Free Automation Specialist Course (6Months)
Automation Specialist:
Brief Job Description
Individuals at this job are responsible for providing support to production operations through maintenance of process control systems installed at shop floor for various Manufacturing processes.
Personal Attributes
This job requires the individual to work independently and take decisions pertaining to ones area of work. The individual should be result oriented. The individual should also be able to demonstrate skills for information ordering, mathematical and logical reasoning, manual dexterity and oral expression skills along with comprehension. The individual must be physically fit as he has to maintain unusual working hours.
Work effectively in a team:
Elements and Performance Criteria
Effective communication
To be competent, the user/individual on the job must be able to:
PC1. maintain clear communication with colleagues
PC2. work with colleagues
PC3. pass on information to colleagues in line with organisational requirements
PC4.. work in ways that show respect for colleagues
PC5. carry out commitments made to colleagues
PC6. let colleagues know in good time if cannot carry out commitments, explaining the reasons
PC7. identify problems in working with colleagues and take the initiative to solve these problems
PC8. follow the organisations policies and procedures for working with colleagues
PC9. ability to share resources with other members as per priority of tasks
Knowledge and Understanding (KU)
The individual on the job needs to know and understand:
KU1. the organisations policies and procedures for working withcolleagues, role and responsibilities in relation to this
KU2. the importance of effective communication and establishing goodworking relationships with colleagues
KU3. different methods of communication and the circumstances inwhich it is appropriate to use these
KU4. benefits of developing productive working relationships withcolleagues
KU5. the importance of creating an environment of trust and mutualrespect
KU6. whether not meeting commitments, will have implications onindividuals and the organisation
KU7. different types of information that colleagues might need and theimportance of providing this information when it is required
KU8. the importance of problems, from colleagues perspective andhow to provide support, where necessary, to resolve these
Generic Skills (GS)
User/individual on the job needs to know how to:
GS1. complete well written work with attention to detail
GS2. read instructions, guidelines/procedures
GS3. listen effectively and orally communicate information
GS4. make decisions on a suitable course of action or response
GS5. plan and organise work to achieve targets and deadlines
GS6. check that the work meets customer requirements
GS7. deliver consistent and reliable service to customers
GS8. apply problem solving approaches in different situations
GS9. apply balanced judgements to different situations
GS10. apply good attention to detail
GS11. check that the work is complete and free from errors
GS12. get work checked by peers
GS13. work effectively in a team environment

Maintain a safe and healthy working environment:
Elements and Performance Criteria
Identify and report the risks identified
To be competent, the user/individual on the job must be able to:
PC1.. Identify activities which can cause potential injury through sharp objects, burns, fall, electricity, gas leakages, radiation, poisonous fumes, chemicals ,loud noise
PC2. Inform the concerned authorities about the potential risks identified in the processes, workplace area/ layout, materials used etc
PC3. Inform the concerned authorities about machine breakdowns, damages which can potentially harm man/ machine during operations
PC4. Create awareness amongst other by sharing information on the identified risks
Create and sustain a Safe, clean and environment friendly work place
To be competent, the user/individual on the job must be able to:
PC5.. Follow the instructions given on the equipment manual describing the operating process of the equipments
PC6.. Follow the Safety, Health and Environment related practices developed by the organization
PC7. Operate the machine using the recommended Personal Protective Equipments (PPE)
PC8. . Maintain a clean and safe working environment near the work place and ensure there is no spillage of chemicals, production waste, oil, solvents etc
PC9. Maintain high standards of personal hygiene at the work place
PC10. Ensure that the waste disposal is done in the designated area and manner as per organization SOP.
PC11. Inform appropriately the medical officer/ HR in case of self or an employees illness of contagious nature so that preventive actions can be planned for others
Knowledge and Understanding (KU)
The individual on the job needs to know and understand:
KU1. relevant standards, procedures and policies related to Health, Safety and Environment followed in the company
KU2. basic knowledge of Safety procedures( fire fighting, first aid) within the organization
KU3. knowledge of various types of PPEs and their usage
KU4. basic knowledge of risks/hazards associated with each occupation in the organization
KU5. how to safely operate various tools and machines and risksassociated with the tools/ equipment
KU6. knowledge of personal hygiene and how an individual an contribute towards creating a highly safe and clean working environment
Generic Skills (GS)
User/individual on the job needs to know how to:
GS1. write basic level notes and observations
GS2. read safety instructions put up across the plant premises
GS3. read safety precautions mentioned in equipment manuals and panels to understand the potential risks associated
GS4. effectively communicate information to team members
GS5. informemployees in the plant and concerned functions about events, incidents & potential risks observed related to Safety, Health and Environment.
GS6. question operator/ supervisor in order to understand the safety related issues
GS7. attentively listen with full attention and comprehend the information given by the speaker during safety drills and training programs
GS8. use common sense and make judgments during day to day basis
GS9. use reasoning skills to identify and resolve basic problems
GS10. use common sense and make judgments during day to day basis
GS11. use reasoning skills to identify and resolve basic problems

Repair and maintain the process control systems:
Elements and Performance Criteria
Inspection of process control and automation systems
To be competent, the user/individual on the job must be able to:
PC1.. prepare a PM schedule for the process control and automation systems listed below installed manufacturing process wise based on recommendations of the OE and past experience Limit switches VFDs HMIs SCADA PLCs Robotics
PC2.. based on the schedule , inspect the systems and identify the replacements in the systems
PC3.. if required , attend to the breakdown of systems during manufacturing processes in operation
PC4.. ensure that all the systems are integrated through a computer interface
PC5.. coordinate with the system vendor and arrange for procurement of critical spares
PC6.. store the spares received in plant at the designated locations of the warehouse for maintenance items in coordination with stores manager
PC7.. ensure that the software used for system interfacing are upgraded as per the requirement
PC8.. coordinate with machine/systems/robot vendors and if required , in consultation with sourcing department , finalize an amc for upkeep of the machines/systems/robots etc.
PC9.. use appropriate ppe, material handling equipment and tools and carry out the task .
PC10.. use recommended methods, consumables, tools,CDs for electrical / electronic connections verification of continuity joints, including soldered software program installations and upgradations
PC11.. take support from technician, experts, user , team members from maintenance during the activity if required
PC12.. clock the time for the task so that the scheduling and planning can be improved in future
PC13.. when carrying out the installation/ shifting activity record the time and unplanned tasks encountered in the activity
PC14.. discuss with seniors in manufacturing, maintenance for improving the activity to ensure all points are adequately considered
Carrying breakdown maintenance
To be competent, the user/individual on the job must be able to:
PC15.. open the process control and automation systems under supervision of maintenance manager and if required , replace the spare parts as per the schedule
PC16.. check / confirm internal conditions of wiring , motherboards, software/ hardware malfunctioning, circuit failures etc. to verify working status to expected conditions.
PC17.. discuss with the user/ operator to learn about problems /unusual phenomenon noticed in the systems
PC18.. change the maintenance due / status sticker on the equipment.
PC19.. to attend the breakdown maintenance verify in appropriate sequence for the equipment charge leakage/ short circuit from parts breakage of wires, clamps unusual contact of electrical wires with moving parts erratic / problematic performance any problem condition as reported in the complaint
PC20.. execute sequence of activities for changing , correcting the situation after opening, verifying contact/ insulation conditions, failure of internal wires etc. and ensure the circuit elements, consumables are available at the work place.
PC21.. use appropriate ppe, material handling equipment and tools and carry out the task .
PC22.. use recommended methods, consumables, tools,CDs for electrical / electronic connections verification of continuity joints, including soldered software program installations and upgradations
PC23.. take support from technician, experts, user , team members from maintenance during the activity if required
PC24.. clock the time for the task so that the scheduling and planning can be improved in future
PC25.. when carrying out the installation/ shifting activity record the time and unplanned tasks encountered in the activity
PC26.. discuss with seniors in manufacturing, maintenance for improving the activity to ensure all points are adequately considered
Maintain the documentation
To be competent, the user/individual on the job must be able to:
PC27.. maintain a record of all the vendor and system 2d/3d- as built drawings , equipment operation related diagrams , program codes etc. in a legible and safe condition
PC28.. maintain the history of the equipment for the pm/breakdown maintenance activities in log book/history sheets / erp
PC29.. prepare the documents required for process control and automation as per the quality management system (qms) requirements
PC30.. ensure that all the documents for qms are controlled and easily traceable for future requirements too
Knowledge and Understanding (KU)
The individual on the job needs to know and understand:
KU1. company manufacturing processes & the equipment in use
KU2. existing layout for the processes
KU3. sequence of operations for each process
KU4. contract agencies for maintenance activities outsourcing in the company
KU5. complete knowledge of the process in consideration
KU6. process control and automation systems installed for the processes
KU7. type of systems being used for the process
KU8. electrical -wiring drawings of existing layout/ equipment/systems
KU9. operation of electrical equipments viz motors etc . being used for the process
KU10. robotic instruments used for process
KU11. PLC , SCADA , & electrical elements operation ,testing
KU12. Trouble shooting/ fault finding in Pneumatic, Hydraulic, Electrical control system elements
KU13. QMS system requirements
KU14. material and information flow of the process
KU15. Problem solving techniques TOPS 8D 7 QC tools etc
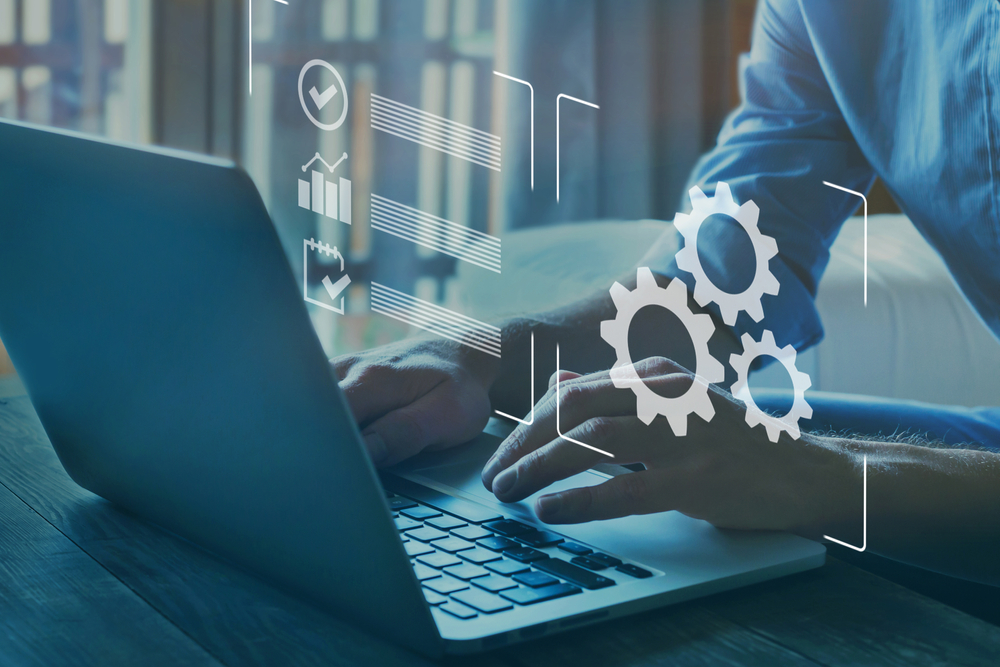
Generic Skills (GS)
User/individual on the job needs to know how to:
GS1. read the information displayed at the workplace
GS2. draft a pictorial representation of the existing layout for better comprehension
GS3. interpret the outputs obtained from process control systems like PLC , SCADA, HMI etc.
GS4. communicate with shop floor workers gathering inputs/requirements
GS5. coordinate with the shop floor workers , colleagues and enter the information related to maintenance activities in hard and soft copy as desired
GS6. interact with workers and gather all the information related to process requirements
GS7. share operation knowledge with co-workers
GS8. execute the PM of the process control and automation systems in an effective manner and on timely basis
GS9. provide inputs to maintenance manager for developing more economic and feasible measures for controlling the process parameters and specifications using the best systems
Plan and arrange for installation of new systems:
Elements and Performance Criteria
Requirements gathering
To be competent, the user/individual on the job must be able to:
PC1.. under supervision of the maintenance/ Process Engineering manager , identify the requirements for following process control and automation systems manufacturing process wise based on the organizations production capacity expansion/new capacity addition plans Limit switches VFDs HMIs SCADA PLCs Robotics RFIDs
PC2.. based on the requirements gathered , compute the individual quantity of the systems to be installed
PC3.. plan on the basis of standardization, modular arrangements etc.
Coordinate with Sourcing department for system trials
To be competent, the user/individual on the job must be able to:
PC4.. identify from the existing vendor base for the new systems procurement
PC5.. send the required drawings for the systems along with rfq to vendors and based on the quotation received , approve the most conforming vendor
PC6.. in case of the existing vendor non-competency for providing the new system , identify and approve the most economically feasible and technologically advanced vendor
PC7.. visit the approved vendors site and review the trial system run at its facility
PC8.. suggest modification (if any) in the new system for meeting the requirements
PC9.. conduct re-trials with the modified system as per convenience of vendor and approve the final system for installation communicate to the maintenance manager the system trial progress and seek feedback, if required
PC10.. based on the feedback received , finalize the technical specifications for the new system and instruct the vendor for system installation within the desired process of the organization
Procure and install the new system
To be competent, the user/individual on the job must be able to:
PC11.. raise the purchase order (p.o.) and procure the system in the organization
PC12.. inspect the system components for physical damages and if required , reject the damaged components with subsequent procurement of the fresh component
PC13.. in coordination with the vendor representative , install the new system within the desired locations in manufacturing processes
PC14.. on completion of installation , test run the entire system and identify the discrepancies (if any)
PC15.. in case of discrepancies observed , in team suggest and implement the countermeasure and re-run the system
PC16.. repeat steps pc13. to pc15. till the system is free from any discrepancies
PC17.. understand from the vendor the software coding , programming logic , electrical connections logic, hardware requirements, robotic parameters and its operation sequence etc. as per the applicability of the system. get these appropriately documented for future references
PC18.. communicate the progress to the maintenance manager and if required , run the system in his presence and seek feedback
PC19.. based on the feedback , resolve the minor discrepancies observed (if any) and finally submit the necessary system related documents and invoices to souring/purchase department
PC20.. continuously monitor the system functioning and if required consult the vendor for any issues observed
Knowledge and Understanding (KU)
The individual on the job needs to know and understand:
KU1. company manufacturing processes & the equipment in use
KU2. existing layout for the processes
KU3. sequence of operations for each process
KU4. protocol for new system installation followed in the company
KU5. approved vendor database for the process and automation systems
KU6. complete knowledge of the process in consideration
KU7. process control and automation systems installed for the processes
KU8. type of systems being used for the process
KU9. electrical -wiring drawings of existing layout/ equipment/systems
KU10. operation of electrical equipments viz motors etc . being used for the process
KU11. robotic instruments used for process
KU12. PLC , SCADA , & electrical elements operation ,testing
KU13. Trouble shooting, fault finding for electrical, Pneumatic, hydraulic controls
KU14. QMS system requirements
KU15. material and information flow of the process
Generic Skills (GS)
User/individual on the job needs to know how to:
GS1. read the information displayed at the workplace
GS2. draft a pictorial representation of the existing layout for better comprehension
GS3. interpret the outputs obtained from process control systems like PLC , SCADA, HMI etc.
GS4. communicate with shop floor workers gathering inputs/requirements
GS5. coordinate with the shop floor workers , colleagues and enter the information related to maintenance activities in hard and soft copy as desired
GS6. communicate with Sourcing and Purchase department for system trials, procurement and installation
GS7. interact with workers and gather all the information related to process requirements
GS8. share operation knowledge with co-workers
GS9. coordinate with shop floor workers and team for performing the new system installation activity efficiently
GS10. execute the requirements gathering and installation for the process control and automation systems in an effective manner and on timely basis
GS11. plan the new system trials and installation in the process without disrupting the production schedule for the process
GS12. provide inputs to maintenance manager for developing more economic and feasible measures for controlling the process parameters and specifications using the best systems
GS13. decide the most economically and technologically feasible automation and process control system for the designated manufacturing process
GS14. identify the major alternate/new vendors for the new system procurement
GS15. assess the problem, evaluate the possible solution(s) and use an optimum /best possible solution(s)
GS16. identify immediate or temporary solutions to resolve delays and crisis situations
Assessment Guidelines
- Criteria for assessment for each Qualification Pack will be created by the Sector Skill Council. Each Element/ Performance Criteria (PC) will be assigned marks proportional to its importance in NOS. SSC will also lay down proportion of marks for Theory and Skills Practical for each Element/ PC.
- The assessment for the theory part will be based on knowledge bank of questions created by the SSC.
- Assessment will be conducted for all compulsory NOS, and where applicable, on the selected elective/option NOS/set of NOS.
- Individual assessment agencies will create unique question papers for theory part for each candidate at each examination/training center (as per assessment criteria below).
- Individual assessment agencies will create unique evaluations for skill practical for every student at each examination/ training center based on these criteria.
- To pass the Qualification Pack assessment, every trainee should score the Recommended Pass % aggregate for the QP.
- In case of unsuccessful completion, the trainee may seek reassessment on the Qualification Pack.