding joints or approved WPS & PQR select appropriate gas, pressure, amperage and voltage as per approved WPS & PQR register the work piece / section to be welded to the shop supervisor understand the fabrication tolerances, root gap, hot pass margins as per the welding specification and approved WPS & PQR for type of weld joint perform tag welding to the work piece and obtain approval from supervisor perform full weld as per WPS & PQR and avoid over welding finish the surface by filing, brushing etc. inform supervisor about completion and perform self-check of the finished output and send it for the next process as per instructions Unique equipment used; Gas cylinder Safety gagets (gloves, apron, goggles, nose mask & ear plugs) Welding helmets TIG welding machine, with foot pedal Special Tool Kit Mechanical tool box Welding material (Inconel & SS321) Fillet Guidelines for Assessment Criteria for assessment for each Qualification Pack will be created by the Sector Skill Council. Each Performance Criteria (PC) will be assigned marks proportional to its importance in NOS. SSC will also lay down proportion of marks for Theory and Skills Practical for each PC. The assessment for the theory part will be based on knowledge bank of questions created by the SSC. Assessment will be conducted for all compulsory NOS, and where applicable, on the selected elective/option NOS/set of NOS. Individual assessment agencies will create unique question papers for theory part for each candidate at each examination/training center (as per assessment criteria below Individual assessment agencies will create unique evaluations for skill practical for every student at each examination/training center based on this criterion. To pass the Qualification Pack , every trainee should score a minimum of 70% of aggregate marks to successfully clear the assessment. In case of unsuccessful completion, the trainee may seek reassessment on the Qualification Pack. |