Supervisor Erection (6 month course)
Supervisor Erection click here
Brief Job Description: Supervisor Erection is responsible for planning activities, managing
and allocating resources for heavy lifting and erection operations of structural steel
assemblies and RCC precast components at construction sites. The individual is
responsible for supervising and monitoring heavy lifting, erection works and activities by
workforce while ensuring observation of health, safety and environmental practices at
work site and completing necessary documentation as per work requirement.
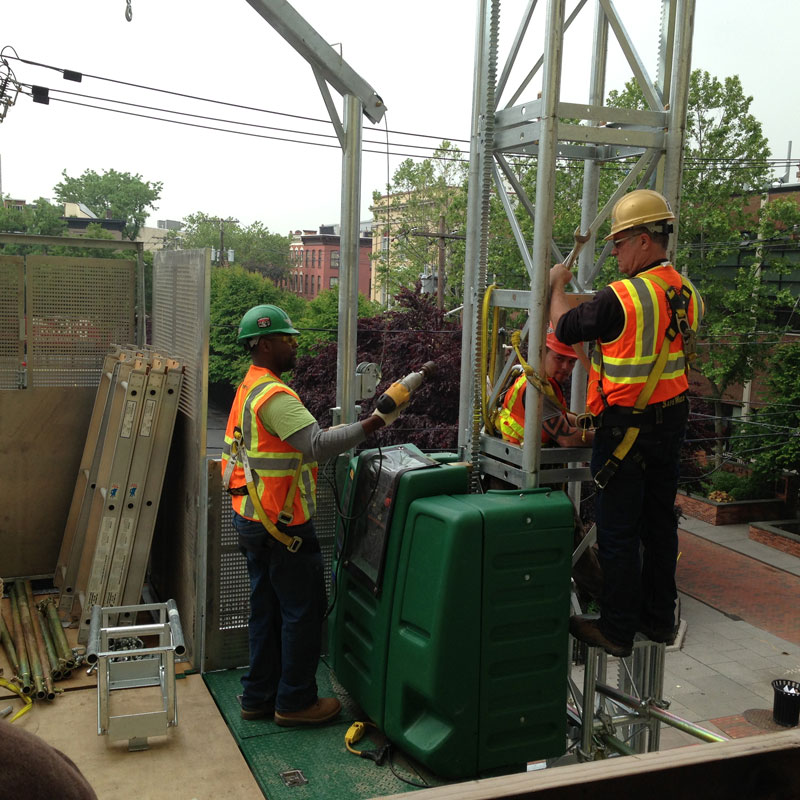
Personal Attributes: This job role requires the individual to have considerable domain
expertise to plan, sequence, supervise and troubleshoot activities at construction sites.
Individual in job role should possess good analytical skills to carry out calculation for
resource and anticipate consequences of various activities in heavy lifting and erection.
Moreover, the job holder should preferably be free from vertigo problem,
cardiovascular diseases as the nature of work involves handling heavy loads and working
at heights.
Description
Sector Sector is conglomeration of different business operations having similar
business and interests. It may also be defined as a distinct subset of the
economy whose components share similar characteristics and interests.
Sub‐Sector Sub‐Sector is derived from a further breakdown based on the characteristics
and interests of its components
Occupation Occupation is a set of job roles, which perform similar/related set of
functions in an industry
Job role Job role defines a unique set of functions that together form a unique
employment opportunity in an organization.
Occupational Standards
(OS)
OS specify the standards of performance an individual must achieve when
carrying out a function in the workplace, together with the knowledge and
understanding they need to meet the standard consistently. Occupational
Standards are applicable both in the Indian contexts.
Performance Criteria Performance Criteria are statements that together specify the standard of
performance required when carrying out a task.
Qualifications Pack (QP) Qualifications Pack comprises the set of OS, together with the educational,
training and other criteria required to perform a job role. A Qualification Pack
is assigned a unique qualification pack code
Qualification Pack Code Qualification Pack Code is a unique reference code that identifies a
qualifications pack.
National Occupational
Standards (NOS) NOS are Occupational Standards which apply uniquely in the Indian context.
Scope Scope is the set of statements specifying the range of variables that an
individual may have to deal with in carrying out the function which have a
critical impact on the quality of performance required.
Knowledge and Understanding
Knowledge and Understanding are statements which together specify th
technical, generic, professional and organizational specific knowledge that an
individual needs in order to perform to the required standard

Organizational Context Organizational Context includes the way the organization is structured and
how it operates, including the extent of operative knowledge managers have
of their relevant areas of responsibility.
Technical Knowledge Technical Knowledge is the specific knowledge needed to accomplish specific
designated responsibilities.
Core Skills / Generic Skills Core Skills or Generic Skills are a group of skills that are key to learning and
working in today’s world. These skills are typically needed in any work environment. In the context of the OS, these include communication related skills that are applicable to most job roles.
Keywords /Terms Description
CON Construction
NSQF National Skill Qualifications Framework
QP Qualification Pack
OS Occupational Standards
TBD To Be Decided
Prepare work plan for erection and ensure completion of preparatory work
Description This unit describes the skills and knowledge required to prepare work plan for
erection and ensure completion of preparatory work
Scope The scope covers the following:
Provide required inputs for planning of lifting and erection
Supervise and ensure completion of preparatory works
Performance Criteria (PC) w.r.t. the Scope
Element Performance Criteria Provide required inputs for planning of lifting and erection
To be competent, the user / individual on the job must be able to:
PC1. identify work activities as per GFC drawing requirements and report to
concerned superior
PC2. assist engineer in sequencing key activities related to lifting and erection for
making schedule
PC3. assist engineer in planning of duration and time require for identified key
activities
PC4. determine requirement of manpower to complete works in accordance with
lifting and erection work schedule
PC5. ascertain type and capacity of lifting equipment to be used as per
nature of lifting/ load to be lifted
PC6. provide inputs to concerned engineer regarding requirements for
manpower, tools, and materials as per work requirements
PC7. determine method of lifting, route and mode of transportation of structural
elements from stock yard to erection point
PC8. determine resources to be used in accordance with safety practices to be
observed during material lifting, shifting and erection operations
Supervise and ensure completion of preparatory works
PC9. prepare indent for required material, tools and tackles as per requirement
and instruction
PC10. ensure proper survey points are available at respective locations for erection
PC11. check and carry out required measurements to erection base for designed
area of bearing, embedded anchor bolts, insert plates or any other relevant
provisions according to drawing or specification
PC12. ensure shifting of structural elements from yard to lifting points in
accordance with lifting plan
PC13.supervise base preparation for lifting equipment’s and ensure completion of
all other relevant works
PC14. ensure erection of relevant safety arrangement such as signage, barricading
at specified work locations as per work safety plan
PC15. check for license of operators and certificates relevant to statutory
requirements of equipment’s to be used
PC16. deal with client, superior and subordinate as and when required
Knowledge and Understanding (K)
A. Organizational Context (Knowledge of the company / organization and its processes)
The user/individual on the job needs to know and understand:
KA1. standard practices for rigging work
KA2. safety rules and regulations for handling and storing required tools,
equipment’s and materials for rigging works
KA3. personal protection including the use of the related safety gears and
equipment
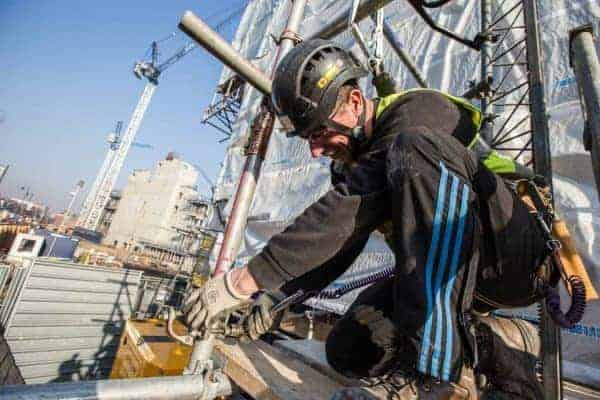
KA4. concept of job related safety precautions and deployment of safety
measurement to be observed at workplace
KA5. service request procedures for tools, materials and equipment’s
KA6. statutory compliance requirements related to working at height
KA7. statutory compliance requirement related to workmen engagement
B. Technical Knowledge
The user/individual on the job needs to know and understand:
KB1. how to read relevant structural drawings and extract technical specifications
related to erection
KB2. standard procedure for heavy load lifting operations using lifting equipment’s
KB3. sequence of lifting and erection operation as per agreed erection plan
KB4. factors affecting lifting and erection operations such as
details of the load to be handled
details of the lifting equipment and lifting gears to be used
statutory requirement of heavy lifting cranes and their operators
means of communications during lifting and erection works
key competencies required from the personnel involved in the relevant operations
ideal physical and environmental conditions for heavy lifting and erection operations
details of the zone of operation
KB5. approved code of practice related load lifting and rigging operations
KB6. concept of arithmetic and basic geometry applicable to lifting and erection operations
KB7. documentation related to rigging operation such as filling up check lists,
permits, preparation of reports etc.
KB8. documentation required to resource management such as preparation of
indents, material and manpower calculation, preparation of daily labor reports.
Skills (S)
A. Core Skills/
Generic Skills
Writing Skills
The user/ individual on the job needs to know and understand how to:
SA1. write in at least two language, preferably in the local language of the site and basic English
SA2. provide clear and simple instructions, details & sketches to sub-ordinate
SA3. record and documents daily productivity report, daily labor attendance & details regarding work
SA4. prepare basic status updates for the superiors in the prescribed format
Reading Skills
The user/ individual on the job needs to know and understand how to:
SA5. read one or more language, preferably in the local language of the site
SA6. read drawing, rigging specification and standards
SA7. read key documents including quality standards, standards working methods
& applicable tolerance limits
SA8. read various, sign boards, safety rules and safety tags , instructions related
to exit routes during emergency at the workplace
Oral Communication (Listening and Speaking skills)
The user/ individual on the job needs to know and understand how to:
SA9. speak in one or more language, preferably in one of the local language of the site
SA10. listen and follow instructions clearly given by the superior
SA11. provide clear instructions to subordinates for completion of task as per work
plan, time schedule and quality.
A. Professional Skills
Decision Making
The user/individual on the job needs to know and understand how to:
SB1. estimate required material and resources for work
SB2. decide alternate course of action in case of hindrance to work
SB3. decide on manpower required for execution of erection works
SB4. decide on appropriate method of lifting, route and mode of transportation
of structural elements from stock yard to erection point
Plan and Organize
The user/individual on the job needs to know and understand how to:
SB5. plan work & organize required resource in coordination with team members and superior
SB6. plan work targets, allocate time schedule to sub-ordinates and organize completion of task within allocated time
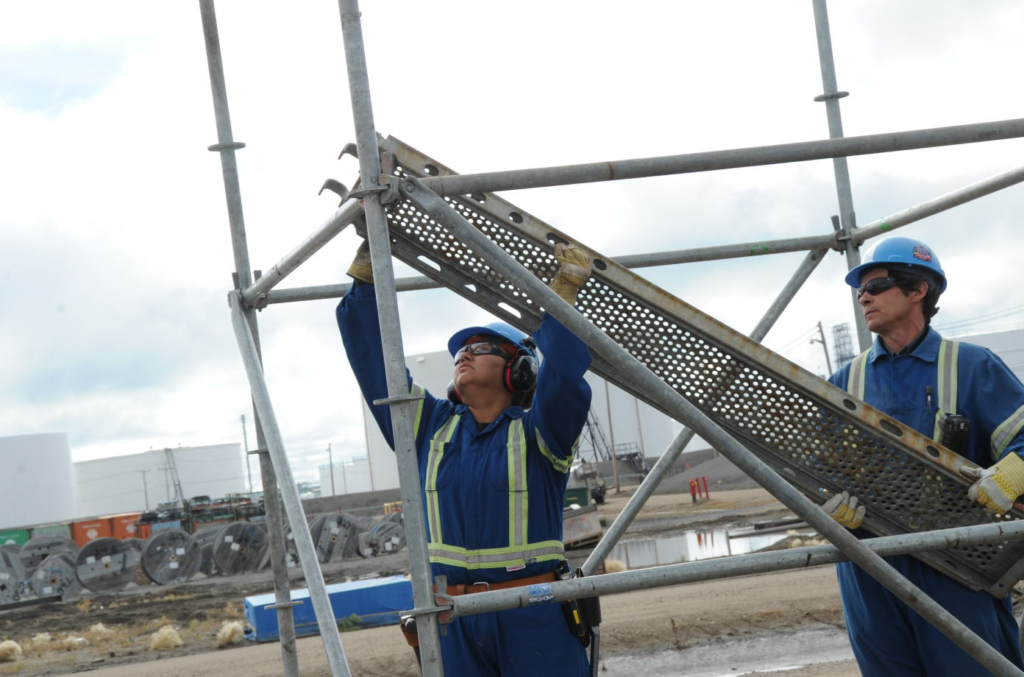
Customer centricity
The user/individual on the job needs to know and understand how to:
SB7. ensure completion of work as per agreed time schedule and quality
SB8. engage with client as per requirements
Problem solving
The user/individual on the job needs to know and understand how to:
SB9. resolve and solve any conflict within the team
Analytical Thinking
The user/individual on the job needs to know and understand how to:
SB10. assess quantity of materials and personnel for work as per plan
SB11. optimize resources
SB12. minimize wastages
SB13. analyze the type and capacity of lifting equipment to be used
Critical Thinking
The user/individual on the job needs to know and understand how to:
SB14. assess complexity of the tasks and provide guidance for carrying out
corrective action as per requirement
SB15. identify and assess how violation of any safety norms may lead to accidents
Manage equipment, manpower involved in heavy lifting and erection work
Description This unit describes the skills and knowledge required to manage equipment,
manpower involved in heavy lifting and erection work
Scope The scope covers the following:
Ensure optimum utilization of material, equipment and manpower resources
Brief lifting and erection teams on lifting plan, safe lifting
Performance Criteria (PC) w.r.t. the Scope
Element Performance Criteria
Ensure optimum utilization of material, equipment and manpower resources
To be competent, the user / individual on the job must be able to:
PC1. monitor operation of lifting equipment and keep track of runtime, idle time
and break down of cranes
PC2. instruct concerned authorities, equipment operators for starting and
stopping lifting works as per daily work plan
PC3. monitor signaling and material movement by equipment’s to meet timeline
and equipment productivity
PC4. allocate manpower to respective activities on the basis of work requirement
PC5. ensure productivity of manpower by providing instruction, checking
completed works as per drawing and reporting to senior authorities
PC6. report efficiently to the concerned authorities for equipment breakdown,
discrepancies found in the jobs
Brief lifting and erection teams on lifting plan, safe lifting
PC7. brief about scope and timelines to be adhered for respective activities
PC8. describe about rigging gears to be used in material lifting operations and
standard procedure for checking the same
PC9. describe standard procedure of using rigging gears while lifting heavy loads
by equipments
PC10. provide information about hazards and risks involved in heavy lifting and
erection operations
PC11. provide direction regarding PPEs to be used during lifting and erection
operations by respective gangs
PC12. brief about standard hand signaling procedure to be adhered and use of
communication devices during material handling
PC13. provide direction for reporting procedure to be maintained during activity
and under emergency situations
Knowledge and Understanding (K)
A. Organizational Context (Knowledge of the company / organization and its processes)
The user/individual on the job needs to know and understand:
KA1. standard practices for rigging work
KA2. safety rules and regulations for handling and storing required tools,
equipment’s and materials for rigging works
KA3. personal protection including the use of the related safety gears and equipment
KA4. concept of job related safety precautions and deployment of safety
measurement to be observed at workplace
KA5. service request procedures for tools, materials and equipment’s
KA6. statutory compliance requirements related to working at height
KA7. statutory compliance requirement related to workmen engagement
B. Technical Knowledge
The user/individual on the job needs to know and understand:
KB1. how to calculate productivity of equipment used in rigging works
KB2. ideal time of day to conduct heavy lifting operations
KB3. standard procedure of signaling using hand and communication devices
KB4. job requirement and level of competencies required from a worker to
execute specific works
KB5. how to communicate efficiently to achieve desired outcome form a team
KB6. reporting procedure as per organizational norms
KB7. scope of work and timelines to be met according to agreed lifting and erection plan
KB8. commonly used rigging gears for heavy material lifting and their respective uses
KB9. safe working load, selection and method of inspecting lifting gears for their usability
KB10.hazards and risk associated with lifting and erection operation their evaluation and risk control measures

Skills (S)
A. Core Skills/ Generic Skills Writing Skills
The user/ individual on the job needs to know and understand how to:
SA1. write in at least two language, preferably in the local language of the site
and basic English
SA2. provide clear and simple instructions, details & sketches to sub-ordinate
SA3. record and documents daily productivity report, daily labor attendance &
details regarding work
SA4. prepare basic status updates for the superiors in the prescribed format
Reading Skills
The user/ individual on the job needs to know and understand how to:
SA5. read one or more language, preferably in the local language of the site
SA6. read drawing, rigging specification and standards
SA7. read key documents including quality standards, standards working methods
& applicable tolerance limits
SA8. read various, sign boards, safety rules and safety tags , instructions related
to exit routes during emergency at the workplace
Oral Communication (Listening and Speaking skills)
The user/ individual on the job needs to know and understand how to:
SA9. speak in one or more language, preferably in one of the local language of
the site
SA10. listen and follow instructions clearly given by the superior
SA11. provide clear instructions to subordinates for completion of task as per work
plan, time schedule and quality
B. Professional Skills
Decision Making
The user/individual on the job needs to know and understand how to:
SB1. estimate required material and resources for work
SB2. decide alternate course of action in case of hindrance to work
Plan and Organize
The user/individual on the job needs to know and understand how to:
SB3. plan work & organize required resource in coordination with team members and superior
SB4. plan work targets, allocate time schedule to sub-ordinates and organize completion of task within allocated time
SB5. assess the timelines and scope of work in order to brief the team appropriately
Customer centricity
The user/individual on the job needs to know and understand how to:
SB6. ensure completion of work as per agreed time schedule and quality
SB7. engage with client as per requirements
Problem solving
The user/individual on the job needs to know and understand how to:
SB8. resolve and solve any conflict within the team
SB9. allocate necessary resources and manpower to necessary work basis
requirements
Analytical Thinking
The user/individual on the job needs to know and understand how to:
SB10. assess quantity of materials and personnel for work as per plan
SB11. optimize resources
SB12. minimize wastages
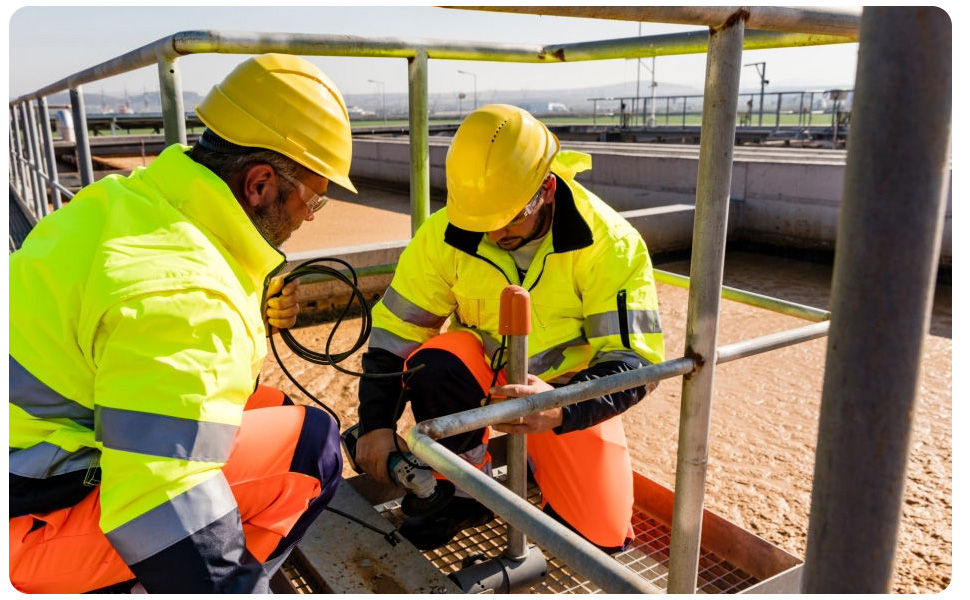
Critical Thinking
The user/individual on the job needs to know and understand how to:
SB13. assess complexity of the tasks and provide guidance for carrying out
corrective action as per requirement
SB14. identify and assess how violation of any safety norms may lead to accidents
Supervise and monitor lifting operations as per agreed work plan
Description This unit describes the skills and knowledge required to supervise and monitor lifting
operations as per agreed work plan
Scope The scope covers the following:
Ensure lifting operations comply with agreed work plan
Performance Criteria (PC) w.r.t. the Scope
Element Performance Criteria
Ensure lifting operations comply with agreed work plan
To be competent, the user / individual on the job must be able to:
PC1. ensure that the equipment being used for lifting is as per plan,
specifications and meets following required purpose
Adequate capacity of lifting
Height and distance to be covered for erection
Number of lift possible within specified time duration
Period of time for the lifting operation
Suitability of working on the available base
Provision for extending boom length
PC2. ensure that only registered crane operators, appointed riggers and
appointed signalmen participate in respective operations involving the use
of mobile and tower cranes
PC3. ensure load lifting equipment’s are in appropriate working position as per
standard practice for load lifting operations
PC4. ensure safe distance of lifting equipment’s from existing structures, live
electrical cables, service lines and stability of its outriggers
PC5. ensure proper use of rigging gears and their usability for lifting
PC6. ensure proper sequence is followed for continuous lifting process
PC7. read, interpret and adhere manufacturer’s specification and load chart
provided for lifting equipment while undertaking lifting operations
PC8. monitor and ensure effective signaling procedure while carrying out heavy
lifting operations
PC9. monitor, supervise and provide direction to the subordinates for safe and
effective lifting operation as per work requirement
PC10. monitor weather and wind speed and stop work in adverse condition in
consultation of subordinate workmen and superior authority
PC11. ensure adequate illumination is provided and they are functioning properly
at lifting area
Knowledge and Understanding (K)
A. Organizational Context (Knowledge of the company / organization and its processes)
The user/individual on the job needs to know and understand:
KA1. standard practices for rigging work
KA2. safety rules and regulations for handling and storing required tools,
equipments and materials for rigging works
KA3. personal protection including the use of the related safety gears and
equipment
KA4. concept of job related safety precautions and deployment of safety
measurement to be observed at workplace
KA5. service request procedures for tools, materials and equipment’s
KA6. statutory compliance requirements related to working at height
KA7. statutory compliance requirement related to workmen engagement
B. Technical Knowledge
The user/individual on the job needs to know and understand:
KB1. approved code of practice related load lifting and rigging operations
KB2. factors to be considered while selecting heavy lifting equipment’s
KB3. hazard and risk associated with operation of heavy lifting machines
KB4. job requirement and level of competencies required from a worker to
execute specific works
KB5. ideal position of lifting equipment while lifting heavy loads as per
manufacturer’s specification and standard practice
KB6. commonly used rigging gears for heavy material lifting and their respective uses
KB7. safe working load, selection and method of inspecting lifting gears for their usability
KB8. sequence of lifting activities as per agreed work plan
KB9. how to read and interpret load chart and its implementation while lifting heavy loads
KB10.standard procedure of signaling using hand and communication devices
KB11.how to communicate efficiently to achieve desired outcome form a team
KB12.weathering effects which has direct influence on lifting and erection
operations such as rain, heavy wind flow, storm etc.
KB13.requirement of proper illumination in lifting works
Skills (S)
A. Core Skills/
Generic Skills
Writing Skills
The user/ individual on the job needs to know and understand how to:
SA1. write in at least two language, preferably in the local language of the site
and basic English
SA2. provide clear and simple instructions, details & sketches to sub-ordinate
SA3. record and documents daily productivity report, daily labor attendance & details regarding work
SA4. prepare basic status updates for the superiors in the prescribed format
Reading Skills
The user/ individual on the job needs to know and understand how to:
SA5. read one or more language, preferably in the local language of the site
SA6. read drawing, rigging specification and standards
SA7. read key documents including quality standards, standards working methods
& applicable tolerance limits
SA8. read various, sign boards, safety rules and safety tags , instructions related
to exit routes during emergency at the workplace
Oral Communication (Listening and Speaking skills)
The user/ individual on the job needs to know and understand how to:
SA9. speak in one or more language, preferably in one of the local language of the site
SA10. listen and follow instructions clearly given by the superior
SA11. provide clear instructions to subordinates for completion of task as per work
plan, time schedule and quality
B. Professional Skills
Decision Making
The user/individual on the job needs to know and understand how to:
SB1. estimate required material and resources for work
SB2. decide alternate course of action in case of hindrance to work
SB3. decide on whether equipment used for lifting meets the required purpose
SB4. decide on appropriate sequence of work for continuous lifting operations
Plan and Organize
The user/individual on the job needs to know and understand how to:
SB5. plan work & organize required resource in coordination with team members and superior
SB6. plan work targets, allocate time schedule to sub-ordinates and organize
completion of task within allocated time
Customer centricity
The user/individual on the job needs to know and understand how to:
SB7. ensure completion of work as per agreed time schedule and quality
SB8. engage with client as per requirements
Problem solving
The user/individual on the job needs to know and understand how to:
SB9. resolve and solve any conflict within the team
SB10. stop work in adverse weather and wind conditions to avoid undue risks
Analytical Thinking
The user/individual on the job needs to know and understand how to:
SB11. assess quantity of materials and personnel for work as per plan
SB12. optimize resources
SB13. minimize wastages
Critical Thinking
The user/individual on the job needs to know and understand how to:
SB14. assess complexity of the tasks and provide guidance for carrying out
corrective action as per requirement
SB15. identify and assess how violation of any safety norms may lead to accidents
Supervise and ensure erection works in accordance with agreed work plan
Description This unit describes the skills and knowledge required to supervise and ensure
erection works in accordance with agreed work plan
Scope The scope covers the following:
Ensure erection process is according to the work plan
Ensure appropriate erection in structural steel bridge construction works
using strand jack
Performance Criteria (PC) w.r.t. the Scope
Element Performance Criteria
Ensure erection process is according to the work plan
To be competent, the user / individual on the job must be able to:
PC1. ensure timely completion of the erection activity on daily basis
PC2. coordinate with respective departments for required supporting activities to
achieve smooth erection work
PC3. ensure adequate illumination at the location of erection
PC4. ensure proper location, elevation and alignment of erected structural
components are as per drawing and specification and within limit of
tolerance
PC5. ensure joining activities such as bolting, riveting welding are being carried
out as per specifications and checked by respective authorised personnel
PC6. monitor weather and wind speed and stop work in adverse condition in
consultation of subordinate workmen and superior authority
PC7. trouble shoot if any critical situation arises and report to senior authority if
cannot be resolved
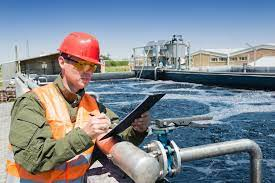
PC8. keep records of work stoppage, labor report, force majeure and report it
to senior authority as per company norms
PC9. ensure presence and efficient use of PPEs, work permits and work relevant
safety devices at work area
Ensure appropriate erection in structural steel bridge construction works using strand jack
PC10. check for positioning of anchor plates at steel assembly to be erected
PC11. check for proper locking of strands in to specified locations in order to pull assembly safely
PC12. ensure that optimum torque is provided for locking of strands
PC13. carry out visual inspection for rigidity of guiderails provided
PC14. ensure adequate number and thickness of bearing pads prior to exposing the structure to load
PC15. check displacements of structural assembly periodically at appropriate
intervals as per work method statement
PC16. provide appropriate direction during pulling to equipment operators to ensure its appropriate location, alignment as per drawing
Knowledge and Understanding (K)
A. Organizational Context (Knowledge of the company / organization and its processes)
The user/individual on the job needs to know and understand:
KA1. standard practices for rigging work
KA2. safety rules and regulations for handling and storing required tools,
equipments and materials for rigging works
KA3. personal protection including the use of the related safety gears and
equipment
KA4. concept of job related safety precautions and deployment of safety
measurement to be observed at workplace
KA5. service request procedures for tools, materials and equipment’s
KA6. statutory compliance requirements related to working at height
KA7. statutory compliance requirement related to workmen engagement
B. Technical Knowledge
The user/individual on the job needs to know and understand:
KB1. work and time scheduled to be adhered during erection operations
KB2. details of authorized persons of respective departments and mode of communication to be followed
KB3. requirement of proper illumination in lifting works
KB4. structural specification to be followed in erection works regarding alignment, orientation and elevation of erected structure
KB5. permissible limit of tolerance for specific erection activities
KB6. how to read relevant structural drawings and extract technical specifications related to erection
KB7. weathering effects which has direct influence on lifting and erection operations such as rain, heavy wind flow, storm etc.
KB8. technical specifications related to use of bolts, rivets or welded joints as per applicability
KB9. standard torque to be provided during bolting works as per specification
KB10. how to resolve undesired occurrences and procedure of reporting as per organizational norms
KB11. hazards and risk associated with lifting and erection operation their evaluation and risk control measures
Skills (S)
A. Core Skills/ Generic Skills Writing Skills
The user/ individual on the job needs to know and understand how to:
SA1. write in at least two language, preferably in the local language of the site
and basic English
SA2. provide clear and simple instructions, details & sketches to sub-ordinate
SA3. record and documents daily productivity report, daily labor attendance & details regarding work
SA4. prepare basic status updates for the superiors in the prescribed format
Reading Skills
The user/ individual on the job needs to know and understand how to:
SA5. read one or more language, preferably in the local language of the site
SA6. read drawing, rigging specification and standards
SA7. read key documents including quality standards, standards working
methods & applicable tolerance limits
SA8. read various, sign boards, safety rules and safety tags , instructions related
to exit routes during emergency at the workplace
Oral Communication (Listening and Speaking skills)
The user/ individual on the job needs to know and understand how to:
SA9. speak in one or more language, preferably in one of the local language of the site
SA10. listen and follow instructions clearly given by the superior
SA11. provide clear instructions to subordinates for completion of task as per work plan, time schedule and quality
B. Professional Skills Decision Making
The user/individual on the job needs to know and understand how to:
SB1. estimate required material and resources for work
SB2. decide alternate course of action in case of hindrance to work
SB3. decide on optimum level of torque for locking of strands
SB4. decide on appropriate number and thickness of bearing pads required

Plan and Organize
The user/individual on the job needs to know and understand how to:
SB5. plan work & organize required resource in coordination with team members
and superior
SB6. plan work targets, allocate time schedule to sub-ordinates and organize
completion of task within allocated time
Customer centricity
The user/individual on the job needs to know and understand how to:
SB7. ensure completion of work as per agreed time schedule and quality
SB8. engage with client as per requirements
Problem solving
The user/individual on the job needs to know and understand how to:
SB9. resolve and solve any conflict within the team
SB10. stop work in case of adverse weather or wind conditions
Analytical Thinking
The user/individual on the job needs to know and understand how to:
SB11. assess quantity of materials and personnel for work as per plan
SB12. optimize resources
SB13. minimize wastages
Critical Thinking
The user/individual on the job needs to know and understand how to:
SB14. assess complexity of the tasks and provide guidance for carrying out
corrective action as per requirement
SB15. identify and assess how violation of any safety norms may lead to accidents
Supervise, monitor and evaluate performance of subordinates at workplace
Description This OS covers the skills and knowledge required by an individual to supervise,
monitor and evaluate performance of subordinates at work place
Scope The scope covers the following:
Monitor all construction work activities performed by subordinates, evaluate
their performance and ensure strict adherence to quality instructions and
timelines as per organizational policies and procedures
Performance Criteria (PC) w.r.t. the Scope
Element Performance Criteria
Supervise, monitor and evaluate performance of all subordinates and ensure adherence to
organizational policies and procedures
To be competent, the user/individual on the job must be able to:
PC1. fix expected targets for the respective gang as per site requirements
and allocate work to subordinates
PC2. establish expected performance standards and expectations for the respective
gang of workers to meet the desired outcomes
PC3. inspect assigned work to the respected gang of workers through progressive
checking
PC4. observe and verify the work activities performed by the subordinates at the
construction site
PC5. monitor overall performance of subordinates on the designed measures to
ensure quality requirements set by the concerned authority
PC6. ensure adherence to the organizational policies and procedures for all
relevant construction activities by the workmen subordinations
Knowledge and Understanding (K)
A. Organizational Context (Knowledge of the company / organization and its processes)
The user/individual on the job needs to know and understand:
KA1. policies, procedures and work targets for performance evaluation and appraisals
KA2. organizational policies, procedures and protocol for smooth completion of work at the respective workplace
B. Technical Knowledge
The user/individual on the job needs to know and understand:
KB1. how to complete work/task accurately by following standard specifications
and procedures by optimized and correct used of materials , tools, tackles and
equipment
Skills (S)
A. Core Skills/
Generic Skills
Writing Skills
The user/ individual on the job needs to know and understand how to:
SA1. write in at one or more language, preferably in the local language of the site
Reading Skills
The user/ individual on the job needs to know and understand how to:
SA2. read in at one or more language, preferably in the local language of the site
Oral Communication (Listening and Speaking skills)
The user/ individual on the job needs to know and understand how to:
SA3. speak in at one or more language, preferably in one of the local languages of
the site
SA4. effectively communicate with team members at workplace
B. Professional
Skills
Decision Making
The user/individual on the job needs to know and understand how to:
SB1. rectify errors, select workman according to the performance and carry out
appropriate allocation of task
SB2. motivate the subordinate for better quality work
Plan and Organize
The user/individual on the job needs to know and understand how to:
SB3. plan work as per right sequence and organize required resources in
coordination with the team members
Customer centricity
The user/individual on the job needs to know and understand how to:
SB4. complete work as per the requirement
Problem solving
The user/individual on the job needs to know and understand how to:
SB5. solve any anomalies in work processes, critical problems & cause for delays at
workplace
Analytical Thinking
The user/individual on the job needs to know and understand how to:
SB6. sort workers activities in order of sequence and importance workers
SB7. identify root cause and effects of workers conflicts at workplace
Critical Thinking
The user/individual on the job needs to know and understand how to:
SB8. evaluate and find solutions to minimize errors and suggest improvements for
optimizing resource utilization
SB9. assess which situations would require intervention of superiors
Manage workplace for safe and healthy work environment
Description This unit describes the skill and knowledge required to maintain a healthy & safe
working environment for the group of people working under an individual
Scope The scope covers the following:
Ensure healthy and safe working environment for subordinates.
Ensure effective implementation of health, safety and environment policies
and procedures
Identify and respond to risks / fire and emergencies associated with the work
practices, workplace and ensure related organizational & statuary
requirement as followed
Performance Criteria (PC) w.r.t. the Scope
Element Performance Criteria
Ensure a healthy and
safe working
environment for
subordinates.
To be competent, the user / individual on the job must be able to:
PC1. ensure proper housekeeping at workplace
PC2. implement safe handling , stacking methods at workplace / store
PC3. ensure that health and safety plan is followed by all subordinates
PC4. identify any hazard in workplace and notify them to appropriate authority
PC5. ensure that all safety and protection installation are correctly placed &
adequate
PC6. ensure safe access is available at work place for movement of workers &
materials
PC7. ensure safe use of tools and tackles by the workmen as per applicability
PC8. ensure appropriate use of following Personal Protective Equipment (PPE) as
per applicability:
Head Protection (Helmets)
Ear Protection
Fall Protection
Foot Protection
Face and Eye Protection,
Hand &Body Protection
Respiratory Protection
PC9. maintain entrances & exit from confined spaces , excavated pits and other
location in concurrence with safety parameters or instruction form safety
personals
Identify and respond
to risks /
emergencies
associated with the
work practices,
workplace
PC10. ensure organizational policies and procedures are followed for health , safety
and welfare, in relation to:
methods of receiving or sourcing information
dealing with accidents and emergencies associated with the work and
environment
reporting
stooping work
evacuation
fire risks and safe exit procedures
PC11. follow procedures for accident recording and reporting as per organizational
and statuary requirements
PC12. ensure effective adherence to response to emergency procedures / protocols
PC13. report any case of emergency / risks to the concern people at the
construction site
PC14. report any perceived risk hazards to the superiors / concerned EHS
PC15. demonstrate the use of fire protection equipment’s for different type of fire
hazard
PC16. implement control measures to reduce risk & meet legal requirement as per
organizational policies
Knowledge and Understanding (K)
A. Organizational
Context
(Knowledge of
the company /
organization and
its processes)
The user/individual on the job needs to know and understand:
KA1. the policies, procedures and protocol set up by the EHS Department With
respect to Health , Safety and Environment at the respective construction site
KA2. reporting procedures in cases of breaches or hazards in site safety, accidents
or emergency situations
KA3. safe working practices for tools, tackles and equipment
KA4. workplace policies and health and safety requirements for dealing with
potential risks as defined by the EHS department
B. Technical Knowledge
The user/individual on the job needs to know and understand:
KB1. how to respond to accidents & emergencies
KB2. the appropriate personal protective equipment to be used based on various
working conditions
KB3. how to use necessary material ,tools, tackles and equipment in a safe and
appropriate manner as specified by site EHS for each level and respective
workman gang
KB4. how to monitor working in workplace keeping safety & health in mind
Skills (S)
A. Core Skills/
Generic Skills
Writing Skills
The user/ individual on the job needs to know and understand how to:
SA1. write in one or more languages
Reading Skills
The user/ individual on the job needs to know and understand how to:
SA2. read in one or more languages
SA3. read instructions, rules, guidelines, sign boards related to safety as per the
requirements
Oral Communication (Listening and Speaking skills)
The user/ individual on the job needs to know and understand how to:
SA4. speak in one or more language, preferably in one of the local languages of the site
SA5. listen and follow instructions shared by site EHS and superiors regarding site safety
SA6. communicate reporting of site conditions, hazards, accidents, etc.
B. Professional
Skills
Decision Making
The user/individual on the job needs to know and understand how to:
SB1. decide upon the appropriate application & installation of safety equipment’s
like barricades and nets
SB2. decide upon the tools box talks contents
Plan and Organize
The user/individual on the job needs to know and understand how to:
SB3. identify any hazards in workplace organize safety equipment’s prior to
commencing work
Customer centricity
The user/individual on the job needs to know and understand how to:
SB4. work to ensure safe and healthy environmental conditions at workplace
Problem solving
The user/individual on the job needs to know and understand how to:
SB5. identify analysis & report hazards, accidents, health and safety risks, etc. or
seek help from the appropriate authorities to address the same as per the
guidelines laid down by site EHS
Analytical Thinking
The user/individual on the job needs to know and understand how to:
SB6. analyze areas of work which are potential safety hazards and could result
in damage to life or property for the respective gang at the construction site
Critical Thinking
The user/individual on the job needs to know and understand how to:
SB7. respond to critical health risks or accidents on an urgent basis through
appropriate actions