Ship and Yard Planning Supervisor (1 years diploma)
Ship and Yard Planning Supervisor click here
Brief Job Description: The individual allocates and supervises resources for
storage and movement of cargo in port terminal yard, while ensuring compliance
to statutory requirements/documentation to ensure smooth operations.
Qualifications Pack for Ship and yard planning supervisor
Electives
Elective 1: Dry Bulk Cargo
This unit is about supervision of cargo handling and storage operations for dry
bulk cargo
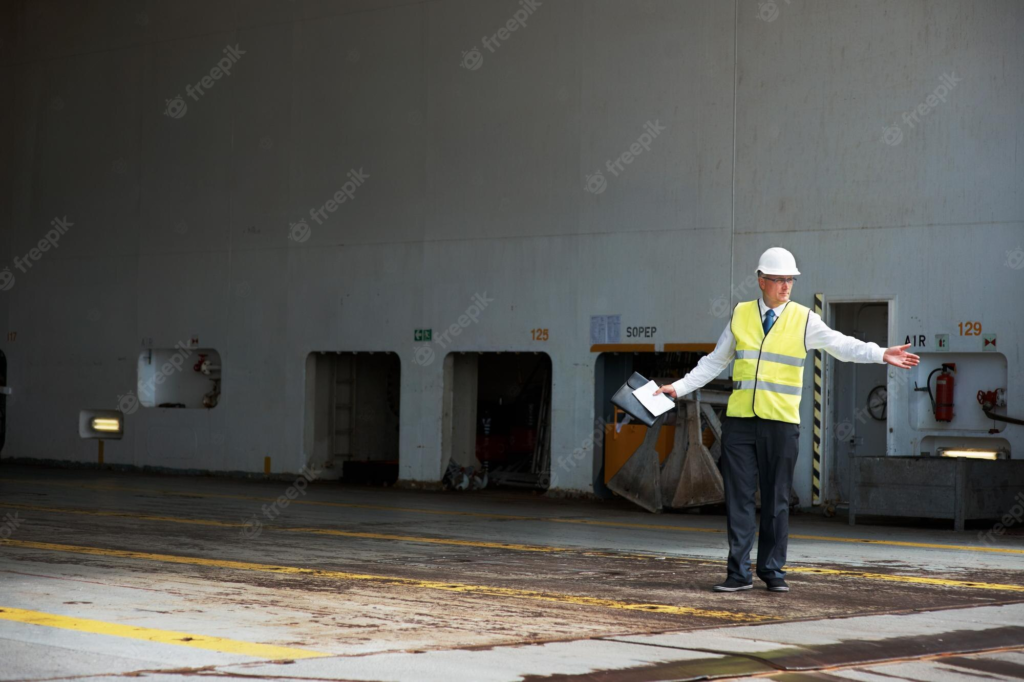
Elective 2: Containerized Cargo
This unit is about supervision of cargo handling and storage operations for
containerized cargo including reefer cargo
Options
Option 1: Agency Operations
This unit is about developing relations with key accounts and developing new
business with existing and new customers
Option 2: Container Tracking and Vessel Planning
This unit is about reporting on position of different containers across the globe
and making berthing and terminal plans for vessels docking for the week
Personal Attributes:
The job holder should plan and budget for activities. S/he should have
digital/computer skills and mathematical aptitude to estimate yard space
requirement, and quantity estimation. S/he should have English and Vernacular
language proficiency, demonstrable in spoken, written and oral communication.
hip and yard planning supervisor
Role Description
The individual would be responsible for cargo planning, storage
and movement in the yard at port terminal for optimal
utilisation. S/He will also be responsible for resource allocation
and required statutory documentation to ensure smooth
operations.
NSQF
Minimum Educational Qualifications
Maximum Educational Qualifications
5
Graduate (or) Diploma/ Class XII with relevant experience (or) Class X with relevant experience
Prerequisite License or Training Not Applicable for License. Should be proficient and cleared Level 4
Minimum Job Entry Age 21 years
Experience
Diploma/ Class XII with 3 years of experience in Warehouse and
EXIM/ Ports, ICD& CFS operations (or)
Class X with 5 years of experience in Warehouse and EXIM/ Ports, ICD
& CFS operations
Description
Core Skills/Generic
Skills
Core Skills or Generic Skills are a group of skills that are key to learning and
working in today’s world. These skills are typically needed in any work
environment. In the context of the NOS, these include communication related
skills that are applicable to most job roles.
Function
Function is an activity necessary for achieving the key purpose of the sector,
occupation, or area of work, which can be carried out by a person or a group
of persons. Functions are identified through functional analysis and form the
basis of NOS.
Job role Job role defines a unique set of functions that together form a unique
employment opportunity in an organization.
Knowledge and Understanding
Knowledge and Understanding are statements which together specify the
technical, generic, professional and organizational specific knowledge that an
individual needs in order to perform to the required standard.
National Occupational
Standards (NOS) NOS are Occupational Standards which apply uniquely in the Indian context
Electives
Electives are NOS/set of NOS that are identified by the sector as contributive
to specialization in a job role. There may be multiple electives within a QP for
each specialized job role. Trainees must select atleast one elective for the
successful completion of a QP with Electives
Options
Options are NOS/set of NOS that are identified by the sector as additional
skills. there may be multiple options within a QP. It is not mandatory to select
any of the options to complete a QP with Options.
Unit Code Unit code is a unique identifier for an Occupational Standard, which is
denoted by an ‘N’
Unit Title Unit title gives a clear overall statement about what the incumbent should be
able to do.
Occupation Occupation is a set of job roles, which perform similar/related set of functions
in an industry.
Organisational Context
Organisational Context includes the way the organization is structured and
how it operates, including the extent of operative knowledge managers have
of their relevant areas of responsibility.
Performance Criteria Performance Criteria are statements that together specify the standard of
performance required when carrying out a task.
Qualifications
Pack(QP)
Qualifications Pack comprises the set of NOS, together with the educational,
training and other criteria required to perform a job role. A Qualifications
Pack is assigned a unique qualification pack code.
Qualifications Pack
Code
Qualifications Pack Code is a unique reference code that identifies a
qualifications pack.
Scope Scope is the set of statements specifying the range of variables that an
individual may have to deal with in carrying out the function which have a critical impact on the quality of performance required.
Sector
Sector is a conglomeration of different business operations having similar
businesses and interests. It may also be defined as a distinct subset of the
economy whose components share similar characteristics and interests.
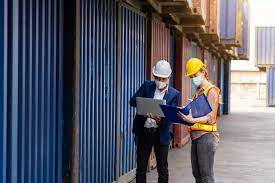
Sub-Sector Sub-sector is derived from a further breakdown based on the characteristics
and interests of its components.
Sub-functions Sub-functions are sub-activities essential to fulfil the achieving the objectives
of the function.
Technical Knowledge Technical Knowledge is the specific knowledge needed to accomplish specific
designated responsibilities.
Description
CFS Container Freight Station
DG Directorate General
ERP Enterprise Resource Planning
EXIM Export Import
GPS Global Positioning System
GSU Grab Ship Unloader
HAZCHEM Hazardous Chemicals
HR Human Resources
ICD Inland Container Depot
IMDG International Maritime Dangerous Goods
IMSBC International Maritime Solid Bulk Cargo
JIT Just In Time
MHE Material Handling Equipment
NSQF National Skills Qualifications Framework
OSHA Occupational Safety and Health Administration
OH&S Occupational Health and Safety
OS Occupational Standards
PGA Partner Government Agencies
PPE Personal Protective Equipment
QP Qualifications Pack
RFID Radio-Frequency Identification
SLA Service Level Agreement
SOP Standard Operating Procedures
TAT Turn Around Time
VHF Very High Frequency
Allocate resources and streamline operations at yard
Description This unit is about allocating resources for cargo movement, supervision of operations
and streamlining operations at yard
Scope This unit/task covers the following:
• Prepare work plan and allocate resources
• Monitor daily operations
• Yard Inspection
• Resolve escalated issues
Range: Stationery, Radio-Frequency Identification (RFID) scanner, bar code scanner,
plastic bags, markers, Personal Protective Equipment (PPEs), Enterprise Resource
Planning (ERP), computer, printers, Global Positioning System (GPS) tracker,
Material Handling Equipment (MHEs), etc.
Performance Criteria(PC) w.r.t. the scope
Element Performance Criteria
Prepare work plan
and allocate
resources
To be competent, the user/ individual must be able to:
PC1. obtain details of vessel docking plans, cargo and container movement plans,
etc.
PC2. develop daily work plan factoring in priority cases, time bound requirements,
special handling requirements, etc.
PC3. get the work plan approved by the yard manager or Container Freight Station
(CFS)/ Inland Container Depot (ICD) manager and allocate tasks to
subordinates
PC4. budget and allocate the requisite MHE for tasks at hand
Monitor daily
operations
To be competent, the user/individual on the job must be able to:
PC5. inspect yard for markings/demarcation, storage and cleanliness as per safety
norms
PC6. monitor cargo loading, unloading and movement operations
PC7. engage resources in alternate operation when there is a delay of planned
operations
PC8. allocate additional and ad-hoc manpower and equipment during exigency
PC9. escalate issues regarding MHE operations, transporter delays, vessel delays,
accidents, damages, etc. to manager
PC10. provide corrective and preventive action plans based on accident and damage
reports
PC11. liaise with port officials, customs officials and external stakeholders
Yard inspection To be competent, the user/ individual must be able to:
PC12. conduct periodic inspection of the yard for cleanliness, usage of PPEs and adherence to SOP and regulations
PC13. ensure cargo bays are clearly marked and segregated, containers and cargo
are stored as per prescribed norms
PC14. check for parking and positioning of equipment as per SOP
PC15. ensure all necessary precautions for storage of hazardous cargo are complied
with and emergency services are available
PC16. submit inspection report highlighting any deviation from SOP
Resolve escalated
issues
To be competent, the user/ individual must be able to:
PC17. review escalated issues and identify root cause for providing corrective action
PC18. provide technical guidance to the team for execution
PC19. escalate the issues to manager when external or additional help is required
PC20. coordinate with other departments, transporters, freight operators, port
authorities, shipping companies and others to resolve escalations if required
Knowledge and understanding (K)
A. Organizational
context
(Knowledge of the
company /
organization and
its processes)
The individual on the job needs to know and understand:
KA1. organizational and security procedures
KA2. documentation and reporting as per organization’s mandate
KA3. escalation matrix for reporting identified problems
KA4. risk and impact of not following defined procedures/work instructions
KA5. coding system followed to label cargo
KA6. IT system and ERP system of the organization
B. Technical
knowledge
The individual on the job needs to know and understand:
KB1. yard operations and its technicalities
KB2. different type of cranes and MHEs – their capacities, constraints and usage
KB3. use of rope, flags and other manual equipment
KB4. vessel layout and loading and unloading activities
KB5. different type of vessels, cargo, container sizes and their handling
KB6. handling of hazardous and non-hazardous cargo – International Maritime
Dangerous Goods (IMDG) code
KB7. stuffing and de-stuffing norms with respect to different cargo and its special
characteristics
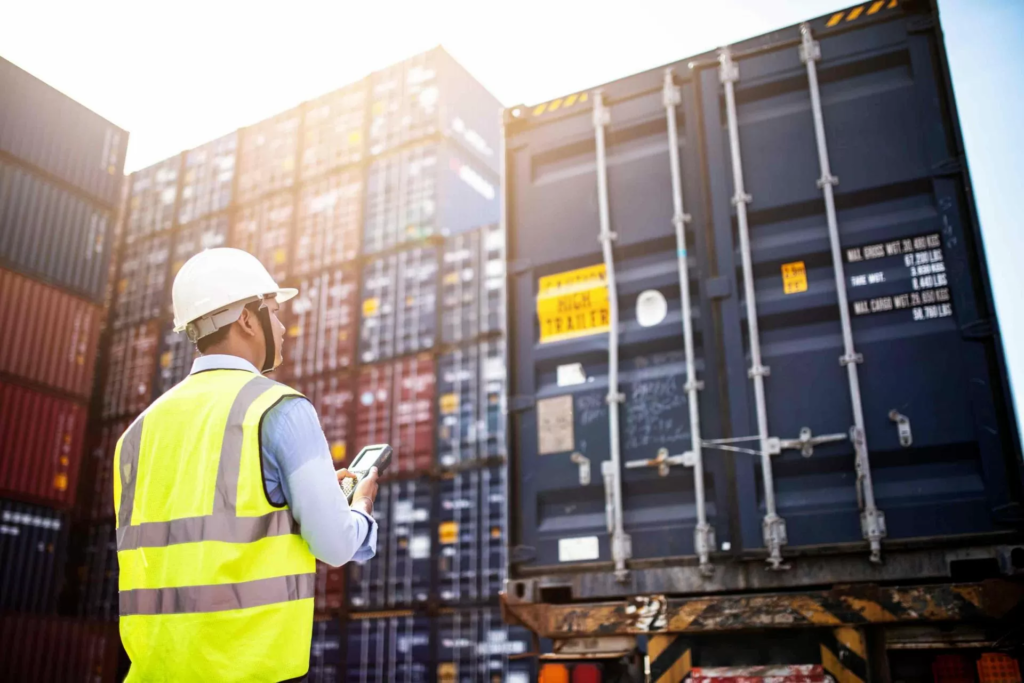
Skills (S)
A. Core skills/
generic skills
Reading skills
The user/individual on the job needs to know how to read:
SA1. written instructions
SA2. shiping manifest, Bill of lading shipping bills and related documents
SA3. ERP and computer generated reports
SA4. cargo stowage plans and vessel plans
SA5. Standard Operating Procedures (SOPs) and safety regulation manuals
Writing skills
The user/individual on the job needs to know how to write:
SA6. work-orders and instructions
SA7. checklist of activities, delays, undelivered items, contacts, etc
SA8. daily reports
Oral communication (listening and speaking skills)
The user/individual on the job needs to know how to:
SA9. communicate with customers, fireght operators, transporters, shipping
companies, other supervisors and port authorities
SA10. communicate with cargo equipment operators and ground staff over Very High
Frequency (VHF) radio
SA11. guide cargo handlers for smooth operations
B. Professional skills Decision making
The user/individual on the job needs to know how to:
SB1. decide on required workforce and equipment for performing a particular task
SB2. assess the environmental condition and type of cargo to assess if it is safe for
operations
SB3. resolve a problem quickly internally
SB4. prioritise shipments
SB5. decide on deployment of alternate resources when required
Plan and organize
The user/individual on the job needs to know how to:
SB6. plan and estimate the co-ordination required for resolving a querry.
SB7. maintain punctuality
SB8. respond to the client in a timely manner
SB9. prioritize and execute tasks based on client requirements
SB10.make work plans and resource allocation plans
SB11.make checks on execution of work plans
SB12. be a team player and achieve joint goals
Customer centricity
The user/individual on the job needs to know how to:
SB13. adhere to the customer timelines
SB14. address the urgency regarding shipments and activities
Problem solving
The user/individual on the job needs to know how to:
SB15. make adjustment to working requirements for difficult weathers and
hazardous goods
SB16. identify trends/common causes for delays, damages, etc.
SB17. co-ordinate and handle major issues with different departments
SB18. identify bottlenecks and operational problems and suggest remedial action
Analytical thinking
The user/individual on the job needs to know how to:
SB19. assess the resource requirement for a particular task at hand
SB20. assess and prepare for backup resources in case of delays
SB21. plan for cargo movement so that the resources and stroage space is optimally
utilised
Critical thinking
The user/individual on the job needs to know and understand how to:
SB22. resolve issues in a qucik and cost effective manner
SB23. develop work plans factoring in external factors
SB24. Check that all security measures and safety protocals are followed at all times
Yard planning and cargo handling
Description This unit is about yard planning for cargo storage, supervision of movement of cargo
and preparing reports
Scope This unit/task covers the following:
• Review yard utilisation and plan for storage requirement
• Prepare for cargo movement
• Supervise cargo movement
• Report and Document
Range: Stationery, Standard Operating Procedures (SOP), Radio-Frequency
Identification (RFID) scanner, bar code scanner, markers, Personal Protective
Equipment (PPEs), Enterprise Resource Planning (ERP), computer, display board,
printer, Material Handling Equipment (MHEs), etc.
Performance Criteria(PC) w.r.t. the scope
Element Performance Criteria
Review yard
utilisation and plan
for storage
requirement
To be competent, the user/ individual must be able to:
PC1. check yard space utilization data in terms of open and closed yards, dry bulk
cargo vs container, and assess available storage capacity
PC2. review ageing of cargo and containers in yard, identify reasons for delay, and
enable timely movement
PC3. identify and finalise bays for storage of incoming cargo considering the
various demarcations and precautions to be taken particularly for hazardous
and dry bulk cargo
PC4. plan for yard traffic and material movement routes considering terminal
layout, container and cargo type, and available equipment
PC5. prepare goods storage plans based on vessel berthing plan and get it
approved by the terminal manager
PC6. escalate issues to terminal manager if required
Prepare for cargo
movement
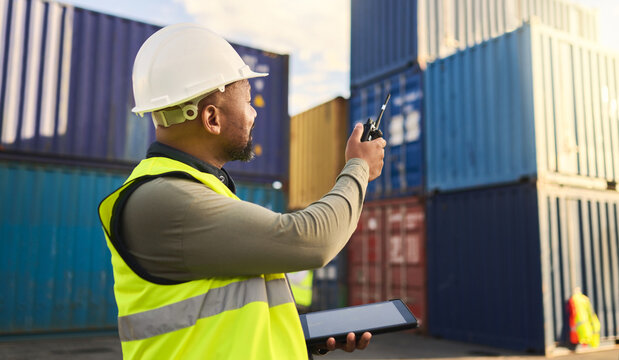
To be competent, the user/ individual must be able to:
PC7. obtain vessel information related to docking schedule, berth, bays and
containers to be unloaded/ loaded
PC8. obtain information regarding movement of containers/ cargo from port
terminals to Container Freight Station/ Inland Container Depot (CFS/ ICD) or
client
PC9. communicate and finalise cargo movement plan with lifting supervisors,
vessel supervisors, cargo equipment handlers, and manual cargo handlers
PC10. ensure that all equipment and workforce are ready for operations at the time
of vessel docking / transport arrival
PC11. ensure all necessary precautions are taken and adequate PPEs are used
Supervise cargo
movement
To be competent, the user/ individual must be able to:
PC12. coordinate with vessel docking supervisor/ transport supervisor and vessel
officer and get a go-ahead for cargo/ container loading/ unloading
PC13. coordinate with cargo surveyor for receiving ‘safe and secured’ go-ahead
before loading/ unloading
PC14. address the queries of shipping lines and agents regarding cargo operations
and storage
PC15. check that all cargo handling activities executed are as per schedule and SOP
PC16. document damages to cargo/ container during loading/ unloading
PC17. provide guidance and resolve/escalate any issues faced in loading/ unloading
PC18. check that all cargo is stored at the planned/allocated storage location in the
yard
Report and
Document
To be competent, the user/ individual must be able to:
PC19. obtain ‘safe and secured’ go-ahead from the cargo surveyor upon completion
of loading/ unloading activities
PC20. collect counter signature from transporter for actuals received or dispatched
PC21. check consignments received against order and delivery documentation to
confirm that the quality, quantity and condition of the cargo is acceptable,
identifying and referring any discrepancies
PC22. maintain records relating to the receipt / storage / despatch of cargo,
ensuring that these are up to date and complete
PC23. check if receipt and delivery are documented in ERP
PC24. prepare daily report highlighting the cargo storage and movement, plan vs
actual performance, cargo ageing, details of accidents and damages if any
Knowledge and understanding (K)
A. Organizational
context
(Knowledge of the
company /
organization and
its processes)
The individual on the job needs to know and understand:
KA1. organizational procedures
KA2. documentation and reporting as per organization’s mandate
KA3. security procedures to be followed
KA4. escalation matrix for reporting identified problems
KA5. risk and impact of not following defined procedures/work instructions
KA6. coding system followed to label cargo
KA7. IT system and ERP system of the organization
B. Technical
knowledge
The individual on the job needs to know and understand:
KB1. basics of operations in a port terminal, ICD and CFS
KB2. use of various cargo handling equipment
KB3. use of rope, flags and other manual equipment
KB4. vessel layout and loading and unloading activities
KB5. procedures of tank cleaning, cargo movement
KB6. requirements regarding handling of cargo
KB7. different type of vessels and cargo and container sizes
KB8. different type of cranes and MHEs – their capacities, constraints and usage
KB9. handling of hazardous and non-hazardous cargo – – International Maritime
Dangerous Goods (IMDG) code
KB10. marking of material and people movement areas
KB11. stuffing and de-stuffing norms with respect to different cargo
KB12. special characteristics and handling requirements of shipments, if any
Skills (S)
C. Core skills/
generic skills
Reading skills
The user/individual on the job needs to know how to read:
SA1. written instructions
SA2. shiping manifest, Bill of lading shipping bills and related documents
SA3. ERP and computer generated reports
SA4. cargo stowage plans and vessel plans
SA5. SOPs and safety regulation manuals
Writing skills
The user/individual on the job needs to know how to write:
SA6. work-orders and instructions
SA7. checklist of activities, delays, undelivered items, contacts, etc
SA8. daily reports
Oral communication (listening and speaking skills)
The user/individual on the job needs to know how to:
SA9. communicate with customers, fireght operators, transporters, shipping
companies, other supervisors and port authorities
SA10. communicate with cargo equipment operators and ground staff over VHF
radio
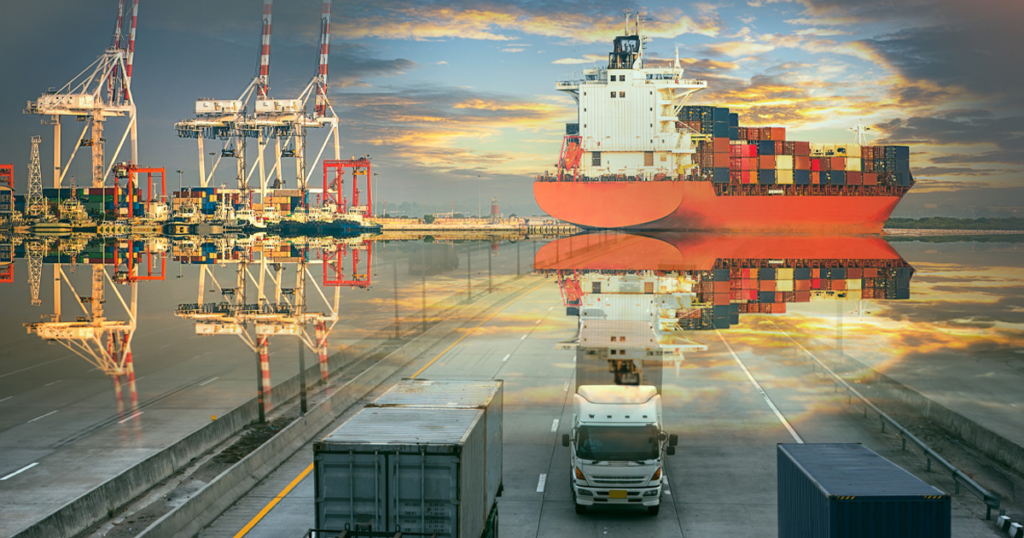
SA11. guide cargo handlers for smooth operations
D. Professional skills Decision making
The user/individual on the job needs to know how to:
SB1. decide on required workforce and equipment for performing a particular task
SB2. assess the environmental condition and type of cargo to assess if it is safe for
operations
SB3. resolve a problem quickly internally
SB4. prioritise shipments
SB5. decide on deployment of alternate resources when required
Plan and organize
The user/individual on the job needs to know how to:
SB6. plan and estimate the co-ordination required for resolving a querry.
SB7. maintain punctuality
SB8. respond to the client in a timely manner
SB9. prioritize and execute tasks based on client requirements
SB10. make work plans and resource allocation plans
SB11. make checks on execution of work plans
SB12. be a team player and achieve joint goals
Customer centricity
The user/individual on the job needs to know how to:
SB13. adhere to the customer timelines
SB14. address the urgency regarding shipments and activities
Problem solving
The user/individual on the job needs to know how to:
SB15. make adjustment to working requirements for difficult weathers and
hazardous goods
SB16. identify trends/common causes for delays, damages, etc.
SB17. co-ordinate and handle major issues with different departments
SB18. identify bottlenecks and operational problems and suggest remedial action
Analytical thinking
The user/individual on the job needs to know how to:
SB19. assess the resource requirement for a particular task at hand
SB20. assess and prepare for backup resources in case of delays
SB21. plan for cargo movement so that the resources and stroage space is optimally
utilised
Critical thinking
The user/individual on the job needs to know and understand how to:
SB22. resolve issues in a qucik and cost effective manner
SB23. develop work plans factoring in external factors
SB24. check that all security measures and safety protocals are followed at all times
Handle hazardous goods
Description The unit is about handling hazardous cargo at port terminals, CFS and ICDs
Scope This unit/task covers the following:
• Identify and segregate hazardous cargo
• Oversee that adequate precuations are taken while handling hazardous goods
• Inspect and review storage of hazardous cargo
Range: Stationery, Standard Operating Procedures (SOP), Radio-Frequency
Identification (RFID) scanner, bar code scanner, markers, Personal Protective
Equipment (PPEs), Enterprise Resource Planning (ERP), computer, display board,
printer, Material Handling Equipment (MHEs), etc.
Performance Criteria(PC) w.r.t. the scope
Element Performance Criteria
Identify and
segregate hazardous
goods
To be competent, the user/ individual must be able to:
PC1. read and interpret different cargo labels associated with different class and
types of hazardous goods
PC2. check for permissible limits and available documentation for hazardous goods
as per approvals and acceptable specifications
PC3. check IMDG code to identify the precautions and permissible limits for
handling
PC4. ensure that the port and yard terminal if the port is equipped to handle the
identified class of hazardous goods
PC5. check if all the necessary precautions, PPEs and emergency response teams
are in position prior to loading/unloading of cargo
PC6. check that the allocated storage bay in the yard is adequately separated and
precautions with respect to heat, light, temperature control, etc. are taken
PC7. provide instructions for segregation of hazard goods as per classification
PC8. use separate teams for handling different classes of hazardous goods
Oversee that
adequate
precautions are taken
while handling
hazardous goods
To be competent, the user/ individual must be able to:
PC9. check if appropriate PPEs, MHEs and other equipment are being used to
prevent contamination or exposure
PC10. check if all PPEs and equipment are functional and contamination proof
PC11. ensure all precautions are taken as per SOP while handling hazardous cargo
PC12. confirm emergency response action with the emergency team and cargo
handling team prior to operations
PC13. inspect containers for damages, leakage, exposure and labels
PC14. check if cargo movement via conveyors, dump trucks is spillage free
PC15. ensure clear and obstacle free movement of cargo from vessel to yard and yard to transport
PC16. ensure that all required precautions and segregation for cargo storage are
undertaken
PC17. report closure of exercise highlighting handling losses, storage location and
coordinates, etc.
Inspect and review
storage of hazardous
goods
To be competent, the user/ individual must be able to:
PC18. periodically inspect yard space to check if adequate segregation and
precautions are taken for storage of hazardous goods
PC19. report to manager in case of any leakage, damages, exceptions in handling
precautions and segregation
PC20. document and file inspection reports
Knowledge and understanding (K)
A. Organizational
context
(Knowledge of the
company /
organization and
its processes)
The individual on the job needs to know and understand:
KA1. organizational procedures
KA2. documentation and reporting as per organization’s mandate
KA3. security procedures to be followed
KA4. escalation matrix for reporting identified problems
KA5. risk and impact of not following defined procedures/work instructions
KA6. coding system followed to label cargo
KA7. IT system and ERP system of the organization
B. Technical
knowledge
The individual on the job needs to know and understand:
KB1. basics of operations in a port terminal, Inland Container Depot (ICD) and
Container Freight Station (CFS)
KB2. different type of vessels and cargo and container sizes
KB3. vessel layout and loading and unloading activities
KB4. use of rope, flags and other manual equipment
KB5. different type of cranes and MHEs – their capacities, constraints and usage
KB6. identifying dangerous goods/hazardous substances using labels, International
Maritime Dangerous Goods (IMDG) Code markings, Hazardous Chemicals
(HAZCHEM) signs and other relevant identification criteria
KB7. handling of hazardous and non-hazardous cargo
KB8. identifying job and site hazards, and planning work to minimise risks
KB9. selecting and using the right PPE equipment as per the industry standards
KB10. procedures of tank cleaning, cargo movement
KB11. marking of material and people movement areas
KB12. stuffing and de-stuffing norms with respect to different cargo
KB13. special characteristics and handling requirements of shipments, if any
KB14. usage of electronic communication equipment
Skills (S)
C. Core skills/ Reading skills generic skills
The user/individual on the job needs to know how to read:
SA1. written instructions
SA2. shiping manifest, Bill of lading shipping bills and related documents
SA3. ERP and computer generated reports
SA4. cargo stowage plans and vessel plans
SA5. SOPs and safety regulation manuals
Writing skills
The user/individual on the job needs to know how to write:
SA6. work-orders and instructions
SA7. checklist of activities, delays, undelivered items, contacts, etc
SA8. daily reports
Oral communication (listening and speaking skills)
The user/individual on the job needs to know how to:
SA9. communicate with customers, freight operators, transporters, shipping
companies, other supervisors and port authorities
SA10. communicate with cargo equipment operators and ground staff over VHF radio
SA11. guide cargo handlers for smooth operations
D. Professional skills Decision making
The user/individual on the job needs to know how to:
SB1. decide on required workforce and equipment for performing a particular task
SB2. assess the environmental condition and type of cargo to assess if it is safe for
operations
SB3. resolve a problem quickly internally
SB4. prioritise shipments
SB5. decide on deployment of alternate resources when required
Plan and organize
The user/individual on the job needs to know how to:
SB6. plan and co-ordinate resolution of queries
SB7. maintain punctuality
SB8. respond to the client in a timely manner
SB9. prioritize and execute tasks based on client requirements
SB10. make work plans and resource allocation plans
SB11. make checks on execution of work plans
SB12. be a team player and achieve joint goals
Customer centricity
The user/individual on the job needs to know how to:
SB13. adhere to the customer timelines
SB14. address the urgency regarding shipments and activities
Problem solving
The user/individual on the job needs to know how to:
SB15. make adjustment to working requirements for difficult weathers and hazardous
goods
SB16. identify trends/common causes for delays, damages, etc.
SB17. co-ordinate and handle major issues with different departments
SB18. identify bottlenecks and operational problems and suggest remedial action
Analytical thinking
The user/individual on the job needs to know how to:
SB19. assess the resource requirement for a particular task at hand
SB20. assess and prepare for backup resources in case of delays
SB21. plan for cargo movement so that the resources and storage space is optimally
utilised
Critical thinking
The user/individual on the job needs to know and understand how to:
SB22. resolve issues in a quick and cost-effective manner
SB23. develop work plans factoring in external factors
SB24. check that all security measures and safety protocals are followed at all times
Maintain and monitor integrity and ethics in operations
Description This unit is about maintaining integrity, ensuring data security, and following
professional and ethical practices
Scope This unit/task covers the following:
• Maintain integrity and ensure data security
• Professional and ethical practice
• Ensure regulatory compliance
Range: Standard Operating Procedures (SOP), worksheets, computer, projector,
printer, display board and markers
Performance Criteria(PC) w.r.t. the scope
Element Performance Criteria
Maintain integrity
ensuring data
security
To be competent, the user/ individual must be able to:
PC1. refrain from indulging in corrupt practices
PC2. avoid using company’s funds, property or resources for undertaking personal
activities
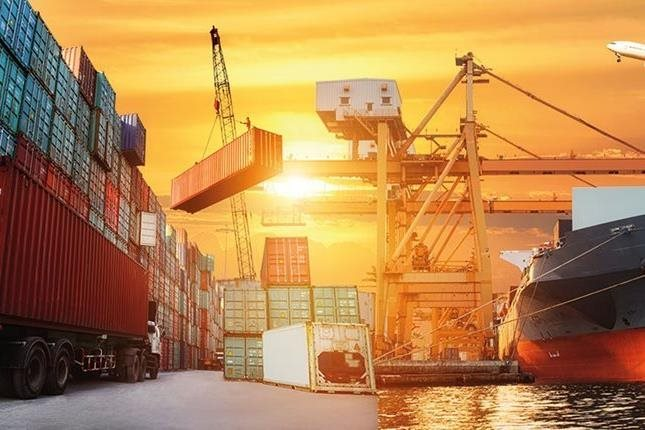
PC3. protect customer’s information and ensure it is not misused
PC4. protect data and information related to business or commercial decisions
Professional and
ethical practice
To be competent, the user/ individual must be able to:
PC5. avoid acceptance of cash or kind from vendors for support or contract
negotiations
PC6. demonstrate and practice ethics in day-to-day processes and dealings with
customers and colleagues
PC7. avoid nepotism
PC8. consult supervisor or senior management when in situations that may require
differentiating between ethical and unethical
PC9. report promptly all violations of code of ethics
PC10. dress up and conduct in a professional manner
PC11. communicate with clients and stakeholders in a soft and polite manner
PC12. follow etiquettes in accordance to the place
Ensure regulatory
compliance
To be competent, the user/ individual must be able to:
PC13. check for regulatory documentation and compliances for the shop floor as per
information from the supervisor
PC14. perform activities considering the regulatory requirements
PC15. use PPEs in accordance to regulatory requirements
PC16. identify the different types of dangerous goods and handling methodologies
PC17. follow the SOP for handling of different types of dangerous goods
PC18. consult supervisor or senior management when in situations that may require
differentiating between ethical and unethical
PC19. promptly report all regulatory violations
Knowledge and understanding (K)
A. Organizational
context
(Knowledge of the
company /
organization and
its processes)
The user/individual on the job needs to know and understand:
KA1. company’s policies on use of language
KA2. company’s Human Resources policies
KA3. company’s code of ethics and business
KA4. company’s whistle blower policy
KA5. company’s rules related to sexual harassment
KA6. company’s reporting structure
KA7. company’s documentation policy
B. Technical
knowledge
The user/individual on the job needs to know and understand:
KB1. principles of code of ethics and business ethics
KB2. different regulations and acts that are applicable for the sub-sector and
logistics sector as a whole
KB3. understand the documentary compliance required for different type of
products
Skills (S)
A. Core skills/
generic skills
Reading skills
The individual on the job needs to know how to read:
SA1. policy documents and work related documents
SA2. emails letters and communications
SA3. acts and regulations
Writing skills
The individual on the job needs to know and understand how to write:
SA4. instructions, communications to internal staff
SA5. emails and letters
SA6. reports
Oral communication (listening and speaking skills)
The individual on the job needs to know how to:
SA7. interact with internal and external stakeholders
SA8. communicate with peers and subordinates
B. Professional skills
Decision making
The individual on the job needs to know how to:
SB1. take appropriate action in a vulnerable situation
SB2. identify breaches and take necessary actions
SB3. identify documentary requirement for a specific product or regulation and
take necessary action
Plan and organize
The individual on the job needs to know how to:
SB4. plan and organise steps/ actions as per company’s guidelines, if any violation of code of ethics is noticed in the company
SB5. plan and organise training sessions, sensitization sessions for work force
SB6. plan review meetings to monitor compliance with ethics and regulations
Customer centricity
The individual on the job needs to know how to:
SB7. prevent company and customer information leakage
Problem Solving
The individual on the job needs to know how to:
SB8. provide proper advice or guidance to colleagues to deal with sensitive issue
SB9. suggest solutions to supervisors and workers when in an ethical dilemma
SB10. identify conflict of interests and take necessary actions
Analytical thinking
The individual on the job needs to know how to:
SB11. review reports to identify common trends of defaults
SB12. conduct review to analyse the reasons for default
Critical thinking
The individual on the job needs to know how to:
SB13. check that all regulatory compliances are adhered to
SB14. check that any unethical behaviour gets captured before a damage or
negative impact happens
Follow and monitor health, safety and security procedures
Description This OS unit is about ensuring compliance with health, safety and security procedures
at the workplace.
Scope This unit/task covers the following:
• Follow health, safety and security procedures
• Ensure compliance to health, safety and security
Range: Personal Protective Equipment (PPE), Material Handling Equipment (MHE),
instructional material, safety guidelines, safety signs, computer, projector etc.
Performance Criteria(PC) w.r.t. the scope
Element Performance Criteria
Follow health, safety
and security
procedures
To be competent, the user/ individual must be able to:
PC1. make note of all safety processes in different location (cargo loading area,
ramp operation area, etc.) with reference to area of operation
PC2. wear all personal protective equipment (PPE) such as goggles, ear plugs,
helmet, mask, shoes, etc. as applicable in the cargo movement area
PC3. follow standard driving practice to ensure safety of life and material
PC4. follow organizational protocol to deploy action in case of signs of any
emergency situation or accident or breach of safety
PC5. undertake periodical preventive health check ups
PC6. follow necessary standard operating procedures (SOP) and precautions
while handling dangerous and hazardous goods
PC7. follow security procedures like green gate in port, customs area, factory
security, etc.
PC8. comply with data safety regulations of the organisation
PC9. follow standard safety procedures while handling hazardous / fragile cargo
and walk only on the designated pathway
Ensure compliance to
health, safety and
security
To be competent, the user/ individual must be able to:
PC10. recognise unsafe conditions and safety practices at the workplace and
report it to concerned authority
PC11. inspect the activity area and equipment for appropriate and safe condition
PC12. check if stacking is done at defined height and is not on the walk way
PC13. check if walk way is free from grease/ oil
PC14. check if emergency fire alarms, water sprinklers and smoke detectors are
installed at all places
PC15. participate in fire drills
PC16. check if standard material handling procedure are being followed
PC17. check if hold ladders, platforms and hand rails to be in a sound and safe
condition
PC18. check if all the safety and security related tags, labels and signage are
placed in the cargo
PC19. check if loading instrument is certified and operational
PC20. implement 5S at workplace
PC21. check if cargo has passed security checks and report in case of any violation
Knowledge and understanding (K)
A. Organizational
context
(Knowledge of the
company /
organization and
its processes)
The individual on the job needs to know and understand:
KA1. health, safety and security policies and procedures
KA2. Special instructions for hazardous cargo handling
KA3. defined standard operating procedures
KA4. risk and impact of not following defined procedures/work instructions with
reference to health, safety and security operations
KA5. escalation matrix for reporting identified problem
B. Technical
knowledge
The individual on the job needs to know and understand:
KB1. basics of Occupational Safety and Health Administration (OSHA)
KB2. 5S implementation and practice
KB3. necessary security procedures for airport, customs area, etc.
KB4. tools and equipment for material handling
KB5. standard material handling procedures while handling cargo
KB6. safety and security signage and their functions
KB7. knowledge of security tags, labels and signage
KB8. handling procedure for hazardous / fragile cargo
KB9. security procedures for dangerous / hazardous goods
KB10. Different PPE, their usage and purpose
KB11. safe driving techniques
Skills (S)
A. Core skills/
generic skills
Reading skills
The user/individual on the job needs to know how to read:
SA1. various procedures and standards related to health, safety and security
SA2. various documents related to security and movement of cargo
Writing skills
The user/individual on the job needs to know how to:
SA3. fill forms related to health, safety and security procedures
Oral communication (listening and speaking skills)
The user/individual on the job needs to know and understand how to:
SA4. communicate clearly with colleagues regarding safety procedures
SA5. share experience and provide guidance to peers
B. Professional skills Decision making
The user/individual on the job needs to know how to:
SB1. make a judgment as to what actions to be taken to avoid any damage /accident to personal health / cargo handled
SB2. act objectively, rather than impulsively or emotionally when faced with
difficult/stressful or emotional situations
Plan and organize
The user/individual on the job needs to know how to:
SB3. plan clearance of cargo in manner that it does hamper the safety of the cargo
and the loader/unloader
SB4. prioritize and execute tasks within the schedule time limits
SB5. Plan emergency drills, fire drills and inspections
Customer centricity
The user/individual on the job needs to know and understand how to:
SB6. ensure safe and secure movement of packages, cargos etc.
Problem solving
The user/individual on the job needs to know and understand how to:
SB7. identify any threats on personal health, safety, security, etc. and take
appropriate actions
SB8. identify risks at the workplace and address them
Analytical thinking
The user/individual on the job needs to know and understand how to:
SB9. analyse past mistakes and address them to avoid mishap in the future
Critical thinking
The user/individual on the job needs to know and understand how to:
SB10. ensure right safety measures and procedures are in place
Handle dry bulk cargo
Description This unit is about supervision of dry bulk cargo loading/unloading and movement
Scope This unit/task covers the following:
• Loading/unloading of dry bulk cargo
Range: Personal Protective Equipment (PPE), Material Handling Equipment (MHE),
instructional material, safety guidelines, safety signs, computer, projector etc.
Performance Criteria(PC) w.r.t. the scope
Element Performance Criteria
Loading/unloading
dry bulk cargo
To be competent, the user/ individual must be able to:
PC1. obtain details of incoming cargo from port/ shipper into the Container Freight
Station (CFS), Inland Container Depot (ICD) as per the cargo plan and allocate
resources
PC2. check the International Maritime Solid Bulk Cargo (IMSBC) code of the item to
be loaded/unloaded is presented in the documentation and the vessel/yard
has the appropriate safety systems in place
PC3. identify and finalise bays for storage of incoming cargo considering the
various demarcations and precautions to be taken based on cargo type
PC4. discuss, finalise and communicate cargo movement plan with workforce and
ensure all equipment are ready for operations at the time of vessel
docking/transport arrival
PC5. review the pre-operative checklist to ensure all equipment are functional and
get a “OK” report from all operators and handlers
PC6. review that the unloading area has been prepared for receipt of material and
necessary precautions and PPEs have been taken
PC7. supervise unloading/loading of dry bulk cargo using Grab Ship Unloader (GSU)
crane, conveyor belts etc.
PC8. ensure minimum spillage and wastage of dry bulk cargo during transfer
operations and monitor the same
PC9. check for compliance to IMDG, Directorate General (DG) shipping and other
material handling guidelines while unloading hazardous/dangerous cargo
PC10. ensure the yard space is cleaned post loading/unloading of cargo
PC11. oversee movement of cargo from port terminal, CFS via rail and road lines and
export via vessels