Free CNC Operator Level 4 Course (6Months)
CNC Operator Level 4:
Brief Job Description

Machining Technician is also known as Machinist or CNC machine operator. The role covers operations of different machine tools performed both manually and through automatic/ CNC machines/ robots. This role primarily involves all kinds of machining and in-line inspection activities for quality verification, ad hoc repair work, change of worn out parts, gauging and de-burring activities.
Personal Attributes
The individual should be detailed oriented, observant; should have the ability of operation monitoring i.e., observing gauges , dials etc., good level of hand eye coordination, two hand coordination, maintaining arm steadiness, ability to quickly move hand to grasp and assemble objects (Dexterity), reading, writing and communication skills and sensitivity towards safety for self and equipment.
Maintain a safe and healthy working environment:
Elements and Performance Criteria
Identify and report the risks identified
To be competent, the user/individual on the job must be able to:
PC1.. Identify activities which can cause potential injury through sharp objects, burns, fall, electricity, gas leakages, radiation, poisonous fumes, chemicals ,loud noise
PC2. Inform the concerned authorities about the potential risks identified in the processes, workplace area/ layout, materials used etc
PC3. Inform the concerned authorities about machine breakdowns, damages which can potentially harm man/ machine during operations
PC4. Create awareness amongst other by sharing information on the identified risks
Create and sustain a Safe, clean and environment friendly work place
To be competent, the user/individual on the job must be able to:
PC5.. Follow the instructions given on the equipment manual describing the operating process of the equipments
PC6.. Follow the Safety, Health and Environment related practices developed by the organization
PC7. Operate the machine using the recommended Personal Protective Equipments (PPE)
PC8. . Maintain a clean and safe working environment near the work place and ensure there is no spillage of chemicals, production waste, oil, solvents etc
PC9. Maintain high standards of personal hygiene at the work place
PC10. Ensure that the waste disposal is done in the designated area and manner as per organization SOP.
PC11. Inform appropriately the medical officer/ HR in case of self or an employees illness of contagious nature so that preventive actions can be planned for others
Knowledge and Understanding (KU)
The individual on the job needs to know and understand:
KU1. relevant standards, procedures and policies related to Health, Safety and Environment followed in the company
KU2. basic knowledge of Safety procedures( fire fighting, first aid) within the organization
KU3. knowledge of various types of PPEs and their usage
KU4. basic knowledge of risks/hazards associated with each occupation in the organization
KU5. how to safely operate various tools and machines and risksassociated with the tools/ equipment
KU6. knowledge of personal hygiene and how an individual an contribute towards creating a highly safe and clean working environment
Generic Skills (GS)
User/individual on the job needs to know how to:
GS1. write basic level notes and observations
GS2. read safety instructions put up across the plant premises
GS3. read safety precautions mentioned in equipment manuals and panels to understand the potential risks associated
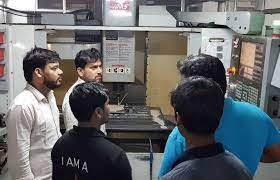
GS4. effectively communicate information to team members
GS5. informemployees in the plant and concerned functions about events, incidents & potential risks observed related to Safety, Health and Environment.
GS6. question operator/ supervisor in order to understand the safety related issues
GS7. attentively listen with full attention and comprehend the information given by the speaker during safety drills and training programs
GS8. use common sense and make judgments during day to day basis
GS9. use reasoning skills to identify and resolve basic problems
GS10. use common sense and make judgments during day to day basis
GS11. use reasoning skills to identify and resolve basic problems
Maintain 5S at the work premises:
Elements and Performance Criteria
Ensure sorting
To be competent, the user/individual on the job must be able to:
PC1.. follow the sorting process and check that the tools, fixtures & jigs that are lying on workstations are the ones in use and unnecessary items are not cluttering the workbenches or work surfaces.
PC2.. ensure segregation of waste in hazardous/ non hazardous waste as per the sorting work instructions
PC3.. follow the technique of waste disposal and waste storage in the proper bins as per sop
PC4.. segregate the items which are labelled as red tag items for the process area and keep them in the correct places
PC5. sort the tools/ equipment/ fasteners/ spare parts as per specifications/ utility into proper trays, cabinets, lockers as mentioned in the 5s guidelines/ work instructions
PC6. . ensure that areas of material storage areas are not overflowing
PC7. properly stack the various types of boxes and containers as per the size/ utility to avoid any fall of items/ breakage and also enable easy sorting when required
PC8. return the extra material and tools to the designated sections and make sure that no additional material/ tool is lying near the work area
PC9. follow the floor markings/ area markings used for demarcating the various sections in the plant as per the prescribed instructions and standards
PC10. follow the proper labeling mechanism of instruments/ boxes/ containers and maintaining reference files/ documents with the codes and the lists
Ensure proper documentation and storage ( organizing , streamlining)
To be competent, the user/individual on the job must be able to:
PC11. check that the items in the respective areas have been identified as broken or damaged
PC12. follow the given instructions and check for labelling of fluids, oils. lubricants, solvents, chemicals etc. and proper storage of the same to avoid spillage, leakage, fire etc
PC13. make sure that all material and tools are stored in the designated places and in the manner indicated in the 5s instructions
Ensure cleaning of self and the work place
To be competent, the user/individual on the job must be able to:
PC14. check whether safety glasses are clean and in good condition
PC15. keep all outside surfaces of recycling containers are clean
PC16.. ensure that the area has floors swept, machinery clean and generally clean. in case of cleaning, ensure that proper displays are maintained on the floor which indicate potential safety hazards
PC17.. check whether all hoses, cabling & wires are clean, in goodcondition and clamped to avoid any mishap or mix up
PC18.. ensure workbenches and work surfaces are clean and in good condition
PC19. follow the cleaning schedule for the lighting system to ensure proper illumination
PC20. store the cleaning material and equipment in the correct location and in good condition
PC21. ensure self-cleanliness – clean uniform, clean shoes, clean gloves, clean helmets, personal hygiene
Ensure sustenance
To be competent, the user/individual on the job must be able to:
PC22. follow the daily cleaning standards and schedules to create a clean working environment
PC23. attend all training programs for employees on 5 s
PC24. support the team during the audit of 5 s
PC25. participate actively in employee work groups on 5s and encourage team members for active participation
PC26. follow the guidelines for what to do and what not to do to build sustainability in 5s as mentioned in the 5s check lists/ work instructions
Knowledge and Understanding (KU)
The individual on the job needs to know and understand:
KU1. relevant standards, procedures and policies related to 5S followed in the company
KU2. have basic knowledge of 5S procedures
KU3. know various types 5s practices followed in various areas
KU4. understand the 5S checklists provided in the department/ team
KU5. have skills to identify useful & non useful items
KU6. have knowledge of labels , signs & colours used as indicators
KU7. knowledge on how to sort and store various types of tools, equipment, material etc.
KU8. know , how to identify various types of waste products
KU9. understand the impact of waste/ dirt/ dust/unwanted substances on the process/ environment/ machinery/ human body
KU10. have knowledge of best ways of cleaning & waste disposal
KU11. understand the importance of standardization in processes
KU12. understand the importance of sustainability in 5S
KU13. have knowledge of TQM process
KU14. have knowledge of various materials and storage norms
KU15. understand visual controls, symbols, graphs etc.

Generic Skills (GS)
User/individual on the job needs to know how to:
GS1. write basic level notes and observations
GS2. note down observations (if any) related to the process
GS3. read 5S instructions put up across the plant premises
GS4. effectively communicate information to team members inform employees in the plant and concerned functions about 5S
GS5. question the process head in order to understand the 5S related issues
GS6. attentively listen with full attention and comprehend the information given by the speaker during 5S training programs
GS7. use common sense and make judgments during day to day basis
GS8. use reasoning skills to identify and resolve basic problems using 5S
GS9. persuade co team members to follow 5 S
GS10. ensure that the co team members understand the importance of using 5 S tool
GS11. use innovative skills to perform and manage 5 S activities at the work desk and the shop floor
GS12. exhibit inquisitive behaviour to seek feedback and question on the existing set patterns of work
GS13. do what is right, not what is a popular practices
GS14. follow shop floor rules& regulations and avoid deviations; make 5S an integral way of life
GS15. ensure self-cleanliness on a daily basis
GS16. demonstrate the will to keep the work area in a clean and orderly manner
Carry out pre-machining activities:
Elements and Performance Criteria
Understanding the component requirements
To be competent, the user/individual on the job must be able to:
PC1. . before starting the machining operations, obtain a detailed and thorough understanding of the task at hand: o understand the output product requirement by reading the engineering drawing specified in the work instructions/ work order o reading the control panel instructions/ job orders to determine the correct output product specifications o understanding the tooling instructions (fixtures, cutting tools, jigs etc.) as specified in the operating manual/ work instructions or standard operating procedures o selection of proper coolant and lubricant required for machining the required component
Checking the dimensions for the component
To be competent, the user/individual on the job must be able to:
PC2. . set the machine stops or guides or programmes as per the specified lengths indicated through scales or work instructions
PC3. . measure and mark reference points/ cutting lines on the work pieces, using compasses, callipers, rulers and other measuring tools
PC4. . understand acceptance requirements/ limits of machining e.g. surface finish, specific orientation, gauge inspection etc.
PC5. . understand any other specific requirement for machining
Programming the machine for specific tool operations
To be competent, the user/individual on the job must be able to:
PC6. . assist the master machining technician in programming the cnc/ numerically controlled machine as per the work instructions
PC7.. set the right material removal rate while programming the machine as per specified requirements e.g. for hobbing set the ratio for the rotation of the shafts/spindle which determine the number of teeth made on the work piece
PC8. . discuss technical matters related to machine programming with engineer/ supervisory/ personnel in the maintenance team
Performing wheel dressing activities for grinding operations
To be competent, the user/individual on the job must be able to:
PC9. . always put machine guards in place before turning on grinding wheel
PC10.. run the wheels for a least one minute before actual work begins
PC11. . ensure proper balancing and dressing of wheels before use
PC12. . select and mount grinding wheels on machine, according to work instructions
PC13. . using hand tools and applying knowledge of abrasives and grinding procedures
PC14. . always use eye protection while performing these activities
Knowledge and Understanding (KU)
The individual on the job needs to know and understand:
KU1. relevant standards and procedures followed in the company
KU2. different types of products manufactured by the company
KU3. different types of machining processes/ tools available
KU4. different types of machining processes
KU5. basic fundamentals of machines and mechanics
KU6. different types of tools used in the machining process with respect to type of process to be conducted
KU7. basic principles of 5 S in manufacturing Cleaning, sorting, scrap handling etc.
KU8. the application of coolant and lubricants
KU9. impact of various machining processes on the final product outcome
KU10. basic Arithmetic and calculation methods for tolerance limits
KU11. safety guidelines related to different machines
Generic Skills (GS)
User/individual on the job needs to know how to:
GS1. write basic level notes and observations
GS2. draw basic level geometrical/ mechanical drawings and charts
GS3. read and interpret workplace related documentation
GS4. read and interpret engineering drawings and sketches to understand the dimension of the output product
GS5. discuss task lists and job requirements with co-workers
GS6. effectively communicate information to team members
GS7. discuss with supervisor in order to understand the nature of the problem
GS8. attentively listen with full attention and comprehend the information given by the speaker
GS9. judge when to ask for help from a supervisor
GS10. suggest options to operators in case any issue is observed during operations
GS11. plan work assigned on a daily basis and provide estimates of time required for each piece of work
GS12. prioritize actions to achieve required outcomes
GS13. analyse the complexity of work to determine if it can be successfully carried out
GS14. ability to visualize the final product from the engineering drawing/ machine drawing, sketch provided by the supervisor
GS15. analyse the cause of defects related to e.g. cutting tools, machine, fixtures etc
GS16. learn from mistakes by analysing and discussing with peers/ seniors
GS17. discuss new ideas and participate in new initiatives
GS18. follow instructions and work on areas of improvement identified
GS19. complete the assigned tasks with minimum supervision
GS20. complete the job defined by the supervisor within the timelines and quality norms
Perform different kinds of machining operations:
Elements and Performance Criteria
Setting up machine as per work instructions
To be competent, the user/individual on the job must be able to:
PC1. . change the cutting tool of the Special Purpose Machine as per the process requirement
PC2. . set-up, adjust machine tools, fixtures/ jigs and cutting tools in order to perform machining operations and keep dimension within the specified tolerance limit specified in the Standard Operating Procedures/ Operating manuals/ Control Panel
PC3. . lift the work piece/ metal stock manually or through hoist and position the same securely in the machine using fasteners and hand tools and verify their positions with measuring instruments
PC4. . check the centring and facing of the work pieces and check for alignment of the work pieces as per the final product output specifications
PC5. . check the working of different holding fixtures, gears, stops etc. to control work piece movement, using hand tools, power tools, measuring instruments
PC6. . while performing Grinding/ Boring machining activities, mark spots on the work piece/ metal stock before performing the operation
PC7. . move controls to adjust, start, or stop equipment during grinding process
PC8.. clearly understanding the does and donts of the manufacturing process as defined in SOPs/ Work Instructions or defined by supervisors
Performmachining on the component
To be competent, the user/individual on the job must be able to:
PC9. . start the lathe/ turning/milling/ shaping/ grinding/ boring/ broaching/ hobbing / facing/ shaping/ blanking/ piercing/ special purposemachine for operations
PC10.. select the right cutting/ grinding/ broaching (teeth) tool as per tooling instructions and as per the work / supervisor s instructions
PC11. . for manual grinding activities ensure the following: o Clear understanding of the metallurgical properties of the machined parts o two hand coordination is appropriate o checking the surface of the grinding plate to identify any abrasions, holes, plate inclination o Checking the rotation of the grinding wheel o understanding the usage of hardness testing machine
PC12.. for milling operations check to ensure: o revolution ridges/marks are within the defined roughness limits associated with surface finish of the work piece o two hand coordination is appropriate as for manual operations o gap setting between milling rod and component is appropriate o correct angle is selected for cutting the parts o usage of measurement such as scales, venire calipers is made as per the work instructions
PC13. . ensure that the right command is entered in the CNC machine as defined machining parameters
PC14. . in case of boring operations ensure that the length to bore diameter is fixed so that is does not cause deflection in the cutting tool
PC15. . operate hand wheels or valves in order to feed the component and allow cooling and lubricating to the tool
PC16. . turn on the coolantvalves and start their flow to maintain temperature in the machine chamber
PC17. . brush or spray lubricating material on work pieces where applicable
PC18. . move tool holders manually or by turning the hand wheels in order to feed tools along the machined component/ piece
PC19. . take appropriate action in case of any irregularities e.g. power failure, rejection, tool breakage etc.
PC20. . extract or lift jammed pieces from machines through use of wire hooks, lift bars, hands etc.
Observe/ Record the machining operations
To be competent, the user/individual on the job must be able to:
PC21. . observe machine operations to detect defects in the component manufactured
PC22.. observe the machine operations for any malfunctions and immediately inform the supervisor/ maintenance team of any malfunction observed to prevent damage to the machining equipment/ output product
PC23. . ensure recording operational data such as pressure readings, length of strokes, feed rates, speed etc. in the formats specified by the supervisor
PC24. . ensure tool replacement as per recommended tool life in no. of pieces
PC25.. enter readings of key dimensions on control charts/ SPC record; provide required tool offsetting with the help of supervisor on correct side based on the reading
Knowledge and Understanding (KU)
The individual on the job needs to know and understand:
KU1. relevant standards and procedures followed in the company
KU2. different types of products manufactured by the company
KU3. different types of machining processes/ tool available
KU4. process flow/ routing of various components in the machine shop/ organization
KU5. different types of machining processes
KU6. different types of tools used in the machining process and their identification
KU7. basic fundamentals of machines and mechanics
KU8. how to read machine drawing and machining the part to create the output as defined in the machine drawing
KU9. knowledge of metal properties/ metallurgy
KU10. knowledge of gear changing techniques and minor maintenance as per checklist
KU11. basic principles of 5 S in manufacturing Cleaning, sorting, scrap handling etc.
KU12. the application of coolants and lubricants
KU13. basic Arithmetic and calculation methods for tolerance limits
Generic Skills (GS)
User/individual on the job needs to know how to:
GS1. write basic level notes and observations
GS2. draw basic level drawings and charts
GS3. read& comprehend documents and notes, process documentation & Control Plan
GS4. interpret/ Comprehend the information given in the documents and notes
GS5. read and interpret symbols given on equipments and work area
GS6. read machine drawings/ engineering drawings, sketches
GS7. discuss task lists and job requirements with co-workers
GS8. effectively communicate information to team members
GS9. question supervisor in order to understand the nature of the problem
GS10. attentively listen with full attention and comprehend the information given by the speaker
GS11. judge when to ask for help from a supervisor
GS12. suggest options to operators in case any issue is observed during operations
GS13. plan work assigned on a daily basis and provide estimates of time required for each piece of work
GS14. ensure that customer needs are assessed and every effort is made to provide satisfactory service
GS15. recognise a workplace problem or a potential problem and take action
GS16. determine problems needing priority action
GS17. refer problems outside area of responsibility to appropriate person
GS18. gather information and provide assistance as required to solve problems
GS19. use common sense and make judgments during day to day basis
GS20. use reasoning skills to identify and resolve basic problems
GS21. follow instructions and work on areas of improvement identified
GS22. complete the assigned tasks with some supervision
GS23. complete the job defined by the supervisor within the timelines and quality norms
GS24. analyse, evaluate and apply the information gathered from observation, experience, reasoning, or communication to act efficiently
Conduct all post machining operations:
Elements and Performance Criteria
Perform minor machine maintenance activities
To be competent, the user/individual on the job must be able to:
PC1.. maintain the machine as per proper operational condition/ daily maintenance check
PC2. . perform minor machine maintenance activities such as oiling or cleaning machine and its components per the schedules given in the maintenance plan
PC3.. clean the hydraulic tank/ gauge/ tools/ fixtures as per the cleaning schedule and the process mentioned in the work instruction/ sop manual
PC4. . add coolant and lubricant in machine reservoir as per the sops
PC5. . removing chips from different machine areas and dispose of scrap or waste material into the disposal area in accordance with the company policies and environmental regulations
PC6. . for broaching operations ensure that the broaching teeth is not broken and is flushed out of any metal chips
PC7. . perform minor repairs and adjustments to the machine and notify supervisor/ maintenance team when major service/ repair is required
Perform de burring activity on the machined components
To be competent, the user/individual on the job must be able to:
PC8. . with the help of the correct tool remove the extra burrs, sharp edges, rust and chips from the metal surface
PC9. . use files, hand grinders, wire brushes, or power tools for performing de burring operations.ensure usage of personal protective equipment like eye glasses and hand gloves
PC10.. trim, scrape, or deburr objects or parts, using chisels, scrapers, and other hand tools and equipment
PC11. . for automated processes perform shot blasting/ vibro processes for completing de-burring operations
Check quality of machined component (Gauging)
To be competent, the user/individual on the job must be able to:
PC12.. measure the specifications of the finished component and verify conformance as per control plan/ work instruction
PC13. . use devices like micrometers, vernier calipers, gauges, rulers and any other inspection equipment for measuring specificationswith valid calibration status.
PC14.. note down the observations of thebasic inspection process and identify pieces which comply with the specified standards
PC15.. separate the defective pieces into two categories pieces which can be repaired/ modified and pieces which are beyond repair and maintain records of each category
PC16. . for all special parameters get the inspection done by qa/ standard room as per the frequency in the control plan and record the observations
PC15.. separate the defective pieces into two categories – pieces which can be repaired/ modified and pieces which are beyond repair and maintain records of each category
Tool Changing Process
To be competent, the user/individual on the job must be able to:
PC17. . organize changing different worn machine accessories, such as cutting/ grinding/ broaching/ hobbing tools( as per tool life listed, recommended) other hand tools
PC18.. ensure that the blunt tool is timely and safely replaced by a new tool
PC19.. replace machine part as per work instructions, using hand tools or notify supervisor/ engineering personnel for taking corrective actions
PC20. . for automated process observe the tool change cycle in order to ensure that the selected tool is transferred to the spindle from magazine after the previous tool is transferred to the magazine from the spindle
PC21. . ensure that the zero offset value is chosen at the time of tool changing process
Knowledge and Understanding (KU)
The individual on the job needs to know and understand:
KU1. relevant standards and procedures followed in the company
KU2. different types of products manufactured by the company
KU3. different types of machining processes
KU4. different types of tools used in the machining process and de-burring process
KU5. basic principles of 5 S in manufacturing Cleaning, sorting
KU6. post machining processes like deburring
KU7. Impact of presence of burrs, edges, chips on the final product performance KB6. the application of coolant and lubricants
KU8. basic Arithmetic and calculation methods
Generic Skills (GS)
User/individual on the job needs to know how to:
GS1. write basic level notes and observations
GS2. draw basic level drawings and charts
GS3. read documents and notes
GS4. interpret/ Comprehend the information given in the documents and notes
GS5. read and interpret symbols given on equipments and work area
GS6. discuss task lists and job requirements with co-workers
GS7. effectively communicate information to team members
GS8. question operator/ supervisor in order to understand the nature of the problem
GS9. attentively listen with full attention and comprehend the information given by the speaker
GS10. analyse information and evaluate results to discuss the best solution with the operator to solve problemse.g. inspection results, rework status
GS11. plan work assigned on a daily basis and provide estimates of time required for each piece of work
GS12. recognise a workplace problem or a potential problem and take action by referring problems to the supervisor/ machine setter
GS13. gather information and provide assistance as required to solve problems
GS14. use common sense and make judgments during day to day basis
GS15. use reasoning skills to identify and resolve basic problems
GS16. escalate problem beyond individuals scope
GS17. follow instructions and work on areas of improvement identified
GS18. complete the assigned tasks with some supervision
GS19. complete the job defined by the supervisor within the timelines and quality norms
Assessment Guidelines
- Criteria for assessment for each Qualification Pack will be created by the Sector Skill Council. Each Element/ Performance Criteria (PC) will be assigned marks proportional to its importance in NOS. SSC will also lay down proportion of marks for Theory and Skills Practical for each Element/ PC.
- The assessment for the theory part will be based on knowledge bank of questions created by the SSC.
- Assessment will be conducted for all compulsory NOS, and where applicable, on the selected elective/option NOS/set of NOS.
- Individual assessment agencies will create unique question papers for theory part for each candidate at each examination/training center (as per assessment criteria below).
- Individual assessment agencies will create unique evaluations for skill practical for every student at each examination/ training center based on these criteria.
- To pass the Qualification Pack assessment, every trainee should score the Recommended Pass % aggregate for the QP.
- In case of unsuccessful completion, the trainee may seek reassessment on the Qualification Pack.