Tank Farm Supervisor (1 years diploma )
Tank Farm Supervisor click here
Brief Job Description: The individual supervises tank farm operations related to
resource allocation, inspection, compliance to regulation, documentation and
performance. S/he is also responsible for conducting trend analysis to prepare
forecasts and maintenance schedules.
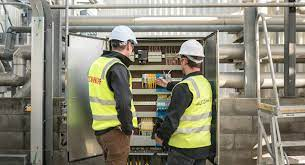
Qualifications Pack for Tank Farm Supervisor
Options
Option 1: Tank Farm Infrastructure Management
The unit is about assisting in management of tank farm infrastructure across
regions
Option 2: Ship and Yard Planning
The unit is about supervising cargo handling and storage operations in the port
terminal, Inland Container Depot (ICD) or Container Freight Station (CFS)
Personal Attributes:
The job holder should be medically and physically fit to operate in liquid
terminals. S/he should be observant and diligent in monitoring operations and
performance. S/he should have analytical, organisational and leadership traits to
prepare forecasts, budgets and schedules and implement them. The individual
should have English and Vernacular language proficiency, demonstrable in
spoken, written and oral communication.
Description
Core Skills/Generic
Skills
Core Skills or Generic Skills are a group of skills that are key to learning and
working in today’s world. These skills are typically needed in any work
environment. In the context of the NOS, these include communication related
skills that are applicable to most job roles.
Function
Function is an activity necessary for achieving the key purpose of the sector,
occupation, or area of work, which can be carried out by a person or a group
of persons. Functions are identified through functional analysis and form the
basis of NOS.
Job role Job role defines a unique set of functions that together form a unique
employment opportunity in an organization.
Knowledge and Understanding
Knowledge and Understanding are statements which together specify the
technical, generic, professional and organizational specific knowledge that an
individual needs in order to perform to the required standard.
National Occupational
Standards NOS are Occupational Standards which apply uniquely in the Indian context
Electives
Electives are NOS/set of NOS that are identified by the sector as contributive
to specialization in a job role. There may be multiple electives within a
Qualifications Pack (QP) for each specialized job role. Trainees must select
atleast one elective for the successful completion of a QP with Electives
Options
Options are NOS/set of NOS that are identified by the sector as additional
skills. there may be multiple options within a QP. It is not mandatory to select
any of the options to complete a QP with Options.
Unit Code Unit code is a unique identifier for an Occupational Standard, which is
denoted by an ‘N’
Unit Title Unit title gives a clear overall statement about what the incumbent should be
able to do.
Occupation Occupation is a set of job roles, which perform similar/related set of functions
in an industry.
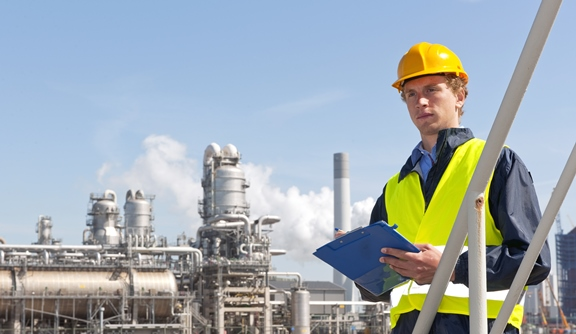
Organisational Context
Organisational Context includes the way the organization is structured and
how it operates, including the extent of operative knowledge managers have
of their relevant areas of responsibility.
Performance Criteria Performance Criteria are statements that together specify the standard of
performance required when carrying out a task.
Qualifications Pack
QP comprises the set of NOS, together with the educational, training and
other criteria required to perform a job role. A Qualifications Pack is assigned
a unique qualification pack code.
Qualifications Pack
Code
Qualifications Pack Code is a unique reference code that identifies a
qualifications pack.
Scope Scope is the set of statements specifying the range of variables that an
individual may have to deal with in carrying out the function which have a
critical impact on the quality of performance required.
Sector
Sector is a conglomeration of different business operations having similar
businesses and interests. It may also be defined as a distinct subset of the
economy whose components share similar characteristics and interests.
Sub-Sector Sub-sector is derived from a further breakdown based on the characteristics
and interests of its components.
Sub-functions Sub-functions are sub-activities essential to fulfil the achieving the objectives
of the function.
Technical Knowledge Technical Knowledge is the specific knowledge needed to accomplish specific
designated responsibilities.
API American Petroleum Institute
CFS Container Freight Station
ERP Enterprise resource planning
GPS Global Positioning System
HAZCHEM Hazardous Chemicals
HR Human Resources
ICD Inland Container Depot
IEC International Electrotechnical Commission
IMDG International Maritime Dangerous Goods
ISCO International Standard Classification of Occupations
IOT Internet of Things
IT Information Technology
MHE Material Handling Equipment
MIS Management information system
NCO National Classification of Occupations
NFPA National Fire Protection Association
NOS National Occupational Standards
NSQC National Skills Qualifications Committee
NSQF National Skills Qualifications Framework
OH&S Occupational Health and Safety
OS Occupational Standards
OSHA Occupational Safety and Health Administration
PC Performance Criteria
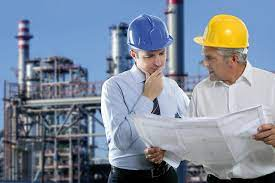
PGA Participating Government Agencies
PPE Personal Protective Equipment
QP Qualifications Pack
RFID Radio Frequency Identification
SOPs Standard Operating Procedures
SSC Sector Skill Council
VHF Very high frequency
Allocate resources and streamline operations at liquid terminals
Description This unit is about Allocating resources and streamlining operations at liquid terminals
Scope This unit/task covers the following:
• Prepare work plan and allocate resources
• Monitor daily operations
• Resolve escalated issues
Range: Stationery, radio frequency identification (RFID) scanner, bar code scanner,
markers, Personal Protective Equipment (PPEs), Enterprise resource planning (ERP),
computer, printers, Global Positioning System (GPS) tracker, piping and pumping
equipment, International Maritime Dangerous Goods (IMDG), hazardous chemicals
(HAZCHEM) codes and Standard Operating Procedures (SOPs) etc.
Performance Criteria (PC) w.r.t. the scope
Element Performance Criteria
Prepare work plan
and allocate
resources
To be competent, the user/ individual must be able to:
PC1. obtain details of vessel docking plans, cargo loading and unloading plans, etc.
PC2. develop daily work plan factoring in priority cases, time bound requirements,
special handling requirements, capacity of tanks etc.
PC3. get the work plan approved by the terminal manager and allocate tasks to
subordinates
PC4. budget and allocate the requisite equipment and systems for tasks at hand
Monitor daily
operations
To be competent, the user/individual on the job must be able to:
PC5. conduct inspection of terminal for safety, cleanliness, marking of material
movement and people movement areas, etc.
PC6. conduct field inspections to review the status of loading, unloading and
maintenance activities

PC7. engage resources in alternate operation when there is a delay of planned
operations
PC8. allocate additional and ad-hoc manpower and equipment during exigency
PC9. escalate issues regarding pipeline operations, transporter delays, vessel
delays, accidents, damages, etc. to manager
PC10. provide corrective and preventive action plans based on accident and damage
reports
PC11. liaise with port officials, customs officials and external stakeholders
Resolve escalated
issues
To be competent, the user/ individual must be able to:
PC12. review escalated issues and identify root cause for providing corrective action
PC13. provide technical guidance to the team for execution
PC14. escalate the issues to manager when external or additional help is required
PC15. coordinate with other departments, transporters, freight operators, port
authorities, shipping companies and others to resolve escalations if required
A. Organizational
context
(Knowledge of the
company /
organization and
its processes)
The individual on the job needs to know and understand:
KA1. organizational procedures
KA2. documentation and reporting as per organization’s mandate
KA3. security procedures to be followed
KA4. escalation matrix for reporting identified problems
KA5. risk and impact of not following defined procedures/work instructions
KA6. coding system followed to label cargo
KA7. Information Technology (IT) system and ERP system of the organization
B. Technical
knowledge
The individual on the job needs to know and understand:
KB1. basics of operations in a port terminals and liquid terminals
KB2. different type of cargo, their classification – A, B, C and their handling
procedure and precautions
KB3. SOPs for different operations, Petro-chemical standards – International
Electrotechnical Commission (IEC) 61511, IEC 61508, American Petroleum
Institute (API) 2350, National Fire Protection Association (NFPA), Oil industry
safety directorate guidelines and various committee recommendations
KB4. use of various cargo handling equipment
KB5. use of rope , flags and other manual equipment
KB6. vessel layout and loading and unloading activities
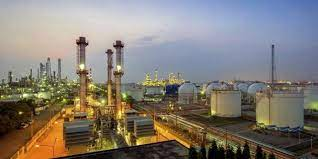
KB7. procedures of tank cleaning, cargo movement
KB8. requirements regarding handling of cargo
KB9. different type of vessels and cargo and container sizes
KB10. different type of cranes and Material Handling Equipment (MHEs) – their
capacities, constraints and usage
KB11. handling of hazardous and non-hazardous cargo – – IMDG code
KB12. marking of material and people movement areas
KB13. stuffing and de-stuffing norms with respect to different cargo
KB14. special characteristics and handling requirements of shipments, if any
Skills (S)
A. Core skills/
generic skills
Reading skills
The user/individual on the job needs to know how to read:
SA1. written instructions
SA2. ERP alarms, gauges and meters, message and notifications, daily reports
SA3. checklists
Writing skills
The user/individual on the job needs to know how to write:
SA4. monitoring and inspection reports
SA5. instructions
SA6. training pedagogy
Oral communication (listening and speaking skills)
The user/individual on the job needs to know how to:
SA7. communicate with supervisors, ground workforce, pumping attendants,
transport operators
SA8. coordinate with local authorities, external support agencies
B. Professional skills Decision making
The user/individual on the job needs to know how to:
SB1. decide on required workforce and equipment for performing a particular task
SB2. assess the environmental condition and type of cargo to assess if it is safe for
operations
SB3. resolve a problem quickly internally
SB4. prioritise shipments
SB5. decide on deployment of alternate resources when required
Plan and organize
The user/individual on the job needs to know how to:
SB6. plan and estimate the co-ordination required for resolving a querry.
SB7. maintain punctuality
SB8. respond to the client in a timely manner
SB9. prioritize and execute tasks based on client requirements
SB10. make work plans and resource allocation plans
SB11. make checks on execution of work plans
SB12. be a team player and achieve joint goals
Customer centricity
The user/individual on the job needs to know how to:
SB13. adhere to the customer timelines
SB14. address the urgency regarding shipments and activities
Problem solving
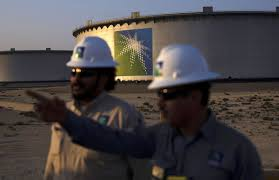
The user/individual on the job needs to know how to:
SB15. make adjustment to working requirements for difficult weathers and
hazardous goods
SB16. identify trends/common causes for delays, damages, etc.
SB17. co-ordinate and handle major issues with different departments
SB18. identify bottlenecks and operational problems and suggest remedial action
Analytical thinking
The user/individual on the job needs to know how to:
SB19. assess the resource requirement for a particular task at hand
SB20. assess and prepare for backup resources in case of delays
Critical thinking
The user/individual on the job needs to know and understand how to:
SB21. resolve issues in a quick and cost effective manner
Perform tank farm inspections, inventory tracking and training
Description This unit is about monitoring the tank farm operations, conducting inspections,
tracking inventory and estimating losses and training of workers
Scope This unit/task covers the following:
• Monitor tank farm operations and inventory
• Inspect the tank farm
• Train subbordinates
Range – Tank farm, pipeline, pumps, controls and valves, central control unit,
simulator, Personal Protective Equipment (PPE), computer, projector, worksheets,
stationery etc.
Performance Criteria(PC) w.r.t. the scope
Element Performance Criteria
Monitor tank farm
operations and
inventory
To be competent, the user/ individual must be able to:
PC1. review daily reports related to tank farm equipment such as alarms, control
valves and ensure they are correctly functioning
PC2. review the daily recording of different measuring devices in the control room
to check that all parameters are under prescribed limits
PC3. instruct subordinates to take preventive actions such as pressure release,
pumping of liquid, etc., in case of any anomaly in reports
PC4. monitor daily inventory report with regards to pressure, temperature and
cargo levels to check for losses
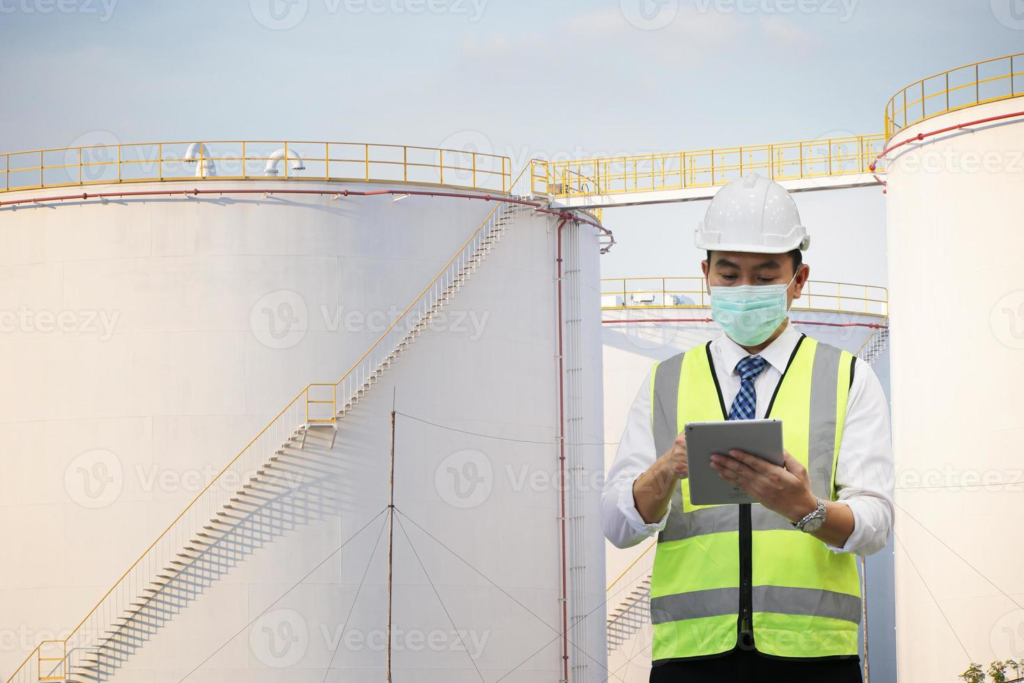
PC5. take corrective and preventive actions if cargo loss is over the prescribed
limits
PC6. ensure compliance to hazardous material handling norms
PC7. estimate loss and submit reports detailing the loss, status of controls and
monitoring parameters
PC8. escalate issues to manager and external technical support team as and when
required
Inspect tank farms To be competent, the user/ individual must be able to:
PC9. inspect tanks and check for corrosion, missing paints, fractures and leakages
from welding and drainage, cleanliness, adherence to regulatory and
company norms, etc.
PC10. provide instructions for maintenance works like surface painting, cleaning of
exteriors, removal of residuals lying outside etc.
PC11. check and ensure that emergency pathways are not obstructed, and
emergency systems are operational and easily accessible
PC12. check that all pumps, pipelines are functional and free from corrosion
PC13. escalate issues that need external technical repairs and servicing
Train subordinates To be competent, the user/ individual must be able to:
PC14. train subordinates on monitoring, cleaning and loading/unloading of tanks
PC15. train subordinates on common causes for errors, accidents, standard
precautions, post-accident disaster response, and regulatory compliances etc.
PC16. conduct specific incident-based training and detail the preventive and disaster
response to be undertaken in such cases
PC17. document trainings conducted and track of regularity of training
Knowledge and understanding (K)
B. Organizational
context
(Knowledge of the
company /
organization and
its processes)
The individual on the job needs to know and understand:
KA1. organizational procedures and Standard Operating Procedures (SOPs) for tasks
at hand, documentation policy and emergency responses
KA2. security and safety procedures to be followed
KA3. reporting structure of the organization and the supplier for escalation of issues
KA4. risk and impact of not following defined procedures/work instructions
KA5. coding system followed for different type of liquids and their distress codes
B. Technical
knowledge
The individual on the job needs to know and understand:
KB1. different type of cargo, their classification – A, B, C and their handling
procedure and precautions
KB2. SOPs for different operations, Petro-chemical standards – International
Electrotechnical Commission (IEC) 61511, IEC 61508, American Petroleum
Institute (API) 2350, National Fire Protection Association (NFPA), Oil industry
safety directorate guidelines and various committee recommendations
KB3. using fire extinguisher and protocols for emergencies
KB4. operations of control systems, pumps, valves, alarm systems, etc.
KB5. documentation requirement for different type of cargo and their handling
KB6. handling and emergency procedures for hazardous cargo
KB7. training methodology
KB8. current events regarding liquid tank farms happening across the world
including new technologies and best practices
KB9. various common mistakes and precautions to be taken in tank farms
Skills (S)
C. Core skills/
generic skills
Reading skills
The user/individual on the job needs to know how to read:
SA1. written instructions
SA2. Enterprise resource planning (ERP) alarms, gauges and meters, message and
notifications, daily reports
SA3. Checklists
Writing skills
The user/individual on the job needs to know how to write:
SA4. monitoring and inspection reports
SA5. instructions
SA6. training pedagogy
Oral communication (listening and speaking skills)
The user/individual on the job needs to know how to:
SA7. communicate with supervisors, ground workforce, pumping attendants,
transport operators
SA8. coordinate with local authorities, external support agencies
D. Professional skills Decision making
The user/individual on the job needs to know how to:
SB1. identify anomaly in operations
SB2. identify damage or abnormalities in tank structure
SB3. decide on need for servicing, repair and training
Plan and organize
The user/individual on the job needs to know how to:
SB4. plan and coordinate between teams to achieve joint goals.
SB5. maintain punctuality and respond in a timely manner
SB6. prioritize and execute tasks based on checklist and priorty requirements
SB7. do a check of activity completion
Customer centricity
The user/individual on the job needs to know how to:
SB8. adhere to the assigned timelines
SB9. address the urgency regarding cargo and emergencies
Problem solving
The user/individual on the job needs to know how to:
SB10. anticipate need for repair or maintenance in tanks
SB11. anticipate additional precautions to be taken for different operations
SB12. coordinate with manager, external stakeholders to quickly address issues
Analytical thinking
The user/individual on the job needs to know how to:
SB13. analyse trends of cargo level, alarms, servicing requirement, etc. to draw
inferences and future requirements
SB14. analyse trend of type of cargo stored to understand future requirement
SB15. estimate ageing of cargo and periodic requirement for tank maintenance
Critical thinking
The user/individual on the job needs to know and understand how to:
SB16. anticipate and identify hazardous situations and take necessary precautions
SB17. raise alarm and quick emergency response in case of hazards and accidents
SB18. monitor inventory to track losses, theft, etc.
Supervise cleaning, pumping and loading activities
Description This unit is about supervising and monitoring different tank farm operations – cleaning
pumping and loading/unloading activities
Scope This unit/task covers the following:
• Supervise cleaning activties
• Supervise pumping operations
• Supervise loading/unloading operations
Range: Tank farm, loading/unloading equipment, cleaning equipment and
consumables, control equipment, Standard Operating Procedures (SOP),
documentation, computer, projector, worksheets, stationery etc.
Performance Criteria(PC) w.r.t. the scope
Element Performance Criteria
Supervise cleaning
activities
To be competent, the user/ individual must be able to:
PC1. provide instructions for residual removal and cleaning process and monitor
the activities
PC2. check reports regarding residual removals to verify the quantity of cargo
removed from the tank
PC3. review reports for presence of noxious and hazardous gases or liquid prior to
cleaning operations
PC4. coordinate with external cleaning agencies and provide the necessary support
PC5. inspect tank post cleaning and check for corrosion, cracks, remaining residue,
presence of gases, humidity, etc.
Supervise pumping
operations
To be competent, the user/ individual must be able to:
PC6. coordinate with vessel, port, inland receiving supervisor regarding cargo to be
transferred and get the requisite authorizations and documentation
PC7. coordinate with manager, stakeholders to set volume to be pumped out and
inform associate
PC8. review pre-pumping report regarding fitness of equipment, pipelines, pumps
and connections
PC9. monitor pumping operations from the control room recording liquid flow,
pressure, operation of various valves and pumps, etc.
PC10. stop operations and instruct for maintenance check in case of any leakages,
pressure drops, etc.
PC11. review and authorise post operation report and confirm the same with the
receiving supervisor
Supervise
loading/unloading
To be competent, the user/ individual must be able to:
PC12. plan for daily loading/unloading based on requirement
PC13. coordinate with transporters and arrange adequate number of rail wagons or trucks
PC14. review fitness report of transport vehicles before loading and seek
replacement if they are unfit for operation
PC15. review fitness reports of loading/unloading terminal equipment and
manpower with respect to regulatory and company compliance
PC16. inspect loading/unloading terminal to check for compliance to SOP
,
cleanliness, use of Personal Protective Equipment (PPEs), compliance to
regulatory requirements, functioning of emergency controls, etc.
PC17. review records of daily inventory movement – loading/ unloading and
available inventory with respect to assigned targets
Knowledge and understanding (K)
A. Organizational
context
(Knowledge of the
company /
organization and
its processes)
The individual on the job needs to know and understand:
KA1. organizational procedures and SOPs for tasks at hand, documentation policy
and emergency responses
KA2. security and safety procedures to be followed
KA3. reporting structure of the organization and the supplier for escalation of
issues
KA4. risk and impact of not following defined procedures/work instructions
KA5. coding system followed for different type of liquids and their distress codes
B. Technical
knowledge
The individual on the job needs to know and understand:
KB1. different type of cargo, their classification – A, B, C and their handling
procedure and precautions
KB2. SOPs for different operations, Petro-chemical standards – International
Electrotechnical Commission (IEC) 61511, IEC 61508, American Petroleum
Institute (API) 2350, National Fire Protection Association (NFPA), Oil industry
safety directorate guidelines and various committee recommendations
KB3. using fire extinguisher and protocols for emergencies
KB4. operations of control systems, pumps, valves, alarm systems, etc.
KB5. documentation requirement for different type of cargo and their handling
KB6. handling and emergency procedures for hazardous cargo
KB7. various common mistakes and precautions to be taken in loading, unloading
and cleaning process
KB8. monitoring of cargo during loading, unloading and pumping
KB9. coordination with related stakeholders – cleaning agencies, receiving
supervisors, vessels, ports, etc.
KB10. documents and certificates to be verified in case of transports both trucks and
wagons
Skills (S)
C. Core skills/ Reading skills
The user/individual on the job needs to know how to read:
generic skills
SA1. written instructions
SA2. Enterprise Resource Planning (ERP), alarms, gauges and meters, message and
notifications, daily reports
SA3. checklists
Writing skills
The user/individual on the job needs to know how to write:
SA4. monitoring and inspection reports
SA5. instructions
SA6. letters and communications via email
Oral communication (listening and speaking skills)
The user/individual on the job needs to know how to:
SA7. communicate with supervisors, ground workforce, pumping attendants,
transport operators
SA8. coordinate with local authorities, external support agencies
D. Professional skills Decision making
The user/individual on the job needs to know how to:
SB1. identify hazards and losses in transports
SB2. decide if cleaning is adequate and the tank is fit for use
Plan and organize
The user/individual on the job needs to know how to:
SB3. plan and coordinate between teams to achieve joint goals.
SB4. maintain punctuality and respond in a timely manner
SB5. prioritize and execute tasks based on checklist and priorty requirements
SB6. do a check of activity completion
Customer centricity
The user/individual on the job needs to know how to:
SB7. adhere to the assigned timelines
SB8. address the urgency regarding cargo and emergencies
Problem solving
The user/individual on the job needs to know how to:
SB9. resolve documentation issues with other stakeholders to facilitate transports
SB10. guide for additional precautions to be taken for different operations
SB11. coordinate with manager, external stakeholders to quickly address issues
Analytical thinking
The user/individual on the job needs to know how to:
SB12. analyse time rrequired and trend of loading/unloading to estimate efficiencies
and daily targets
SB13. analyse trend of type of cargo stored to understand future requirement
Critical thinking
The user/individual on the job needs to know and understand how to:
SB14. anticipate and identify hazardous situations and take necessary precuations
SB15. raise alarm and quick emergency response in case of hazards and accidents
SB16. monitor inventory to track losses, theft, etc.
Review documentation and regulatory compliances for liquid cargo
Description This unit is about reviewing port and cargo documentation, documenting regulatory
compliances and coordinating for the same
Scope This unit/task covers the following:
• Review cargo and compliance documentation
• Coordinate and perform customer service
Range: Cargo documentation, vehicle documentation, International Maritime
Dangerous Goods (IMDG), Hazardous Chemicals (HAZCHEM) documents, Standard
Operating Procedures (SOP), computer, projector, worksheets, stationery etc.
Performance Criteria(PC) w.r.t. the scope
Element Performance Criteria
Review cargo and
compliance
documentation
To be competent, the user/ individual must be able to:
PC1. coordinate with shipping lines, vessels, freight transporters, importers and
exporters and the port authorities to obtain requisite cargo documents
PC2. review documentation of transport vehicles including their certificates for
fitness for operation, availability of requisite license, etc.
PC3. review cargo documents like bill of lading, shipping bills, Participating
Government Agencies (PGA) clearances, etc. for compliance to regulations
and standards
PC4. review fitness certificates and related documents of Material Handling
Equipment (MHEs), cranes and terminal equipment
PC5. review and approve gate entry and exit passes for transporters, vehicles
PC6. check for fitness and functionality of disaster response equipment and
systems
PC7. ensure periodic training and fitness of disaster response team
PC8. review evacuation and first response protocol to be followed in case of
pollutions and disasters
PC9. prepare compliance and fitness reports as per regulatory requirements
regarding tank farm layout, disaster response, fitness of equipment, etc.
Coordinate and
perform customer
service
To be competent, the user/ individual must be able to:
PC10. respond and resolve queries raised by port and custom authorities, custom
brokers, shipping liners, clients, transporters regarding status of different
shipments
PC11. coordinate between the vessel, shipper/ importer/exporter, agents and port
authorities to ensure that all compliances and requirements are met
PC12. respond and coordinate with various PGAs and regulatory authorities
regarding cargo handling and their specific requirements
Knowledge and understanding (K)
A. Organizational
context
(Knowledge of the
company /
organization and
its processes)
The individual on the job needs to know and understand:
KA1. organizational procedures and SOPs for tasks at hand, documentation policy
and emergency responses
KA2. security and safety procedures to be followed
KA3. reporting structure of the organization and the supplier for escalation of
issues
KA4. risk and impact of not following defined procedures/work instructions
KA5. coding system followed for different type of liquids and their distress codes
B. Technical
knowledge
The individual on the job needs to know and understand:
KB1. different type of cargo, their classification – A, B, C and their handling
procedure and precautions
KB2. SOPs for different operations, Petro-chemical standards – International
Electrotechnical Commission (IEC) 61511, IEC 61508, American Petroleum
Institute (API) 2350, National Fire Protection Association (NFPA), Oil industry
safety directorate guidelines, International Maritime Dangerous Goods
(IMDG), Hazardous Chemicals (HAZCHEM) guidelines and various committee
recommendations
KB3. different regulatory authorities, PGAs, stakeholders involved
KB4. regulatory requirements with respect to cargo handling and terminal layout
KB5. using fire extinguisher and protocols for emergencies
KB6. documentation requirement for different type of cargo, equipment and their
handling
KB7. handling and emergency procedures for hazardous cargo
KB8. coordination with related stakeholders
KB9. documents and certificates to be verified in case of transports both trucks
and wagons
Skills (S)
A. Core skills/
generic skills
Reading skills
The user/individual on the job needs to know how to read:
SA1. written instructions
SA2. shiping manifest, Bill of lading shipping bills and related documents
SA3. Enterprise resource planning (ERP) and computer generated reports
SA4. Terminal layout and storage plans
SA5. SOPs and safety regulation and compliance manuals and reports
Writing skills
The user/individual on the job needs to know how to write:
SA6. work-orders and instructions
SA7. various reports and letters
Oral communication (listening and speaking skills)
The user/individual on the job needs to know how to:
SA8. communicate with customers, fireght operators, transporters, shipping
companies, other supervisors and port authorities
SA9. communicate with regulatory authorities and PGAs
B. Professional skills Decision making
The user/individual on the job needs to know how to:
SB1. check if the cargo, equipment, layout meets compliance
SB2. decide on the approproate response and documentation of different queries
and events
Plan and organize
The user/individual on the job needs to know how to:
SB3. plan and estimate the co-ordination required for resolving a querry.
SB4. maintain punctuality and respond in a timely manner
SB5. prioritize and execute tasks based on client requirements
SB6. make work plans and resource allocation plans
SB7. make checks on execution of work plans
SB8. be a team player and achieve joint goals
Customer centricity
The user/individual on the job needs to know how to:
SB9. adhere to assigned timelines and compliance requirements
SB10. address the urgency regarding various documentation and compliance
requests
Problem solving
The user/individual on the job needs to know how to:
SB11. identify trends/common mistakes in compliance to a procedure and its
documentation
SB12. co-ordinate and handle major issues with different departments
SB13. provide suggestions for meeting compliance in different activities
Analytical thinking
The user/individual on the job needs to know how to:
SB14. anticipate compliance requirements for different activities
SB15. review layout plans to ensure storage plan meets complaince
Critical thinking
The user/individual on the job needs to know and understand how to:
SB16. ensure complaince in all documentation and operations
SB17. check that all security measures and safety protocals are followed at all times
Analyse trends and prepare forecasts and schedules
Description This unit is analysing cargo trends, prepare forecasts and monitor schedules
Scope This unit/task covers the following:
• Analyse cargo trends and prepare forecasts
• Analyse operational trends and estimate maintenance
Range: Enterprise resource planning (ERP), Management information system (MIS)
reports, computer, projector, stationery, worksheets etc.
Performance Criteria(PC) w.r.t. the Scope
Element Performance Criteria
Analyse cargo trends
and prepare forecasts
To be competent, the user/individual on the job must be able to:
PC1. analyse the historic trends of different types of cargo handled in the terminal
and their frequency of operations
PC2. analyse cargo ageing in tank farm, pipeline usage, cleaning frequency, and
loss trends
PC3. analyse wagon and truck loading/unloading operations and their efficiencies
PC4. draw inferences regarding the most commonly stored cargo, average ageing,
daily transactions in terms of loading/unloading and pumping operations
PC5. estimate average utlization of tank capacities, operational costs, estimated
product wise costs, product loss trends etc.
PC6. suggest recommendation for increasing utilization of tanks, reducing
transactional losses, better monitoring of operational parameters, improving
loading/unloading turn around time, reducing costs etc.
PC7. prepare near future forecasts in terms of cargo mix and quantity based on
historic analysis and committed cargo traffic
PC8. estimate resources and budget required for handling the forecasted cargo mix
PC9. report the analysis and forecast to manager for inputs and further analysis
Analyse operational
trends to estimate
maintenance
To be competent, the user/ individual must be able to:
PC10. analyse tank equipment performance in terms of repairs undertaken, time
elapsed since last scheduled maintenance, frequency of emergency alarms,
component breakdown, cargo loss, rate of corrosion, etc.
PC11. estimate the maintenance requirement and frequency considering
performance and frequency of change of cargo
PC12. prepare maintenance schedules based on analysis and implement the same
PC13. prepare analysis and reports for manager
Knowledge and understanding (K)
A. Organizational
Context
(Knowledge of the
company /
organization and
its processes)
The individual on the job needs to know and understand:
KA1. organizational procedures and Standard Operating Procedures (SOPs) for
tasks at hand, documentation policy and emergency responses
KA2. security and safety procedures to be followed
KA3. reporting structure of the organization and the supplier for escalation of
issues
KA4. risk and impact of not following defined procedures/work instructions
KA5. coding system followed for different type of cargo and their distress codes
B. Technical
Knowledge
The individual on the job needs to know:
KB1. different type of cargo, their classification – A, B, C and their handling
procedure and precautions
KB2. SOPs for different operations, Petro-chemical standards – International
Electrotechnical Commission (IEC) 61511, IEC 61508, American Petroleum
Institute (API) 2350, National Fire Protection Association (NFPA), Oil industry
safety directorate guidelines and various committee recommendations
KB3. using fire extinguisher and protocols for emergencies, pollution and leakages
KB4. operations of control systems pumps, valves, alarm systems, etc.
KB5. use of analytical tools, ERPs, software
KB6. understanding of tanks, their life terms, repair and maintenance
requirements, etc.
KB7. basic understanding of different tank farm/ liquid terminal operation costs,
their norms and estimates
Skills (S)
A. Core Skills/
Generic Skills
Reading Skills
The user/individual on the job needs to know how to read:
SA1. information on documents and in ERP
SA2. various cargo labels and requirements
SA3. handling instructions/company log books and records
SA4. SOPs and safety manuals
SA5. reports, presentations, etc.
Writing Skills
The user/individual on the job needs to know how to:
SA6. written instructions, reports and analysis
SA7. prepare presentations, schedules, forecasts
Oral Communication (Listening and Speaking skills)
The user/individual on the job needs to know how to:
SA8. communicate clearly with managers, supervisors and other stakeholders
SA9. provide advice and guidance to peers and juniors
B. Professional Skills Decision Making
The user/individual on the job needs to know how to:
SB1. decide on ageing of the cargo
SB2. decide on forecasts of cargo
SB3. decide schedules for maintenance
Plan and Organize
The user/individual on the job needs to know how to:
SB4. clearly coordinate with ground staff for smooth operations
SB5. prioritize and execute tasks within the scheduled time limits
SB6. maintain schedules and punctuality
SB7. be a team player and achieve joint goals
Customer Centricity
The user/individual on the job needs to know how to:
SB8. adhere to the timelines and ensure that they are met
SB9. analyse customer requirements, cargo trends and prepare plans to handle the
same
Problem Solving
The user/individual on the job needs to know how to:
SB10. prepare right budgets to best utilize resources
SB11. identify areas for enhancing productivity and minimizing losses
Analytical Thinking
The user/individual on the job needs to know how to:
SB12. analyse cargo trends – ageing, frequency, etc.
SB13. analyse maintenance and tank operation trends
Critical Thinking
The user/individual on the job needs to know how to:
SB14. prepare correct estimates for forecasts and budgets
SB15. prepare and strictly implement maintenance schedules
SB16. identify areas for improvement
Maintain and monitor integrity and ethics in operation
Description This unit is about maintaining integrity, ensuring data security, and professional and
ethical practices
Scope This unit/task covers the following:
• Maintain integrity and ensure data security
• Professional and ethical practices
• Ensure regulatory compliance
Range: Standard Operating Procedures (SOP), computer, projector, worksheets,
stationery etc.
Performance Criteria(PC) w.r.t. the Scope
Element Performance Criteria
Maintain integrity
ensuring data
security
To be competent, the user/ individual must be able to:
PC1. refrain from indulging in corrupt practices
PC2. avoid using company’s funds, property or resources for undertaking personal
activities
PC3. protect customer’s information and ensure it is not missed
PC4. protect data and information related to business or commercial decisions
Professional and
ethical practices
To be competent, the user/ individual must be able to:
PC5. avoid acceptance of cash or kind from vendors for support or contract
negotiations
PC6. demonstrate and practice ethics in day-to-day processes and dealings with
customers and colleagues
PC7. avoid nepotism
PC8. consult supervisor or senior management when in situations that may require
differentiating between ethical and unethical
PC9. report promptly all violations of code of ethics
PC10. dress up and conduct in a professional manner
PC11. communicate with clients and stakeholders in a soft and polite manner
PC12. follow etiquettes in accordance to the place
Ensure regulatory
compliance
To be competent, the user/ individual must be able to:
PC13. check for regulatory documentation and compliances for the shop floor as per
information from the supervisor
PC14. perform activities considering the regulatory requirements
PC15. use Personal Protective Equipment (PPEs) in accordance to regulatory
requirements
PC16. identify the different types of dangerous goods and handling methodologies
PC17. follow the SOP for handling of different types of dangerous goods
PC18. consult supervisor or senior management when in situations that may require
differentiating between ethical and unethical
PC19. promptly report all regulatory violations
Knowledge and understanding (K)
A. Organizational
context
(Knowledge of the
company /
organization and
its processes)
The user/individual on the job needs to know and understand:
KA1. company’s policies on use of language
KA2. company’s Human Resources policies
KA3. company’s code of ethics
KA4. company’s whistle blower policy
KA5. company’s rules related to sexual harassment
KA6. company’s reporting structure
KA7. company’s documentation policy
B. Technical
knowledge
The user/individual on the job needs to know and understand:
KB1. principles of code of ethics and business ethics
KB2. various regulatory requirements
KB3. documentary compliance for various regulations
KB4. different dangerous shipment
KB5. regulations w.r.t dangerous shipment
Skills (S)
A. Core skills/
generic skills
Reading Skills
The individual on the job needs to know how to read:
SA1. company policy documents and work related documents
SA2. emails and written instructions
Writing Skills
The individual on the job needs to know how to fill:
SA3. documentation pertaining to ethics and regulatory requirement
Oral Communication (Listening and Speaking skills)
The individual on the job needs to know how to communicate with:
SA4. team members to work efficiently
SA5. peers and subordinates about information security and building trust
B. Professional skills
Decision making
The individual on the job needs to know how to:
SB1. identify a shipment as dangerous goods
SB2. assess if the situation needs to be reported regarding regulations
Plan and Organize
The individual on the job needs to know how to:
SB3. plan and organise actions as per company’s guidelines
Customer centricity
The individual on the job needs to know how to:
SB4. prevent company and customer information leakage
Problem solving
The individual on the job needs to know how to:
SB5. advise colleagues regarding sensitive issues pertaining to conduct and
regulations
Analytical Thinking
The individual on the job needs to know how to:
SB6. provide professional services diligently and with integrity
Critical Thinking
The individual on the job needs to know how to:
SB7. avoid defaming company’s name by indulging into pilferage or fiddling with
quality or quantity of shipment
SB8. be fair and reasonable in profession and disclose conflict of interests
Follow health, safety and security procedures in liquid logistics
Description This Occupational Standards (OS) unit is about ensuring compliance with health, safety
and security procedures at the workplace
Scope This unit/task covers the following:
• Follow health, safety and security procedures
• Ensure compliance to health, safety and security
• Prepare for disaster and pollution control response
Range: Personal Protective Equipment (PPE), Material Handling Equipment (MHE),
instructional material, alarms, safety guidelines, safety signs, computer, projector etc.
Performance Criteria(PC) w.r.t. the Scope
Element Performance Criteria
Follow health, safety
and security
procedures
To be competent, the user/ individual must be able to:
PC1. make note of all safety checks and comply with safety regulations
PC2. wear PPE such as goggles, ear plugs, helmet, mask, shoes, etc. as required
PC3. follow standard driving and equipment/ machine operating practice
PC4. follow protocol to initiate action in case of signs of any emergency situation
like accident or breach of safety
PC5. undertake periodical preventive health check ups
PC6. follow necessary standard operating procedures (SOP) and precautions while
handling dangerous and hazardous shipment
PC7. follow security procedures like green gate in port, customs area, factory
security, etc.
Ensure compliance to
health, safety and
security
To be competent, the user/ individual must be able to:
PC8. identify unsafe conditions and practices and report it to concerned authority
PC9. implement 5S at workplace
PC10. inspect the activity area and equipment for safe working condition
PC11. check that pathways/ emergency escape routes are clear and free from
grease/ oil
PC12. participate in fire drills
PC13. follow standard material handling procedures
PC14. hold ladders, platforms and hand rails in a safe position
PC15. check that the safety and security related tags, labels and signage are placed
on cargo
PC16. report in case of any violation
Prepare for disaster
and pollution control
response
To be competent, the user/ individual must be able to:
PC17. raise alarms and inform supervisors in case of any emergency – fire, leakage,
or pollution
PC18. coordinate with local authorities and nearby village representatives for
evacuation
PC19. follow SOP to contain the disaster or pollution – use fire extinguisher, start
emergency controls, close emergency valves, etc.
PC20. assist fellow workers in quick response and evaluation as per SOP
Knowledge and understanding (K)
A. Organizational
context
(Knowledge of the
company /
organization and
its processes)
The individual on the job needs to know and understand:
KA1. health, safety and security policies and procedures
KA2. special instructions for hazardous cargo handling
KA3. defined standard operating procedures
KA4. risk and impact of not following defined procedures/work instructions with
reference to health, safety and security operations
KA5. escalation matrix for reporting identified problem
B. Technical
knowledge
The individual on the job needs to know and understand:
KB1. basics of Occupational Safety and Health Administration (OSHA)
KB2. 5S implementation and practice
KB3. different type of cargo, their classification – A, B, C and their handling
procedure and precautions
KB4. SOPs for different operations, Petro-chemical standards – International
Electrotechnical Commission (IEC) 61511, IEC 61508, American Petroleum
Institute (API) 2350, National Fire Protection Association (NFPA), Oil industry
safety directorate guidelines and various committee recommendations
KB5. using fire extinguisher and protocols for emergencies
KB6. operations of control systems pumps, valves, alarm systems, etc.
KB7. necessary security procedures for airport, customs area, etc.
KB8. tools and equipment for material handling
KB9. standard material handling procedures while handling cargo
KB10. safety and security signage and their functions
KB11. different security tags, labels and signage
KB12. handling procedure for hazardous / fragile cargo
KB13. security procedures for dangerous / hazardous shipment
KB14. different PPE, their usage and purpose
KB15. safe driving techniques
Skills (S)
A. Core skills/
generic skills
Reading skills
The user/individual on the job needs to know how to read:
SA1. SOPs and safety precautions for different ground operations and handling
cargo
SA2. alarms, various gauges and meters regarding temperature, pressure and level
SA3. different documents related to security and movement of cargo
Writing skills
The user/individual on the job needs to know how to:
SA4. fill forms related to health, safety and security procedures
SA5. prepare reports regarding pollution and disaster control, accidents, etc.
Oral communication (listening and speaking skills)
The user/individual on the job needs to know how to:
SA6. communicate clearly with colleagues regarding safety procedures
SA7. share experience and guide peers
SA8. coordinate with local authorities and disaster management teams
B. Professional skills Decision making
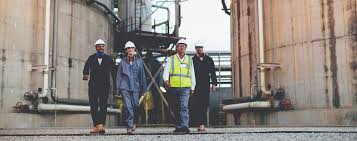
The user/individual on the job needs to know how to:
SB1. decide how to avoid any damage / accident to personal health / cargo
handled, whenever required
SB2. act objectively, rather than impulsively or emotionally when faced with
difficult/stressful or emotional situations
Plan and organize
The user/individual on the job needs to know how to:
SB3. plan clearance of area with safety of nearby population and workforce as top
priority
SB4. prioritize and execute tasks within the schedule time limits
SB5. plan and drive based on traffic and road condition using radio links/navigation
aids wherever available
Customer centricity
The user/individual on the job needs to know how to:
SB6. ensure safe and secure movement of liquid, cargo at all times
Problem solving
The user/individual on the job needs to know how to:
SB7. identify any threats on personal health, safety, security, etc. and take
appropriate actions
SB8. identify risks at the workplace and address them
Analytical thinking
The user/individual on the job needs to know how to:
SB9. analyse past mistakes and address them to avoid mishap in the future
Critical thinking
The user/individual on the job needs to know how to:
SB10. check that right safety measures and procedures are in place
SB11. quickly escalate and begin disaster management response
Conduct daily review and facilitate operations in tank farms
Description This unit is about conducting daily status reviews and facilitating daily operations in
multiple tank farms across regions
Scope This unit/task covers the following:
• Review status and facilitate daily operations
• Forecast and budget
• Approve workplans and allocate tasks
• Ensure compliance to legal and regulatory requirements
Range: Computers, Management information system (MIS), Enterprise resource
planning (ERP), performance review softwares, budgeting and forecasting softwares,
etc.

Performance Criteria (PC) w.r.t. the scope
Element Performance Criteria
Review status and
facilitate smooth
operations
To be competent, the user/individual on the job must be able to:
PC1. monitor cargo levels, tank farm alarms and infrastructure status, utilization
status, repair and cargo handling schedules, etc. on the Internet of Things
(IOT) system controls
PC2. review reports of loading, pumping and cleaning and high priority activities
performed
PC3. review work schedules, resource allocation and make amendments as
required
PC4. review inspection, fitness and maintenance reports
PC5. coordinate with port authorities, clients, Partnering Government Agencies
(PGAs), etc. for resolving cargo transfers, pending cases, tank repairs, etc.
PC6. monitor resource performance and take corrective action to improve
utilisation
PC7. periodically inspect tank farms to check for safety compliance, cargo storage
and handling, cleanliness, use of adequate Personal Protective Equipment
(PPEs), resources, fitness of equipment and personnel, etc.
Forecast and budget To be competent, the user/ individual must be able to:
PC8. analyse cargo storage and handling trends across tank farms
PC9. prepare storage and revenue forecasts and budget for tank farm units
PC10. set-up consensus meetings with peers and seniors and get their approval on
the forecasts and budgets
PC11. make amendments in budgets periodically based on review of actual
performance
Approve work plans
and allocate tasks
To be competent, the user/individual on the job must be able to:
PC12. assess tasks, identify priorities and inform supervisors and executives
PC13. review and approve tank cleaning, maintenance schedules, work plans shared
by supervisors
PC14. review and approve disaster management plans, drill schedules shared by
supervisors
Ensure compliance to
legal and regulatory
requirements
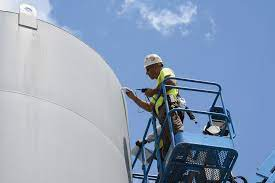
To be competent, the user/ individual must be able to:
PC15. monitor compliance to local, country and international laws and processes on
a regular basis
PC16. monitor compliance with respect to cargo handling and storage norms
particularly for hazardous cargo
PC17. identify areas of non-compliance, and implement policies for compliances
PC18. conduct inspections to check compliance to Standard Operating Procedures
(SOPs) and regulations
Knowledge and Understanding (K)
A. Organizational
Context
(Knowledge of the
company /
organization and
its processes)
The individual on the job needs to know and understand:
KA1. organizational procedures
KA2. documentation and reporting as per organization’s mandate
KA3. security procedures to be followed
KA4. escalation matrix for reporting identified problems
KA5. risk and impact of not following defined procedures/work instructions
KA6. coding system followed to label cargo
KA7. Information Technology (IT) system and ERP system of the organization
B. Technical
Knowledge
The individual on the job needs to know and understand:
KB1. basics of operations in a port terminals and liquid terminals
KB2. different type of cargo, their classification – A, B, C and their handling
procedure and precautions
KB3. SOPs for different operations, Petro-chemical standards – International
Electrotechnical Commission (IEC) 61511, IEC 61508, American Petroleum
Institute (API) 2350, National Fire Protection Association (NFPA), Oil industry
safety directorate guidelines and various committee recommendations
KB4. vessel layout and loading and unloading activities
KB5. procedures of tank cleaning, cargo movement
KB6. requirements regarding handling of cargo
KB7. handling of hazardous and non-hazardous cargo – – International Maritime
Dangerous Goods (IMDG) code
KB8. special characteristics and handling requirements of cargo, if any
KB9. ERP and automated controls for tank farms
KB10. trend analysis, budgeting, planning and forecasting
A. Core skills/
generic skills
Reading skills
The user/individual on the job needs to know how to read:
SA1. written instructions, reports, ERP data
SA2. system alarms, cargo levels, etc on online systems
SA3. checklists
Writing skills
The user/individual on the job needs to know how to write:
SA4. various reports, letters, presentations, documents
SA5. instructions
SA6. training pedagogy
Oral communication (listening and speaking skills)
The user/individual on the job needs to know how to:
SA7. communicate with supervisors, surveyors, clients, stakeholders custom and
port officers, PGAs
SA8. coordinate with local authorities, external support agencies
B. Professional skills Decision making
The user/individual on the job needs to know how to:
SB1. decide on resource requirement, budgets, maintenance schedules, forecasts
SB2. decide key clients for business development
SB3. decide on strategies for operations, disaster management, process
improvement
Plan and organize
The user/individual on the job needs to know how to:
SB4. plan and estimate the co-ordination required for resolving a querry
SB5. maintain punctuality
SB6. respond to the client in a timely manner
SB7. prioritize and execute tasks based on client requirements
SB8. be a team player and achieve joint goals
Customer centricity
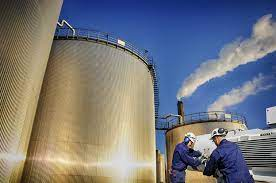
The user/individual on the job needs to know how to:
SB9. adhere to the customer timelines
SB10. address the urgency regarding approvals for cargo handling, repairs, etc.
Problem solving
The user/individual on the job needs to know how to:
SB11. coordinate to resolve stuck cases for cargo transfers, repair requirements, etc.
SB12. identify trends and plan accordingly to improve processes
SB13. identify bottlenecks and operational problems and suggest remedial action
Analytical thinking
The user/individual on the job needs to know how to:
SB14. analyse trends and prepare budgets and forecasts
SB15. identify trends and plan accordingly to improve processes
Critical thinking
The user/individual on the job needs to know and understand how to:
SB16. review and ensure safe handling and storage of liquid cargo
SB17. ensure adequate utilization of tank farm resources
SB18. adapt and implement global best practices
Perform ship and yard planning
Description This unit is about about container tracking and developing vessel berthing plans
Scope This This unit/task covers the following:
• Plan yard to receive cargo
• Inspect yard to check for space utilization, segregation of cargo, cleanliness,
necessary precautions
Range: Stationery, Standard Operating Procedures (SOP), Radio Frequency
Identification (RFID) scanner, bar code scanner, markers, Personal Protective
Equipment (PPEs), Enterprise resource planning (ERP), computer, display board,
printer, Material Handling Equipment (MHEs), etc
Performance Criteria(PC) w.r.t. the Scope
Element Performance Criteria
Plan yard to receive
cargo
To be competent, the user/ individual must be able to:
PC1. obtain information regarding the vessel details – docking schedule and berth,
bays and containers to be unloaded and loaded
PC2. obtain information regarding movement of containers / cargo from port
terminals to Container Freight Station (CFS)/ Inland Container Depot (ICD) or
client
PC3. check yard’s capacity utilization and open bays and locations
PC4. assess the quantity of cargo to be moved and plan storage space for cargo
PC5. allocate resources for cargo movement
PC6. communicate the task at hand to cargo equipment handlers, manual cargo
handlers and lifting and vessel supervisors
PC7. discuss the plan for cargo movement with the operators to finalise the
container/ cargo movement plan
PC8. review that all equipment and workforce is ready for operations at the time of
vessel docking / transport arrival
PC9. review that the necessary precautions and PPEs have been taken
PC10. deploy resources for loading/ unloading as per cargo stowage plan
PC11. coordinate with cargo surveyor for safe and secured loading/ unloading
Inspect yard to check
for space utilization,
segregation of cargo,
cleanliness,
necessary
precautions
To be competent, the user/ individual must be able to:
PC12. conduct periodic inspections of the yard
PC13. check for cleanliness, adequate use of PPEs, regulations and norms for
workforce are clearly followed
PC14. check that cargo bays are clearly marked and segregated, containers and
cargo are stored as per prescribed norms
PC15. check that equipment is parked at right positions
PC16. check that all necessary precautions for storage of hazardous cargo is in place
including emergency services
PC17. prepare inspection report highlighting any anomaly or changes, as required
Knowledge and understanding (K)
A. Organizational
context
(Knowledge of
the company /
organization and
its processes)
The individual on the job needs to know and understand:
KA1. organizational procedures and SOPs for tasks at hand, documentation policy
and emergency responses
KA2. security and safety procedures to be followed
KA3. reporting structure of the organization and the supplier for escalation of
issues
KA4. risk and impact of not following defined procedures/work instructions
KA5. coding system followed for different type of cargo and their distress codes
B. Technical
knowledge
The individual on the job needs to know and understand:
KB1. basics of operations in a port terminal, ICD and CFS
KB2. use of various cargo handling equipment
KB3. use of rope , flags and other manual equipment
KB4. vessel layout and loading and unloading activities
KB5. procedures of tank cleaning, cargo movement
KB6. requirements regarding handling of cargo
KB7. different type of vessels and cargo and container sizes
KB8. different type of cranes and MHEs – their capacities, constraints and usage
KB9. handling of hazardous and non-hazardous cargo
KB10. marking of material and people movement areas
KB11. stuffing and de-stuffing norms with respect to different cargo
KB12. special characteristics and handling requirements of shipments, if any
Skills (S)
A. Core skills/
generic skills
Reading skills
The user/individual on the job needs to know how to read:
SA1. written instructions
SA2. shiping manifest, Bill of lading shipping bills and related documents
SA3. ERP and computer generated reports
SA4. cargo stowage plans and vessel plans
SA5. SOPs and safety regulation manuals
Writing skills
The user/individual on the job needs to know how to write:
SA6. work-orders and instructions
SA7. checklist of activities, delays, undelivered items, contacts, etc
SA8. daily reports
Oral communication (listening and speaking skills)
The user/individual on the job needs to know how to:
SA9. communicate with customers, fireght operators, transporters, shipping
companies, other supervisors and port authorities
SA10. communicate with cargo equipment operators and ground staff over Very
high frequency (VHF) radio
SA11. guide cargo handlers for smooth operations
B. Professional skills Decision making
The user/individual on the job needs to know how to:
SB1. decide on required workforce and equipment for performing a particular task
SB2. assess the environmental condition and type of cargo to assess if it is safe for
operations
SB3. resolve a problem quickly internally
SB4. prioritise shipments
SB5. decide on deployment of alternate resources when required
Plan and organize
The user/individual on the job needs to know how to:
SB6. plan and estimate the co-ordination required for resolving a querry.
SB7. maintain punctuality
SB8. respond to the client in a timely manner
SB9. prioritize and execute tasks based on client requirements
SB10. make work plans and resource allocation plans
SB11. make checks on execution of work plans
SB12. be a team player and achieve joint goals
Customer centricity
The user/individual on the job needs to know how to:
SB13. adhere to the customer timelines
SB14. address the urgency regarding shipments and activities
Problem solving
The user/individual on the job needs to know how to:
SB15. make adjustment to working requirements for difficult weathers and
hazardous goods
SB16. identify trends/common causes for delays, damages, etc.
SB17. co-ordinate and handle major issues with different departments
SB18. identify bottlenecks and operational problems and suggest remedial action
Analytical thinking
The user/individual on the job needs to know how to:
SB19. assess the resource requirement for a particular task at hand
SB20. assess and prepare for backup resources in case of delays
SB21. plan for cargo movement so that the resources and storage space is optimally
utilized
Critical thinking
The user/individual on the job needs to know and understand how to:
SB22. resolve issues in a quicks and cost effective manner
SB23. develop work plans factoring in external factors
SB24. check that all security measures and safety protocals are followed at all times