Cold Chain Process Management Specialist (1 years diploma)
Cold Chain Process Management Specialist click here
Brief Job Description: The individual at work performs market and product
demand-supply assessment for cold storage, prepares project execution and cost
plan, designs plant layout, manages project execution of cold storage, select
vendors and maintains relationship that is strategic to business and commissions
the cold storage.

Personal Attributes: The job requires the individual to have: attention to details,
ability to sit and stand at one place for a long time, physical fitness to tolerate
temperature difference in and outside cold storage, sun heat, and noise.
Description
Core Skills/Generic
Skills
Core Skills or Generic Skills are a group of skills that are key to learning and
working in today’s world. These skills are typically needed in any work
environment. In the context of the NOS, these include communication related
skills that are applicable to most job roles.
Function
Function is an activity necessary for achieving the key purpose of the sector,
occupation, or area of work, which can be carried out by a person or a group
of persons. Functions are identified through functional analysis and form the
basis of NOS.
Job role Job role defines a unique set of functions that together form a unique
employment opportunity in an organization.
Knowledge and
Understanding
Knowledge and Understanding are statements which together specify the
technical, generic, professional and organizational specific knowledge that an
individual needs in order to perform to the required standard.
National Occupational
Standards (NOS) NOS are Occupational Standards which apply uniquely in the Indian context
Occupation Occupation is a set of job roles, which perform similar/related set of functions
in an industry.
Organizational Context
Organizational Context includes the way the organization is structured and
how it operates, including the extent of operative knowledge managers have
of their relevant areas of responsibility.
Performance Criteria Performance Criteria are statements that together specify the standard of
performance required when carrying out a task.
Qualifications
Pack(QP)
Qualifications Pack comprises the set of NOS, together with the educational,
training and other criteria required to perform a job role. A Qualifications
Pack is assigned a unique qualification pack code.
Qualifications Pack
Code
Qualifications Pack Code is a unique reference code that identifies a
qualifications pack.
Scope
Scope is the set of statements specifying the range of variables that an
individual may have to deal with in carrying out the function which have a
critical impact on the quality of performance required.
Sector
Sector is a conglomeration of different business operations having similar
businesses and interests. It may also be defined as a distinct subset of the
economy whose components share similar characteristics and interests.
Sub-Sector Sub-sector is derived from a further breakdown based on the characteristics
and interests of its components.
Sub-functions Sub-functions are sub-activities essential to fulfil the achieving the objectives
of the function.
Technical Knowledge Technical Knowledge is the specific knowledge needed to accomplish specific
designated responsibilities.
Description
NSQF National Skills Qualifications Framework
QP Qualifications Pack
OS Occupational Standards
OH&S Occupational Health and Safety
PPE Personal Protective Equipment
HR Human Resources
Assess production and plan for setting-up cold storage plant
Description This OS unit is about understanding and analysing client requirements, assessing
market demand, defining project timeline and preparing for project execution and
management
Scope This unit/task covers the following:
• Gather client requirements
• Assess production demand
• Prepare for project execution and management
Range: Refrigeration unit, Evaporating unit, Condenser, Compressor, programmable
logic controller equipment, packaging lines, dock levelers, advanced graders, stacking
system, MS Office Software
Performance Criteria(PC) w.r.t. the Scope
Element Performance Criteria
Gathering client
requirements
To be competent, the user/ individual must be able to:
PC1. seek appointment and schedule meeting with client
PC2. understand and gather client requirements on type of products (Horticulture,
Dairy, Poultry, Marine, Processed food), facility (manual, semi-automated and
automated) and services (warehouse and transport)
PC3. analyse client requirements and document requirements which are clear,
unambiguous and feasible for the project as per company’s standards
PC4. share the project’s requirement document with the client
PC5. make necessary changes in the project’s requirement document as suggested
by client
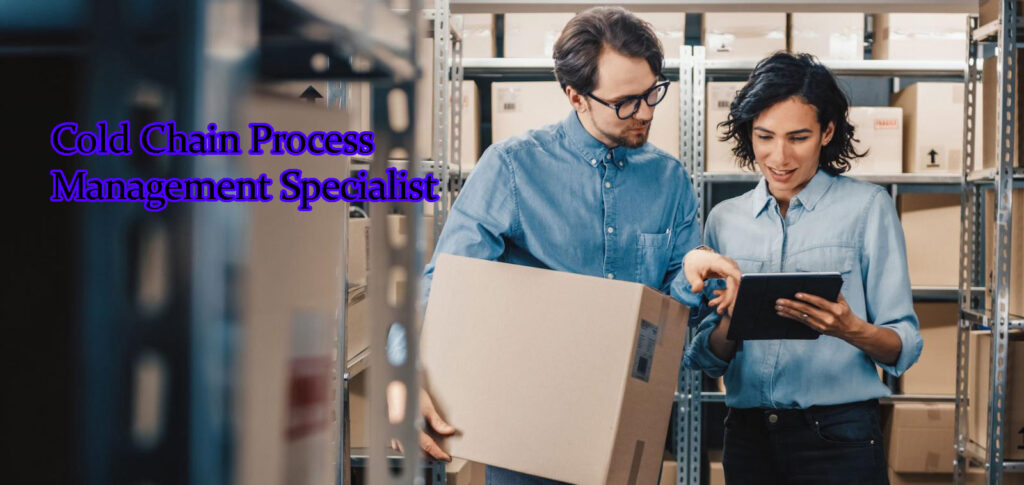
PC6. take sign-off from client
Assessing production
demand
To be competent, the user/ individual must be able to: –
PC7. visit site and assess proximity of cold storage location from market and
agricultural fields
PC8. check power availability, potable water availability and road access at the
location
PC9. determine sample size for accurate results
PC10. use quantitative and qualitative research techniques to collect data on
products, seasonality of products, product demand etc
PC11. perform secondary research on products, seasonality of products, product
demand etc
PC12. analyse information gathered from primary and secondary research
PC13. assess demand-supply of products
PC14. select products on various factors like profitability, market demand, cost of
production and transport etc
PC15. assess capacity of cold storage to meet present and future demand
PC16. prepare and share market research and assessment report with client
Preparing for project
execution and
management
To be competent, the user/ individual must be able to:
PC17. define project milestones and timelines for project activities: design, project
costing, implementation, testing and maintenance, and consulting fees
PC18. prepare communication plan, project execution plan and quality management
plan
PC19. assess risk and prepare plan for risk managment
PC20. take sign-off from client to start the project
Knowledge and Understanding (K)
A. Organizational
Context
(Knowledge of the
company /
organization and
its processes)
The individual on the job needs to know and understand: –
KA1. vision, mission and values of the company
KA2. business and performance of the company
KA3. organisation structure of the company to have better understanding of
various departments and skills set present in the company
KA4. knowledge repository and various projects done by the company
KA5. reporting structure to support and expedite project acivities
KA6. company’s policy and work instructions on quality standards
KA7. company’s policy on procurement and vendor mananagement
KA8. company’s personnel management and incentives rules
KA9. importance of the individual’s role in the workflow
KA10. occupational health and safety standards
KA11. company’s policy on business ethics and code of conduct
B. Technical
Knowledge
The individual on the job needs to know and understand: –
KB1. materials, equipments and machinery required for cold storage construction
KB2. components of modernization: programmable logic controller equipment,
packaging lines, dock levelers, advanced graders, alternate technologies,
stacking system, modernization of insulation and refrigeration etc
KB3. project management terminologies: Work breakdown structure(WBS),
Network diagram, slack, lag etc
KB4. project management methodology
KB5. types of market research techniques: quantitative and qualitative
KB6. secondary data collection methods
KB7. data analysis techniques: factor, discriminant, cluster etc
KB8. types of forecasting techniques
KB9. tools for project management and documentation: MS Project, MS excel, MS
visio, MS PowerPoint, MS Word
KB10. cold chain operation
KB11. business engineering design
KB12. arithmetic and geometry
KB13. basics of statistics: sample size, confidence interval, confidence level,
standard of deviation

Skills (S)
A. Core Skills/ Reading Skills
The user/individual on the job needs to know and understand how to:
SA1. read company’s work instructions, customer requirement and quality policy
Generic Skills SA2. read detailed project and market research reports
SA3. search and read information online for market research
Writing Skills
The user/individual on the job needs to know and understand how to:
SA4. maintain the record of job completed as per company’s policy
SA5. prepare project related documents
SA6. write business emails
Oral Communication (Listening and Speaking skills)
The user/individual on the job needs to know and understand how to:
SA7. communicate with seniors to report on any issues or delay in approvals
SA8. interact with other departments and team members to work efficiently
B. Professional Skills Decision Making
The user/individual on the job needs to know and understand how to:
SB1. decide cold storage capacity
SB2. decide market research approach and methodology
SB3. decide project duration and milestones to achieve
SB4. decide project team
SB5. decide what documents to be shared with the client required for the
implementation and commissioning of the project
Plan and Organize
The user/individual on the job needs to know and understand how to:
SB6. schedule and plan for meeting the target
SB7. plan and organise activities for market research and project management
documentation
Customer Centricity
The user/individual on the job needs to know and understand how to:
SB8. ensure completion of work as per schedule and budget
SB9. answer queries from client promptly
SB10. schedule meeting and maintain proper communication plan to keep the client
aware of progress
Problem Solving
The user/individual on the job needs to know and understand how to:
SB11. keep contigent plan ready incase of any deviation from plan
Analytical
The user/individual on the job needs to know and understand how to:
SB12. estimate project timelines and schedule
SB13. assess inputs gathered from primary and secondary research
SB14. asses market demand
Critical
The user/individual on the job needs to know and understand how to:
SB15. meet target to gather inputs from people equal to or more than sample
number in a given project timeframe
SB16. convince people to participate in primary research excercise so that market
research can be completed as per the schedule
Design cold storage plant layout and prepare project costing
Description This OS unit is about visiting and assessing site to design layout of the plant, sharing
plan and drawings of cold storage plant as per client’s requirements and calculating
cost of the project
Scope This unit/task covers the following:
• Design plant layout
• Calculate project cost
Range: Refrigeration unit, Evaporating unit, Condenser, Compressor, programmable
logic controller equipment, packaging lines, dock levelers, advanced graders, stacking
system, MS Office Software, CAD, 3D Max SketchUp, STAAD pro and CRO pro
Performance Criteria(PC) w.r.t. the Scope
Element Performance Criteria
Designing plant
layout
To be competent, the user/ individual must be able to: –
PC1. visit site and assess proposed site surroundings for designing purpose
PC2. assess space available for refrigeration, equipment, machinery, elevator,
stairs, offices, circulation and facility for loading and unloading materials
PC3. analyse functional flow and goods movement (cold rooms, warehouse,
loading and unloading facility, washing, grading, ripening chamber, packhouse
as per client’s requirement)
PC4. design corridor or circulation space and fit facilities around it
PC5. prepare plan depending on the cold storage operations, offices, parking area
etc.
PC6. share concept plan, floor plan, 3D ,structural and working drawing with the
client
PC7. calculate product load of the products stored in the cold storage
PC8. perform heat-load calculations for measurements of walls, floors, ceillings,
equipments etc
PC9. calculate size of the compressor
PC10. determine number of storeys and room sizes depending on type of product,
temperature and humidity requirement, storage capacity, manpower and fork
lift movement etc
PC11. calculate area and thickness of insulation
PC12. Determine cold storage refrigerant depending on size of chambers, location,
targeted power saving, refrigerated technology selected etc.
PC13. take sign-off from client
Calculating project
cost
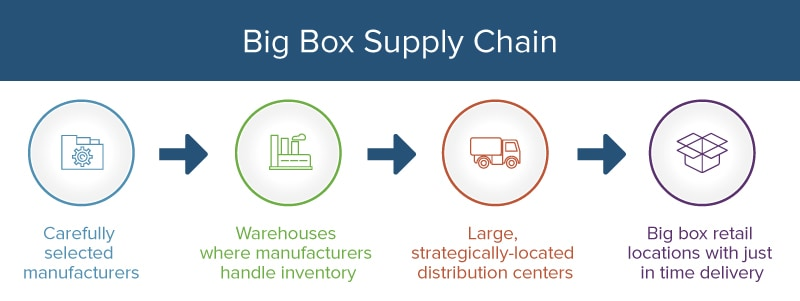
To be competent, the user/ individual must be able to:
PC14. determine land, machinery and miscellaneous assets (furniture and fixtures)
cost
PC15. determine and list down all required part assemblies, their parts, quantity and
unit of measure
PC16. add up cost of all the parts in each assembly and calculate total
PC17. determine labour required for the construction and labour cost
PC18. calculate administrative, survey, analysis and other preliminary expenses
PC19. calculate testing, commissioning and maintenance cost
PC20. calculate project cost by adding up all expenses and cost incurred
Knowledge and Understanding (K)
A. Organizational
Context
(Knowledge of the
company /
organization and
its processes)
The individual on the job needs to know and understand:
KA1. vision, mission and values of the company
KA2. business and performance of the company
KA3. organisation structure of the company to have better understanding of
various departments and skills set present in the company
KA4. standard costing and budgeting processes
KA5. knowledge repository and various projects done by the company
KA6. reporting structure to support and expedite project acivities
KA7. company’s policy and work instructions on quality standards
KA8. company’s policy on procument and vendor mananagement
KA9. company’s personnel management and incentives rules
KA10. importance of the individual’s role in the workflow
KA11. occupational health and safety standards
KA12. company’s policy on business ethics and code of conduct
B. Technical Knowledge
The individual on the job needs to know and understand: –
KB1. designing tools: CAD, 3D Max SketchUp, STAAD pro and CRO pro
KB2. design scales
KB3. how to draw concept plan, working drawing, floor plan, final plan and 3D
drawing
KB4. heat-load calculation formula
KB5. product load calculation formula
KB6. formula for calculating area and thicknes of insulation
KB7. compressor size calculation formula
KB8. architectural norms and standards
KB9. bills of materials (BOM)
KB10. cooling technology: Diffuser, Gravity cooling and overhead pump feed type
KB11. materials, equipments and machinery required for cold storage construction
KB12. components of modernization: programmable logic controller equipment,
packaging lines, dock levelers, advanced graders, alternate technologies,
stacking system, modernization of insulation and refrigeration, cold storage
refrigerant etc
KB13. tools for documentation: MS excel and MS Word
KB14. cold chain operation
KB15. business engineering design
KB16. arithmetic and geometry
Skills (S)
A. Core Skills/ Reading Skills
The user/individual on the job needs to know and understand how to:
SA1. read company’s work instructions, customer requirement and quality policy
Generic Skills SA2. read concept, working and final design plan, 3D and structural drawing
SA3. read instructions while using software tools
SA4. read project report
Writing Skills
The user/individual on the job needs to know and understand how to:
SA5. maintain the record of job completed as per company’s policy
SA6. prepare concept, working and final design plan, 3D and structural drawing
SA7. write business emails
Oral Communication (Listening and Speaking skills)
The user/individual on the job needs to know and understand how to:
SA8. communicate with seniors to report on any issues or delay in approvals
SA9. interact with other departments and team members to work efficiently
B. Professional Skills Decision Making
The user/individual on the job needs to know and understand how to:
SB1. decide parts, materials, machinery required for constructing cold storage plant
SB2. decide scale for presenting design plans
Plan and Organize
The user/individual on the job needs to know and understand how to:
SB3. schedule and plan for meeting the target
SB4. procure required software applications and get them installed before the
commencement of designing activity

Customer Centricity
The user/individual on the job needs to know and understand how to:
SB5. ensure completion of work as per schehdule and budget
SB6. answer queries from client promptly
SB7. schedule meetings and maintain proper communication plan to keep the client
aware of progress
Problem Solving
The user/individual on the job needs to know and understand how to:
SB8. troubleshoot basic software problems
SB9. keep contigent plan ready incase of any deviation from plan
Analytical
The user/individual on the job needs to know and understand how to:
SB10. estimate project cost without errors
Critical
The user/individual on the job needs to know and understand how to:
SB11. optimise processes and reduce wastage of goods during movement from one
facility to the other
SB12. complete designing activity on time without compromising on creativity
Execute and implement cold storage project
Description This OS unit is about assigning tasks to team members, issuing materials for
construction to concerned person or department, monitoring project related
activities, tracking and documenting progress
Scope This unit/task covers the following:
• Manage material and human resources
• Track and monitor activities
• Report and document activities
Range: Refrigeration unit, Evaporating unit, Condenser, Compressor, programmable
logic controller equipment, packaging lines, dock levelers, advanced graders, stacking
system, Enterprise resource planning software (ERP), MS Office Software, CAD, 3D
Max SketchUp, STAAD pro and CRO pro
Performance Criteria(PC) w.r.t. the Scope
Element Performance Criteria
Managing material
and human resource
To be competent, the user/ individual must be able to:
PC1. refer detailed project report project execution plan and prepare detailed
project construction plan
PC2. break down project execution activities to everyday tasks
PC3. take print out of tasks to be performed everyday
PC4. assign tasks to team members
PC5. take construction requirements from stakeholders
PC6. issue materials as per requirement and availability
PC7. handle grievances of team members and laborer’s
Tracking and monitoring of activities
To be competent, the user/ individual must be able to:
PC8. conduct status meetings
PC9. record minutes of meeting and follow up
PC10. keep a track on expenses incurred and manhours utilized
PC11. keep a track on how much quantity of raw materials etc are ordered and
utilized
PC12. take a round of the premises and inspect the site
PC13. ensure issued materials, equipments, machinery etc are used for construction
PC14. track and monitor activities to ensure tasks’ completion on time
PC15. escalate any non-completion of task or comprise on quality to concerned
authority
Reporting and documenting activities
To be competent, the user/ individual must be able to:
PC16. share detailed project report consisting of details on project team, project
execution, quality management, risk management, stakeholder and
communication management with the client as per company’s standards
PC17. document expenses incurred and manhours utilized
PC18. report to client and seniors about the progress of the project
Knowledge and Understanding (K)
A. Organizational
Context
(Knowledge of the
company /
organization and
its processes)
The individual on the job needs to know and understand:
KA1. vision, mission and values of the company
KA2. business and performance of the company
KA3. organisation structure of the company to have better understanding of
various departments and skills set present in the company
KA4. knowledge repository and various projects done by the company
KA5. reporting structure to support and expedite project acivities
KA6. company’s policy and work instructions on quality standards
KA7. company’s policy on procument and vendor mananagement
KA8. company’s personnel management and incentives rules
KA9. importance of the individual’s role in the workflow
KA10. occupational health and safety standards
KA11. company’s policy on business ethics and code of conduct
KA12. fire Policy from any insurance company as per Company’s Policy
B. Technical
Knowledge
The individual on the job needs to know and understand: –
KB1. tools for project management and documentation: MS Project, MS excel, MS
visio, MS PowerPoint, MS Word
KB1. project management process and related terminologies
KB2. insurance for plant and machinery during erection and commissioning
KB3. application of principles of refrigeration
KB4. materials, equipments and machinery requirements for cold storage
construction activities
KB5. components of modernization: programmable logic controller equipment,
packaging lines, dock levelers, advanced graders, alternate technologies,
stacking system, modernization of insulation and refrigeration etc
KB6. interpreting concept plan, working drawing, floor plan, final plan and 3D
drawing
KB7. cold storage operation
KB8. business engineering design
KB9. bills of materials (BOM)
Skills (S)
A. Core Skills/
Generic Skills
Reading Skills
The user/individual on the job needs to know and understand how to:
SA1. read company’s work instructions, customer requirement and quality policy
SA2. read concept, working and final design plan, 3D and structural drawing
SA3. read project report and other project related documents
Writing Skills
The user/individual on the job needs to know and understand how to:
SA4. maintain the record of job completed as per company’s policy
SA5. document day-to-day progress in project and daily expenses incurred
SA6. write business emails
SA7. write minutes of meeting
SA8. write down observations related to project execution on the site
Oral Communication (Listening and Speaking skills)
The user/individual on the job needs to know and understand how to:
SA9. communicate with seniors to report on any issues or delay in approvals
SA10. interact with other departments and team members to work efficiently
B. Professional Skills Decision Making
The user/individual on the job needs to know and understand how to:
SB1. decide and assign responsibilites to team members
SB2. select the required amount of materials, equipments and machinery for
construction
Plan and Organize
The user/individual on the job needs to know and understand how to:
SB3. schedule and plan for meeting the target
SB4. decide order of completion of tasks
SB5. arrange required materials, workforce and machinery as per quantity
mentioned and keep them ready before commencement of any construction
activity
Customer Centricity
The user/individual on the job needs to know and understand how to:
SB6. ensure completion of work as per schehdule and budget
SB7. answer queries from client promptly
SB8. schedule meeting and maintain proper communication plan to keep the client
aware of progress
Problem Solving
The user/individual on the job needs to know and understand how to:
SB9. solve issues related to workforce,material, machine, etc.
SB10. keep contigent plan ready incase of any deviation from plan
Analytical
The user/individual on the job needs to know and understand how to:
SB11. estimate requirement of materials, parts, equipment, machinery etc
SB12. optimise operations to reduce turn-around time and cost
SB13. assess risk and take appropriate action
Critical
The user/individual on the job needs to know and understand how to:
SB14. make sure team members and construction workers follow safety instructions
to avoid any accident at construction site
Manage vendor and maintain relationship
Description This OS unit is about selecting and working with vendors meeting project
requirements, negotiating contracts, evaluating performance and maintaining
relationship with vendors
Scope This unit/task covers the following:
• Assess and select new vendors
• Work with vendors
• Evaluate performance of vendors
• Establish relationship with vendors
Range: Refrigeration unit, Evaporating unit, Condenser, Compressor, programmable
logic controller equipment, packaging lines, dock levelers, advanced graders, stacking
system, Enterprise resource planning software (ERP), MS Office Software
Performance Criteria(PC) w.r.t. the Scope
Element Performance Criteria
Assessing and
selecting new
vendors
To be competent, the user/ individual must be able to:
PC1. search for possible vendors meeting project requirements
PC2. use appropriate tendering processes to receive proposals from vendors
PC3. assess and evaluate proposals submitted by vendors
PC4. call vendors for presentation or query session
PC5. select the most suitable vendor as per company’s evaluation criteria
PC6. negotiate and manage contract, Statement of work(SOW), service level
agreement(SLA) etc with the vendor
Working with
vendors
To be competent, the user/ individual must be able to:
PC7. prepare a list of materials, equipments, machinery etc
PC8. send purchase order to vendors as per company’s standards (email or courier)
PC9. receive invoice from vendors against the purchase order
PC10. receive and inspect the shipment
PC11. release payments to vendors as per the bills raised and contract signed
Evaluating performance of vendors
To be competent, the user/ individual must be able to:
PC12. record and evaluate performance of vendors on factors like quality of service,
on-time order completion, quality of material, client satisfaction, call answer
time
PC13. perform analysis on recorded information and take corrective measures to
improve performance of vendors
Establishing relationship with vendors
To be competent, the user/ individual must be able to:
PC14. inform and give purchase orders to respective vendors in advance, so that
necessary materials, machinery etc are available at the commencement of
construction activity
PC15. release payments to vendors on time
PC16. conduct review meetings
Knowledge and Understanding (K)
A. Organizational
Context
(Knowledge of the
company /
organization and
its processes)
The individual on the job needs to know and understand:
KA1. vision, mission and values of the company
KA2. business and performance of the company
KA3. organisation structure of the company to have better understanding of
various departments and skills set present in the company
KA4. knowledge repository and various projects done by the company
KA5. reporting structure to support and expedite project acivities
KA6. company’s policy and work instructions on quality standards
KA7. company’s policy on procument and vendor mananagement
KA8. company’s personnel management and incentives rules
KA9. importance of the individual’s role in the workflow
KA10. occupational health and safety standards
KA11. company’s policy on business ethics and code of conduct
B. Technical Knowledge
The individual on the job needs to know and understand:
KB1. vendor management process
KB2. factors for evaluation of performance of vendors
KB3. procurement related terminologies: Purchase order (PO), Invoice etc
KB4. about contract management, SLA and SOW
KB5. using enterprise resource planning software (ERP)
KB6. procurement process
KB7. tools for documentation: MS excel and MS Word
KB8. materials, equipments and machinery required for cold storage construction
KB9. components of modernization: programmable logic controller equipment,
packaging lines, dock levelers, advanced graders, alternate technologies,
stacking system, modernization of insulation and refrigeration etc
KB10. value chain of cold chain segment
KB11. bills of materials (BOM)
Skills (S)
A. Core Skills/
Generic Skills
Reading Skills
The user/individual on the job needs to know and understand how to:
SA1. read company’s work instructions, customer requirement and quality policy
SA2. read project report
SA3. read contracts, SLA and SOW
SA4. read PO and Invoice
SA5. read and understand vendors’ performance analysis report
Writing Skills
The user/individual on the job needs to know and understand how to:
SA6. maintain the record of job completed as per company’s policy
SA7. record information about vendors on factors like quality of service,on-time
order completion, quality of material, client satisfaction, call answer time etc
SA8. write PO and Invoice
SA9. write understand vendors’ performance analysis report
SA10. write business emails
Oral Communication (Listening and Speaking skills)
The user/individual on the job needs to know and understand how to:
SA11. communicate with seniors to report on any issues or delay in approvals
SA12. interact with other department, team members and vendors to work
efficiently
SA13. carefully listen vendor concerns and issues
B. Professional Skills Decision Making
The user/individual on the job needs to know and understand how to:
SB1. select vendors meeting project requirements
SB2. inspect shipment and decide on accepting or rejecting order
SB3. decide on corrective measures to improve performance of vendors
Plan and Organize
The user/individual on the job needs to know and understand how to:
SB4. schedule and plan for meeting the target
SB5. arrange for materials, workforce and machinery requirement in advance
SB6. plan and organise review meetings with vendors
Customer Centricity
The user/individual on the job needs to know and understand how to:
SB7. ensure completion of work as per schedule and budget
SB8. answer queries from client promptly
SB9. schedule meeting and maintain proper communication plan to keep the client
aware of progress
Problem Solving
The user/individual on the job needs to know and understand how to:
SB10. resolve issues related to vendors ,materials, machinery, etc.
SB11. keep contigent plan ready incase of any deviation from plan
Analytical
The user/individual on the job needs to know and understand how to:
SB12. select and evaluate vendors on project relevant factors
SB13. evaluate vendors on performance criteria relevant to project and business
Critical
The user/individual on the job needs to know and understand how to:
SB14. develop and maintain good and strategic relationship with vendors
Test and commission cold storage plant
Description This OS unit is about creating testing scenerios to test equipments, machinery and
operations of cold storage , escalating issues and following up with the concerned
person to resolve open issues and commissioning of cold storage plant
Scope This unit/task covers the following:
• Test cold storage plant
• Commission cold storage plant
Range: Refrigeration unit, Evaporating unit, Condenser, Compressor, programmable
logic controller equipment, packaging lines, dock levelers, advanced graders, stacking
system, MS Office Software, Cold storage testing equipments like electronic leak
detector, multimeter etc
Performance Criteria(PC) w.r.t. the Scope
Element Performance Criteria
Testing cold storage
plant
To be competent, the user/ individual must be able to:
PC1. check internal and external joints, panels and vapour seals
PC2. ensure no voids and gaps in the insulation
PC3. ensure proper fitting of doors and door heaters
PC4. confirm thermal conductivity of the insulation material fall within the range
specified by the supplier or ISO/FDIS 4898
PC5. test refrigeration sytem is functioning as per company’s standards
PC6. make certain that cold rooms are operating and maintaining defined
temperature
PC7. make certain proper functionality of control panel
PC8. make sure proper ventillation in cold rooms and ripening chambers
PC9. make sure proper installation of generator/s and electricity supply is in the
plant
PC10. ensure seamless flow of materials from one facility to the other
PC11. check rack system is in place and able to take products as well as labour load
PC12. check fire and emergency alarm
PC13. escalate issues or defects to stakeholders
PC14. follow up and resolve issues
Commissioning of cold storage plant
To be competent, the user/ individual must be able to: –
PC15. prepare schedule for commissioning activities
PC16. assign responsibilities to team members
PC17. create test scenarios for each stage of the process
PC18. determine success and failure of any test scenario
PC19. escalate failure of test scenario to stakeholders, resolve and re-test
PC20. conduct drill successfully
PC21. ensure safety mechanisms are in place
PC22. perform client training and demonstrations
PC23. obtain statutory approvals and insurance approvals
PC24. ensure maintenance of refrigeration system, machinery, equipments etc as
per contract
Knowledge and Understanding (K)
A. Organizational
Context
(Knowledge of the
company /
organization and
its processes)
The individual on the job needs to know and understand:
KA1. vision, mission and values of the company
KA2. business and performance of the company
KA3. organisation structure of the company to have better understanding of
various departments and skills set present in the company
KA4. knowledge repository and various projects done by the company
KA5. reporting structure to support and expedite project acivities
KA6. company’s policy and work instructions on quality standards
KA7. company’s policy on procurement and vendor mananagement
KA8. company’s personnel management and incentives rules
KA9. importance of the individual’s role in the workflow
KA10. occupational health and safety standards
KA11. company’s policy on business ethics and code of conduct
KA12. technical standards for design and construction of cold storages: Bureau of
Indian standards(BIS), International standard(ISO) etc
B. Technical Knowledge
The individual on the job needs to know and understand:
KB1. categories of cold storages to determine technical standards
KB2. types of testing: component testing, performance testing etc
KB3. about statutory approvals and insurance approvals required for the operation
of cold storage
KB4. process and procedure to be followed to obtain statutory approvals and
insurance approvals required for the operation of cold storage
KB5. how to conduct fire drill
KB6. equipments required for testing
KB7. components of modernization: programmable logic controller equipment,
packaging lines, dock levelers, advanced graders, alternate technologies,
stacking system, modernization of insulation and refrigeration etc
KB8. tools for project management and documentation: MS Project, MS excel, MS
visio, MS PowerPoint, MS Word
KB9. project management terminology: Work breakdown structure(WBS), Network
diagram, slack, lag etc
KB10. project management methodology
KB11. principles of refrigeration
KB12. cold chain operation
KB13. business engineering design
Skills (S)
A. Core Skills/
Generic Skills
Reading Skills
The user/individual on the job needs to know and understand how to:
SA1. read company’s work instructions, customer requirement and quality policy
SA2. read project report
SA3. read test scenarios
Writing Skills
The user/individual on the job needs to know and understand how to:
SA4. maintain the record of job completed as per company’s policy
SA5. prepare test scenarios and document results
Oral Communication (Listening and Speaking skills)
The user/individual on the job needs to know and understand how to:
SA6. communicate with seniors to report on any issues or delay in approvals
SA7. interact with other department, team members and vendors to work
efficiently
B. Professional Skills Decision Making
The user/individual on the job needs to know and understand how to:
SB1. determine success and failure of test scenario
SB2. decide on commissioning activities and the commissioning team
SB3. decide plant is functioning as per company’s standards and is ready to
handover
Plan and Organize
The user/individual on the job needs to know and understand how to:
SB4. schedule and plan for meeting the target
SB5. plan and organise testing and commissioning activities in an appropriate order
Customer Centricity
The user/individual on the job needs to know and understand how to:
SB6. ensure completion of work as per schehdule and budget
SB7. answer queries from client promptly
SB8. schedule meeting and maintain proper communication plan to keep the client
aware of progress
Problem Solving
The user/individual on the job needs to know and understand how to:
SB9. keep contigent plan ready incase of any deviation from plan
SB10. follow up and resolve open issues
Analytical
The user/individual on the job needs to know and understand how to:
SB11. differentiate defects based on high, medium and low priority
SB12. optimise operations to reduce turn-around time and cost
Critical
The user/individual on the job needs to know and understand how to:
SB13. resolve issues or defects without disturbing other functions
Maintain food and personnel safety, health and hygiene in cold storage plant
Description This OS unit is about complying with safety, health and hygiene at the workplace to
have a hazard-free environment and avoid downtime
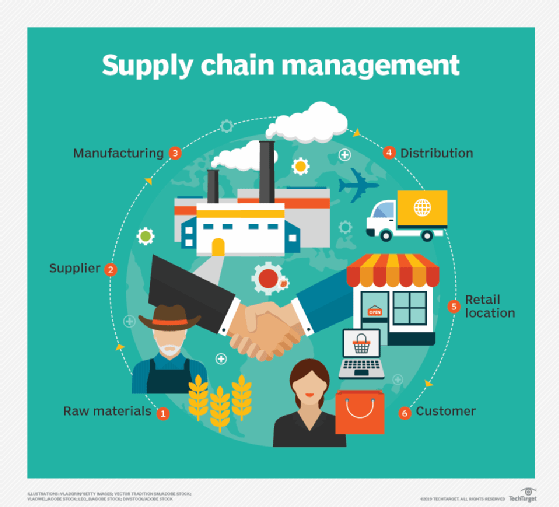
Scope This unit/task covers the following:
• Take precautionary measures to avoid work hazards
• Follow standard health, safety and hygiene procedures
Performance Criteria(PC) w.r.t. the Scope
Element Performance Criteria
Taking precautionary
measures to avoid
work hazards
To be competent, the user/ individual must be able to:
PC1. assess the various health, safety and environmental hazards in the cold storage
PC2. take necessary steps to eliminate or minimize the hazards
PC3. analyze the causes of accidents at the workplace
PC4. take preventive measures to avoid risk of cold burns and other injury due to
contact with hot surfaces, gas, fire, hot fluids/ liquids, etc.
PC5. ensure the employees have access to first aid kit when needed
PC6. ensure to use personal protective equipment and safety gear such as gloves,
jacket, footwear etc. for loading and unloading material in cold rooms to
protect themselves from hypothermia, frostbite etc
PC7. ensure to display safety signs at places where necessary for people to be
cautious
PC8. use rubber mats in the places where floors are constantly wet
PC9. ensure electrical precautions such as insulated clothing, adequate equipment
insulation, dry work area, switch off the power supply when not required, etc
PC10. display emergency exit plan at prominent places and have emergency assembly
area earmarked as a grid for easy counting of on duty associates and workers.
PC11. unplug the control panel, compressor, condensor etc before performing
maintenance
PC12. report to the superior on any problems and hazards identified
PC13. install fire alarms (electrical/manual) in cold store/deep freeze and keep other
safety devices like hammer/mallet in the storage area
Following standard health, safety and hygiene procedures
To be competent, the user/individual must be able to:
PC14. maintain appropriate ventilation in the cold rooms to avoid unacceptable
accumulation of heat, condensation or odours
PC15. check and review the cold storage areas frequently
PC16. stack items in an organized way and use safe lifting techniques to reduce risk
of injuries from handling procedures at the storage areas
PC17. ensure no sign of pest infestation and install rodent traps, fly glues and
insectocutors wherever needed
PC18. follow hygiene & sanitation standards of Government bodies like FSSAI, APEDA
and /or EIA or importing countries like FAO, EU standards after PC 20
PC19. use effective loading and unloading systems
PC20. proper stock rotation (First in First out) to be practised
PC21. segregate damaged/ non-conforming products from other products to
designate area for appropriate disposition
PC22. fumigate containers depending upon product and contamination or as per
customers’ requirement
PC23. avoid smoking, spitting, eating etc near food storage area
PC24. ensure reefers are covered, clean, free from pest infestation & other
contaminants
PC25. dispose cold storage plant waste in the designated areas safely as per
company’s policies and rules
PC26. ensure to be safe while handling machines(generator, compressor, condensor
etc), gas (ammonia) and chemicals(ethylene, refrigerants etc)
PC27. keep the floors free from oil, water and grease to avoid slippery surface
PC28. cut nails regularly and avoid applying nail paint. Avoid wearing bangles, rings,
and chains in cold storage
PC29. wash hands with soap solution and dry under a dryer as they enter for duty or
after using wash room
PC30. periodic examination of protective devices, pressure vessels and pipelines, and
parts of pipework by a competent person to prevent defect that may give rise
to danger
PC31. ensure workers suffering from abscess, boils etc should be relieved from food
handling
PC32. develop personal hygiene habits like brushing teeth, taking shower everybody,
wearing clean and tidy clothes after ironing etc
Knowledge and Understanding (K)
A. Organizational
Context
(Knowledge of the
company /
organization and
its processes)
The individual on the job needs to know and understand:
KA1. company’s HR policies on personnel management
KA2. company’s reporting structure
KA3. occupational health and safety standards
KA4. cold storageplant inspection checklist
KA5. company’s sanitary standard operating procedures
KA6. procedures to follow during emergency maintenance issues
KA7. technical standards for design and construction of cold storages: Bureau of
Indian standards(BIS), International standard(ISO) etc
B. Technical Knowledge
The individual on the job needs to know and understand:
KB1. the purpose and usage of protective gears such as gloves , jackets etc. while
working
KB2. use of first aid at workplace
KB3. cold storage order 1980
KB4. food safety and standards act 2006
KB5. reporting procedure or heirarchy for signs of damage and potential hazards
KB6. methods to minimize accidental risks
KB7. safe storage and handling of chemicals like refrigerants, ammonia, ethylene
etc
KB8. loading and unloading systems
KB9. standard operating procedure for safety drills and equipment maintenance
KB10. operation of machines: compressor, condensor, evaporator etc
KB11. emergency procedures to be followed in case of an mishap such as fire,
accidents, etc. and communication of safety instructions to subordinate
staff
KB12. emergency responses in case of malfunctioning of refrigeration equipment as
a whole or its components like evaporator, condenser or compressor
KB13. solid, liquid and gaseous waste disposal, treatment norms and equipment
KB14. necessary action to be taken for the hazards identified
KB15. knowledge of Quality systems like BRC, FSSAI, ISO, FSSC, HACCP etc
Skills (S)
A. Core Skills/
Generic Skills
Reading Skills
The user/individual on the job needs to know and understand how to:
SA1. read and interpret the relevant organisation policies, procedures and
diagrams that identify health, safety and safe environmental practices.
SA2. read job sheets, company policy documents and information displayed at the
workplace for health, safety and environment.
SA3. read notes/comments from the senior
Writing Skills
The user/individual on the job needs to know and understand how to:
SA4. fill up documentation related to health, safety and environmental standards,
if required
Oral Communication (Listening and Speaking skills)
The user/individual on the job needs to know and understand how to:
SA5. verbally report health, safety and environmental hazards and poor
organisation practice.
SA6. communicate to the supervisor about the work health, safety and
environmental issues
SA7. receive instructions from supervisor on minimizing the risks
SA8. communicate with co-workers about the precautions to be taken for hazards
free work
B. Professional Skills Decision Making
The user/individual on the job needs to know and understand how to:
SB1. take preventive measures for the identified hazards
SB2. select appropriate hand tools and personal protection equipment
SB3. identify first aid needs in case of an injury
Plan and Organize
The user/individual on the job needs to know and understand how to:
SB4. formalize and display evacuation plan at strategic locations
Customer Centricity
The user/ individual on the job needs to know and understand how to:
SB5. ensure targeted product delivery by practicing stipulated standards of
occupational health safety and environmental measures
Problem Solving
The user/individual on the job needs to know and understand how to:
SB6. take care of personal and equipment protection
SB7. identify the hazards and suggest possible solutions
Analytical
The user/individual on the job needs to know and understand how to:
SB8. use safety equipment such as fire extinguisher during fire accidents
SB9. store tools in a safe way
SB10. analyse the seriousness of the hazards
Critical
The user/individual on the job needs to know and understand how to:
SB11. evolve smooth workflow by avoiding hazards at workplace
SB12. evaluate and apply the possible solutions for the hazards, as necessary