Chargehand – Precast Erection (6 month course)
Chargehand – Precast Erection click here
Brief Job Description: The job role is responsible for lifting heavy RCC Precast units using
cranes or suitable equipment and erects them in appropriate locations as per drawing.
Individuals in this job role also supervise grouting and caulking works as applicable to the
precast erection operations at construction sites.

Personal Attributes: The job holder is expected to be fit by physical and mental aspects
and should have good analytical and problem solving skills. Individual in this job role
should be able to guide a team of riggers through effective communication in order to
get the assigned task completed as per stipulated tolerance limit and applicable statutory
requirements. The job holder should preferably be free from vertigo problem,
cardiovascular diseases as the nature of work involves handling heavy loads and working
at heights.
Description
Sector Sector is conglomeration of different business operations having similar
business and interests. It may also be defined as a distinct subset of the
economy whose components share similar characteristics and interests.
Sub‐Sector Sub‐Sector is derived from a further breakdown based on the characteristics
and interests of its components
Occupation Occupation is a set of job roles, which perform similar/related set of
functions in an industry
Job role Job role defines a unique set of functions that together form a unique
employment opportunity in an organization.
Occupational Standards
(OS)
OS specify the standards of performance an individual must achieve when
carrying out a function in the workplace, together with the knowledge and
understanding they need to meet the standard consistently. Occupational
Standards are applicable both in the Indian contexts.
Performance Criteria Performance Criteria are statements that together specify the standard of
performance required when carrying out a task.
Qualifications Pack (QP) Qualifications Pack comprises the set of OS, together with the educational,
training and other criteria required to perform a job role. A Qualification Pack
is assigned a unique qualification pack code
Qualification Pack Code Qualification Pack Code is a unique reference code that identifies a
qualifications pack.

National Occupational
Standards (NOS) NOS are Occupational Standards which apply uniquely in the Indian context.
Scope Scope is the set of statements specifying the range of variables that an
individual may have to deal with in carrying out the function which have a
critical impact on the quality of performance required.
Knowledge and Understanding
Knowledge and Understanding are statements which together specify the
technical, generic, professional and organizational specific knowledge that an
individual needs in order to perform to the required standard
Organizational Context Organizational Context includes the way the organization is structured and
how it operates, including the extent of operative knowledge managers have
of their relevant areas of responsibility.
Technical Knowledge Technical Knowledge is the specific knowledge needed to accomplish specific
designated responsibilities.
Core Skills / Generic Skills Core Skills or Generic Skills are a group of skills that are key to learning and
working in today’s world. These skills are typically needed in any work
environment. In the context of the OS, these include communication related
skills that are applicable to most job roles.
Keywords /Terms Description
CON Construction
NSQF National Skill Qualifications Framework
QP Qualification Pack
OS Occupational Standards
TBD To Be Decided
Supervise lifting of heavy RCC Precast components at construction sites
Description This unit describes the skills and knowledge required to supervise lifting of heavy RCC
Precast components at construction sites.
Scope The scope covers the following:
Check and ensure that preparatory works are completed as per work
requirement prior to lifting
Supervise lifting operations and provide signals to lifting equipment operators
Carry out heavy lifting operations using multiple lifting equipment’s (Tandem
Lifting)
Performance Criteria (PC) w.r.t. the Scope
Element Performance Criteria
Check and ensure that preparatory works are completed as per work requirement prior to lifting
To be competent, the user/individual on the job must be able to:
PC1. check and ensure the lifting route is free from obstacles such as live overhead
electrical cables, service lines, close vicinity to existing structures or persons
PC2. ensure area of operation (lifting, unloading) is safely marked, barricaded and
safe access path is available to the lifting point
PC3. ensure that the lifting area is adequately illuminated and clear visibility can be
maintained from lifting point to erection location
PC4. ensure loads to be lifted are placed appropriately at the point of lifting
PC5. confirm that the lifting equipment’s under operation and its accessories are in
safe working condition
PC6. check and ensure safe working conditions of lifting gears like shackles, pulleys,
hooks, ropes, slings etc. prior to start lifting work
PC7. check for adequate tightness of slings, belts or ropes anchored to the load as
per applicable standard procedure, prior to lifting
Supervise lifting operations and provide signals to lifting equipment operators
PC8. monitor lifting operation considering size and shape of the loads being lifted
PC9. use appropriate lifting gear considering weight, shape and size of the load
PC10. closely monitor angle between slings under tension and tightness of locks at
attached points to ensure stability of the suspended load
PC11. ensure elements or assemblies do not get damaged during lifting operations
PC12.supervise controlling the movement of suspended loads using tag line or guy rope
PC13.maintain clear line of vision with the equipment operator
PC14.provide appropriate signals during various stages at lifting as per standard
hand signaling guidelines
PC15.seek assistance for signaling if load or operator is not visible from own location
PC16.report to superior promptly and clearly in case of unsafe conditions, safety violations
Carry out heavy lifting operations using multiple lifting equipment’s (Tandem Lifting)
PC17.brief subordinate workmen about lifting plan and safe working methods prior
to commencing heavy lifting operations
PC18. ensure safe distance of equipments and objects as per agreed work plan from
human and other near objects while carrying out lifting activity
PC19. assess position of cranes and loads in order to keep accordance with load
lifting plan, safety norms provided for conducting tandem lifting operations
PC20. confirm full functional tests have been carried out of all power, transmission,
control and safety systems of the equipments by competent personnel prior
to the commencement of the lift
PC21. confirm that the weather condition is favorable to heavy lifting activities
PC22.prioritize and sequence activities related to tandem lifting operations
PC23.monitor and control speed of lifting when multiple lifting equipments are
engaged simultaneously
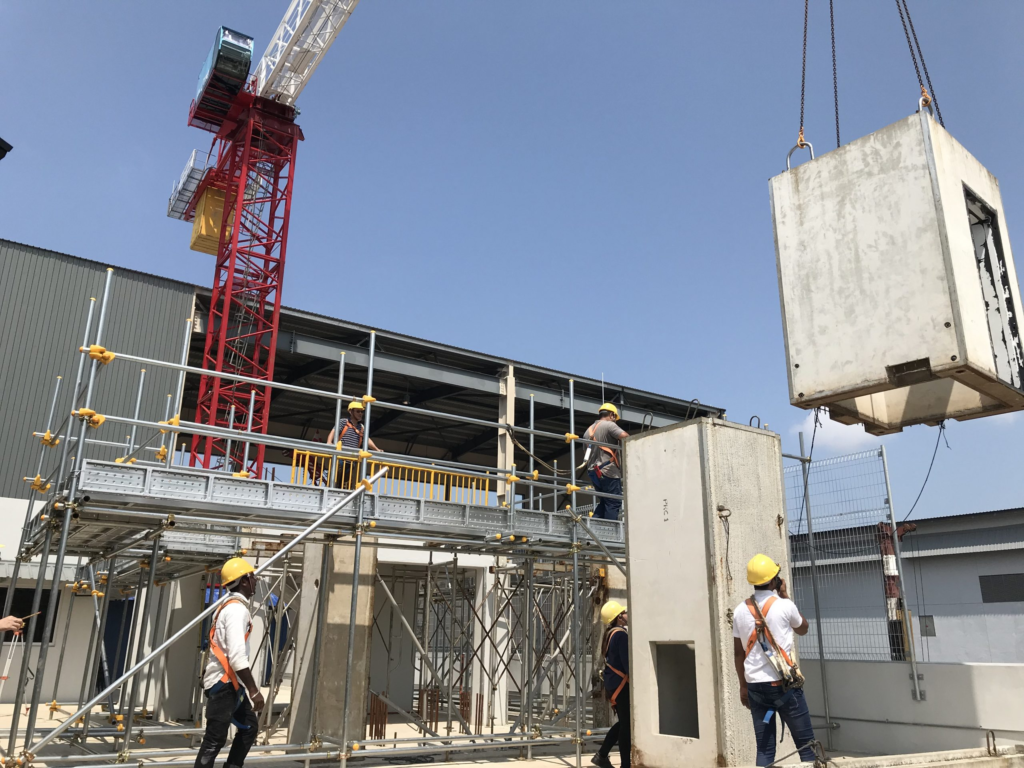
PC24. keep close coordination with equipment operators and maintain
synchronization throughout lifting activity
PC25.maintain stable position of objects under suspension (while being lifted) as per
standard practice by providing signals to the equipment operators
PC26. guide objects to the desired locations and ensure their safe lowering to the
specified positions
PC27. execute task as per considerations, assumptions, limit of tolerance specified in
applicable work methodology and safety control measures during heavy lifting
work, report concerned personnel if otherwise
Knowledge and Understanding (K)
A. Organizational Context (Knowledge of the company / organization and its processes)
The user/individual on the job needs to know and understand:
KA1. standard procedures for rigging work
KA2. safety rules and regulations for handling and storing relevant tools and
equipment and materials for rigging works
KA3. personal protection including the use of the related safety gears and
equipment
KA4. precautions and measures required in the lifting and movement of heavy
components and materials
KA5. service request procedures for tools, materials and equipments
KA6. statutory compliance requirements related to working at height
B. Technical Knowledge
The user/individual on the job needs to know and understand:
KB1. basic sketches / schematic working drawing relevant to rigging works
KB2. basic principles of measurement, geometry and arithmetic calculation
KB3. conversion of units of linear, areal and volumetric measurements
KB4. how to read and interpret drawings, sketches related to precast erection works
KB5. how to develop sketches and what details to be covered in the sketches
KB6. information of lifting plans and schedules
KB7. how to select lifting gears considering weight, size and shape of loads to be lifted
KB8. ideal weather and environment condition to carry out lifting
KB9. factors affecting lifting operations such as presence of electrical cable,
movement of vehicle or person, slope and compaction of base of lifting equipment’s
KB10.working mechanism and capacity (safe working load- SWL) of different kind of
cranes such as mobile, crawler, telescopic, tower or gantry cranes
KB11.operational details of different types of cranes including load lifting posture of
the equipment, angle of outrigger to be kept during lifting and maximum
reach of the equipment
KB12.working mechanism and SWL of winch machines
KB13.preventive actions to be taken to the cranes under adverse weather condition
like thunder-storm, heavy wind flow
KB14.use of different kind of common lifting gears like hooks, shackles, wire rope
slings, chain slings, belts, eye bolts, rings, links, swivels and spreader beams
KB15.load carrying capacity of each lifting gears and their specifications
KB16.different safety checks to be carried out to respective safety gears to
determine safe usability of them for lifting
KB17.standard hand signaling procedures to be provided during lifting operations
Skills (S)
A. Core Skills/
Generic Skills
Writing Skills
The user/ individual on the job needs to know and understand how to:
SA1. write in one or more language, preferably in the local language of the site and
basic English
SA2. provide clear and simple instructions, details & sketches to sub‐ordinate
Reading Skills
The user/ individual on the job needs to know and understand how to:
SA3. read one or more language, preferably in the local language of the site and
basic English
SA4. read sketches, drawing or instructions provided for the rigging work
SA5. read various, sign boards, safety rules and safety tags , instructions related to
exit routes during emergency at the workplace
Oral Communication (Listening and Speaking skills)
The user/ individual on the job needs to know and understand how to:
SA6. speak one or more language, preferably the local language of the site
SA7. orally and effectively communicate about sketches, drawing or instructions
provided for the rigging work
SA8. speak and convey about various, sign boards, safety rules and safety tags ,
instructions related to exit routes during emergency at the workplace
B. Professional Skills
Decision Making
The user/individual on the job needs to know and understand how to:
SB1. decide whether the work place is safe for working and also relevant task is not
creating hazardous condition for others
SB2. decide on manpower, tools , material and equipment for relevant work
SB3. decide whether the lifting route is free from obstacles
SB4. decide whether the weather condition is favorable to heavy lifting activities
Plan and Organize
The user/individual on the job needs to know and understand how to:
SB5. plan work & organize required resource in coordination with team members
and superior
SB6. prioritize and sequence activities related to tandem lifting operations
Customer centricity
The user/individual on the job needs to know and understand how to:
SB7. perform work as per agreed time schedule and quality
Problem solving
The user/individual on the job needs to know and understand how to:
SB8. resolve concerns raised by the rigging gang
SB9. resolve any conflict within the team
SB10.report to superior in case of unsafe conditions, safety violations
Analytical Thinking
The user/individual on the job needs to know and understand how to:
SB11. correlate the sequence of rigging works with respect to other
proceeding activity of other trade
SB12. optimize resources
SB13. minimize wastages
Critical Thinking
The user/individual on the job needs to know and understand how to:
SB14. evaluate the complexity of the task and seek assistance and support wherever
required
SB15. identify violation of any safety norms which may lead to accidents
Erect and align RCC Precast components at construction sites
Description This unit describes the skills and knowledge required to erect and align RCC Precast
components at construction sites.
Scope The scope covers the following:
Check and ensure that preparatory works are completed as per work
requirement prior to erection
Ensure completion of erection activities are as per specification and planning
Performance Criteria (PC) w.r.t. the Scope
Element Performance Criteria Check and ensure that preparatory works are completed as per work
requirement prior to erection
To be competent, the user/individual on the job must be able to:
PC1. check for proper access is available to the location of erection
PC2. check for survey marks and reference points and carry out necessary
measurement to ascertain exact location of erection
PC3. check for shims, bearing pads at appropriate locations
PC4. check for provisions for bolting, welding, post-tensioning connections are available as per drawing
PC5. ensure designed area of bearing in the platform or support is available for efficient erection of the components
PC6. check the area of erection for desired accessibility of load lifting equipment’s, otherwise report to concerned authority
Ensure completion of erection activities are as per specification and planning
PC7. check for hazardous situations at erection site, such as presence of live
electrical cables, absence of proper barricading, excessive wind speed and
report it to the concerned authority promptly as per requirement
PC8. check availability of all materials and support equipment (identified by the
seniors and required to proceed with the work) and report any shortages
PC9. install shoring, bracing and guying materials as directed by the foreman/
supervisor or specified by erection drawings and details considering local
conditions
PC10. install erection hardware to the units, using appropriate hand tools as per
instruction and specification of erection drawing
PC11.pull, push and hold suspended precast units approximately to the exact
location by hand or suitable means during lowering of load
PC12. communicate efficiently to the signalman or operator for precise movements
required to place the object at accurate location
PC13.supervise and monitor activities by subordinates in order to guide the units
to their location
PC14.place the object to its accurate location efficiently and make required adjustments as per erection requirement
PC15. ensure proper alignment of the erected precast units by carrying out
required measurement and checks using appropriate measuring tools and instruments
PC16. confirm orientation of the erected precast units as per instruction or
drawings
PC17. ensure installation of temporary connections using appropriate tools prior to
final positioning of precast units
PC18.tighten bolted connections to the specified tolerance and torque using
appropriate torque wrench wherever required
PC19. check bolt tightness in case of units having slotted connections
PC20. install special steel washers to ensure that the specified tension has been
developed in the bolt
PC21. check location of shims, bearing pads for their proper positioning
PC22. install expansion bolts using prescribed installation procedures and quality
control specifications
PC23. check temporary supports and connections to ensure stabilization of units in
its position until final connections are made
PC24.report to superior for completion or difficulties faced promptly and
efficiently
PC25.report to concerned authority promptly in case of any safety violation
PC26.supervise observation of applicable safety practices by subordinates at
workplace
Knowledge and Understanding (K)
A. Organizational
Context
(Knowledge of
the company /
organization and
its processes)
The user/individual on the job needs to know and understand:
KA1. standard procedures for rigging work
KA2. safety rules and regulations for handling and storing relevant tools and
equipment and materials for rigging works
KA3. personal protection including the use of the related safety gears and
equipment

KA4. precautions and measures required in the lifting and movement of heavy
components and materials
KA5. service request procedures for tools, materials and equipment’s
KA6. statutory compliance requirements related to working at height
B. Technical Knowledge
The user/individual on the job needs to know and understand:
KB1. basic sketches / schematic working drawing relevant to rigging works
KB2. basic principles of measurement, geometry and arithmetic calculation
KB3. conversion of units of linear, areal and volumetric measurements
KB4. information of lifting plans and schedules
KB5. applicable tolerance to respective erection job
KB6. sequence of erection works as per proposed work method statement
KB7. linear unit of measurement and their conversion
KB8. basic arithmetic and concept of geometry
KB9. checks to be carried out to ensure readiness of base of erections
KB10.how to check alignment of erected elements using measuring tools and
instruments
KB11.technique of positing of elements to their locations within tolerance limits
KB12.use of barricading, safety signage at the location of erection
KB13.how to fill up check lists, permits applicable to erection operations
KB14.hazards related to precast erection activities, height work
Skills (S)
A. Core Skills/
Generic Skills
Writing Skills
The user/ individual on the job needs to know and understand how to:
SA1. write in one or more language, preferably in the local language of the site
and basic English
SA2. provide clear and simple instructions, details & sketches to sub‐ordinate
Reading Skills
The user/ individual on the job needs to know and understand how to:
SA3. read one or more language, preferably in the local language of the site and
basic English
SA4. read sketches, drawing or instructions provided for the rigging work
SA5. read various, sign boards, safety rules and safety tags , instructions related to
exit routes during emergency at the workplace
Oral Communication (Listening and Speaking skills)
The user/ individual on the job needs to know and understand how to:
SA6. speak one or more language, preferably in the local language of the site
SA7. orally and effectively communicate about sketches, drawing or instructions
provided for the rigging work
SA8. speak and convey about various, sign boards, safety rules and safety tags ,
instructions related to exit routes during emergency at the workplace
B. Professional Skills
Decision Making
The user/individual on the job needs to know and understand how to:
SB1. decide whether the work place is safe for working and also relevant task is
not creating hazardous condition for others
SB2. decide on manpower, tools , material and equipment for relevant work
SB3. decide whether the area of operation is safe for precast erection works
Plan and Organize
The user/individual on the job needs to know and understand how to:
SB4. plan work & organize required resource in coordination with team members
and superior
Customer centricity
The user/individual on the job needs to know and understand how to:
SB5. perform work as per agreed time schedule and quality
Problem solving
The user/individual on the job needs to know and understand how to:
SB6. resolve concerns raised by the rigging gang
SB7. resolve any conflict within the team
SB8. report to superior efficiently on arising of unsafe conditions and safety
violations related to erection works
Analytical Thinking
The user/individual on the job needs to know and understand how to:
SB9. correlate the sequence of rigging works with respect to other
proceeding activity of other trade
SB10. optimize resources
SB11. minimize wastages
Critical Thinking
The user/individual on the job needs to know and understand how to:
SB12. evaluate the complexity of the task and seek assistance and support
wherever required
SB13. identify violation of any safety norms which may lead to accidents
Supervise and ensure grouting and caulking activities are as per specification
Description This unit describes the skills and knowledge required to supervise and ensure
grouting and caulking activities are as per specification.
Scope The scope covers the following:
Supervise preparation of grouting and caulking agents prior to their
application
Supervise grouting and caulking works
Performance Criteria (PC) w.r.t. the Scope
Element Performance Criteria
Supervise preparation of grouting and caulking agents prior to their application
To be competent, the user/individual on the job must be able to:
PC1. ensure cleaning of RCC precast unit surfaces prior to application of bonding agents
PC2. supervise installation of temporary arrangements surrounding to the locations to be grouted
PC3. calculate tentative material requirement for grouting works and report to
concerned authority
PC4. ensure necessary materials and tools are present in order to carry out
grouting operations
PC5. ensure proportions of materials used to form grout is as per specification
PC6. supervise execution of grouting operations as per specification and ensure
grouts are being applied within stipulated time according to manufacturer’s
specification
PC7. monitor use of grouting agents and control wastage of the same during work
PC8. take corrective actions in case of faulty grouting works as per instruction of
concerned authority
PC9. ensure use of safety signage and PPEs by subordinates during activities
Supervise grouting and caulking works
PC10. ensure cleaning and preparation of surfaces of precast units for dirt and
other foreign matters using appropriate tools
PC11.supervise preparation of caulking and sealant as per specification, prior to
their application
PC12.place and ensure proper positioning of sealing
PC13.supervise application of primer on RCC precast joints as per specification
PC14. apply caulking agents to complex locations precisely using appropriate hand tools
PC15. check completed works for conformance with specification and proposed
work method and take remedial actions if any discrepancy observed a per
instruction
Knowledge and Understanding (K)
A. Organizational
Context
(Knowledge of
the company /
organization and
its processes)
The user/individual on the job needs to know and understand:
KA1. standard procedures for rigging work
KA2. safety rules and regulations for handling and storing relevant tools and
equipment and materials for rigging works
KA3. personal protection including the use of the related safety gears and
equipment
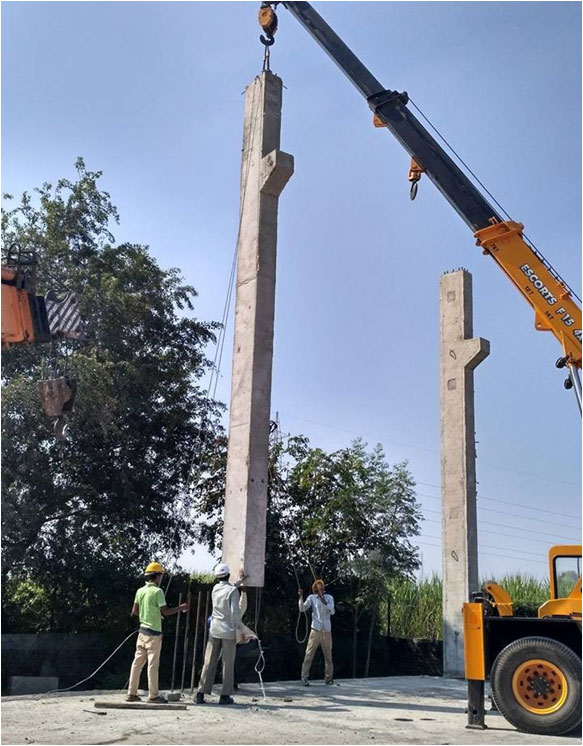
KA4. precautions and measures required in the lifting and movement of heavy
components and materials
KA5. service request procedures for tools, materials and equipments
KA6. statutory compliance requirements related to working at height
B. Technical Knowledge
The user/individual on the job needs to know and understand:
KB1. basic sketches / schematic working drawing relevant to rigging works
KB2. basic principles of measurement, geometry and arithmetic calculation
KB3. conversion of units of linear, areal and volumetric measurements
KB4. information of lifting plans and schedules
KB5. applicable tolerance to respective erection job
KB6. sequence of erection works as per proposed work method statement
KB7. specification related with grouting and caulking operations
KB8. materials used for grouting and caulking works and their physical properties
KB9. how to prepare mix for grouting and caulking work as per specification
KB10. correct technique of application of solution during grouting and caulking
works
KB11.use of hand and power tools during grouting and caulking operations
KB12.how to fill up check lists, permits applicable to erection operations
Skills (S)
A. Core Skills/
Generic Skills
Writing Skills
The user/ individual on the job needs to know and understand how to:
SA1. write in one or more language, preferably in the local language of the site
and basic English
SA2. provide clear and simple instructions, details & sketches to sub‐ordinate
Reading Skills
The user/ individual on the job needs to know and understand how to:
SA3. read one or more language, preferably in the local language of the site and
basic English
SA4. read sketches, drawing or instructions provided for the rigging work
SA5. read various, sign boards, safety rules and safety tags , instructions related to
exit routes during emergency at the workplace
Oral Communication (Listening and Speaking skills)
The user/ individual on the job needs to know and understand how to:
SA6. speak one or more language, preferably in the local language of the site
SA7. orally and effectively communicate about sketches, drawing or instructions
provided for the rigging work
SA8. speak and convey about various, sign boards, safety rules and safety tags ,
instructions related to exit routes during emergency at the workplace
B. Professional Skills
Decision Making
The user/individual on the job needs to know and understand how to:
SB1. decide whether the work place is safe for working and also relevant task is
not creating hazardous condition for others
SB2. decide on manpower, tools , material and equipment for relevant work
SB3. decide whether the preparation of grouting and caulking agents is as per
specifications prior to their application
Plan and Organize
The user/individual on the job needs to know and understand how to:
SB4. plan work & organize required resource in coordination with team members
and superior
Customer centricity
The user/individual on the job needs to know and understand how to:
SB5. perform work as per agreed time schedule and quality
Problem solving
The user/individual on the job needs to know and understand how to:
SB6. resolve concerns raised by the rigging gang
SB7. resolve any conflict within the team
SB8. report to superior efficiently on arising of unsafe conditions and safety
violations related to grouting and caulking works
Analytical Thinking
The user/individual on the job needs to know and understand how to:
SB9. correlate the sequence of rigging works with respect to other
proceeding activity of other trade
SB10. calculate tentative material requirement for grouting works
SB11. optimize resources
SB12. minimize wastages
Critical Thinking
The user/individual on the job needs to know and understand how to:
SB13. evaluate the complexity of the task and seek assistance and support
wherever required
SB14. identify violation of any safety norms which may lead to accidents
Work effectively in a team to deliver desired results at the workplace
Description This unit describes the skills and knowledge required to work effectively within a
team to achieve the desired results.
Scope The scope covers the following:
Interact and communicate effectively with co-workers, superiors and subordinates across different teams
Support co-workers, superiors and sub-ordinates within the team and across
interfacing teams to ensure effective execution of assigned task
Performance Criteria (PC) w.r.t. the Scope
Element Performance Criteria
Interact and communicate in effective and conclusive manner
To be competent, the user / individual on the job must be able to:
PC1. pass on work related information/ requirement clearly to the team members
PC2. inform co-workers and superiors about any kind of deviations from work
PC3. address the problems effectively and report if required to immediate
supervisor appropriately
PC4. receive instructions clearly from superiors and respond effectively on the same
PC5. communicate to team members/subordinates for appropriate work technique and method
PC6. seek clarification and advice as per the requirement and applicability
Support co-workers to execute project requirements
PC7. hand over the required material, tools tackles, equipment and work fronts timely to interfacing teams
PC8. work together with co-workers in a synchronized manner
Knowledge and Understanding (K)
A. Organizational Context (Knowledge of the company / organization and its processes)
The user/individual on the job needs to know and understand:
KA1. own roles and responsibilities
KA2. importance of effective communication and establishing strong working
relationships with co-workers
KA3. risks of a failure in teamwork in terms of effects on project outcomes,
timelines, safety at the construction site, etc.
KA4. different modes of communication, and its appropriate usage
KA5. importance of creating healthy and cooperative work environment among
the gangs of workers
B. Technical Knowledge
The user/individual on the job needs to know and understand:
KB1. different activities within his work area where an interaction with other
workers is required
KB2. applicable techniques of work, properties of materials used, tools and tackles
used, safety standards that co- workers might need as per the requirement
KB3. importance of proper and effective communication and the expected adverse
effects in case of failure relating to quality, timelines, safety, risks at the
construction project site

KB4. importance and need of supporting co-workers facing problems for smooth
functioning of work
Skills (S)
A. Core Skills/
Generic Skills
Writing Skills
The user/ individual on the job needs to know and understand how to:
SA1. write in one or more languages, preferably in the local language of the site
Reading Skills
The user/ individual on the job needs to know and understand how to:
SA2. read in one or more languages, preferably in the local language of the site
SA3. read communication from team members regarding work completed,
materials used, tools and tackles used, support required
Oral Communication (Listening and Speaking skills)
The user/ individual on the job needs to know and understand how to:
SA4. speak in one or more languages, preferably in one of the local languages of the site
SA5. listen and follow instructions / communication shared by superiors/ co-
workers regarding team requirements or interfaces during work processes
SA6. orally communicate with co-workers regarding support required to complete
the respective work
B. Professional Skills
Decision Making
The user/individual on the job needs to know and understand how to:
SB1. decide on what information is to be shared with co-workers within the team
or from interfacing gang of workers
Plan and Organize
The user/individual on the job needs to know and understand how to:
SB2. plan work and organize required resources in coordination with team
members
Customer centricity
The user/individual on the job needs to know and understand how to:
SB3. complete all assigned task in coordination with team members
Problem solving
The user/individual on the job needs to know and understand how to:
SB4. take initiative in resolving issues among co-workers or report the same to
superiors
Analytical Thinking
The user/individual on the job needs to know and understand how to:
SB5. ensure best ways of coordination among team members
SB6. communicate with co-workers considering their educational / social
background
Critical Thinking
The user/individual on the job needs to know and understand how to:
SB7. evaluate the complexity of task and determine if any guidance is required
from superiors
Plan and organize work to meet expected outcomes
Description This unit describes the knowledge and the skills required for an individual to plan and
organize own work in order to meet expected outcome.
Scope This scope covers the following:
Prioritize work activities to achieve desired results
Organize desired resources prior to commencement of work
Performance Criteria (PC) w.r.t. the Scope
Element Performance Criteria
Prioritize work
activities to achieve
desired results
To be competent, the user / individual on the job must be able to:
PC1. understand clearly the targets and timelines set by superiors
PC2. plan activities as per schedule and sequence
PC3. provide guidance to the subordinates to obtain desired outcome
PC4. plan housekeeping activities prior to and post completion of work
Organize desired resources prior to commencement of work
PC5. list and arrange required resources prior to commencement of work
PC6. select and employ correct tools, tackles and equipment for completion of
desired work
PC7. complete the work with allocated resources
PC8. engage allocated manpower in an appropriate manner
PC9. use resources in an optimum manner to avoid any unnecessary wastage
PC10. employ tools, tackles and equipment with care to avoid damage to the same
PC11. organize work output, materials used, tools and tackles deployed,
PC12. processes adopted to be in line with the specified standards and instructions
Knowledge and Understanding (K)
A. Organizational Context (Knowledge of the company / organization and its processes)
The user/individual on the job needs to know and understand:
KA1. importance of proper housekeeping
KA2. policies, procedures and work targets set by superiors
KA3. roles and responsibilities in executing the work for subordinates and self
B. Technical Knowledge
The user/individual on the job needs to know and understand:
KB1. standard practices of work to be adopted for assigned task
KB2. how to use available resources in a judicious and appropriate manner to
minimize wastages or damage
Skills (S)
A. Core Skills/
Generic Skills
Writing Skills
The user/ individual on the job needs to know and understand how to:
SA1. write in one or more language, preferably in the local language of the site
SA1. list out the assigned works and targets
Reading Skills
The user/ individual on the job needs to know and understand how to:
SA2. read in one or more language, preferably in the local language of the site
SA3. read communication from co-workers, superiors and notices from other
departments as per requirement of the level
Oral Communication (Listening and Speaking skills)
The user/ individual on the job needs to know and understand how to:
SA4. speak in one or more language, preferably in one of the local language of the site
SA5. listen and follow communication shared by co-workers regarding standard work processes, resources available, timelines, etc.
SA6. communicate effectively with co-workers and subordinates
B. Professional
Skills
Decision Making
The user/individual on the job needs to know and understand how to:
SB1. decide on what sequence is to be adopted for execution of work
Plan and Organize
The user/individual on the job needs to know and understand how to:
SB2. plan and organize the materials, tools, tackles and equipment required to
execute the work
Customer centricity
The user/individual on the job needs to know and understand how to:
SB3. complete all assigned task with proper planning and organizing
Problem solving
The user/individual on the job needs to know and understand how to:
SB4. arrange or seek help to arrange for material, tools and tackles in case of
shortfall
Analytical Thinking
The user/individual on the job needs to know and understand how to:
SB5. analyze areas of work which could result in a delay of work, wastage of
material or damage to tools and tackles
Critical Thinking
The user/individual on the job needs to know and understand how to:
SB6. evaluate potential solutions to minimize avoidable delays and wastages at
the construction site
Work according to personal health, safety and environment protocol at construction site
Description This NOS covers the skill and knowledge required for an individual to work according
to personal health, safety and environmental protocol at construction site
Scope The scope covers the following:
Follow safety norms as defined by organization
Adopt healthy & safe work practices
Implement good housekeeping and environment protection process and activities
Performance Criteria (PC) w.r.t. the Scope
Element Performance Criteria Follow safety norms as defined by organization
To be competent, the user / individual on the job must be able to:
PC1. identify and report any hazards, risks or breaches in site safety to the
appropriate authority
PC2. follow emergency and evacuation procedures in case of accidents, fires,
natural calamities
PC3. follow recommended safe practices in handling construction materials,
including chemical and hazardous material whenever applicable
PC4. participate in safety awareness programs like Tool Box Talks, safety
demonstrations, mock drills, conducted at site
PC5. identify near miss , unsafe condition and unsafe act
Adopt healthy & safe work practices
PC6. use appropriate Personal Protective Equipment (PPE) as per work
requirements including:
Head Protection (Helmets)
Ear protection
Fall Protection
Foot Protection
Face and Eye Protection,
Hand and Body Protection
Respiratory Protection (if required)
PC7. handle all required tools, tackles , materials & equipment safely
PC8. follow safe disposal of waste, harmful and hazardous materials as per EHS
guidelines
PC9. install and apply properly all safety equipment as instructed
PC10. follow safety protocol and practices as laid down by site EHS department
Implement good
housekeeping
practices
PC11. collect and deposit construction waste into identified containers before
disposal, separate containers that may be needed for disposal of toxic or
hazardous waste
s
PC12. apply ergonomic principles wherever required
Knowledge and Understanding (K)
A. Organizational
Context
(Knowledge of
the company /
organization and
its processes)
The user/individual on the job needs to know and understand:
KA1. reporting procedures in cases of breaches or hazards for site safety, accidents,
and emergency situations as per guidelines
KA2. types of safety hazards at construction sites
KA3. basic ergonomic principles as per applicability
B. Technical
Knowledge
The user/individual on the job needs to know and understand:
KB1. the procedure for responding to accidents and other emergencies at site
KB2. appropriate personal protective equipment to used based on various
working condition
s
KB3. importance of handling tools, equipment and materials as per applicable
KB4. health and environments effect of construction materials as per
applicability
KB5. various environmental protection methods as per applicability
KB6. storage of waste including the following at appropriate location:
non-combustible scrap material and debris
combustible scrap material and debris
general construction waste and trash (non-toxic, non-hazardous)
any other hazardous wastes
any other flammable wastes
KB7. how to use hazardous material, in a safe and appropriate manner as per
applicability
KB8. safety relevant to tools, tackles, & requirement as per applicability
KB9. housekeeping activities relevant to task
Skills (S)
A. Core Skills/
Generic Skills
Writing Skills
The user/ individual on the job needs to know and understand how to:
SA2. write in one or more language, preferably in the local language of the site
SA3. fill safety formats for near miss, unsafe conditions and safety suggestions
Reading Skills
The user/ individual on the job needs to know and understand how to:
SA4. read in one or more language, preferably in the local language of the site
SA5. read sign boards, notice boards relevant to safety
Oral Communication (Listening and Speaking skills)
The user/ individual on the job needs to know and understand how to:
SA6. speak in one or more language, preferably in one of the local language of the
site
SA7. listen instructions / communication shared by site EHS and superiors
regarding site safety, and conducting tool box talk
SA8. communicate reporting of site conditions, hazards, accidents, etc.
B. Professional
Skills
Decision Making
The user/individual on the job needs to know and understand how to:
SB1. not create unsafe conditions for others
SB2. keep the workplace clean and tidy
Plan and Organise
SB3. N.A
Customer centricity
SB4. N.A
Problem solving
The user/individual on the job needs to know and understand how to:
SB5. identify safety risks that affect the health, safety and environment for self and
others working in the vicinity, tackle it if within limit or report to appropriate
authority
Analytical Thinking
The user/individual on the job needs to know and understand how to:
SB6. assess and analyze areas which may affect health, safety and environment
protocol on the site
Critical Thinking
The user/individual on the job needs to know and understand how to:
SB7. ensure personal safety behavior
SB8. respond to emergency