Free Paintshop Assistant Course (4Months)
Paintshop Assistant:
Brief Job Description
A paint shop assistant technician will be involved in BIW Inspection, loading of the body in the conveyor and processes of Sealing and Sandingof the vehicle part.
Personal Attributes
The person should have the following attributes Correct and proper Vision, no color blindness, dexterity, non allergic to chemicals, paints and thinner, able to read and right basic language
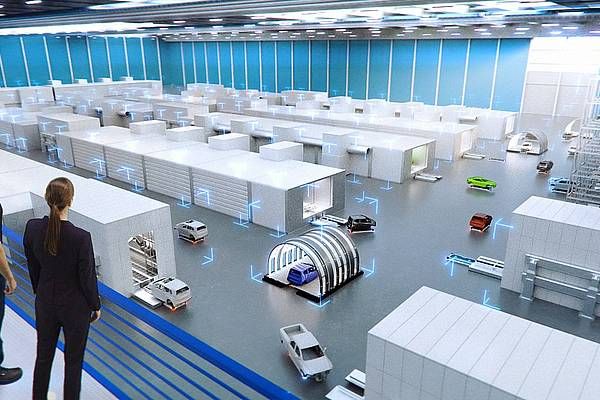
Maintain a safe and healthy working environment:
Elements and Performance Criteria
Identify and report the risks identified
To be competent, the user/individual on the job must be able to:
PC1.. Identify activities which can cause potential injury through sharp objects, burns, fall, electricity, gas leakages, radiation, poisonous fumes, chemicals ,loud noise
PC2. Inform the concerned authorities about the potential risks identified in the processes, workplace area/ layout, materials used etc
PC3. Inform the concerned authorities about machine breakdowns, damages which can potentially harm man/ machine during operations
PC4. Create awareness amongst other by sharing information on the identified risks
Create and sustain a Safe, clean and environment friendly work place
To be competent, the user/individual on the job must be able to:
PC5.. Follow the instructions given on the equipment manual describing the operating process of the equipments
PC6.. Follow the Safety, Health and Environment related practices developed by the organization
PC7. Operate the machine using the recommended Personal Protective Equipments (PPE)
PC8. . Maintain a clean and safe working environment near the work place and ensure there is no spillage of chemicals, production waste, oil, solvents etc
PC9. Maintain high standards of personal hygiene at the work place
PC10. Ensure that the waste disposal is done in the designated area and manner as per organization SOP.
PC11. Inform appropriately the medical officer/ HR in case of self or an employees illness of contagious nature so that preventive actions can be planned for others
Knowledge and Understanding (KU)
The individual on the job needs to know and understand:
KU1. relevant standards, procedures and policies related to Health, Safety and Environment followed in the company
KU2. basic knowledge of Safety procedures( fire fighting, first aid) within the organization
KU3. knowledge of various types of PPEs and their usage
KU4. basic knowledge of risks/hazards associated with each occupation in the organization
KU5. how to safely operate various tools and machines and risksassociated with the tools/ equipment
KU6. knowledge of personal hygiene and how an individual an contribute towards creating a highly safe and clean working environment
Generic Skills (GS)
User/individual on the job needs to know how to:
GS1. write basic level notes and observations
GS2. read safety instructions put up across the plant premises
GS3. read safety precautions mentioned in equipment manuals and panels to understand the potential risks associated
GS4. effectively communicate information to team members
GS5. informemployees in the plant and concerned functions about events, incidents & potential risks observed related to Safety, Health and Environment.
GS6. question operator/ supervisor in order to understand the safety related issues
GS7. attentively listen with full attention and comprehend the information given by the speaker during safety drills and training programs
GS8. use common sense and make judgments during day to day basis
GS9. use reasoning skills to identify and resolve basic problems
GS10. use common sense and make judgments during day to day basis
GS11. use reasoning skills to identify and resolve basic problems
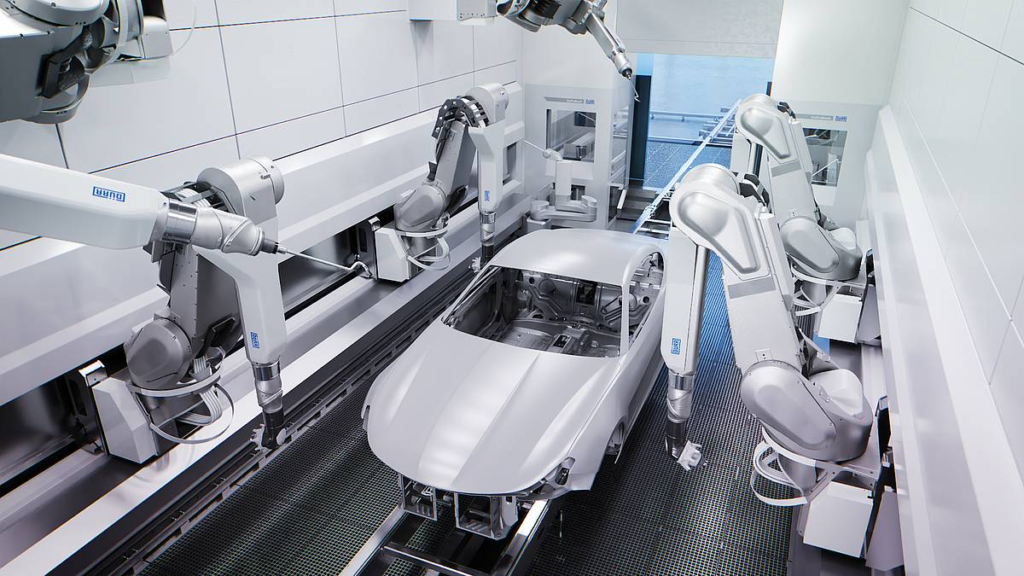
Conduct regular cleaning and maintenance of the equipment:
Elements and Performance Criteria
Storing equipment in proper condition
To be competent, the user/individual on the job must be able to:
PC1.. arrange all equipment in a proper order as indicated in the equipment manual
PC2. . store equipment auxiliaries and spare parts in proper designated areas
PC3.. clearly tag process related equipment parts/ spare parts as per part number or serial number so that sorting of equipment becomes easy
PC4. cover equipment so that there is limited dust collection and moisture contact
Regular cleaning of the equipments and work area
To be competent, the user/individual on the job must be able to:
PC5. regularly clean the equipment and process auxiliaries to remove any dust, moisture, waste material which would have got collected on the equipment
PC6. regularly open the equipment and clean the internal parts of the equipment
PC7. regularly clean the working area under the process and create a healthy, clean and safe working environment
Conduct regular preventive maintenance of equipments
To be competent, the user/individual on the job must be able to:
PC8.. check the working of all bearing, rollers, shafts etc and oil all moving parts of the equipment on a periodic basis
PC9.. check the working of non moving parts and periodically conductpreventive maintenance to prevent machine failure
PC10. periodically check the equipment calibration and report any errors to the maintenance teams for rectification
Recording observations and preparing MIS
To be competent, the user/individual on the job must be able to:
PC11. prepare periodic log sheets of equipment maintenance dates, maintenance schedules and maintenance activity conducted on the equipment
Knowledge and Understanding (KU)
The individual on the job needs to know and understand:
KU1. relevant standards and procedures followed in the company for the process of maintenance and equipment storage
KU2. functional processes like Procurement, Store management, inventory management, quality management and key contact points for query resolution
KU3. basic level maintenance and cleaning techniques
KU4. various solvents, chemicals, lubricants etc. used during the maintenance processes
KU5. procedure for arranging the equipment and spare parts in the prescribed manner including tagging and numbering of machine parts & spares
KU6. safety precautions to be taken during cleaning and maintenance activities
Generic Skills (GS)
User/individual on the job needs to know how to:
GS1. note equipment part codes, name tags etc. in the prescribed formats and records for the same
GS2. note observations related to equipment performance, breakdown, cleaning and maintenance schedules etc. in the prescribed MIS format
GS3. read equipment manuals and process documents to understand the equipment and processes better
GS4. read instructions especially safety instructions related to equipment cleaning and maintenance
GS5. discuss task lists and job requirements with co-workers
GS6. effectively communicate information to team members
GS7. listen and analyse any noise and vibrations in the equipment and report the same to the maintenance team for preventive action
GS8. attentively listen with full attention and comprehend the information given by the speaker
GS9. plan and organize the work order and jobs received from the Operator
GS10. organize all process/ equipment manuals so that sorting/ accessing information is easy as per the part/ machine number in the specified format in the designated area
GS11. use common sense and make judgments during day to day basis
GS12. use reasoning skills to identify and resolve basic problems
Maintain 5S at the work premises:
Elements and Performance Criteria
Ensure sorting
To be competent, the user/individual on the job must be able to:
PC1.. follow the sorting process and check that the tools, fixtures & jigs that are lying on workstations are the ones in use and unnecessary items are not cluttering the workbenches or work surfaces.
PC2.. ensure segregation of waste in hazardous/ non hazardous waste as per the sorting work instructions
PC3.. follow the technique of waste disposal and waste storage in the proper bins as per sop
PC4.. segregate the items which are labelled as red tag items for the process area and keep them in the correct places
PC5. sort the tools/ equipment/ fasteners/ spare parts as per specifications/ utility into proper trays, cabinets, lockers as mentioned in the 5s guidelines/ work instructions
PC6. . ensure that areas of material storage areas are not overflowing
PC7. properly stack the various types of boxes and containers as per the size/ utility to avoid any fall of items/ breakage and also enable easy sorting when required
PC8. return the extra material and tools to the designated sections and make sure that no additional material/ tool is lying near the work area
PC9. follow the floor markings/ area markings used for demarcating the various sections in the plant as per the prescribed instructions and standards
PC10. follow the proper labeling mechanism of instruments/ boxes/ containers and maintaining reference files/ documents with the codes and the lists
Ensure proper documentation and storage ( organizing , streamlining)
To be competent, the user/individual on the job must be able to:
PC11. check that the items in the respective areas have been identified as broken or damaged
PC12. follow the given instructions and check for labelling of fluids, oils. lubricants, solvents, chemicals etc. and proper storage of the same to avoid spillage, leakage, fire etc
PC13. make sure that all material and tools are stored in the designated places and in the manner indicated in the 5s instructions
Ensure cleaning of self and the work place
To be competent, the user/individual on the job must be able to:
PC14. check whether safety glasses are clean and in good condition
PC15. keep all outside surfaces of recycling containers are clean
PC16.. ensure that the area has floors swept, machinery clean and generally clean. in case of cleaning, ensure that proper displays are maintained on the floor which indicate potential safety hazards
PC17.. check whether all hoses, cabling & wires are clean, in goodcondition and clamped to avoid any mishap or mix up
PC18.. ensure workbenches and work surfaces are clean and in good condition
PC19. follow the cleaning schedule for the lighting system to ensure proper illumination
PC20. store the cleaning material and equipment in the correct location and in good condition
PC21. ensure self-cleanliness – clean uniform, clean shoes, clean gloves, clean helmets, personal hygiene
Ensure sustenance
To be competent, the user/individual on the job must be able to:
PC22. follow the daily cleaning standards and schedules to create a clean working environment
PC23. attend all training programs for employees on 5 s
PC24. support the team during the audit of 5 s
PC25. participate actively in employee work groups on 5s and encourage team members for active participation
PC26. follow the guidelines for what to do and what not to do to build sustainability in 5s as mentioned in the 5s check lists/ work instructions
Knowledge and Understanding (KU)
The individual on the job needs to know and understand:
KU1. relevant standards, procedures and policies related to 5S followed in the company
KU2. have basic knowledge of 5S procedures
KU3. know various types 5s practices followed in various areas
KU4. understand the 5S checklists provided in the department/ team
KU5. have skills to identify useful & non useful items
KU6. have knowledge of labels , signs & colours used as indicators
KU7. knowledge on how to sort and store various types of tools, equipment, material etc.
KU8. know , how to identify various types of waste products
KU9. understand the impact of waste/ dirt/ dust/unwanted substances on the process/ environment/ machinery/ human body
KU10. have knowledge of best ways of cleaning & waste disposal
KU11. understand the importance of standardization in processes
KU12. understand the importance of sustainability in 5S
KU13. have knowledge of TQM process
KU14. have knowledge of various materials and storage norms
KU15. understand visual controls, symbols, graphs etc.

Generic Skills (GS)
User/individual on the job needs to know how to:
GS1. write basic level notes and observations
GS2. note down observations (if any) related to the process
GS3. read 5S instructions put up across the plant premises
GS4. effectively communicate information to team members inform employees in the plant and concerned functions about 5S
GS5. question the process head in order to understand the 5S related issues
GS6. attentively listen with full attention and comprehend the information given by the speaker during 5S training programs
GS7. use common sense and make judgments during day to day basis
GS8. use reasoning skills to identify and resolve basic problems using 5S
GS9. persuade co team members to follow 5 S
GS10. ensure that the co team members understand the importance of using 5 S tool
GS11. use innovative skills to perform and manage 5 S activities at the work desk and the shop floor
GS12. exhibit inquisitive behaviour to seek feedback and question on the existing set patterns of work
GS13. do what is right, not what is a popular practices
GS14. follow shop floor rules& regulations and avoid deviations; make 5S an integral way of life
GS15. ensure self-cleanliness on a daily basis
GS16. demonstrate the will to keep the work area in a clean and orderly manner
Support the Operator:
Elements and Performance Criteria
Check the body as per the Quality gate inspection sheets as per Standard Operating Procedures/ Internal Quality Manual
To be competent, the user/individual on the job must be able to:
PC1. . clearly understanding the does and donts of the manufacturing process as defined in sops/ work instructions or defined by supervisors
PC2. . check the incoming body parts for dents as per the instructions given in the work instructions/ sop
PC3. . check the incoming body parts for burrs, metal wires as per the instructions given in the work instructions
PC4. . check the incoming body parts for rustas per the instructions given in the work instructions
PC5.. return the body part if quality parameters not adhered to
Press the carrier rise button in loading panel in auto mode
To be competent, the user/individual on the job must be able to:
PC6. . check visual/manual while loading the panel
Check all rest point of the body .Align the body on clamp hanger if body not properly rested
To be competent, the user/individual on the job must be able to:
PC7. . check the condition of the connector, if is not ok then bypass the hanger.
PC8. . check the pin point of the rested part of the body for alignment, if not properly rested,align with the help of rod.
Feed the data in loading panel according to model and save it
To be competent, the user/individual on the job must be able to:
PC9. . check visual/manual while feeding the data otherwise the hanger will not move
Cut wire to clamp the body
To be competent, the user/individual on the job must be able to:
PC10. . ensure proper wire cutting so that the wire doesn`t come in contact with the body and body shell.
Knowledge and Understanding (KU)
The individual on the job needs to know and understand:
KU1. relevant standards and procedures followed in the company
KU2. different types of products manufactured by the company
KU3. functional processes like store management, inventory management, quality management and key contact points for query resolution
KU4. different types of painting processes and associated equipments
KU5. different types of dents, burrs etc
KU6. different types of defects which may arise due to improper loading
KU7. how to operate loading both in automatic and manual mode
KU8. ability to visualize the final product output and hence decide on the key steps to be followed while loading
Generic Skills (GS)
User/individual on the job needs to know how to:
GS1. document information
GS2. write basic level notes and observations
GS3. draw basic level drawings and charts
GS4. read equipment manuals and process documents to understand the equipments and processes better
GS5. read internal information documents sent by internal customers ( other functions within the organization)
GS6. discuss task lists, schedules, and work-loads with co-workers
GS7. question internal customers/ welding shop supervisor in order to understand the nature of the problem and make a diagnosis
GS8. plan and organize the work order and jobs received from the internal customers
GS9. organize all process/ equipment manuals so that finding out information is fast
GS10. ability to understand what level of defects are acceptable and return the other body parts to the weld shop
GS11. carefully load the body part so that proper pretreatment can happen
GS12. carefully analyze which body has to be loaded manually and which automatically

Assessment Guidelines
- Criteria for assessment for each Qualification Pack will be created by the Sector Skill Council. Each Element/ Performance Criteria (PC) will be assigned marks proportional to its importance in NOS. SSC will also lay down proportion of marks for Theory and Skills Practical for each Element/ PC.
- The assessment for the theory part will be based on knowledge bank of questions created by the SSC.
- Assessment will be conducted for all compulsory NOS, and where applicable, on the selected elective/option NOS/set of NOS.
- Individual assessment agencies will create unique question papers for theory part for each candidate at each examination/training center (as per assessment criteria below).
- Individual assessment agencies will create unique evaluations for skill practical for every student at each examination/ training center based on these criteria.
- To pass the Qualification Pack assessment, every trainee should score the Recommended Pass % aggregate for the QP.
- In case of unsuccessful completion, the trainee may seek reassessment on the Qualification Pack.