Free Loading and Unloading Operator Course (4Months)
Loading and Unloading Operator:
Brief Job Description
Individuals at this job need to safely load and unload different vehicles, parts, assemblies, components etc. internally to various departments of a Manufacturing and R&D process and on to the vehicles for dispatch based on requirements.
Personal Attributes This job requires the individual to coordinate with stores, shop floor, dispatch and other departments for carrying out his day to day loading and unloading activities. The individual should also be able to demonstrate skills for information ordering, oral expression and comprehension. He should have sound health to withstand long hours of duty and the strenuous conditions associated with material handling tasks

Maintain a safe and healthy working environment:
Elements and Performance Criteria
Identify and report the risks identified
To be competent, the user/individual on the job must be able to:
PC1.. Identify activities which can cause potential injury through sharp objects, burns, fall, electricity, gas leakages, radiation, poisonous fumes, chemicals ,loud noise
PC2. Inform the concerned authorities about the potential risks identified in the processes, workplace area/ layout, materials used etc
PC3. Inform the concerned authorities about machine breakdowns, damages which can potentially harm man/ machine during operations
PC4. Create awareness amongst other by sharing information on the identified risks
Create and sustain a Safe, clean and environment friendly work place
To be competent, the user/individual on the job must be able to:
PC5.. Follow the instructions given on the equipment manual describing the operating process of the equipments
PC6.. Follow the Safety, Health and Environment related practices developed by the organization
PC7. Operate the machine using the recommended Personal Protective Equipments (PPE)
PC8. . Maintain a clean and safe working environment near the work place and ensure there is no spillage of chemicals, production waste, oil, solvents etc
PC9. Maintain high standards of personal hygiene at the work place
PC10. Ensure that the waste disposal is done in the designated area and manner as per organization SOP.
PC11. Inform appropriately the medical officer/ HR in case of self or an employees illness of contagious nature so that preventive actions can be planned for others
Knowledge and Understanding (KU)
The individual on the job needs to know and understand:
KU1. relevant standards, procedures and policies related to Health, Safety and Environment followed in the company
KU2. basic knowledge of Safety procedures( fire fighting, first aid) within the organization
KU3. knowledge of various types of PPEs and their usage
KU4. basic knowledge of risks/hazards associated with each occupation in the organization
KU5. how to safely operate various tools and machines and risksassociated with the tools/ equipment
KU6. knowledge of personal hygiene and how an individual an contribute towards creating a highly safe and clean working environment
Generic Skills (GS)

User/individual on the job needs to know how to:
GS1. write basic level notes and observations
GS2. read safety instructions put up across the plant premises
GS3. read safety precautions mentioned in equipment manuals and panels to understand the potential risks associated
GS4. effectively communicate information to team members
GS5. informemployees in the plant and concerned functions about events, incidents & potential risks observed related to Safety, Health and Environment.
GS6. question operator/ supervisor in order to understand the safety related issues
GS7. attentively listen with full attention and comprehend the information given by the speaker during safety drills and training programs
GS8. use common sense and make judgments during day to day basis
GS9. use reasoning skills to identify and resolve basic problems
GS10. use common sense and make judgments during day to day basis
GS11. use reasoning skills to identify and resolve basic problems
/GettyImages-150951481-1--578a50e13df78c09e9e2061b.jpg)
Identify and report the risks identified
PC1.. Identify activities which can cause potential injury through sharp objects, burns, fall, electricity, gas leakages, radiation, poisonous fumes, chemicals ,loud noise
PC2. Inform the concerned authorities about the potential risks identified in the processes, workplace area/ layout, materials used etc
PC3. Inform the concerned authorities about machine breakdowns, damages which can potentially harm man/ machine during operations
PC4. Create awareness amongst other by sharing information on the identified risks
Create and sustain a Safe, clean and environment friendly work place
PC5.. Follow the instructions given on the equipment manual describing the operating process of the equipments
PC6.. Follow the Safety, Health and Environment related practices developed by the organization
PC7. Operate the machine using the recommended Personal Protective Equipments (PPE)
PC8. . Maintain a clean and safe working environment near the work place and ensure there is no spillage of chemicals, production waste, oil, solvents etc
PC9. Maintain high standards of personal hygiene at the work place
PC10. Ensure that the waste disposal is done in the designated area and manner as per organization SOP.
PC11. Inform appropriately the medical officer/ HR in case of self or an employees illness of contagious nature so that preventive actions can be planned for others
Safely unload raw material to stores and load finished goods from stores:
Elements and Performance Criteria
General
To be competent, the user/individual on the job must be able to:
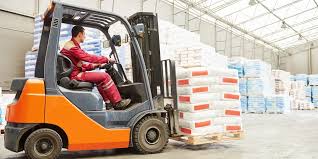
PC1.. understand from supervisor the exact task of loading /unloading and in case of heavy objects co-ordinate with a team member for carrying out the task jointly
PC2.. plan the days / weeks requirement of packing material viz. the boxes, trolleys, strapping etc. as per the bom/wi. report consumption and shortages as per the instructions of the supervisor.
PC3.. take care to load appropriate numbers / quantity to avoid over-loading .
PC4.. in case of large and different shaped objects take help of supervisor and load components, assemblies, vehicles in space efficient layouts.
PC5.. be sure to use appropriate protective equipment for personal safety.
PC6.. always move trolleys / forklifts in designated lanes, paths which do not criss cross any manufacturing process area , or people vehicle movement zones .
PC7.. to work as per the stores officer/ supervisors instructions for tasks such as application of protective treatment (plug, covers, anti-rust oil etc.) counting , physical stock taking, tagging etc.
Unloading
To be competent, the user/individual on the job must be able to:
PC8.. take the trolley/forklift truck and unload the received raw material/ parts safely from vendors vehicle
PC9.. move the material using the trolley /fork lift truck and take it to stores
PC10.. take charge of papers , documents to hand these over to stores for verification.
PC11.. the empty trolleys which are being used after return should be checked for damages and counted to tally with documents.
loading
To be competent, the user/individual on the job must be able to:
PC12.. based on the weight of the goods, load them manually or by material handling equipment like forklift /trolley in a safe manner. take care to follow the wi regarding delicate material, orientation etc.
PC13.. take the trolley /forklift truck to stores and place the finished goods kept in stores that are to be dispatched.
PC14.. move the trolley /fork lift truck along with the goods near to the transport vehicle
PC15.. for usage of component specific trolleys (items being shipped in without packing boxes) take care to check correspondence of id and parts, rain/ dust protective covers, no damage to the parts in the loading /unloading operation.
PC16.. take care that there is no damage to the parts/vehicles paint, finish etc while loading unloading.
PC17.. inform supervisor based on days load if specific material handling equipment like crane etc. needed for loading / unloading for big consignments .
PC18.. hand over the documents ( dispatch, insurance etc.)to the vehicle driver making sure that these are jointly tallied for correspondence, completeness with the shipment.
PC19.. take the trolley /forklift truck to stores and place the finished goods kept in stores that are to be dispatched. move the trolley /fork lift truck along with the goods near to the transport vehicle as is needed.
PC 20.. take care that appropriate rain/ dust protection is used with suitable tieing- up arrangement to last during the travel duration.
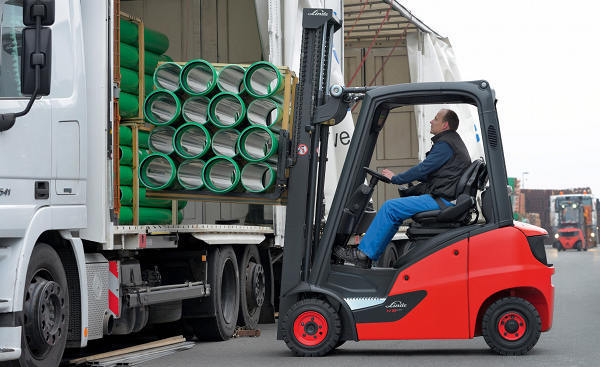
Knowledge and Understanding (KU)
The individual on the job needs to know and understand:
KU1. the location of stores and dispatch departments in company
KU2. material handling equipments used in the company
KU3. escalation procedure in case of emergency and crisis situations
KU4. product knowledge from the point of view of care to be taken during handling, storage and preservation.
Generic Skills (GS)
User/individual on the job needs to know how to:
GS1. communicate with the shop floor and dispatch/stores supervisor in case of any discrepancy arising in the process
General
PC1.. understand from supervisor the exact task of loading /unloading and in case of heavy objects co- ordinate with a team member for carrying out the task jointly
PC2.. plan the days / weeks requirement of packing material viz. the boxes, trolleys, strapping etc. as per the bom/wi. report consumption and shortages as per the instructions of the supervisor.
PC3.. take care to load appropriate numbers / quantity to avoid over-loading .
PC4.. in case of large and different shaped objects take help of supervisor and load components, assemblies, vehicles in space efficient layouts.
PC5.. be sure to use appropriate protective equipment for personal safety.
PC6.. always move trolleys / forklifts in designated lanes, paths which do not criss cross any manufacturing process area , or people vehicle movement zones .
PC7.. to work as per the stores officer/ supervisors instructions for tasks such as application of protective treatment (plug, covers, anti-rust oil etc.) counting , physical stock taking, tagging etc.

Unloading
PC8.. take the trolley/forklift truck and unload the received raw material/ parts safely from vendors vehicle
PC9.. move the material using the trolley /fork lift truck and take it to stores
PC10.. take charge of papers , documents to hand these over to stores for verification.
PC11.. the empty trolleys which are being used after return should be checked for damages and counted to tally with documents.
loading
PC12.. based on the weight of the goods, load them manually or by material handling equipment like forklift /trolley in a safe manner. take care to follow the wi regarding delicate material, orientation etc.
PC13.. take the trolley /forklift truck to stores and place the finished goods kept in stores that are to be dispatched.
PC14.. move the trolley /fork lift truck along with the goods near to the transport vehicle
PC15.. for usage of component specific trolleys (items being shipped in without packing boxes) take care to check correspondence of id and parts, rain/ dust protective covers, no damage to the parts in the loading /unloading operation.
PC16.. take care that there is no damage to the parts/vehicles paint, finish etc while loading unloading.
PC17.. inform supervisor based on days load if specific material handling equipment like crane etc. needed for loading / unloading for big consignments .
PC18.. hand over the documents ( dispatch, insurance etc.)to the vehicle driver making sure that these are jointly tallied for correspondence, completeness with the shipment.
PC19.. take the trolley /forklift truck to stores and place the finished goods kept in stores that are to be dispatched. move the trolley /fork lift truck along with the goods near to the transport vehicle as is needed.
PC 20.. take care that appropriate rain/ dust protection is used with suitable tieing- up arrangement to last during the travel duration.
Assessment Guidelines:
- Criteria for assessment for each Qualification Pack will be created by the Sector Skill Council. Each Element/ Performance Criteria (PC) will be assigned marks proportional to its importance in NOS. SSC will also lay down proportion of marks for Theory and Skills Practical for each Element/ PC.
- The assessment for the theory part will be based on knowledge bank of questions created by the SSC.
- Assessment will be conducted for all compulsory NOS, and where applicable, on the selected elective/option NOS/set of NOS.
- Individual assessment agencies will create unique question papers for theory part for each candidate at each examination/training center (as per assessment criteria below).
- Individual assessment agencies will create unique evaluations for skill practical for every student at each examination/ training center based on these criteria.
- To pass the Qualification Pack assessment, every trainee should score the Recommended Pass % aggregate for the QP.
- In case of unsuccessful completion, the trainee may seek reassessment on the Qualification Pack.