Warehouse Associate (1 years diploma )
Warehouse Associate click here
Brief Job Description: The individual performs basic picking, packing, labeling,
kitting, binning, loading and unloading activities in a warehouse. S/he will
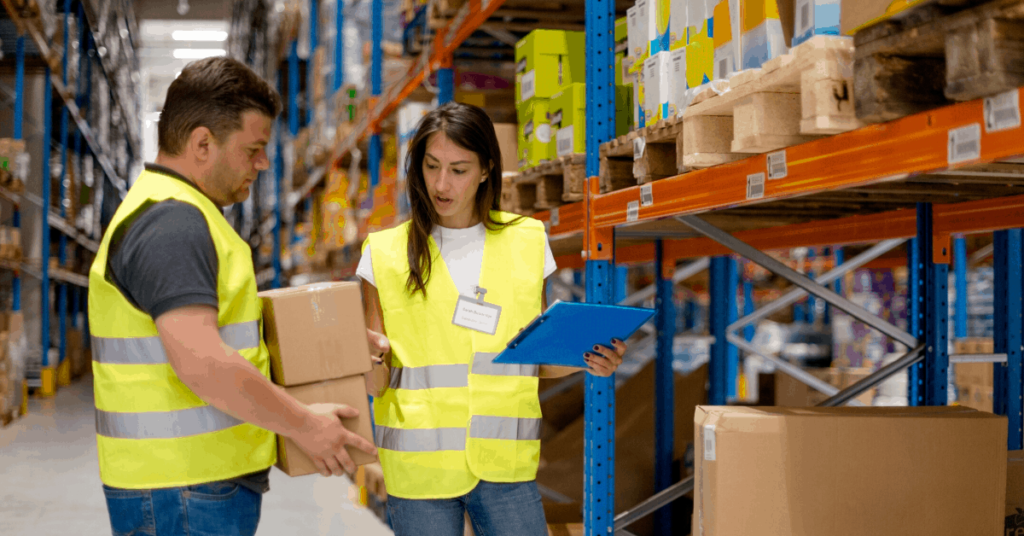
operate manual/battery operated pallet truck (MHE), will engage in inventory
counts and maintaining warehouse work area clean.
Qualifications Pack for Warehouse Associate
Electives
Elective 1: Perishable Goods
The unit is about handling perishable goods such as fruits, vegetables, and other
temperature and time sensitive goods in a warehouse
Elective 2: Fast-Moving Consumer Goods (FMCG)
The unit is about handling FMCG goods such as soaps, packaged goods, white
goods in a warehouse
Elective 3: Automotive Goods
The unit is about handling automotive components and performing palletisation,
segregation, following 5S, Just in time (JIT), Kanban and similar auto sector
processes
Elective 4: Dry Bulk cargo
The unit is about handling dry bulk cargo using conveyors and associated MHE,
undertaking pest control activity and measuring the inventory.
Options
Option 1: Goods and Services Tax (GST) application
Preparing, verifying and review applicability of GST
Personal Attributes: The job holder should be physically and medically fit to
undertake a warehouse operation which includes long hours of active material
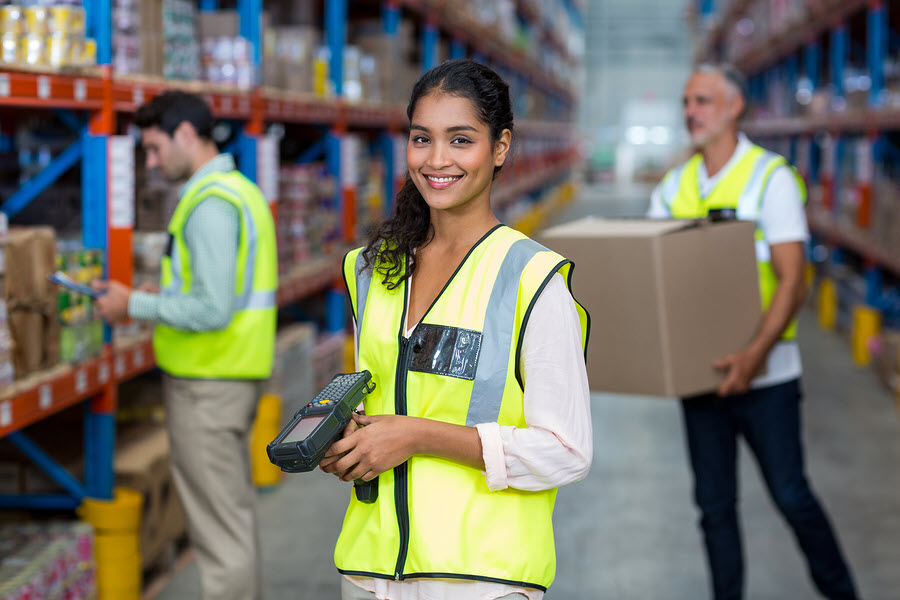
movement. S/he should be observant, diligent, have basic mathematical ability.
S/he should communicate effectively in vernacular language.
Description
Core Skills/Generic
Skills
Core Skills or Generic Skills are a group of skills that are key to learning and
working in today’s world. These skills are typically needed in any work
environment. In the context of the NOS, these include communication related
skills that are applicable to most job roles.
Function
Function is an activity necessary for achieving the key purpose of the sector,
occupation, or area of work, which can be carried out by a person or a group
of persons. Functions are identified through functional analysis and form the
basis of NOS.
Job role Job role defines a unique set of functions that together form a unique
employment opportunity in an organization.
Knowledge and Understanding
Knowledge and understanding are statements which together specify the
technical, generic, professional and organizational specific knowledge that an
individual needs in order to perform to the required standard.
National Occupational
Standards (NOS) NOS are Occupational Standards which apply uniquely in the Indian context
Occupation Occupation is a set of job roles, which perform similar/related set of functions
in an industry.
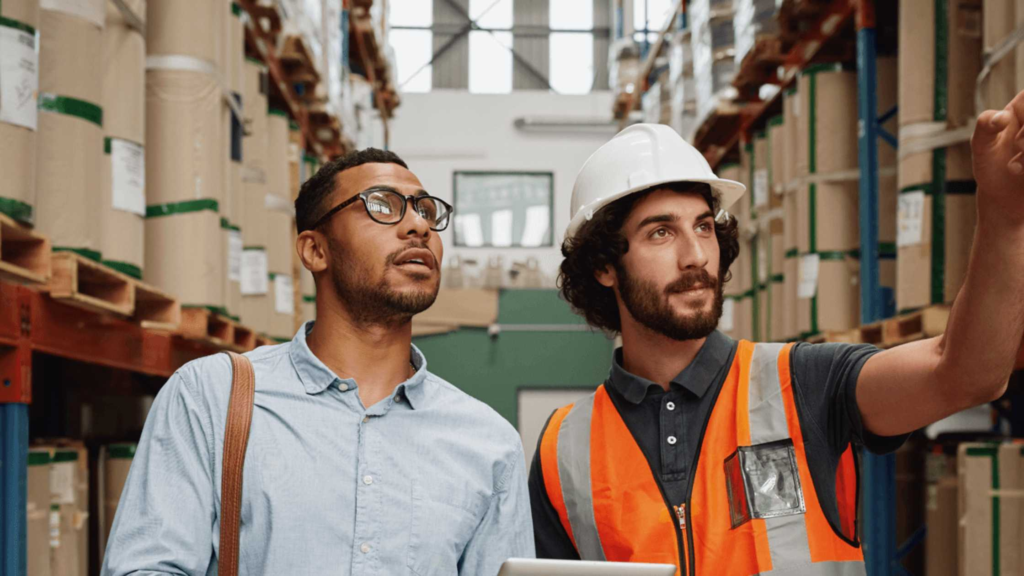
Organizational Context
Organizational Context includes the way the organization is structured and
how it operates, including the extent of operative knowledge managers have
of their relevant areas of responsibility.
Performance Criteria Performance Criteria are statements that together specify the standard of
performance required when carrying out a task.
Qualifications Pack(QP)
Qualifications Pack comprises the set of NOS, together with the educational,
training and other criteria required to perform a job role. A Qualifications
Pack is assigned a unique qualification pack code.
Electives Electives are NOS/set of NOS that are identified by the sector as contributive
to specialization in a job role. There may be multiple electives within a QP for
each specialized job role. Trainees must select at least one elective for the
successful completion of a QP with Electives.
Options Options are NOS/set of NOS that are identified by the sector as additional
skills. There may be multiple options within a QP. It is not mandatory to select
any of the options to complete a QP with Options.
Unit Code Unit code is a unique identifier for an Occupational Standard, which is
denoted by an ‘N’
Unit Title Unit title gives a clear overall statement about what the incumbent should be
able to do.
Qualifications Pack
Code
Qualifications Pack Code is a unique reference code that identifies a
qualifications pack.
Scope Scope is the set of statements specifying the range of variables that an
individual may have to deal with in carrying out the function which have a
critical impact on the quality of performance required.
Sector
Sector is a conglomeration of different business operations having similar
businesses and interests. It may also be defined as a distinct subset of the
economy whose components share similar characteristics and interests.
Sub-Sector Sub-sector is derived from a further breakdown based on the characteristics
and interests of its components.
Sub-functions Sub-functions are sub-activities essential to fulfil the achieving the objectives
of the function.
Technical Knowledge Technical Knowledge is the specific knowledge needed to accomplish specific
designated responsibilities.
Keywords /Terms Description
5S Sort, Set In order, Shine, Standardize and Sustain
BOM Bill of Material
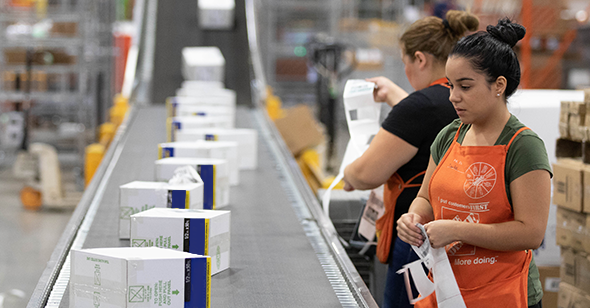
CGST Central Goods and Services Tax
ERP Enterprise resource planning
FIFO First-In, First-Out
FMCG Fast-Moving Consumer Goods
GST Goods and Services Tax
GSTIN GST Identification Number
HR Human Resources
HSN Harmonized System of Nomenclature
IGST Integrated Goods and Services Tax
JIT Just in time
LIFO Last-In, First-Out
MHE Material Handling Equipment
MIS Management Information System
MS Microsoft Office
NPM Non-Production Material
NSQF National Skills Qualifications Framework
OS Occupational Standards
OH&S Occupational Health and Safety
OSHA Occupational Safety and Health Administration
PAN Permanent account number
PPE Personal Protective Equipment
QP Qualifications Pack
RFID Radio frequency identification
SAC Service Accounting Code
SOP Standard Operating Procedures
SGST State Goods and Services Tax
UIN Unique Identification Number
Picking, Packaging, Kitting, Labelling and Binning
Picking, packaging, kitting, labelling, and binning
Description This unit is about performing picking, packing, labeling, kitting and binning operations
at a warehouse
Scope This unit/task covers the following:
• Perform picking
• Perform packing and labeling
• Perform kitting
• Perform binning
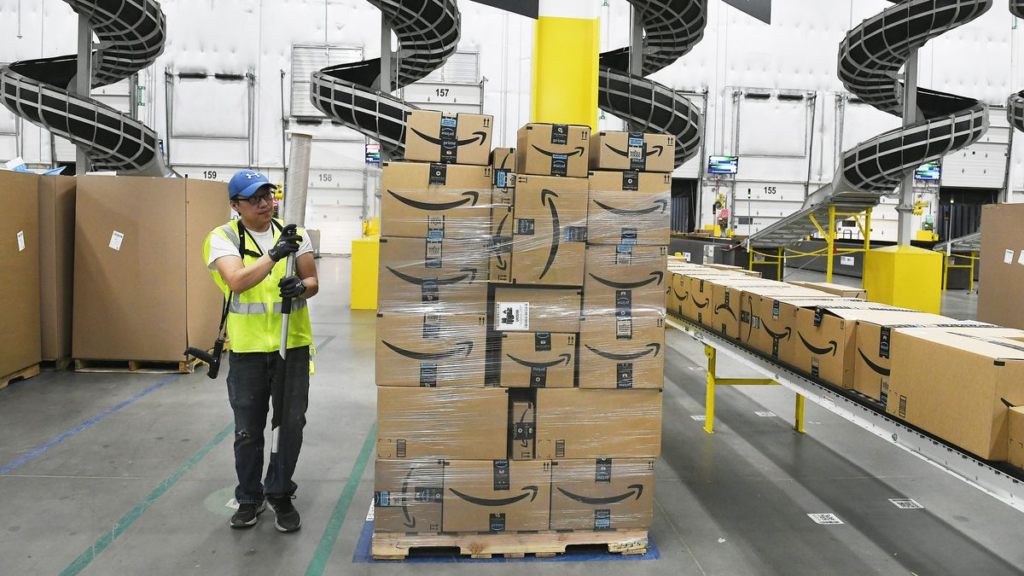
Range: Personal Protective Equipment (PPEs), Material Handling Equipment (MHEs)
like Forklift, Reach stacker, pallet truck, etc., barcode scanner, packing devices,
packing material, markers and stationery, etc.
Performance Criteria(PC) w.r.t. the Scope
Element Performance Criteria
Perform picking
To be competent, the user/individual on the job must be able to:
PC1. obtain picklist from supervisor for picking and arrange MHE equipment, if
required
PC2. locate the physical item in the warehouse
PC3. take the assistance of MHE operator to pick the items from the pallet or racks,
if required
PC4. deliver to packer or binner as per instructions
PC5. submit daily reports to the supervisor
Perform packing and labeling
To be competent, the user/individual on the job must be able to:
PC6. obtain packing list from the supervisor
PC7. collect the packing material and Non-Production Material (NPM) such as labels,
tags, barcodes, etc from the stores
PC8. receive the items for packing from the picker or binner, check for damages and
report on the same to supervisor
PC9. segregate and pack items, label them with bar codes and product tags and seal
the packages
PC10. handover the packed items to binner or loader
PC11. clean the area after packing operations and submit daily reports to the
supervisor
Perform kitting
To be competent, the user/individual on the job must be able to:
PC12. obtain kitting list from supervisor and details of shift schedule for kitting
PC13. use the appropriate PPE based on the product and environment
PC14. check items received for kitting for damages, bar code /product label errors
and report the same to supervisor
PC15. segregate items to be kitted and check Bill of Material (BOM) for any missing
components, and report the same to supervisor
PC16. receive replacement or missing components
PC17. collect required packing cases and sealing material from the packing and
storage supervisor
PC18. kit the items as per BOM, Standard Operating Procedures (SOP) and place it in
the packing case
PC19. seal the packing case and label it with tags and barcodes
PC20. handover kitted items to picker or loader for transport
PC21. clean the area after kitting operation and submit daily reports to supervisor
reporting total kitting done, damages, delays and accidents
Perform binning To be competent, the user/individual on the job must be able to:
PC22.obtain binning instructions for the day from supervisors
PC23. arrange for various equipment and stationery required like bins, bar codes and
product tags
PC24. receive the items for binning, check for damages and report the same to
supervisor
PC25.segregate items that need to be stored in the warehouse and the ones that
need to be shipped in different bins of different geographical regions
PC26. bin the items as per instructions, seal and attach label and bar code
PC27. handover binned items to the picker or loader for transport
PC28. clean the area after binning and submit daily reports to the supervisor
Knowledge and understanding (K)
A. Organizational
context
The individual on the job needs to know and understand:
KA1. organizational procedures and policy on quality, use of PPEs, use of
equipment, MHEs, documentation, etc.
KA2. company’s reporting structure to support and expedite project acivities
KA3. company’s policy and work instructions on quality standards
KA4. importance of the individual’s role in the workflow
KA5. occupational health and safety standards and security procedures to be
followed
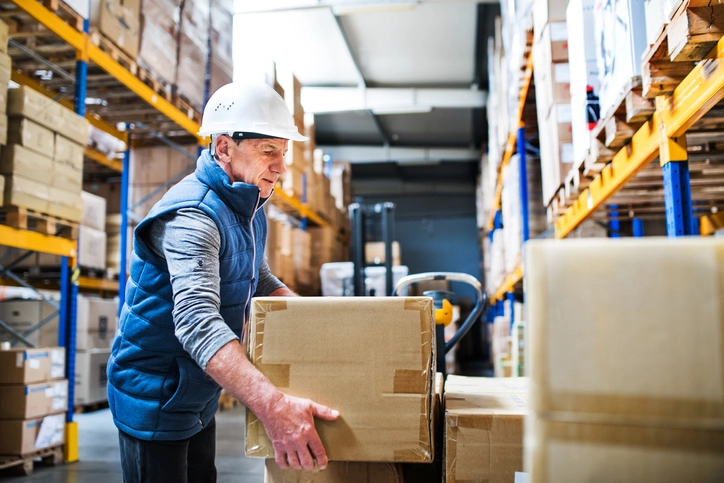
KA6. procedures for dealing with loss or damage to goods
KA7. risk and impact of not following defined work, safety and security procedures
KA8. coding system followed to label items
KA9. Enterprise resource planning (ERP) system of the organization
B. Technical knowledge
The individual on the job needs to know and understand:
KB1. use of computer and data handling devices
KB2. use of different material handling equipment and their uses
KB3. different geographical locations
KB4. types of packing material such as bubble wrap, shrink wrap, corrugated
boxes, beads, etc.
KB5. packing techniques such as boxing, lashing, etc.
KB6. packaging machines and their usage
KB7. product type and corresponding packing process
KB8. country-wise product-wise packaging and labelling requirement
KB9. information from the ERP/ Management Information System (MIS) system,
instruction list
KB10. various escalations regarding resolving and catering to the customer query
KB11. basics of overall process in operations
KB12. different types of goods being handled
KB13. handling requirements for dangerous and special goods, if any
KB14. various types of PPEs and their usage
Skills (S)
A. Core skills/
generic skills
Reading skills
The user/individual on the job needs to know how to read:
SA1. written instructions
SA2. invoicing label and shipment labels
SA3. product tags and labels
Writing skills
The user/individual on the job needs to know how to write:
SA4. damage reports and daily output reports
SA5. daily reports
Oral communication (listening and speaking skills)
The user/individual on the job needs to know how to:
SA6. communicate with supervisors and co-workers
SA7. collect information from supervisors
B. Professional Skills Decision making
The user/individual on the job needs to know how to:
SB1. idenitfy the item as damaged or not
SB2. assess if a problem can be resolved quickly internally or needs to be escalated
SB3. identify acitivities or orders that need to be prioritised as per instructions
Plan and organize
The user/individual on the job needs to know how to:
SB4. plan and estimate the time for each activity
SB5. maintain puntuality
SB6. should respond to the supervisor in a timely manner
SB7. prioritize and execute tasks based on instructions
SB8. be a team player and achieve joint goals
Customer centricity
The user/individual on the job needs to know and understand:
SB9. importance of given timelines
SB10. urgency of priority requests as per the instructions
Picking, Packaging, Kitting, Labelling and Binning
12
The user/individual on the job needs to know how to:
SB11. inform the supervisor regarding delays, issue in doing an activity, etc.
SB12. coordinate and ensure timeliness in receipt and delivery of completed items
Analytical thinking
The user/individual on the job needs to know how to:
SB13. verify the authenticity of the product by looking at the logo, box packaging,
etc.
SB14. analyse and identify the best way to pack an item
Critical thinking
The user/individual on the job needs to know how to:
SB15. check compliance for established norms for weights, package size, of
consignments, etc.
SB16. identify dangerous goods
SB17. focus on task at hand ad complete it without errors and delays
Loading and unloading
Description This unit is about performing loading and unloading of goods at a warehouse
Scope This unit/task covers the following:
• Perform loading and unloading activities
Range: Personal Protective Equipment (PPEs), Material Handling Equipment (MHEs)
like pallet truck (manual and battery operated), etc. barcode scanner, packing
devices, packing material, markers and stationery, etc.
Performance Criteria(PC) w.r.t. the Scope
Element Performance Criteria
Perform loading and
unloading
To be competent, the user/individual on the job must be able to:
PC1. obtain loading and unloading schedule including docking bay and time of
transport arrival from supervisor
PC2. arrange necessary material handling equipment, tools, tackles, chains, and
ropes for loading or unloading
PC3. wear the appropriate PPE required for operations
PC4. check the product to be loaded or unloaded with respect to the order and
report to supervisor, in case of discrepancies
PC5. use the appropriate tools, ropes/chains and secure the product/crate
PC6. operate MHE to load or unload the items from the pallet/ racks/ vehicle as
required
PC7. deliver the unloaded packages to the specified location as per the instructions
PC8. report any breakages, spillages of package or consignment
PC9. move damaged goods to the quarantine area
PC10. park the MHE at the designated parking location
PC11. submit a daily report to the supervisor
Knowledge and understanding (K)
A. Organizational
Context
The individual on the job needs to know and understand:
KA1. organizational procedures and policy on quality, use of PPEs, use of
equipment, MHEs, documentation, etc.
KA2. company’s reporting structure to support and expedite project acivities
KA3. company’s policy and work instructions on quality standards
KA4. importance of the individual’s role in the workflow
KA5. occupational health and safety standards and security procedures to be
followed
KA6. procedures for dealing with loss or damage to goods
KA7. risk and impact of not following defined work, safety and security procedures
KA8. coding system followed to label items
KA9. Enterprise resource planning (ERP) system of the organization
B. Technical knowledge
The individual on the job needs to know and understand:
KB1. use of computer and data handling devices
KB2. use of different MHE and their uses
KB3. operating MHEs
KB4. different geographical locations
KB5. information from the ERP system, instruction list
KB6. various escalations regarding resolving and catering to the customer query
KB7. overall process in operations
KB8. different types of goods being handled
KB9. handling requirements for dangerous and special goods, if any
KB10. various types of PPEs and their usage
Skills (S)
C. Core Skills/
Generic Skills
Reading skills
The user/individual on the job needs to know how to read:
SA1. written instructions
SA2. invoicing label and shipment labels
SA3. product tags and labels
Writing skills
The user/individual on the job needs to know how to write:
SA4. damage reports and daily output reports
SA5. daily reports
Oral communication (listening and speaking skills)
The user/individual on the job needs to know how to:
SA6. communicate with supervisors and co-workers
SA7. collect information from supervisors
D. Professional Skills Decision making
The user/individual on the job needs to know how to:
SB1. idenitfy the item as damaged or not
SB2. decide if a problem can be resolved quickly internally or needs to be escalated
SB3. identify acitivities or orders that need to be prioritised as per instructions
Plan and organize
The user/individual on the job needs to know how to:
SB4. plan and estimate the time for each activity
SB5. maintain puntuality
SB6. should respond to the supervisor in a timely manner
SB7. prioritize and execute tasks based on instructions
SB8. be a team player and achieve joint goals
Customer centricity
The user/individual on the job needs to know and understand:
SB9. importance of customer timelines
SB10. urgency of customers as per the instructions
Problem solving
The user/individual on the job needs to know how to:
SB11. inform the supervisor regarding delays, issue in doing an activity, etc.
SB12. coordinate and ensure timeliness in receipt and delivery of completed items
Analytical thinking
The user/individual on the job needs to know how to:
SB13. verify the authenticity of the product by looking at the logo, box packaging,
etc.
Critical thinking
The user/individual on the job needs to know how to:
SB14. check compliance of consignments for established norms for weights,
package size, etc.
SB15. identify dangerous goods
SB16. suggest improvement in loading and stacking methods to increase efficiency
and space utilization
SB17. focus on task at hand ad complete it without errors and delays