Cold Chain Lead (1years diploma)
Cold Chain Lead click here
Brief Job Description: The individual at work is responsible for managing
temperature sensitive logistics planning, strategic human resource management,
supervise product handling and effective performance in cold storage plant.
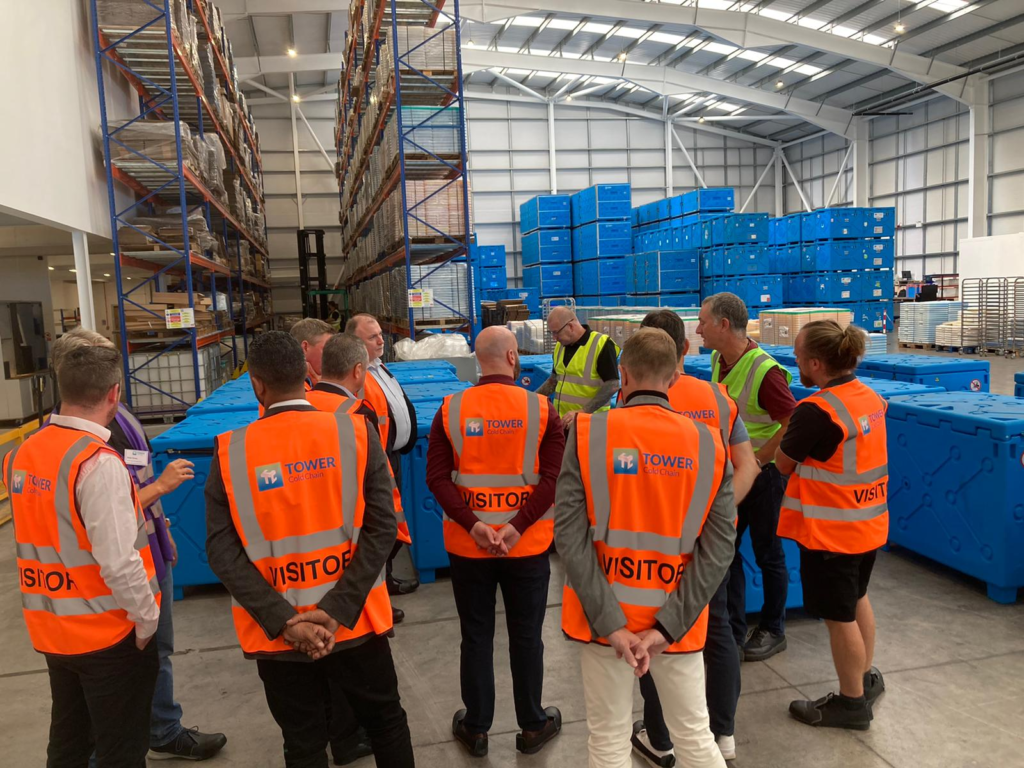
Personal Attributes: The job requires the individual to have: attention to details,
flexibility to move from one location to another, ability to work in low
temperature conditions, good eye sight, arm-hand steadiness and ability to
withstand changing temperature conditions from one facility to another.
Description
Core Skills/Generic
Skills
Core Skills or Generic Skills are a group of skills that are key to learning and
working in today’s world. These skills are typically needed in any work
environment. In the context of the NOS, these include communication related
skills that are applicable to most job roles.
Function
Function is an activity necessary for achieving the key purpose of the sector,
occupation, or area of work, which can be carried out by a person or a group
of persons. Functions are identified through functional analysis and form the
basis of NOS.
Job role Job role defines a unique set of functions that together form a unique
employment opportunity in an organization.
Knowledge and
Understanding
Knowledge and Understanding are statements which together specify the
technical, generic, professional and organizational specific knowledge that an
individual needs in order to perform to the required standard.
National Occupational
Standards (NOS) NOS are Occupational Standards which apply uniquely in the Indian context
Occupation Occupation is a set of job roles, which perform similar/related set of functions
in an industry.
Organisational Context
Organisational Context includes the way the organization is structured and
how it operates, including the extent of operative knowledge managers have
of their relevant areas of responsibility.
Performance Criteria Performance Criteria are statements that together specify the standard of
performance required when carrying out a task.
Qualifications
Pack(QP)
Qualifications Pack comprises the set of NOS, together with the educational,
training and other criteria required to perform a job role. A Qualifications
Pack is assigned a unique qualification pack code.
Qualifications Pack
Code
Qualifications Pack Code is a unique reference code that identifies a
qualifications pack.
Scope
Scope is the set of statements specifying the range of variables that an
individual may have to deal with in carrying out the function which have a
critical impact on the quality of performance required.
Sector
Sector is a conglomeration of different business operations having similar
businesses and interests. It may also be defined as a distinct subset of the
economy whose components share similar characteristics and interests.
Sub-Sector Sub-sector is derived from a further breakdown based on the characteristics
and interests of its components.
Sub-functions Sub-functions are sub-activities essential to fulfil the achieving the objectives
of the function.
Technical Knowledge Technical Knowledge is the specific knowledge needed to accomplish specific
designated responsibilities.
Keywords /Terms Description
NSQF National Skills Qualifications Framework
QP Qualifications Pack
OS Occupational Standards
OH&S Occupational Health and Safety
PPE Personal Protective Equipment
HR Human Resources
Administer manpower planning and labor management across cold chain operations
Description This OS unit is about labor requirement planning, review of worker training in the cold
chain facility and assisting head HR with operational level worker details in taking
appropriate recruitment, attrition and labor welfare decisions.
Scope This unit/task covers the following:
• Identify and review training requirements for cold chain operations
• Assist head HR in recruitment and attrition decisions
• Make decisions on health and fitness of employees for carrying out cold chain
operations
Range: Manual platform trolleys, self-propelled platform trolleys, manual or selfpropelled pallet trucks, belt, chain or roller conveyors, either gravity or self-propelled
Performance Criteria(PC) w.r.t. the Scope
Element Performance Criteria
Identifying and
reviewing training
requirements for
cold chain
operations
To be competent, the user/ individual must be able to:
PC1. identify HACCP (Hazard Analysis and Critical Control Points), HAZMAT
(Hazardous Material) and other training certifications required to be taken by
workers
PC2. ensure timely revision of training requirements based on technological
developments and new equipments introduced in the facility
PC3. attend conferences and seminars conducted by national cold chain
associations for updates in cold chain segment
PC4. update maintenance and quality assurance department about technological
developments incorporated in company’s cold chain; operations
PC5. ensure updated training requirements are appropriately communicated to
workers
Assisting head HR in
recruitment and
attrition decisions
To be competent, the user/ individual must be able to:
PC6. keep track of workers employed across departments
PC7. identify location from where workers should be hired, based on urgency of
requirement
PC8. identify skill sets required in workers for product specific operations, for eg:
ability to handle stress during urgent delivery requirement etc.
PC9. provide prior information on expected labor force requirement to head hr
PC10. supervise transfer of employees from one department to the other based on
requirement
PC11. initiate discussion with workers to analyze the cause of worker attrition
PC12. assist head hr in designing corrective mechanism to reduce attrition
Administer manpower planning and labor management across cold chain operations
Making decisions on
health and fitness of
employees for
carrying out cold
chain operations
To be competent, the user/ individual must be able to:
PC13. take charge of illness or injury incurred to workers during cold chain
operations and update the same to head hr
PC14. ensure timely fitness reports are prepared for every employee
PC15. take non conformance decision in case employee fitness levels do not match
the requirements
PC16. analyze the cause of illness or injury of employees
PC17. update the instructions on fitness requirements and safety measures in the
cold storage facility
Knowledge and Understanding (K)
A. Organizational
Context
(Knowledge of the
company /
organization and
its processes)
The individual on the job needs to know and understand:
KA1. company’s reporting structure
KA2. individual’s role in cold chain process flow
KA3. occupational health and safety standards
KA4. existing quality control standards followed by various industry players
KA5. quality control standards that are applicable to the company and the
products on which they are applicable
KA6. company’s policies, standard operating procedures and governance structure
KA7. action taken in case of breach of defined procedures/work instructions
KA8. company’s personnel management and incentive rules
KA9. clients and suppliers of the company
B. Technical
Knowledge
The individual on the job needs to know and understand:
KB1. HACCP (Hazard analysis and critical control points), HAZMAT (Hazardous
material) and other training certifications required to be taken by workers
KB2. appropriate PPE (Personal Protective Equipment) including gloves, jacket,
shoes, goggles to be worn by operators
KB3. types of goods in which the company deals
KB4. characteristics of the products being handled. for eg: odor, texture, size,
weight, stickiness, effect of exposure to water etc.
KB5. existing labor laws and labor welfare schemes
KB6. product specific quality control and assurance standards
KB7. operational understanding of the safety precautions to be taken for product
handling
KB8. geographical distribution of labor force possessing the required skill sets . for
e.g.: workers may be hired from Chittoor belt which has many cold storage
facilities. thus, the local labor force will already possess the required skill sets
and need not be trained after recruitment
KB9. appropriate Material Handling Equipment (MHE) to be used according to the
size and quantity of goods
KB10. types of workplace hazards that one can encounter in product handling
KB11. steps and remedial measures to be taken in case of injury or hazard caused
due to improper product handling
KB12. recruitment procedure for labor force used by the company
Skills (S)
A. Core Skills/ Reading Skills
Generic Skills The user/individual on the job needs to know and understand how to:
SA1. read instructions on workplace hazards and handling requirements for goods
SA2. read recruitment procedure and labor policies
Writing Skills
The user/individual on the job needs to know and understand how to:
SA3. maintain records of workers who got injured, were replaced or substituted in
place of another worker etc.
SA4. update safety instructions based on technological changes
Oral Communication (Listening and Speaking skills)
The user/individual on the job needs to know and understand how to:
SA5. initiate discussion with workers to understand their grievance
SA6. communicate decisions to workers relating to non-conformance of safety
standards or corrective actions to be taken in case of injury
SA7. communicate types of workplace hazards, safety precautions and remedial
measures to be taken
SA8. communicate with HR regarding worker performance, recruitment procedure,
reason for attrition etc.
B. Professional Skills Decision Making
The user/individual on the job needs to know and understand how to:
SB1. take non conformance decision on health and safety
SB2. identify whether worker training requirement should be updated
Plan and Organize
The user/individual on the job needs to know and understand how:
SB3. prioritize and execute tasks such as transferring labor from one department to
the other, providing prior information about labor force requirement to head
hr etc. in an efficient manner
SB4. plan and organize distribution of workers along different stages of cold chain
Customer Centricity
The user/individual on the job needs to know and understand how to:
SB5. identify customer requirements with respect to quality expectations
SB6. identify goods that are in high demand in market and those for which demand
is expected to increase in future
Problem Solving
The user/individual on the job needs to know and understand how to:
SB7. execute remedial measures in case of injury or hazard in handling technique
SB8. make decision for short term recruitment in case of urgent requirement
Analytical Thinking
The user/individual on the job needs to know and understand how to:
SB9. understand labor requirement based on schedule of activities across the cold
chain
SB10. analyze technological developments taking place in industry and identify if
training and safety instructions need to be updated
Critical Thinking
The user/individual on the job needs to know and understand how to:
SB11. identify appropriate location from where workers should be chosen
SB12. execute appropriate remedial measures in case of injury or hazard in handling
technique
Oversee Ensure smooth and effective execution of cold chain operation
Description This OS unit is about taking corrective and preventive action across the cold chain
from the time goods enter the cold storage facility till they reach consumption centres
and ensure smooth and timely flow of cold chain operations
Scope This unit/task covers the following:
• Take preventive and corrective action and non conformance decision in case of
interruption in cold storage facility
• Assist in budget development and exercise budgetary control over warehouse
operations
• Liaison with maintenance head in case of interruptions in cold storage operations
Range: Manual platform trolleys, self-propelled platform trolleys, manual or selfpropelled pallet trucks, belt, chain or roller conveyors, either gravity or self-propelled
Performance Criteria(PC) w.r.t. the Scope
Element Performance Criteria
Taking preventive
and corrective
action and non
conformance
decision in case of
interruption in cold
storage facility
To be competent, the user/ individual must be able to:
PC1. initiate action to prevent occurrence of any microbiological non-conformities
at any stage of cold chain operations
PC2. analyze and find root cause in case of delays at different stages of the cold
chain operations. for e.g.: a delay in grading of goods may be due to excessive
drying of goods in the previous stage of grading line operations or due to
extra time taken in unloading because of improper space management
PC3. stop operations whenever there is likelihood of occurrence that could affect
product safety and personnel safety or any other emergence
PC4. ensure effective implementation of cleaning schedule for all equipments and
machines is followed
Assisting in budget
development and
exercising budgetary
control over
warehouse
operations
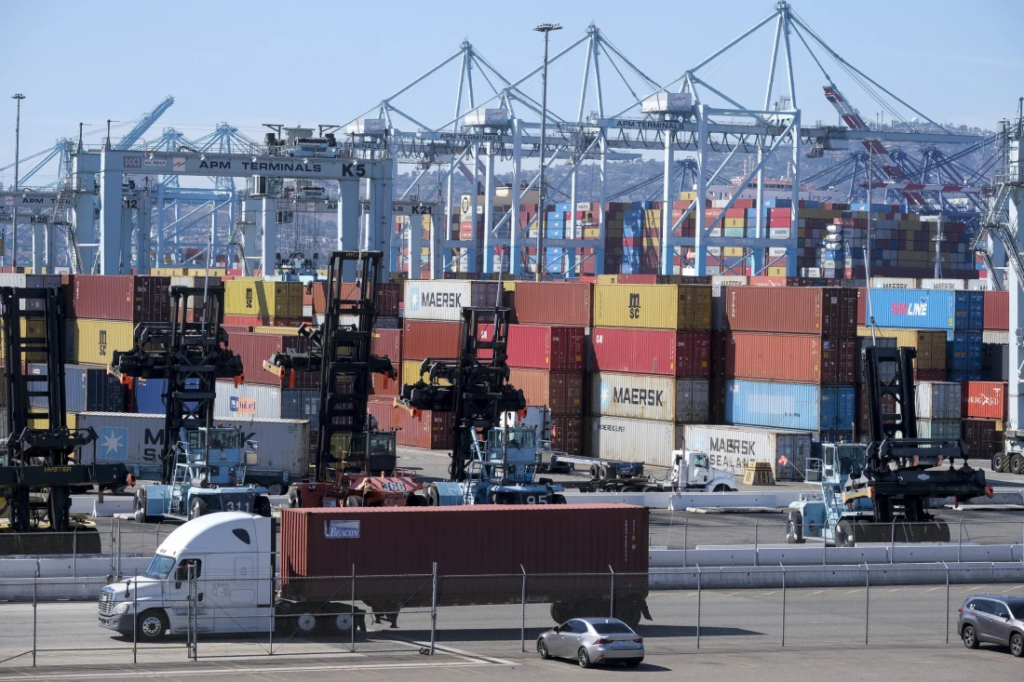
To be competent, the user/ individual must be able to:
PC5. understand requirements of cold storage equipments from perishable
product handling specialist
PC6. identify expenditure required on refrigeration equipments and associated
tools
PC7. estimate maintenance and upgradation expenditure expected to be incurred
on machines and equipments
PC8. identify worker expenses incurred for day-to-day activities such as food,
travel etc.
PC9. ensure correct details of number of workers is provided to budget control
team
PC10. estimate maximum expenditure that might be required to be incurred in
situations of crisis, for e.g.: accident, leakage, injury etc.
Liaising with
maintenance head in
To be competent, the user/ individual must be able to:
PC11. ensure timely compliance of calibration schedule for equipment’s is followed
Ensure smooth and effective execution of cold chain operation
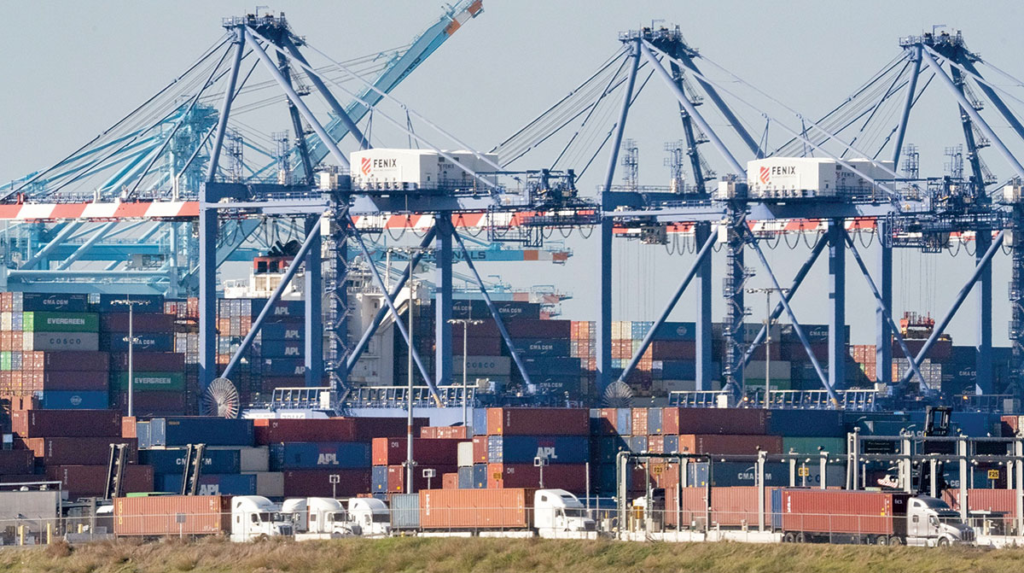
case of interruptions
in cold storage
operations
PC12. update maintenance head and follow up in case equipments and instruments
are not functioning properly
PC13. follow up with maintenance head in case of uninterrupted supply of
electricity and water
PC14. ensure equipments are replaced in appropriate time period based on their
working efficiency and inputs from workers, for eg: timely replacement of
refrigeration valves
PC15. supervise upgradation of evaporators, compressors etc.
A. Organizational
Context
(Knowledge of the
company /
organization and
its processes)
The individual on the job needs to know and understand:
KA1. company’s reporting structure
KA2. individual’s role in cold chain process flow
KA3. occupational health and safety standards
KA4. existing quality control standards followed by various industry players
KA5. quality control standards that are applicable to the company and the
products on which they are applicable
KA6. company’s policies, standard operating procedures and governance structure
KA7. action taken in case of breach of defined procedures/work instructions
KA8. company’s personnel management and incentives rules
KA9. clients and suppliers of the company
B. Technical
Knowledge
The individual on the job needs to know and understand:
KB1. ideal time required for each cold chain activity
KB2. process flow of cold chain operation
KB3. types of goods in which the company deals
KB4. characteristics of the products being handled, for eg: texture, odour,
stickiness etc.
KB5. cleaning schedule of refrigeration equipments
KB6. measurement units and scales used in cold storage equipments
KB7. calibration schedule and correct measurements according to which
calibration is done
KB8. maximum permissible cost norms for equipments, if any
KB9. product market of cold chain equipments (demand, supply, price etc.) and
costing of machines and support tools
KB10. appropriate Material Handling Equipment (MHE) to be used according to the
size and quantity of goods for efficient loading
KB11. types of workplace hazards that one can encounter in product handling
KB12. steps and remedial measures to be taken in case of injury or hazard caused
due to improper product handling and corresponding expenditure expected
to be incurred
Skills (S)
A. Core Skills/
Generic Skills
Reading Skills
The user/individual on the job needs to know and understand how to:
SA1. read budget statements
SA2. read scales and units of cold storage equipments like compressors, evaporators
etc.
Writing Skills
The user/individual on the job needs to know and understand how to:
Ensure smooth and effective execution of cold chain operation
SA3. maintain records of expenditure incurred
SA4. write details of equipments and tools requirement as communicated by
product handling specialist
SA5. maintain records of time periods in which equipments are replaced and
calibrated
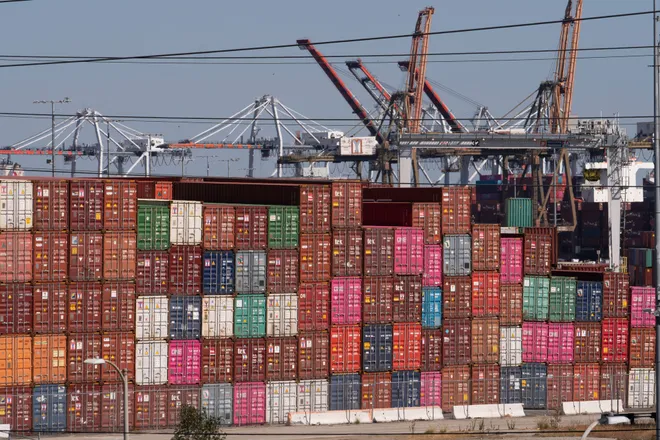
Oral Communication (Listening and Speaking skills)
The user/individual on the job needs to know and understand how to:
SA6. understand requirements of cold storage equipments from perishable product
handling specialist
SA7. coordinate with other supervisors and peers in english or accepted workplace
language
B. Professional Skills Decision Making
The user/individual on the job needs to know and understand how to:
SB1. estimate budget to be allocated for day-to-day worker expenses
SB2. identify correct number of workers required across every activity of cold
storage
Plan and Organize
The user/individual on the job needs to know and understand how to:
SB3. prioritize and execute tasks in an efficient manner
SB4. coordinate time with maintenance head for exchange of details
Customer Centricity
The user/individual on the job needs to know and understand how to:
SB5. identify customer requirements with respect to quality expectations
SB6. identify goods that are in high demand in market and those for which demand
is expected to increase in future
Problem Solving
The user/individual on the job needs to know and understand how to:
SB7. execute remedial measures in case of injury or hazard in handling technique
SB8. take appropriate action in case of microbiological non conformities at any stage
of cold chain
Analytical Thinking
The user/individual on the job needs to know and understand how to:
SB9. analyze and find root cause of delay and disruption of activities
Critical Thinking
The user/individual on the job needs to know and understand how to:
SB10. estimate maintenance and upgradation expenditure on equipments
SB11. identify if there is likelihood of occurrence that could affect product safety and
personnel safety or any other emergence
Monitor and improvise perishable product handling activities
Description This OS unit is about keeping the product handling activities of cold chain in line with
legal, technological changes and environmental laws in industry, supervising energy
consumption and quality control and acting as a link between cold storage and pack
house facilities located across multiple locations.
Scope This unit/task covers the following:
• Update internal systems and machines based on changes taking place in legal,
technological and environmental norms
• Administer product handling in cold storage operations
• Manage back end integrated pack houses and establish link with cold storage
facility at multiple locations
• Supervise cold chain quality control
Range: Manual platform trolleys, self-propelled platform trolleys, manual or self propelled pallet trucks, belt, chain or roller conveyors, either gravity or self-propelled
Performance Criteria(PC) w.r.t. the Scope
Element Performance Criteria
Updating internal
systems and
machines based on
changes taking place
in legal, technological
and environmental
norms
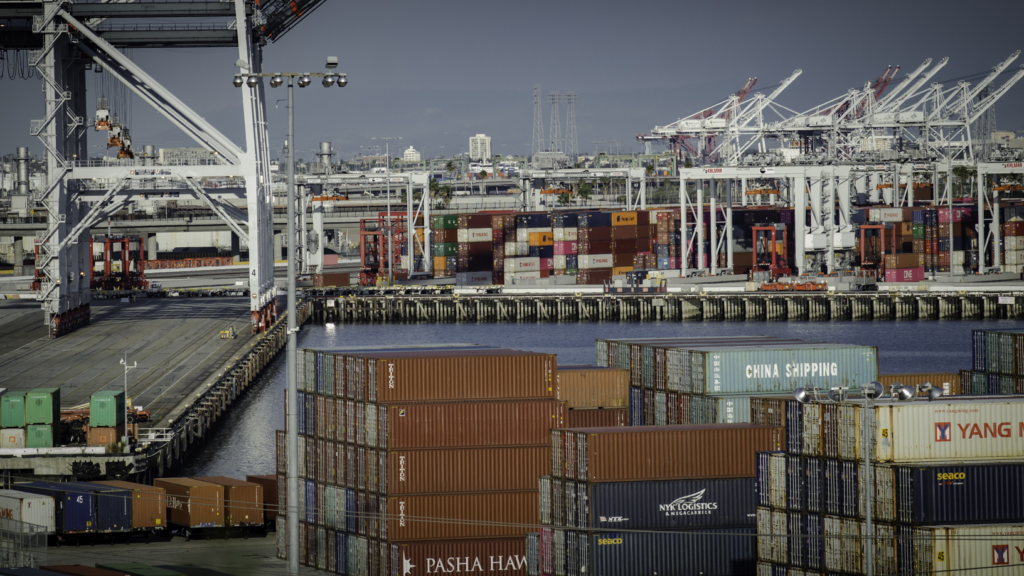
To be competent, the user/ individual must be able to:
PC1. utilize alternate technologies and energy sources in the cold chain with the aim
to have a positive impact on the environment, for eg: solar powered
refrigeration equipment’s
PC2. ensure standardization of handling units of perishable products across all stages
of cold chain
PC3. explore multi modal transport options that can be used in the perishables
logistics chain, especially as speed and good handling is critical to maintaining
quality control
PC4. supervise modernization or up gradation of refrigeration systems in existing
cold storages so as to result in substantial and measurable reduction in carbon
footprint of the facility and reduction in recurring cost of the power consumed
PC5. attend seminars and conferences organized by cold chain associations to get
information about latest updates in the sector
Administering
product handling in
cold storage
operations
To be competent, the user/ individual must be able to:
PC6. identify the appropriate product flow capacity – volume of commodities that
must be handled per unit of time
PC7. determine the appropriate cooling method and system based on volume of
commodity handled per unit of time
PC8. conduct regular check up of the ripening chamber and ensure proper
documentation is done at every stage
PC9. supervise pre-cooling temperature and storage conditions
PC10. identify scope for resource integration or cross-functional utilization of
equipments across the cold chain
PC11. participate in decision making for no. of fans, water pump capacity,
refrigeration of condensing unit etc.
Managing back end
integrated pack
houses and
establishing link with
cold storage facility
at multiple locations
To be competent, the user/ individual must be able to:
PC12. supervise grading, sorting, washing and drying activities on the goods received
in pack house
PC13. identify multiple market routing or value realization options of the graded
units, for eg: sending fresh produce directly to market for refrigeration,
sending to pre-cooling units located at cold storage facility etc.
PC14. supervise packaging for safe transport if the routing requires long travel to
reach the pre-cooling unit or refrigerated consumption centers
PC15. identify rural areas to be supported in the form of back end village level pack
houses
PC16. ensure goods are properly transported from back end pack house to the
appropriate cold chain facility
PC17. ensure uniform practices are followed at all cold storage facilities
Supervising cold
chain quality control
To be competent, the user/ individual must be able to:
PC18. maintain high levels of hygiene at all stages of the product’s life
PC19. together with the haccp (hazard analysis critical control point) team (including
microbiologists and process engineers) construct a flow diagram for all
product/process operations – list all hazards associated with each process step
and the measures to eliminate or reduce hazards
PC20. determine the step at which ccp (critical control point) can be applied in order
to eliminate the hazard
PC21. establish the target levels/tolerances for controlling the ccps
PC22. establish/implement monitoring systems for controlling ccps
PC23. identify corrective actions when a deviation occurs at a ccps
PC24. establish a documentation system for procedures and records
Knowledge and Understanding (K)
A. Organizational
Context
(Knowledge of the
company /
organization and
its processes)
The user/individual on the job needs to know and understand:
KA1. company’s reporting structure
KA2. individual’s role in cold chain process flow
KA3. occupational health and safety standards
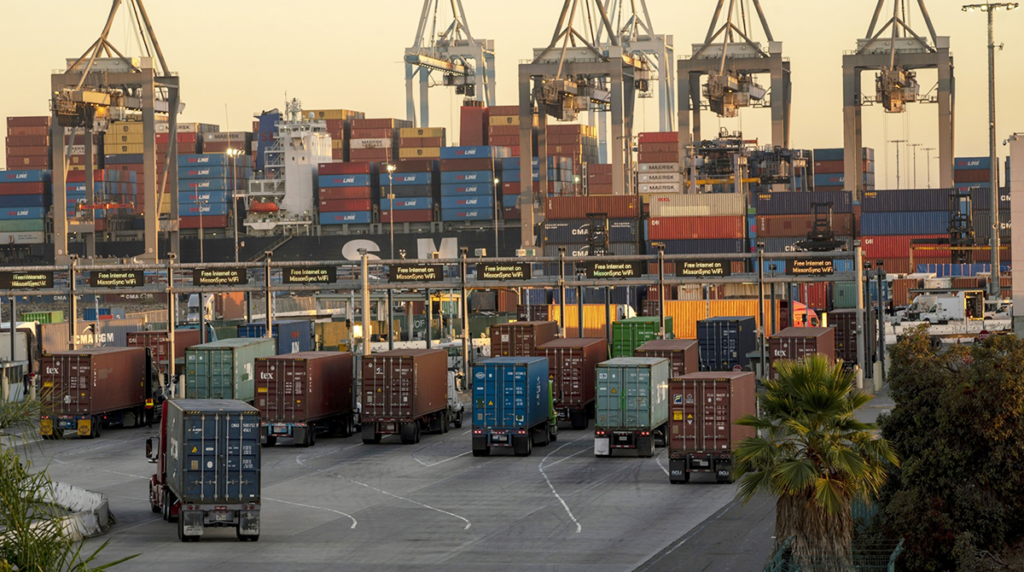
KA4. existing quality control standards followed by various industry players
KA5. quality control standards that are applicable to the company and the
products on which they are applicable
KA6. company’s policies, standard operating procedures and governance
structure
KA7. action taken in case of breach of defined procedures/work instructions
KA8. company’s personnel management and incentives rules
KA9. clients and suppliers of the company
B. Technical
Knowledge
The user/individual on the job needs to know and understand:
KB1. type and characteristics of the products being handled – odour, texture, size,
weight, stickiness etc.
KB2. appropriate material handling equipment (MHE) to be used according to the
size and quantity of goods for efficient loading
KB3. changes in spoiled goods with respect to colour, dehydration and protein
content
KB4. appropriate grading criteria for goods
KB5. extent of chlorination required for washing of fruits
KB6. technique for measurement of hydration levels
KB7. identification of goods based on grading categories
KB8. appropriate oxygen and carbon dioxide levels to be maintained in the
grading line facility
KB9. appropriate water temperature used for washing
KB10. waste water recycling, reuse and disposal procedure
KB11. appropriate time required for each stage of pack house activity
KB12. changes in spoiled goods with respect to colour, dehydration and protein
content
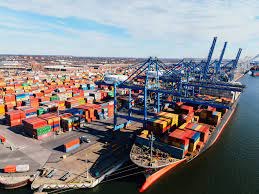
KB13. time for which washed goods should be dried, in order to avoid shrinking
and water loss
KB14. different types of trolleys used within the cold storage facility. for eg: trolleys
can be of following types two-wheeled trolleys – manual platform trolleys,
self-propelled platform trolleys, manual or self-propelled pallet trucks, belt,
chain or roller conveyors, either gravity or self-propelled.
KB15. equipments used for vehicle handling, namely platform elevators, cranes,
gantries, hand-stacking equipment, fork lift trucks, various types of
mechanised stacking equipment etc.
KB16. understand what handling requirements are appropriate for what types of
goods. for eg: some marine products are richer in aroma and thus should be
handled properly to ensure that aroma doesn’t spread to other products
through hands or other tools used while handling.
Skills (S)
A. Core Skills/
Generic Skills
Reading Skills
The user/ individual on the job needs to know and understand how to:
SA1. read product codes, quantity and specifications provided
SA2. read instructions for safety precautions and material handling
Writing Skills
The user/ individual on the job needs to know and understand how to:
SA3. maintain records of goods passing through each stage of grading line
SA4. mention details of rejected goods, along with reason for rejection
Oral Communication (Listening and Speaking skills)
The user/ individual on the job needs to know and understand how to:
SA5. communicate clear instructions to workers about handling techniques
SA6. give instructions about the identification of goods for different categories
B. Professional Skills Decision Making
The user/ individual on the job needs to know and understand how to:
SB1. decide criteria for grading of goods, for eg: market value, weight etc.
SB2. dispose waste water from washing of goods
Plan and Organize
The user/ individual on the job needs to know and understand how to:
SB3. schedule time for activities in each stage of grading line
SB4. re-schedule and re-allocate workers across activities in case of requirement
Customer Centricity
The user/ individual on the job needs to know and understand how to:
SB5. enforce hygienic conditions as per product handling requirements
SB6. segregate goods as per customer requirements
Problem Solving
The user/ individual on the job needs to know and understand how to:
SB7. handle delays in one stage of grading line operations so that it doesn’t affect
the other stage
SB8. handle the situation if units of one grade get mixed with units of other grade
Analytical Thinking
The user/ individual on the job needs to know and understand how to:
SB9. plan the appropriate number of workers to be deployed in grading line
operations
SB10. make changes in grading line temperature conditions based on climatic
changes
Critical Thinking
The user/ individual on the job needs to know and understand how to:
SB11. decided extent of chlorination required in water used for washing
SB12. treat the waste water after washing, whether water should be disposed or
recycled or reused
SB13. decide appropriate time for which goods should be dried to avoid excessive
water loss
Oversee Route Planning and reefer/non-reefer vehicle coordination
Description This unit is about overseeing refrigerated transportation and supervising route
planning and coordination
Scope This unit/task covers the following:
• Attend to client enquiries and orders
• Understand the client requirements
• Check the order requirements
• Assign duty to the reefer/non reefer vehicle operator
• Plan the routes Handle customer complaints and staff problems
• Monitor and follow up the travel
Range: Manual platform trolleys, self-propelled platform trolleys, manual or self propelled pallet trucks, belt, chain or roller conveyors, either gravity or self-propelled
Performance Criteria(PC) w.r.t. the Scope
Element Performance Criteria
Attending to client
enquiries and orders
To be competent, the user/ individual must be able to:
PC1. answer phone calls and emails of the clients regularly and promptly
PC2. follow proper behavioral etiquettes with the clients whether face to face or on
phone or e-mail
PC3. be updated on availability of the products with the order received
PC4. ensure the availability of vehicle and the vehicle operator for the delivery
PC5. be aware of the other delivery schedules for the day
PC6. review and revise transportation and delivery schedule based on priority
PC7. take confirmations from the client and schedule the delivery
PC8. update the order details and the time of booking to the MIS person for record
Understanding the
client requirements
To be competent, the user/ individual must be able to:
PC9. understand from the clients on the type of products, the delivery date,
quantity, delivery address, etc.
PC10. confirm the delivery details with the clients
PC11. update the clients on non availability of any products or reefer/non reefer
vehicle as per their order and requirement
PC12. send confirmation message or email to the clients along with the delivery
summary and invoice
PC13. maintain good rapport and relationships with the client
Checking the order
requirements
To be competent, the user/ individual must be able to:
PC14. ensure the order details and the products match
PC15. check the reefer vehicle maintenance and cleanliness on daily basis
PC16. ensure reefer vehicle is in proper working condition and meets the required
safety standards
PC17. check the temperature and pre cool of the reefer unit as set by the reefer
Oversee Route Planning and reefer/non-reefer vehicle coordination
vehicle operator
PC18. verify the reefer/non reefer vehicle papers are in order
PC19. ensure the safety precautions to be taken with respect to the product quality in
terms of temperature maintenance and other storage conditions based on the
type of product
Assigning duty to the
reefer/non reefer
vehicle operator
To be competent, the user/ individual must be able to:
PC20. assign the reefer/ non reefer vehicle operator to be sent for the delivery
PC21. brief the operator about the client and delivery details
PC22. coordinate the transportation routes and time schedule based on customer
requirement
PC23. advice the reefer/non reefer vehicle operators on their duty and responsibility
to be carried out during the trip
PC24. ensure the reefer/non reefer vehicle operators carry the necessary materials
such as maps, GPS, client details, etc.
PC25. monitor the various actions of the reefer/ non reefer vehicle operator such as
maintenance of the vehicle, defrosting the reefer unit etc.
PC26. ensure the reefer/non reefer vehicles leave for delivery at the designated time
Planning the routes To be competent, the user/ individual must be able to:
PC27. plan the driving routes to ensure on time delivery
PC28. provide the reefer/non reefer vehicle operator with GPS services for routes
PC29. supervise the maps and driving directions of the reefer/non reefer vehicle
operator to ensure efficient route service is provided
PC30. incorporate changes to the schedule if required
PC31. ensure safety and maintenance at the reefer vehicle
PC32. verify the trip sheets submitted by the reefer/non reefer vehicle operator for
mileage and fuel usage
Handling customer
complaints and staff
problems
To be competent, the user/ individual must be able to:
PC33. listen to the customer complaints and problems
PC34. ensure to take proper steps to rectify those problems with immediate action
PC35. monitor the issues of reefer/non reefer vehicle operator such as licensing,
safety, accidents, etc.
PC36. investigate on various staff problems and provide with proper solution
Monitoring and
following up the
travel
To be competent, the user/ individual must be able to:
PC37. ensure the quality of products on delivery
PC38. communicate with the reefer/non reefer vehicle operators during trip in case of
any emergency
PC39. monitor the safe delivery of products at the appropriate temperature, pressure,
humidity and other required parameters maintained
PC40. verify the documentations provided by the reefer/non reefer vehicle operator
PC41. coordinate with the client for payment details
PC42. report and document the details of the travel
PC43. monitor the control and discipline of the reefer/non reefer vehicle operator
with the work
PC44. track the vehicles before and during the journey
PC45. achieve client satisfaction ensuring high level service with timely and quality
Oversee Route Planning and reefer/non-reefer vehicle coordination
delivery as per requirement
Knowledge and Understanding (K)
A. Organizational
Context
(Knowledge of the
company /
organization and
its processes)
The user/individual on the job needs to know and understand:
KA1. company’s reporting structure
KA2. individual’s role in cold chain process flow
KA3. occupational health and safety standards
KA4. existing quality control standards followed by various industry players
KA5. quality control standards that are applicable to the company and the
products on which they are applicable
KA6. company’s policies, standard operating procedures and governance
structure
KA7. action taken in case of breach of defined procedures/work instructions
KA8. company’s personnel management and incentives rules
KA9. clients and suppliers of the company
B. Technical
Knowledge
The user/individual on the job needs to know and understand:
KA10. inspection checks to be conducted at the pre-dispatch stage
KA11. how to operate metal detector and other inspection equipments
KA12. product names and codes used for labelling
KA13. vehicle maintenance and repair procedures
KA14. precautions to be taken to avoid damages to the product while in transit
KA15. site details and traffic management plan
KA16. temperature requirements for the various products and at the reefer
transport, for example,
marine products: -18 to -21 degrees
fruits and vegetables: -1 to 15 degrees; 95% to 98% rh; 65% to 75% rh for
onion and garlic; 40% to 50% rh for beans, dry fruits and vegetables
dairy: -20 to +4 degrees
dry fruits: 4 to 10 degrees
pharma – chemicals and vaccines: – 4 to 10 degree
KA17. check and usage of brakes, stepni, lights, petrol, accelerator, steering
control, gear, etc.
KA18. spacing and air flow specifications for loading into the reefer unit for
respective products
KA19. appropriate packaging material to be used based on product characteristics,
for eg: the materials used for the package must be new, clean and of such a
quality as to avoid causing any external or internal damage to the produce
KA20. procedure for weighing, sealing and labelling
KA21. appropriate temperature for refrigerated transportation
KA22. characteristics of goods being handled, for eg: tolerance to exposure to
water, stickiness, dour etc.
KA23. appropriate medium for client communications
Skills (S)
A. Core Skills/ Reading Skills
Generic Skills The user/ individual on the job needs to know and understand how to:
SA1. read manufacturer specifications related to the vehicle
SA2. read standard operating procedures for service and maintenance
Writing Skills
The user/ individual on the job needs to know and understand how to:
SA3. write document details of maintenance and service activities
SA4. record details of faults and repair operations
SA5. write mail or message to be communicated to the client
SA6. maintain documentation of the product quality and conditions in transit
SA7. maintain documentation of trip details
Oral Communication (Listening and Speaking skills)
The user/ individual on the job needs to know and understand how to:
SA8. understand from the clients on the type of products, the delivery date,
quantity, delivery address, etc.
SA9. confirm the delivery details with the clients
SA10. coordinate with the concerned authority to report on any malfunctions or
repair
B. Professional Skills Decision Making
The user/ individual on the job needs to know and understand how to:
SB1. take decision on correct materials and tools to be used for vehicle
maintenance
SB2. evaluate the complaint raised by the customer and identify the right person
in the organization to address it
SB3. take a non conformance decision on the quality of goods before delivery
Plan and Organize
The user/ individual on the job needs to know and understand:
SB4. plan the vehicle maintenance and service at regular intervals
SB5. plan the driving routes to ensure on time delivery
SB6. supervise the maps and driving directions of the reefer/ non reefer vehicle
operator to ensure efficient route service is provided
Customer Centricity
The user/ individual on the job needs to know and understand:
SB7. customer demand and quality requirements
SB8. update the clients on non availability of any products or reefer/non reefer
vehicle as per their order and requirement
SB9. achieve client satisfaction ensuring high level service with timely and quality
delivery as per requirement
SB10. maintain quality and hygienic vehicle conditions to the extent expected by
customers
Problem Solving
The user/ individual on the job needs to know and understand how to:
SB11. solve customer complaints and reply promptly
SB12. resolve issues if vehicle routing and transit is delayed
SB13. resolve the faults and malfunctions of the vehicle
SB14. perform the emergency repairs such as changing tyres in case of puncture,
checking on light bulbs, etc
Analytical Thinking
The user/ individual on the job needs to know and understand how to:
SB15. analyze the route and incorporate changes to the schedule if needed
SB16. investigate on various staff problems and provide with proper solution
SB17. assess whether the vehicle meets the required condition after the
maintenance and service
Critical Thinking
The user/ individual on the job needs to know and understand how to:
SB18. analyze process disruptions and delays
SB19. monitor the temperature with appropriate device
Supervise Data entry/MIS reports management
Description This OS unit is about supervision and management of staff related problems and
overseeing data entry operations
Scope This unit/task covers the following:
• Supervise the work requirement
• Monitor MIS and data entry operations
• Attend staff related problems and issues
Range: Manual platform trolleys, self-propelled platform trolleys, manual or selfpropelled pallet trucks, belt, chain or roller conveyors, either gravity or self-propelled
Performance Criteria(PC) w.r.t. the Scope
Element Performance Criteria
Supervising the work
requirement
To be competent, the user/ individual must be able to:
PC1. coordinate with the different departments such as storage, transportation,
etc.
PC2. brief the data entry executive on the various documentations to be done
PC3. check the obtained information and documents to be updated
PC4. study the documents in detail and understand the requirements
Monitoring MIS and
data entry operations
To be competent, the user/ individual must be able to:
PC5. check the best software tool identified to update the data
PC6. identify the latest technology updates that would support the data entry
requirements
PC7. examine the required software to perform the MIS and data entry operation
PC8. monitor the working of the software and the procedure to update
PC9. coordinate with the respective departments in case if any additional inputs or
documents are required
PC10. review the entered information and compare with the original source
document
PC11. verify the output for errors and brief the data entry operators
PC12. ensure the update happens on a regular basis
PC13. ensure to maintain the documentation and quality standards to be used in
the data entry operation
PC14. conduct consistent check on the software and database stored
PC15. ensure to maintain the files updated in software as well as the source
documents securely
Attending staff
related problems and
issues
To be competent, the user/ individual must be able to:
PC16. listen to the complaints or problems of the staff
PC17. monitor the issues such as software problem, malfunctions, inadequate or
unclear information or any other technical problems
PC18. ensure access to relevant files, documents and information to the data entry
operator as required