Agriculture Machinery Demonstrator
Agriculture Machinery Demonstrator
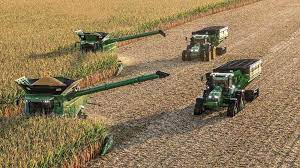
The Agricultural Equipment Supervisor handles the farmers who demonstrate and train the equipment used in agricultural processes such as plowing, sowing, irrigation, crop protection, harvesting, post-harvest equipment, etc. A brief description of the work is the operation of agricultural machinery such as tractors, power tillers, disc plows, harrows, seed drills, planters, irrigation systems, harvesting and rear harvesting machines and their advantages in agricultural operations. Your Qualifications: The Agricultural Equipment Supervisor must be able to work and make various career decisions in his or her workplace. He must have the ability to repair and the basic acumen of agricultural machinery. One should have the ability to read, write, communicate, analyze and communicate.
Carry out pre-training preparations Agriculture Machinery Demonstrator:
In order to be effective, each user / individual must be able to: PC1. identify the exhibits / kisaeng meals planned in the area / region PC2. ensure the completion of various types of PC3 displays. configure demonstration-based calendar training / demonstrations Perform initial demonstration tests In order to be effective, user / individual must be able to: PC4. collect books related to equipment such as hand operator, PC5 handheld. to collect literature on new developments in the field of farm machinery PC6. ensure the availability of all the tools and equipment required for PC7 displays. ensure the availability of all resources and resources such as audio – visual aids, security devices, etc. required for PC8 display. ensure the availability of experts who assist with exhibitions Agriculture Machinery Demonstrator.
Organizational Context (Knowledge of the company / organization and its processes) Agriculture Machinery Demonstrator:
The user / person at work needs to know and understand: KA1. business code of conduct KA2. job and employment obligations KA3. standard tools and procedures for training KA4. organizational pre-screening methods
Technical knowledge:
The user / person at work needs to know and understand: KB1. various exhibitions / kisaeng food taking place in the KB2 region. farmer distribution of areas and a map of the area around KB3. process of attending kisaeng shows / meals KB4 KB4. various tools and visual aids KB5. the importance of audio viewing tools in the KB6 display. various tools and equipment required for periodic maintenance and small repair equipment for farm equipment KB7. advances in the field of farm machinery KB8. hazardous machinery (law), law 1983 Agriculture Machinery Demonstrator.
Core Skills/ Generic Skills:
The user / person at work needs to know and understand how to do this: SA1. note the location and time of the shows / meals SA2. adjust the training calendar according to the SA3 shows. complete entry forms for Learning Skills The user / employee needs to know and understand how to do this: SA4. read and interpret operators and SA5 equipment maintenance manuals. read and translate publications on new developments in the field of farm machinery SA6. read and translate electronic security manual Oral communication (listening and speaking skills) The user / person at work needs to know and understand how to do this: SA7. liaising with experts and other members of the SA8 team. liaising with exhibition managers / kisaeng meals B. Making Professional Skills Decision The user / employee needs to know and understand: SB1. has decided on the display method to be used by SB2. determine the tools, equipment and resources required for the Display and Planning Program The user / person at work needs to know and understand: SB3. plan a training schedule in advance to ensure SB4 readiness. arrange for the availability of resources such as books, tools and experts Customer Centricity Customer / employee needs to know and understand how to do this: SB5. understand customer needs and priorities and choose the right way to demonstrate Problem Solving The user / employee needs to know and understand: SB6. manage last minute change in system and configure SB7. edit other resources in the event of a last-minute change Analytical Thinking The user / person at work needs to know and understand how to do this: SB8. use background information and audience comprehension, equipment and a variety of display options to select the most appropriate SB9 form. use background information about equipment and display types to select the most suitable services Key considerations The user / employee needs to know and understand: SB10. use common sense and make daily decisions Agriculture Machinery Demonstrator.
Perform demonstration of operations of farm equipment and machinery Agriculture Machinery Demonstrator:
His unit / work includes the following: Proof of operation and explain the main advantages of tractors and power springs Prove operation and explain the main advantages of farm-powered agricultural machinery, sowing, crop protection, harvesting and threshing Prove operation and explain the main advantages of pumping and dripping Scope Element Performance Criteria Prove performance and explain the key benefits of tractors and electric tillers In order to be effective, the user / individual must be able to make PC1. describe the functions, uses and significant benefits of tractors, electric tillers, engines and electric motors and their PC2 systems. explain to farmers the terms of construction of tractors and power tillers with a different combination of PC3 equipment. verify the performance of tractors and power tillers PC4. explain the basic considerations to consider when choosing a tractor and other attachments / associated equipment Prove the operation and explain the key benefits of farm-powered farming equipment, sowing, crop protection, harvesting and threshing In order to be effective, each user / individual must know PC5. explain to farmers the principles of agricultural construction, planting, crop protection, harvesting and threshing PC6 equipment. describe the functions, uses and main benefits of disk plow, disc harrows, growers, seed drill, sprayer & dusters, harvesters and harvesters, rice packaging rice PC7. demonstrate the operation of electric farm machinery, tractor machinery, electric tiller machinery and other machinery Demonstrate the operation and explain the main advantages of water pumping and pumping system equipment In order to be effective, each user / individual must be able to PC8. explain the principles for the construction of water lift devices and PC9 spraying. describe the functions, uses and significant benefits of spraying and irrigation systems, water pumps and equipment PC10. describe the installation and operation of irrigation systems Agriculture Machinery Demonstrator
Organizational Context (Knowledge of the company / organization and its processes):
The user / person at work needs to know and understand: KA1. business code of conduct KA2. job and employment obligations KA3. standard operating procedures for demonstrating KA4 performance. information sharing processes
Technical Knowledge: The user / person at work needs to know and understand: KB1. benefits of all types of machinery, electric tillers, tractors etc. KB2. operation of farm tractors, agricultural machinery, electric power, diesel engine, pumps, etc. KB3. operation and construction of irrigation systems and water supply systems KB4. operation and design of post-harvest equipment such as cutter, cane cane KB5. hazardous machinery (law), law 1983
Core Skills/ Generic Skills:
The user / person at work needs to know and understand how to do this: SA1. prepare lessons in a visual and understandable way for SA2. describe functionality and design using blackboard SA3. prepare detailed reports during training Learning Skills The user / employee needs to know and understand how to do this: SA4. read and interpret manuals required from periodic maintenance of SA5 equipment. read and understand the security manual Oral Communication (listening and speaking skills) The user / person at work needs to know and understand how to do this: SA6. communication with farmers in the local language SA7. communicate the importance of safety and periodic maintenance SA8. listen to workers, team members and farmers to know and understand their work-related problems B. Creating Professional Skills Making a user / employee need to know and understand that: SB1. has decided on the display method to be used by SB2. determine the tools, equipment and resources required for display The user / employee needs to know and understand: SB3. schedule SB4 training sessions in advance. arrange for the availability of resources such as books, tools and experts Customer Centricity Customer / employee needs to know and understand how to do this: SB5. understand customer needs and priorities and choose the appropriate SB6 display method. describe language training courses for farmers who are most comfortable with problem solving The user / employee needs to know and understand: SB7. manage last minute change in system and configure SB8. edit other resources in case of change at the last minute SB9. manage customer queries and take appropriate steps for Analytical Thinking The user / employee needs to know and understand: SB10. use background information and audience comprehension, equipment and a variety of display options to select the most appropriate SB11 form. use background information about equipment and display types to select the most suitable resources Key considerations The user / employee needs to know and understand: SB12. use common sense and make daily decisions Agriculture Machinery Demonstrator
Demonstrate minor repair and maintenance works and safety procedures Agriculture Machinery Demonstrator:
In order to be effective, each user / individual must be able to: PC1. describe the management and use of working tools and PC2 measurement equipment. describe the process for monitoring the repair of various PC3 components. confirm the error detection process on various systems of tractors, power tiller, engine and PC4 motor motors. prove the error detection process in various disc programs, harrows, cultivators, seed drills, sprayer and dusters, harvesters and PC5 threshing machines. confirm the error detection process on water lift devices and PC6 irrigation systems. show the error detection process for various post harvesting items such as cleaner, grader, dryer, size reduction, PC7 oil extraction equipment. explain the importance of making PC8 minor repairs and its maintenance from time to time. verify the maintenance process from time to time Provide details of the security procedures, security features required for operation To be competent, the user / individual must be able to: PC9. explain the importance of following the safe operating procedures for PC10. describe the safety procedures to be followed during the operation of the tractor, power tillers, farm machinery, irrigation equipment, harvesters behind the PCC. prove the use and importance of protective equipment and equipment to be used while periodically using or storing the tractor, farm machinery, irrigation equipment, harvesting equipment supplied by PC12. describe the safety procedures to be followed during the operation of items such as disc plows, harrows, seed drills, sprayer and duster PC13. provide details of the operator manual, security manual and maintenance manual.
Organizational Context (Knowledge of the company / organization and its processes):
The user/individual on the job needs to know and understand: KA1. code of business conduct KA2. job responsibilities and duties KA3. standard operating procedures for demonstration of operations KA4. procedures for information sharing
Technical Knowledge:
The user / person at work needs to know and understand: KB1. how to make minor repairs to agricultural machinery and KB2 equipment. periodic maintenance of tractor, electric power, engine and vehicles KB3. common problems with field performance, minor maintenance adjustments and their solutions KB4. safety methods and procedures while using a tractor, power tiller, engine and motors KB5. safety methods and procedures while using disc plows, harrows, cultivators, seed drills, sprayer and dusters, harvesters and KB6 threshers. safety measures and procedures while using water pumps, sprinklers and KB7 irrigation systems. preventive maintenance methods and when the equipment replacement KB8 should be done. safety methods and procedures while using harvesting equipment posted KB9. operator protection during machine operation against environmental hazards and air pollution KB10. emergency management and first aid services KB11. hazardous machinery (law), law 1983 Agriculture Machinery Demonstrator
Core Skills/ Generic Skills Agriculture Machinery Demonstrator:
The user / person at work needs to know and understand how to do this: SA1. prepare lessons in a visual and understandable way for SA2. describe functionality and design using blackboard SA3. prepare detailed reports during training Learning Skills The user / employee needs to know and understand how to do this: SA4. read and translate the manuals required for SA5 equipment maintenance. read and understand the security manual Oral Communication (listening and speaking skills) The user / person at work needs to know and understand how to do this: SA6. communication with farmers in the local language SA7. communicate the importance of safety and periodic maintenance SA8. listen to workers, team members and farmers to know and understand their work-related problems B. Creating Professional Skills Making a user / employee need to know and understand that: SB1. has decided on the display method to be used by SB2. determine the tools, equipment and resources needed for display Agriculture Machinery Demonstrator
Plan and Organize The user / person at work needs to know and understand how to do this: SB3. schedule SB4 training sessions in advance. arrange for the availability of resources such as books, tools and experts Customer Centricity Customer / employee needs to know and understand how to do this: SB5. understand customer needs and priorities and choose the appropriate SB6 display method. describe language training courses for farmers who are most comfortable with problem solving The user / employee needs to know and understand: SB7. manage last minute change in system and configure SB8. edit other resources in case of change at the last minute SB9. manage customer queries and take appropriate steps for Analytical Thinking The user / employee needs to know and understand: SB10. use background information and audience comprehension, equipment and a variety of display options to select the most appropriate SB11 form. use background information about equipment and display types to select the most suitable resources Key considerations The user / employee needs to know and understand: SB12. use common sense and make daily decisions

Maintain health and safety at the workplace:
In order to be effective, that person must be able to: PC1. perform a basic safety test before the operation of all equipment and vehicles and report all potential hazards to the PC2 manager. identify the function for which protective clothing or equipment is required and perform those functions according to the PC3 workplace policy. Read and understand the risks of use and pollution mentioned in pesticides / fumigants labels, etc. PC4. check the risk before performing manual operations, and work in accordance with current PC5 safe practices. use equipment and building materials and restore the same to designated storage where PC6 can be used. dispose of waste again at the selected PC7 location. detect hazards in viewers and take steps to reduce the risks associated with activities in the PC8 workplace. performs work in a manner that minimizes environmental damage throughout the process and ensures that hazard control task instructions are followed by PC9. report any accidents, incidents or problems without delay to the appropriate person and take immediate steps to minimize further risks Provide appropriate emergency procedures In order to be effective, that person must be able to: PC10. follow risk management procedures, fires and emergencies, including local communications and PC11 emergency evacuation guidelines. follow emergency procedures in the normal / corporate environment PC12. use emergency equipment with manufacturer specifications and PC13 job requirements. provide appropriate treatment for the patient’s injury in accordance with PC14 first aid strategies. locate (if possible), clean, inspect / test, refresh, replace and maintain first aid equipment properly
PC15. report details of first aid services under workplace information Knowledge and understanding Agriculture Machinery Demonstrator
(K) A. Organizational context (Company / organization information and procedures) Agriculture Machinery Demonstrator:
User / employee needs knowledge and understanding: KA1. hygiene and fitness requirements KA2. general duties under the relevant health and safety law KA3. protective equipment to be worn and how to care for KA4. efficient and safe use of materials and equipment required for work KA5. the importance of proper housing maintenance in the work of KA6. KA7 safe waste disposal methods. ways to reduce environmental damage during work B. Technical knowledge The user / person on the job needs to know and understand: KB1. health and safety hazards and steps to be taken to manage those risks in your workplace KB2. workplace procedures and requirements for occupational injury / illness33. basic emergency first aid program KB4. local paramedics KB5. the importance of reporting accidents, incidents and problems and the steps to be taken Agriculture Machinery Demonstrator
Core Skills/ Generic Skills:
The user / person at work needs to know and understand how to do this: SA1. state the required particulars of record keeping SA2. report problems to relevant staff during SA3. write descriptions and details of events in reports Learning Skills The user / employee needs to know and understand how to do this: SA4. read handbook and handbooks Oral communication (listening and speaking skills) The user / person at work needs to know and understand how to do this: SA5. liaising with others such as farmers, relevant stakeholders / stakeholders SA6. understanding the information shared by senior people and professionals B. Practicing Professional Skills The user / employee needs to know and understand how to do it: SB1. make decisions about the types of tools SB2 will use. identify the need for first aid and provide it Plan and Edit The user / person at work needs to know and understand that: SB3. plan daily tasks and draw priorities, split start times, estimate completion times and building materials, equipment and assistance needed for completion
Plan and Organize The user / person at work needs to know and understand how to do this: SB3. schedule SB4 training sessions in advance. arrange for the availability of resources such as books, tools and experts Customer Centricity Customer / employee needs to know and understand how to do this: SB5. understand customer needs and priorities and choose the appropriate SB6 display method. describe language training courses for farmers who are most comfortable with problem solving The user / employee needs to know and understand: SB7. manage last minute change in system and configure SB8. edit other resources in case of change at the last minute SB9. manage customer queries and take appropriate steps for Analytical Thinking The user / employee needs to know and understand: SB10. use background information and audience comprehension, equipment and a variety of display options to select the most appropriate SB11 form. use background information about equipment and display types to select the most suitable resources Key considerations The user / employee needs to know and understand: SB12. use common sense and make daily decisions Agriculture Machinery Demonstrator
Guidelines for Assessment:
- Criteria for assessment for each Qualification Pack will be created by the Sector Skill Council. Each Performance Criteria
(PC) will be assigned marks proportional to its importance in NOS. SSC will also lay down proportion of marks for Theory and
Skills Practical for each PC - The assessment for the theory part will be based on knowledge bank of questions created by the SSC
- Individual assessment agencies will create unique question papers for theory part for each candidate at each
examination/training center (as per assessment criteria below) - Individual assessment agencies will create unique evaluations for skill practical for every student at each
examination/training center based on this criteria - To pass the Qualification Pack , every trainee should score a minimum of 70% in aggregate
- In case of successfully passing only certain number of NOS’s, the trainee is eligible to take subsequent assessment on the
balance NOS’s to pass the Qualification Pack