Material Handling Equipment (MHE) Operator and Technician (1 years diploma )
Material Handling Equipment (MHE) Operator and Technician click here
Brief Job Description: The individual operates MHE to move, load and unload cargo
in a warehouse, undertakes basic maintenance activities for MHE and prepares
performance reports.
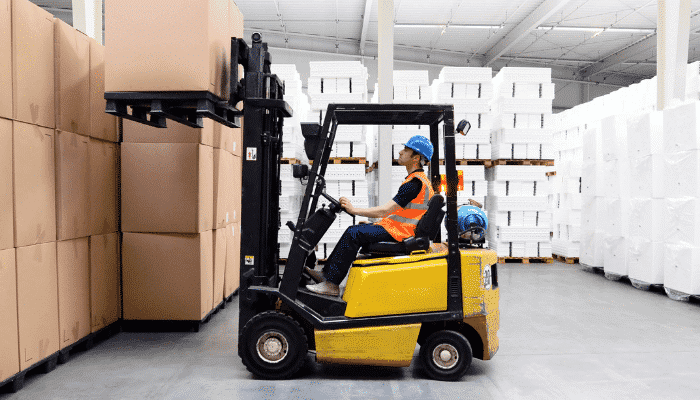
Qualifications Pack for MHE Operator and Technician
Elective 1: Battery Operated Pallet Truck
The unit is about operating Battery operated Pallet truck (BOPT) in a warehouse
or industrial environment to move cargo
Elective 2: Reach Truck
The unit is about operating Reach truck in a warehouse or industrial environment
to move cargo
Elective 3: Forklift
The unit is about operating Fork lift in a warehouse or industrial environment to
move cargo
Elective 3: Order Picker
The unit is about receiving pick list, inspect and operate order picker, perform
maintenance and reporting in a warehouse or industrial environment to move
cargo
Options
Option 1: Supervise Receiving & Dispatch
The unit is about supervising goods receiving and dispatch activities in a
warehouse
Personal Attributes: The job holder should be physically fit, judge distance and
should have good eye-hand-foot coordination to drive MHE continuously for
long hours. S/He must be able to prioritize and execute tasks within scheduled
time limits. S/he should have English and Vernacular language proficiency,
demonstrable in all written and oral communication
Job Role Material Handling Operator and Technician
Role Description
The individual operates MHE to move, load and unload cargo in
a warehouse, undertakes basic maintenance activities for MHE
and prepares performance reports.
NSQF level
Minimum Educational Qualifications
Maximum Educational Qualifications
4
Class X; candidate should have completed 18 years of age
Prerequisite License or Training Should have Light Motor Vehicle (LMV) license for four-wheeler
driving. Should be proficient and cleared Level 3
Minimum Job Entry Age 18 years
Experience Nil
Description
Core Skills/Generic
Skills
Core Skills or Generic Skills are a group of skills that are key to learning and working in
today’s world. These skills are typically needed in any work environment. In the
context of the NOS, these include communication related skills that are applicable to
most job roles
Function
Function is an activity necessary for achieving the key purpose of the sector,
occupation, or area of work, which can be carried out by a person or a group of
persons. Functions are identified through functional analysis and form the basis of
NOS.
Job role Job role defines a unique set of functions that together form a unique employment
opportunity in an organization.
Knowledge and Understanding

Knowledge and understanding are statements which together specify the technical,
generic, professional and organizational specific knowledge that an individual need in
order to perform to the required standard.
National Occupational
Standards (NOS) NOS are Occupational Standards which apply uniquely in the Indian context
Occupation Occupation is a set of job roles, which perform similar/related set of functions in an
industry.
Organizational Context
Organizational Context includes the way the organization is structured and how it
operates, including the extent of operative knowledge managers have of their
relevant areas of responsibility.
Performance Criteria Performance Criteria are statements that together specify the standard of
performance required when carrying out a task.
Qualifications Pack(QP)
Qualifications Pack comprises the set of NOS, together with the educational, training
and other criteria required to perform a job role. A Qualifications Pack is assigned a
unique qualification pack code.
Qualifications Pack
Code
Qualifications Pack Code is a unique reference code that identifies a qualifications
pack.
Electives
Electives are NOS/set of NOS that are identified by the sector as contributive
to specialization in a job role. There may be multiple electives within a QP for
each specialized job role. Trainees must select at least one elective for the
successful completion of a QP with Electives.
Options
Options are NOS/set of NOS that are identified by the sector as additional
skills. There may be multiple options within a QP. It is not mandatory to select
any of the options to complete a QP with Options.
Unit Code Unit code is a unique identifier for an Occupational Standard, which is
denoted by an ‘N
Unit Title Unit title gives a clear overall statement about what the incumbent should be
able to do
Description
Description gives a short summary of the unit content. This would be helpful
to anyone searching on a database to verify that this is the appropriate OS
they are looking for.

Scope
Scope is the set of statements specifying the range of variables that an individual may
have to deal with in carrying out the function which have a critical impact on the
quality of performance required.
Sector
Sector is a conglomeration of different business operations having similar businesses
and interests. It may also be defined as a distinct subset of the economy whose
components share similar characteristics and interests.
Sub-Sector Sub-sector is derived from a further breakdown based on the characteristics and
interests of its components.
Sub-functions Sub-functions are sub-activities essential to fulfil the achieving the objectives of the
function.
Technical Knowledge Technical Knowledge is the specific knowledge needed to accomplish specific
designated responsibilities.
Description
5S Sort, Set In order, Shine, Standardize and Sustain
BOPT Battery Operated Pallet Truck
ERP Enterprise resource planning
HR Human Resources
LMV Light Motor Vehicle
MIS Management information system
MHE Material Handling Equipment
NSQF National Skills Qualifications Framework
OH&S Occupational Health and Safety
OS Occupational Standards
OSHA Occupational Safety and Health Administration
PO Purchase Order
PPE Personal protective equipment
QP Qualification Pack
SOP Standard operating procedures
TAT Turnaround time
Perform material handling activities
Description This unit is about preparing and performing material handling activities
Scope This unit/task covers the following:
• Obtain work schedule and plan
• Inspect and operate the Material Handling Equipment (MHE)
• Report and document of MHE
Range: Personal Protective Equipment (PPEs), Forklift, Reach stacker, pallet truck,
pallet jacks, hand trucks, side loader, order picker, walkie, stacker, etc.
Performance Criteria(PC) w.r.t. the Scope
Element Performance Criteria
Obtain work
schedule and plan
To be competent, the user/individual on the job must be able to:
PC1. obtain the work schedule, daily targets and priorities (if any) from the
supervisor
PC2. obtain the list of goods to be put away or picked along with the quantities
and their respective locations
PC3. check with the supervisor the assistance required for other activities such as
daily stock counting, quality inspection etc.
PC4. plan the sequence in which the operation would be carried out so as to
optimize time and travel distance
Inspect and
operate the MHE
To be competent, the user/ individual must be able to:
PC5. inspect if the battery/fuel levels of the MHE is adequate for operation
before moving it from the dock
PC6. perform basic check of the vehicle condition as per the Preventive
Maintenance checklist before starting the work
PC7. collect the necessary PPE, inspect its fitness and wear throughout the work
schedule

PC8. identify goods to be moved and their location in terms of aisle number, rack
number and bin number from the putaway list during receiving and dispatch
PC9. assess the tooling requirement and collect the necessary tools from the tool
crib/storage racks
PC10. lift or move the pallet using the MHE and place correctly into specified
location
PC11. check for damages/spills, transport them to quarantine area and unload
them for further action
PC12. report supervisor if there are any issues such as count mismatch, breakage/
damage of goods/ packaging during
PC13. check that movement of goods should be carried out as per standard
operating procedures (SOP)
PC14. check for safe and error free loading and unloading of the goods
PC15. park the MHE in specified location after completing the job
PC16. check for minor issues, technical issues, cleaning etc. w.r.t. MHE and inform
supervisor accordingly
Report and
document of MHE
To be competent, the user/ individual must be able to:
PC17. report any delays, damages, accidents and other incidents to the supervisor
PC18. report on the condition of the MHE and any maintenance activity or
replacement that may be required to the supervisor
PC19. fill out forms such as damage to goods, insurance claims in accordance with
company procedures, if required
PC20. log any maintenance activity undertaken
Knowledge and Understanding (K)
A. Organizational
Context
(Knowledge of
the company /
organization
and its
processes)
The individual on the job needs to know:
KA1. types of documentation used in organization and importance of the same
KA2. risk and impact of not following defined procedures/work instructions
KA3. records to be maintained and implications of non-maintenance of the same
KA4. knowledge of security procedures e.g. secure storage of inventory
KA5. rules and regulations of shop floor as per SOP
KA6. risk and impact of not following safety procedures
KA7. escalation matrix for reporting identified problems
KA8. cost of equipment and loss for the company that results from damage of
equipment
KA9. implications of delays in process to the company
B. Technical Knowledge
The individual on the job needs to know:
KB1. controls and switches used to operate the MHE properly
KB2. basic technicalities associated with the MHE
KB3. road signs, factory signs and other safety and emergency signals
KB4. hazardous labels for the supplies being used
KB5. correct maintenance procedures for MHE
KB6. response to emergencies e.g. fire
KB7. safety regulations while operating the MHE
KB8. optimal working condition of MHE and their components.
KB9. optimal levels of fluids and lubricants and greasing
KB10. MHE components and their functions
KB11. how to handle MHE such as forklifts, pallet trucks, cages and lifts.
KB12. how to test and safely carry out maintenance tasks on the MHE.
KB13. how to identify deviations from normal operations, diagnose and repair MHE
Skills (S)
A. Core Skills/
Generic Skills
Reading Skills
The user/individual on the job needs to know how to read:
SA1. labels and codes as per company procedures
SA2. handling instructions/company log books and records
SA3. safety manuals and safety signs on the warehouse floor
Writing Skills
The user/individual on the job needs to know how to:
SA4. fill out checklists, maintenance logbooks detailing maintenance activities
conducted
SA5. prepare detailed technical reports
SA6. note down condition of MHE and any maintenance or repair that was carried
out on a daily basis.

SA7. fill out any complaint/ insurance related forms for damaged goods
Oral Communication (Listening and Speaking skills)
The user/individual on the job needs to know how to:
SA8. communicate clearly with supervisors and peers
SA9. regularly communicate with all employees in the chain of activities on the
shop floor to ensure activities are running smoothly
SA10. provide advice and guidance to peers and juniors
B. Professional
Skills
Decision Making
The user/individual on the job needs to know how to:
SB1. decide if a certain MHE is the best fit for the identified use
SB2. make judgment as to whether the MHE are in good condition or not.
Plan and Organize
The user/individual on the job needs to know how to:
SB3. adjust according to volume, capacity and manpower needs during peak and
non-peak hours
SB4. prioritize and execute tasks within the scheduled time limits
SB5. maintain schedules and punctuality
SB6. avoid absenteeism
SB7. be a team player and achieve joint goals.
Customer Centricity
The user/individual on the job needs to know how to:
SB8. adhere to the timelines and ensure that they are met
SB9. handle the shipments with proper care so as to avoid damage while
transportation
Problem Solving
The user/individual on the job needs to know how to:
SB10. suggest ways to handle difficult material handling situations that require
complex situations
SB11. resolve basic technical issues with the equipment through preventive and
basic maintenance
Analytical Thinking
The user/individual on the job needs to know how to:
SB12. suggest methods to streamline the maintenance process.
SB13. assess the condition of each MHE
Critical Thinking
The user/individual on the job needs to know how to:
SB14. concentrate at the task at hand and complete it without errors
Perform preventive & first-line maintenance checks
Description This unit is about performing preventive and breakdown maintenance checks of MHE
Scope This unit/task covers the following:
• Carry out preventive maintenance
• Carry out first-line repair and maintenance
• Report maintenance activities
Range: Personal protective equipment (PPEs), forklift, reach stacker, reach truck,
battery operated pallet truck, pallet jacks, hand trucks, order picker, tools and tackles,
maintenance kit etc.
Performance Criteria(PC) w.r.t. the Scope
Element Performance Criteria
Carry out preventive
maintenance
To be competent, the user/ individual must be able to:
PC1. collect the preventive maintenance checklist and maintenance log book for
the MHE concerned
PC2. collect necessary tools and PPE necessary for conducting the preventive
maintenance
PC3. understand the complaints noted in the log book, if any
PC4. observe the overall functioning of the MHE to identify problems if any
PC5. adjust in settings or operating parameters if required
PC6. check for damage in tyres, parking break, main horn, reverse horn, warning
lamp, etc.
PC7. check fluid l
evels of engine, transmission, differential, hydraulic, radiator
coolant and brake oil and top up any fluids as required
PC8. assess the MHE and escalate to supervisor if there is a likelihood of future
problems or replacement is required.
PC9. identify any parts that have worn out or nearing their end of life cycle as
specified by the manufacturer and put in request to obtain the required parts
from the store (if available) or inform inventory clerk to place orders.
PC10. make replacement of part and test for its safety and smooth operation
PC11. in case of a machine overhaul, plan well in advance and perform it during
holidays or non-peak hours.
PC12. test the MHE to ensure that it is fully functional and safe for use.
PC13. regularly maintain spare batteries and ensure they are fully charged
PC14. prepare and update maintenance card for every MHE
Carry out first-line
repair and
maintenance
To be competent, the user/ individual must be able to:
PC15. understand the type of breakdown reported/ witnessed during operation
PC16. identify and examine MHE to determine the source of the problem
PC17. determine if the problem could be resolved using existing skills or if it requires
the attention of a specialized technician from the manufacturing company
PC18. if the problem could be resolved, determine whether the part could be
repaired and carry out repairs using available spare parts/ machine shop
equipment, or else put in part replacement request
PC19. receive required parts and change the parts as per manufacturer’s guidelines.
PC20. complete and check all the line items in the first-line maintenance checklist
PC21. post first line repair, test the MHE to ensure that it is fully functional and safe
for use
Report maintenance
activities
To be competent, the user/ individual must be able to:
PC22. escalate to supervisor in case of delays or if a specialized technician from the
manufacturing company is required to solve the problem
PC23. report to supervisor for replacement of MHE parts
PC24. provide daily report to manager regarding condition of equipment, damage if
any, etc.

PC25. update MHE condition in the appropriate health card and the next review
dates in the maintenance schedules
PC26. prepare a detailed report explaining the cause for the problem, solution,
expected lifespan and suggested replacement dates
Knowledge and Understanding (K)
A. Organizational
Context
(Knowledge of the
company
organization and
its processes)
The user/individual on the job needs to know:
KA1. organizational procedures
KA2. occupational health and safety standards
KA3. procedures for dealing with loss or damage to goods
KA4. value of items handled and implications of damage/loss of the same
KA5. organisation structure of the company
KA6. risk and impact of not following defined work, safety and security procedures
KA7. chain of command for reporting problems and status of work
KA8. types of documentation used in organization
KA9. records to be maintained and implications of non-maintenance of the same
KA10. security procedures e.g. secure storage of inventory
KA11. rules and regulations of shop floor as per company’s standard operating
procedure (SOP)
KA12. risk and impact of not following safety procedures
KA13. escalation matrix for reporting identified problems
KA14. cost of equipment and loss for the company that results from damage of
equipment
B. Technical
Knowledge
The user/individual on the job needs to know:
KB1. controls and switches used to operate MHE
KB2. basic technicalities associated with the MHE
KB3. road signs, factory signs and other safety and emergency signals
KB4. hazardous labels for the supplies being used.
KB5. correct maintenance procedures for MHE
KB6. response to emergencies e.g. fire
KB7. safety regulations while operating the MHE
KB8. optimal levels of fluids and lubricants.
KB9. MHE Components and particular areas that require greasing.
KB10. all the MHE components and their functions
KB11. to test and safely carry out maintenance tasks on the MHE.
KB12. to identify deviations from normal operations, diagnose and repair MHE
Skills (S)
A. Core Skills/
Generic Skills
Reading Skills
The user/ individual on the job needs to know how to read:
SA1. labels to identify product and its associated hazard.
SA2. instructions from checklists /company log books and records
SA3. safety manuals and safety signs on the warehouse floor
Writing Skills
The user/ individual on the job needs to know how to:
SA4. fill out checklists, maintenance logbooks detailing maintenance activities
conducted
SA5. prepare detailed technical reports

Oral Communication (Listening and Speaking skills)
The user/ individual on the job needs to know how to:
SA6. communicate clearly with supervisors and peers
SA7. regularly communicate with all employees in the chain of activities on the shop
floor to ensure activities are running smoothly
SA8. provide advice and guidance to peers and juniors
B. Professional Skills Decision Making
The user/ individual on the job needs to know how to:
SB1. make a judgment as to whether the MHE are in good condition or not
SB2. make judgment if a certain task can be best performed by the selected MHE
SB3. decide if the MHE requires any additional servicing by company technicians
SB4. decide if there is a requirement for change of parts
SB5. decide if the MHE can be put back into use or not