Container Freight Station (CFS) and Inland Container Depot (ICD) Supervisor (1 years diploma)
Container Freight Station (CFS) and Inland Container Depot (ICD) Supervisor click here
Brief Job Description: The individual allocates resources for cargo handling and
container movement, plans and supervises repair and maintenance of
containers, while overseeing operations and general cleanliness within a CFS or
ICD.
Qualifications Pack for CFS and ICD supervisor
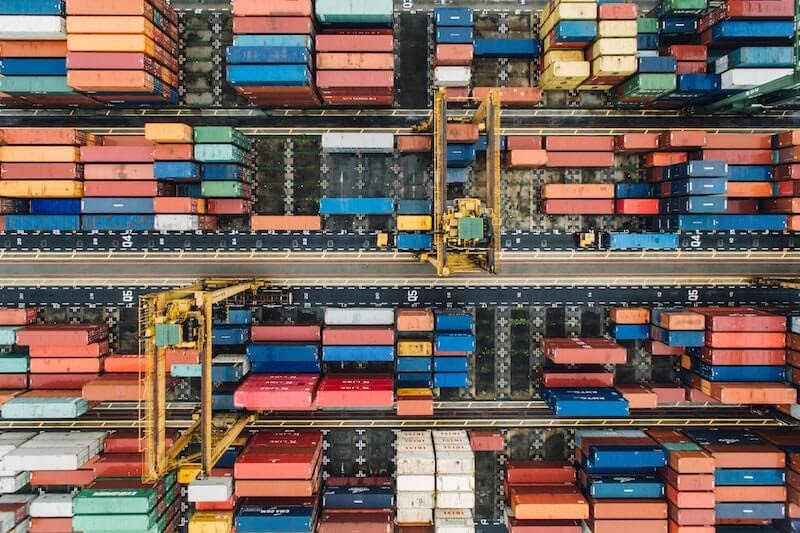
Option
Option 1: Yard and Cargo Handling
The unit is about supervising cargo handling and storage operations in the port
terminal, ICD or CFS
Personal Attributes:
The job holder should plan and budget for activities. S/he should have
digital/computer skills and mathematical aptitude to estimate yard space
requirement, and quantity estimation. S/he should have English and Vernacular
language proficiency, demonstrable in spoken, written and oral communication
Description
Core Skills/Generic
Skills
Core Skills or Generic Skills are a group of skills that are key to learning and
working in today’s world. These skills are typically needed in any work
environment. In the context of the NOS, these include communication related
skills that are applicable to most job roles.
Function
Function is an activity necessary for achieving the key purpose of the sector,
occupation, or area of work, which can be carried out by a person or a group
of persons. Functions are identified through functional analysis and form the
basis of NOS.
Job role Job role defines a unique set of functions that together form a unique
employment opportunity in an organization.
Knowledge and
Understanding
Knowledge and Understanding are statements which together specify the
technical, generic, professional and organizational specific knowledge that an
individual needs in order to perform to the required standard.
National Occupational
Standards (NOS) NOS are Occupational Standards which apply uniquely in the Indian context
Electives
Electives are NOS/set of NOS that are identified by the sector as contributive
to specialization in a job role. There may be multiple electives within a QP for
each specialized job role. Trainees must select atleast one elective for the
successful completion of a QP with Electives
Options
Options are NOS/set of NOS that are identified by the sector as additional
skills. there may be multiple options within a QP. It is not mandatory to select
any of the options to complete a QP with Options.
Unit Code Unit code is a unique identifier for an Occupational Standard, which is
denoted by an ‘N’
Unit Title Unit title gives a clear overall statement about what the incumbent should be
able to do.
Occupation Occupation is a set of job roles, which perform similar/related set of functions
in an industry.
Organizational Context
Organizational Context includes the way the organization is structured and
how it operates, including the extent of operative knowledge managers have
of their relevant areas of responsibility.
Performance Criteria Performance Criteria are statements that together specify the standard of
performance required when carrying out a task.
Qualifications
Pack(QP)
Qualifications Pack comprises the set of NOS, together with the educational,
training and other criteria required to perform a job role. A Qualifications
Pack is assigned a unique qualification pack code.
Qualifications Pack
Code
Qualifications Pack Code is a unique reference code that identifies a
qualifications pack.
Scope Scope is the set of statements specifying the range of variables that an
individual may have to deal with in carrying out the function which have a
critical impact on the quality of performance required.
Sector
Sector is a conglomeration of different business operations having similar
businesses and interests. It may also be defined as a distinct subset of the
economy whose components share similar characteristics and interests.
Sub-Sector Sub-sector is derived from a further breakdown based on the characteristics
and interests of its components.
Sub-functions Sub-functions are sub-activities essential to fulfil the achieving the objectives
of the function.
Technical Knowledge Technical Knowledge is the specific knowledge needed to accomplish specific
designated responsibilities.
Description
CFS Container Freight Station
DG Directorate General
ERP Enterprise Resource Planning
EXIM Export Import
FCL Full Container Load
GPS Global Positioning System
HAZCHEM Hazardous Chemicals
HR Human Resources
ICD Inland Container Depots
IMDG International Maritime Dangerous Goods
LCL Less than Container Load
MHE Material Handling Equipment
MIS Management Information Systems
NSQF National Skills Qualifications Framework
OH&S Occupational Health and Safety
OS Occupational Standards
OSHA Occupational Safety and Health Administration

PPE Personal Protective Equipment
QP Qualifications Pack
RFID Radio-Frequency Identification
SOP Standard Operating Procedure
VHF Very High Frequency
Allocate resources and streamline operations at yard
Description This unit is about allocating manpower and equipment for execution of work;
supervision and streamlining operations at a port terminal, ICD or CFS
Scope This unit/task covers the following:
• Prepare daily work plan and allocate resources
• Monitor daily operations
• Yard Inspection
• Resolve escalated issues
Range: Stationery, Radio-Frequency Identification (RFID) scanner, bar code scanner,
plastic bags, markers, Personal Protective Equipment (PPEs), Enterprise Resource
Planning (ERP), computer, printers, Global Positioning System (GPS) tracker,
Material Handling Equipment (MHEs), etc.
Performance Criteria(PC) w.r.t. the scope
Element Performance Criteria
Prepare daily work
plan and allocate
resources
To be competent, the user/ individual must be able to:
PC1. obtain details of vessel docking plans, cargo and container movement plans,
etc.
PC2. develop daily work plan factoring in priority cases, time bound
requirements, special handling requirements, etc.
PC3. get the work plan approved from the yard manager or Container Freight
Station (CFS)/ Inland Container Depot (ICD) manager and allocate tasks to
workers and associates
PC4. budget and allocate the requisite MHE for different tasks at hand
Monitor daily
operations
To be competent, the user/individual on the job must be able to:
PC5. inspect yard for markings/demarcation, storage and cleanliness, as per
safety norms
PC6. monitor cargo loading, unloading and movement operations
PC7. engage resources in alternate operation when there is a delay of planned
operations
PC8. allocate additional and ad-hoc manpower and equipment during exigency
PC9. escalate issues regarding MHE operations, transporter delays, vessel delays,
accidents, damages, etc. to manager
PC10. provide corrective and preventive action plans based on accident and
damage reports
PC11. liaise with port officials, customs officials and external stakeholders
Yard inspection To be competent, the user/ individual must be able to:
PC12. conduct periodic inspection of the yard for cleanliness, usage of PPEs and
adherence to Standard Operating Procedures (SOP) and regulations
PC13. ensure cargo bays are clearly marked and segregated, containers and cargo
are stored as per prescribed norms
PC14. check for parking and positioning of equipment as per SOP
PC15. ensure all necessary precautions for storage of hazardous cargo are
complied with and emergency services are available
PC16. submit inspection report highlighting any deviation from SOP
Resolve escalated
issues
To be competent, the user/ individual must be able to:
PC17. review escalated issues and identify root cause for providing corrective
action
PC18. provide technical guidance to the team for execution
PC19. escalate the issues to manager when external or additional help is required
PC20. coordinate with other departments, transporters, freight operators, port
authorities, shipping companies and others to resolve escalations if required
Knowledge and understanding (K)
A. Organizational
context (Knowledge of
the company /
organization
and its
processes)
The individual on the job needs to know and understand:
KA1. organizational procedures
KA2. documentation and reporting as per organization’s mandate
KA3. security procedures to be followed
KA4. escalation matrix for reporting identified problems
KA5. risk and impact of not following defined procedures/work instructions
KA6. coding system followed to label cargo
KA7. IT system and ERP system of the organization
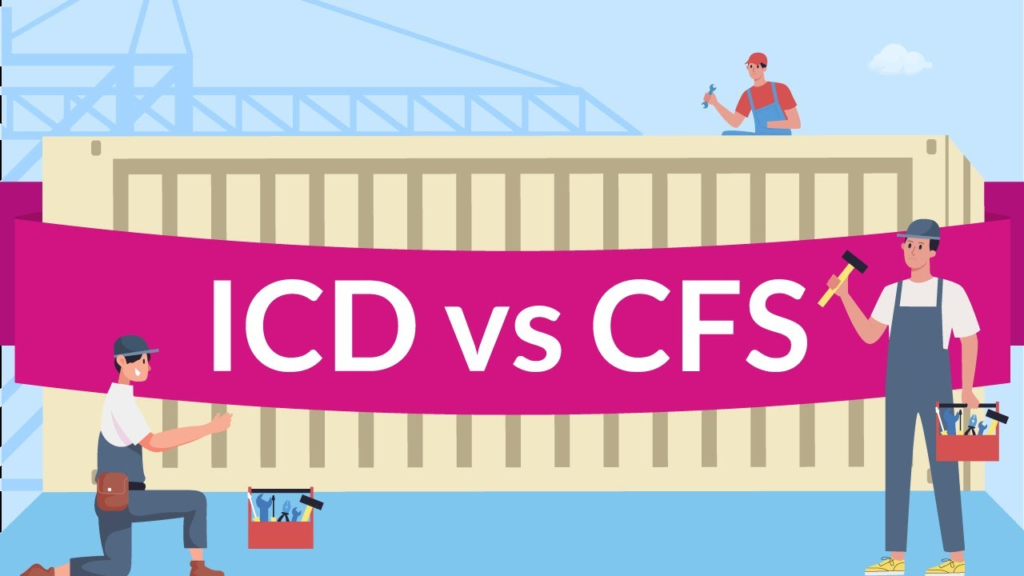
B. Technical
knowledge
The individual on the job needs to know and understand:
KB1. yard operations and its technicalities
KB2. different type of cranes and MHEs – their capacities, constraints and usage
KB3. use of rope, flags and other manual equipment
KB4. vessel layout and loading and unloading activities
KB5. different type of vessels, cargo, container sizes and their handling
KB6. handling of hazardous and non-hazardous cargo – International Maritime
Dangerous Goods (IMDG) code
KB7. stuffing and de-stuffing norms with respect to different cargo and its special
characteristics
KB8. handling of hazardous and non-hazardous cargo – – IMDG code
KB9. special characteristics and handling requirements of shipments, if any
Skills (S)
A. Core skills/
generic skills
Reading skills
The user/individual on the job needs to know how to read:
SA1. written instructions
SA2. shiping manifest, Bill of lading shipping bills and related documents
SA3. ERP and computer generated reports
Allocate resources and streamline operations at port, ICD and CFS
SA4. cargo stowage plans and vessel plans
SA5. SOPs and safety regulation manuals
Writing skills
The user/individual on the job needs to know how to write:
SA6. work-orders and instructions
SA7. checklist of activities, delays, undelivered items, contacts, etc
SA8. daily reports
Oral communication (listening and speaking skills)
The user/individual on the job needs to know how to:
SA9. communicate with customers, fireght operators, transporters, shipping
companies, other supervisors and port authorities
SA10. communicate with cargo equipment operators and ground staff over VHF
radio
SA11. guide cargo handlers for smooth operations
B. Professional
skills
Decision making
The user/individual on the job needs to know how to:
SB1. decide on required workforce and equipment for performing a particular
task
SB2. assess the environmental condition and type of cargo to assess if it is safe
for operations
SB3. resolve a problem quickly internally
SB4. prioritise shipments
SB5. decide on deployment of alternate resources when required
Plan and organize
The user/individual on the job needs to know how to:
SB6. plan and estimate the co-ordination required for resolving a querry.
SB7. maintain punctuality
SB8. respond to the client in a timely manner
SB9. prioritize and execute tasks based on client requirements
SB10. make work plans and resource allocation plans
SB11. check on execution of work plans
SB12. be a team player and achieve joint goals
Customer centricity
The user/individual on the job needs to know how to:
SB13. adhere to the customer timelines
SB14. address the urgency regarding shipments and activities
Problem solving
The user/individual on the job needs to know how to:
SB15. make adjustment to working requirements for difficult weathers and
hazardous goods
SB16. identify trends/common causes for delays, damages, etc.
SB17. co-ordinate and handle major issues with different departments
SB18. identify bottlenecks and operational problems and suggest remedial action
Analytical thinking
The user/individual on the job needs to know how to:
SB19. assess the resource requirement for a particular task at hand
SB20. assess and prepare for backup resources in case of delays
SB21. plan for cargo movement so that the resources and stroage space is
optimally utilised
Critical thinking
The user/individual on the job needs to know and understand how to:
SB22. resolve issues in a qucik and cost effective manner
SB23. develop work plans factoring in external factors
SB24. check that all security measures and safety protocals are followed at all
times
Extract and analyse shipment information from IT systems
Description This unit is about reading shipment tracking ERPs, extracting information and
analysing the same
Scope This unit/task covers the following:
• Feed information into the ERP
• Track position of consignments and containers globally
• Document and report
Range: Stationery, Standard Operating Procedures (SOP), Radio-Frequency
Identification (RFID) scanner, bar code scanner, markers, ERP, computer, display
board, printer, etc.
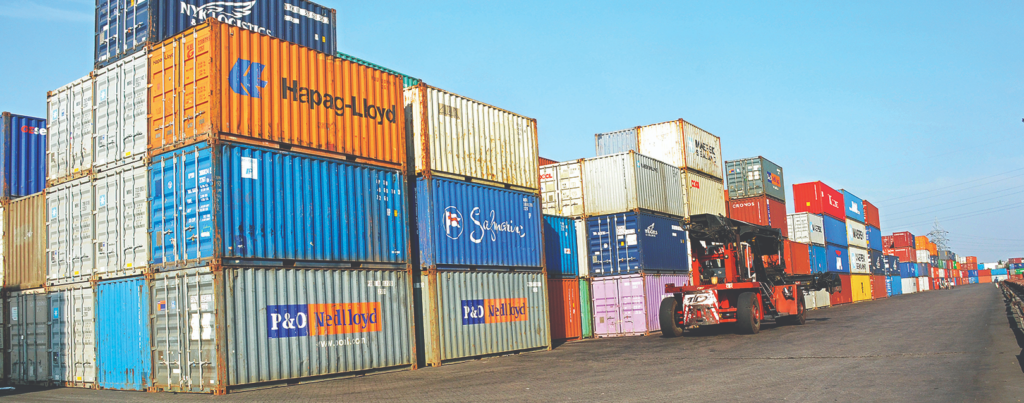
Performance Criteria(PC) w.r.t. the scope
Element Performance Criteria
Feed information
into ERP
To be competent, the user/ individual must be able to:
PC1. obtain details of all containers moving in and out the Container Freight
Station (CFS) including container number, cargo content, destination, shipper
and vessel details, date of servicing, etc.
PC2. cross verify container status based on physical inspection report and yard
utilization report
PC3. correct the information in the shipment tracking ERP
Track position of
consignments and
containers globally
To be competent, the user/ individual must be able to:
PC4. track position of container in the ERP by feeding the Container index number
PC5. extract information regarding present location, shipper details, cargo content,
estimated date of arrival at destination, etc.
PC6. estimate equipment and workforce requirement considering the type of
cargo, stuffing/destuffing/packing requirement based on location and route
Document and report To be competent, the user/ individual must be able to:
PC7. prepare detailed documentation and present the analysis to the CFS or Inland
Container Depots (ICD) manager
PC8. highlight any accidents, issues in tracking, etc.
PC9. suggest corrective action in case of container packing mistakes, sealing errors,
that has led to damage or accidents
Knowledge and understanding (K)
A. Organizational
context
(Knowledge of the
company /
organization and
its processes)
The individual on the job needs to know and understand:
KA1. organizational procedures
KA2. documentation and reporting as per organization’s mandate
KA3. security procedures to be followed
KA4. escalation matrix for reporting identified problems
KA5. risk and impact of not following defined procedures/work instructions
KA6. coding system followed to label cargo
KA7. IT system and ERP system of the organization
B. Technical
knowledge
The individual on the job needs to know and understand:
KB1. basics of operations in a port terminal, ICD and CFS
KB2. use of various cargo handling equipment
KB3. vessel layout and loading and unloading activities
KB4. procedures of tank cleaning, cargo movement
KB5. requirements regarding handling of cargo
KB6. different type of vessels and cargo and container sizes
KB7. different type of cranes and Material Handling Equipment (MHEs) – their
capacities, constraints and usage
KB8. handling of hazardous and non-hazardous cargo – – International Maritime
Dangerous Goods (IMDG) code

KB9. marking of material and people movement areas
KB10. stuffing and de-stuffing norms with respect to different cargo
KB11. special characteristics and handling requirements of shipments, if any
KB12. different container tracking ERPs and their operation
KB13. location of different destinations on the map and the globe
Skills (S)
C. Core skills/
generic skills
Reading skills generic skills
The user/individual on the job needs to know how to read:
SA1. written instructions
SA2. shiping manifest, Bill of lading shipping bills and related documents
SA3. ERP and computer generated reports
SA4. cargo stowage plans and vessel plans
SA5. SOPs and safety regulation manuals
Writing skills
The user/individual on the job needs to know how to write:
SA6. work-orders and instructions
SA7. checklist of activities, delays, undelivered items, contacts, etc
SA8. daily reports
Oral communication (listening and speaking skills)
The user/individual on the job needs to know how to:
SA9. communicate with customers, freight operators, transporters, shipping
companies, other supervisors and port authorities
SA10. communicate with cargo equipment operators and ground staff over VHF
radio
SA11. guide cargo handlers for smooth operations
D. Professional skills Decision making
The user/individual on the job needs to know how to:
SB1. decide if a particular shipment has been correctly tagged in the ERP
SB2. decide the ageing and decide for container repairs and servicing
Plan and organize
The user/individual on the job needs to know how to:
SB3. plan and estimate the co-ordination required for resolving a querry.
SB4. maintain punctuality
SB5. respond to the client in a timely manner
SB6. prioritize and execute tasks based on client requirements
SB7. make work plans and resource allocation plans
SB8. make checks on execution of work plans
SB9. be a team player and achieve joint goals
Customer centricity
The user/individual on the job needs to know how to:
SB10. adhere to the customer timelines
SB11. address the urgency regarding shipments and activities
Problem solving
The user/individual on the job needs to know how to:
SB12. make adjustment to effectively track missing containers
SB13. identify trends/common causes for delays, damages, etc.
SB14. co-ordinate and handle major issues with different departments
SB15. identify bottlenecks and operational problems and suggest remedial action
Analytical thinking
The user/individual on the job needs to know how to:
SB16. assess if the availble resources fit for the type and volume of cargo handled as
per ERP
SB17. identify commonly carried cargo and routes and destination
SB18. plan for container repair and servicing
Critical thinking
The user/individual on the job needs to know and understand how to:
SB19. resolve issues in a qucik and cost effective manner
SB20. develop inferences based on analysis and data of ERPs
SB21. check that all security measures and safety protocals are followed at all times
for all its containers across the globe
Plan and check for optimal utilization of yard space
Description This unit is about planning to ensure optimal utilization of yard space within the port,
CFS or ICD and supervision of timely cargo movement
Scope This unit/task covers the following:
• Review yard space utilization
• Assess storage requirement for incoming cargo
• Coordinate for timely movement of cargo
• Inspect yard
Range: Stationery, Standard Operating Procedures (SOP), Radio-Frequency
Identification (RFID) scanner, bar code scanner, markers, Enterprise Resource
Planning (ERP), computer, display board, printer, etc.
Performance Criteria(PC) w.r.t. the scope
Element Performance Criteria
Review yard space
utilization
To be competent, the user/ individual must be able to:
PC1. review the yard and bay space utilization by cargo and container and assess
current available storage capacity
PC2. review ageing of different containers and dry bulk cargo that has come onto
the port / CFS and are due for movement to the CFS/ client respectively
PC3. conduct meeting with yard staff and check for reasons for over or
underutilization of yard space, reasons for delay in cargo movement and take
corrective action
PC4. escalate issues to terminal manager if required
Assess storage
requirement of
incoming cargo
To be competent, the user/ individual must be able to:
PC5. obtain details of vessel berthing plan and cargo loading and unloading plan
into the CFS, ICD
PC6. check if the yard has appropriate yard capacity to handle the incoming cargo
PC7. make adjustment by shipping out aged cargo onto the CFS, shipper or
exporting the cargo onto the vessel (port in case of CFS)
PC8. identify and finalise yards and bays for storage of incoming cargo considering
the various demarcations and precautions to be taken, particularly for
hazardous and dry bulk cargo
PC9. prepare cargo storage plans based on vessel berthing plan and get it
approved from the terminal manager
PC10. communicate the cargo storage plan to the cargo handlers, lifting supervisors
and vessel planners
Coordinate for timely
movement of cargo
To be competent, the user/ individual must be able to:
PC11. coordinate with vessels, transporters and shippers for movement cargo to
Plan and ensure optimal utilization of yard space

and from the CFS/ICD
PC12. oversee movement of cargo from port terminal, CFS via rail and road lines
and export via vessels
PC13. review cargo movement documentation and ensure correctness
PC14. prepare report on cargo storage plans, their adherence, cargo movement
plans and cargo ageing
Inspect yard To be competent, the user/ individual must be able to:
PC15. check for cleanliness, adequate use of Personal Protective Equipment (PPEs),
regulations and norms for workforce are clearly followed
PC16. ensure that cargo bays are clearly marked and segregated, containers and
cargo are stored as per prescribed norms
PC17. inspect that equipment are parked are right positions
PC18. confirm that all necessary precautions for storage of hazardous cargo is in
place including emergency services
PC19. prepare inspection report highlighting any anomalies or changes, as required
Knowledge and understanding (K)
A. Organizational
context (Knowledge
of the
company /
organization
and its
processes)
The individual on the job needs to know and understand:
KA1. organizational procedures
KA2. documentation and reporting as per organization’s mandate
KA3. security procedures to be followed
KA4. escalation matrix for reporting identified problems
KA5. risk and impact of not following defined procedures/work instructions
KA6. coding system followed to label cargo
KA7. IT system and ERP system of the organization
B. Technical
knowledge
The individual on the job needs to know and understand:
KB1. basics of operations in a port terminal, ICD and CFS
KB2. use of various cargo handling equipment
KB3. use of rope , flags and other manual equipment
KB4. vessel layout and loading and unloading activities
KB5. procedures of tank cleaning, cargo movement
KB6. requirements regarding handling of cargo
KB7. different type of vessels and cargo and container sizes
KB8. different type of cranes and MHEs – their capacities, constraints and usage
KB9. handling of hazardous and non-hazardous cargo – International Maritime
Dangerous Goods (IMDG) code
KB10. marking of material and people movement areas
KB11. stuffing and de-stuffing norms with respect to different cargo
KB12. special characteristics and handling requirements of shipments, if any
Skills (S)
C. Core skills/ Reading skills generic skills
The user/individual on the job needs to know how to read:
SA1. written instructions
SA2. shiping manifest, Bill of lading shipping bills and related documents
SA3. ERP and computer generated reports
SA4. cargo stowage plans and vessel plans
SA5. SOPs and safety regulation manuals
Writing skills
The user/individual on the job needs to know how to write:
SA6. work-orders and instructions
SA7. checklist of activities, delays, undelivered items, contacts, etc
SA8. daily reports
Oral communication (listening and speaking skills)
The user/individual on the job needs to know how to:
SA9. communicate with customers, freight operators, transporters, shipping
companies, other supervisors and port authorities
SA10. communicate with cargo equipment operators and ground staff over VHF
radio
SA11. guide cargo handlers for smooth operations
D. Professional
skills
Decision making
The user/individual on the job needs to know how to:
SB1. decide on required workforce and equipment for performing a particular task
SB2. assess the environmental condition and type of cargo to assess if it is safe for
operations
SB3. resolve a problem quickly internally
SB4. prioritise shipments
SB5. decide on deployment of alternate resources when required
Plan and organize
The user/individual on the job needs to know how to:
SB6. plan and estimate the co-ordination required for resolving a querry.
SB7. maintain punctuality
SB8. respond to the client in a timely manner
SB9. prioritize and execute tasks based on client requirements
SB10. make work plans and resource allocation plans
SB11. make checks on execution of work plans
SB12. be a team player and achieve joint goals
Customer centricity
The user/individual on the job needs to know how to:
SB13. adhere to the customer timelines
SB14. address the urgency regarding shipments and activities
Problem solving
The user/individual on the job needs to know how to:
SB15. make adjustment to working requirements for difficult weathers and
hazardous goods
SB16. identify trends/common causes for delays, damages, etc.
SB17. co-ordinate and handle major issues with different departments
SB18. identify bottlenecks and operational problems and suggest remedial action
Analytical thinking
The user/individual on the job needs to know how to:
SB19. assess the resource requirement for a particular task at hand
SB20. assess and prepare for backup resources in case of delays
SB21. plan for cargo movement so that the resources and stroage space is optimally
utilised
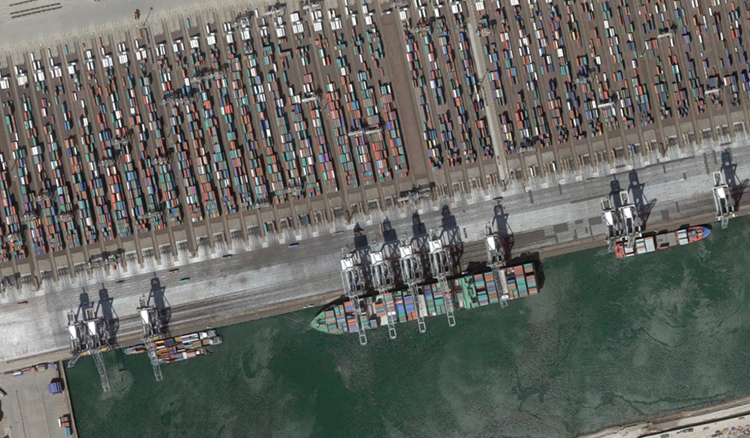
Critical thinking
The user/individual on the job needs to know and understand how to:
SB22. resolve issues in a qucik and cost effective manner
SB23. develop work plans factoring in external factors
SB24. check that all security measures and safety protocals are followed at all times
Plan and coordinate for optimal utilization of available containers
Description The unit is about and planning and coordinating for utilization of available containers
and their stuffing and cargo containerisation
Scope This unit/task covers the following:
• Identify and use available containers
• Allocate resources for container stuffing and de-stuffing
• Allocate resources for container handling
• Review gate movement of containers and reporting
Range: Stationery, Standard Operating Procedures (SOP), Personal Protective
Equipment (PPE), Material Handling Equipment (MHEs), Radio-Frequency
Identification (RFID) scanner, bar code scanner, markers, Enterprise Resource
Planning (ERP), computer, display board, printer, etc.
Performance Criteria(PC) w.r.t. the scope
Element Performance Criteria
Identify and use
available containers
To be competent, the user/ individual must be able to:
PC1. track status of containers in the ERP and identify containers that are empty or
returning from servicing or repairs, and containers that are carrying Less than
Container Load (LCL) load
PC2. check with shipper the requirement regarding the type of cargo and if Full
Container Load (FCL) or LCL is required and recommend solution with
available container
PC3. check that necessary precaution and segregation of type of cargo has been
considered while allocating LCL containers
PC4. coordinate with client and finalise the timelines for container loading and
movement
Allocate resources for
container stuffing
and de-stuffing
To be competent, the user/ individual must be able to:
PC5. obtain the weekly container movement plan and prepare the daily stuffing
and de-stuffing plan
PC6. budget and allocate resources for stuffing, de-stuffing
PC7. conduct morning meeting with staff and workers to communicate the daily
plan and allocate the tasks
PC8. coordinate with the shipper or transporter to ensure if the cargo is available
for stuffing
PC9. oversee that container cargo handling operations are done with all
precautions and as per SOP to minimise errors and damages
Allocate resources for
container handling
To be competent, the user/ individual must be able to:
PC10. allocate resources and work orders for storage of stuffed/ de-stuffed
containers within the yard
PC11. coordinate with the equipment handlers regarding daily task for container
movement within the yard
PC12. coordinate with shipper and transporter for movement of stuffed/ de-stuffed
containers outside the Container Freight Station/ Inland Container Depots
(CFS/ ICD)
Review gate
movement of
containers and
reporting
To be competent, the user/ individual must be able to:
PC13. check gate logs and entries for movement of containers into and outside of
the CFS/ ICD
PC14. prepare documentation of daily container movement and cargo handling
activities
PC15. update the ERP regarding the container details, location and status
PC16. provide daily end of the day report to manager regarding status of activities
Knowledge and understanding (K)
A. Organizational
context (Knowledge
of the company /
organization and its
processes)
The individual on the job needs to know and understand:
KA1. organizational procedures
KA2. documentation and reporting as per organization’s mandate
KA3. security procedures to be followed
KA4. escalation matrix for reporting identified problems
KA5. risk and impact of not following defined procedures/work instructions
KA6. coding system followed to label cargo
KA7. IT system and ERP system of the organization
B. Technical
knowledge
The individual on the job needs to know and understand:
KB1. basics of operations in a port terminal, ICD and CFS
KB2. use of various cargo handling equipment
KB3. use of rope, flags and other manual equipment
KB4. vessel layout and loading and unloading activities
KB5. procedures of tank cleaning, cargo movement
KB6. requirements regarding handling of cargo
KB7. different type of vessels and cargo and container sizes
KB8. different type of cranes and MHEs – their capacities, constraints and usage
KB9. handling of hazardous and non-hazardous cargo – International Maritime
Dangerous Goods (IMDG) code
KB10. marking of material and people movement areas
KB11. stuffing and de-stuffing norms with respect to different cargo
KB12. special characteristics and handling requirements of shipments, if any
KB13. IMDG code
Skills (S)
C. Core skills/
generic skills
Reading skills
The user/individual on the job needs to know how to read:
SA1. written instructions
SA2. shiping manifest, Bill of Lading, shipping bills and related documents
SA3. ERP and computer generated reports
SA4. cargo stowage plans and vessel plans
SA5. SOPs and safety regulation manuals
Writing skills
The user/individual on the job needs to know how to write:
SA6. work-orders and instructions
SA7. checklist of activities, delays, undelivered items, contacts, etc
SA8. daily reports
Oral communication (listening and speaking skills)
The user/individual on the job needs to know how to:
SA9. communicate with customers, freight operators, transporters, shipping
companies, other supervisors and port authorities
SA10. communicate with cargo equipment operators and ground staff over VHF
radio
SA11. guide cargo handlers for smooth operations
D. Professional skills Decision making
The user/individual on the job needs to know how to:
SB1. decide on required workforce and equipment for performing a particular task
SB2. assess the environmental condition and type of cargo to assess if it is safe for
operations
SB3. resolve a problem quickly internally
SB4. prioritise shipments
SB5. decide on deployment of alternate resources when required
Plan and organize
The user/individual on the job needs to know how to:
SB6. plan and estimate the co-ordination required for resolving a querry.
SB7. maintain punctuality
SB8. respond to the client in a timely manner
SB9. prioritize and execute tasks based on client requirements
SB10. make work plans and resource allocation plans
SB11. make checks on execution of work plans
SB12. be a team player and achieve joint goals
Customer centricity
The user/individual on the job needs to know how to:
SB13. adhere to the customer timelines
SB14. address the urgency regarding shipments and activities
Problem solving
The user/individual on the job needs to know how to:
SB15. make adjustment to working requirements for difficult weathers and
hazardous goods
SB16. identify trends/common causes for delays, damages, etc.
SB17. co-ordinate and handle major issues with different departments
SB18. identify bottlenecks and operational problems and suggest remedial action
Analytical thinking
The user/individual on the job needs to know how to:
SB19. assess the resource requirement for a particular task at hand
SB20. assess and prepare for backup resources in case of delays
SB21. plan for cargo movement so that the resources and stroage space is optimally
utilised
Critical thinking
The user/individual on the job needs to know and understand how to:
SB22. resolve issues in a qucik and cost effective manner
SB23. develop work plans factoring in external factors
SB24. check that all security measures and safety protocals are followed at all times