Foreman – Reinforcement ( 6 month course)
Foreman – Reinforcement click here
Brief Job Description: Foreman – Reinforcement is responsible for reading and
interpreting drawings, calculate quantity of material required for reinforcement work,
arrange and allocate resources, instruct proper sequence of work, ensure execution of

work as per plans, specifications and working drawings. The individual should possess
sound technical knowledge, should be able to monitor and maintain safe and quality
working practices.
Personal Attributes: This job role requires the individual to be physically and mentally
strong enough to oversee the reinforcement work at a construction site. The individual
should be having strong organizational, interpersonal and communication skills, along
with comprehensive technical knowledge of reinforcement work and ability to
supervise construction crew.
Description
Sector Sector is conglomeration of different business operations having similar
business and interests. It may also be defined as a distinct subset of the
economy whose components share similar characteristics and interests.
Sub‐Sector Sub‐Sector is derived from a further breakdown based on the characteristics
and interests of its components
Occupation Occupation is a set of job roles, which perform similar/related set of
functions in an industry
Job role Job role defines a unique set of functions that together form a unique
employment opportunity in an organization.
Occupational Standards
(OS)
OS specify the standards of performance an individual must achieve when
carrying out a function in the workplace, together with the knowledge and
understanding they need to meet the standard consistently. Occupational
Standards are applicable both in the Indian contexts.
Performance Criteria Performance Criteria are statements that together specify the standard of
performance required when carrying out a task.
Qualifications Pack (QP) Qualifications Pack comprises the set of OS, together with the educational,
training and other criteria required to perform a job role. A Qualification Pack
is assigned a unique qualification pack code.
Qualification Pack Code Qualification Pack Code is a unique reference code that identifies a
qualifications pack.
National Occupational
Standards (NOS) NOS are Occupational Standards which apply uniquely in the Indian context.
Scope Scope is the set of statements specifying the range of variables that an
individual may have to deal with in carrying out the function which have a
critical impact on the quality of performance required.
Knowledge and Understanding
Knowledge and Understanding are statements which together specify the
technical, generic, professional and organizational specific knowledge that an
individual needs in order to perform to the required standard
Organizational Context Organizational Context includes the way the organization is structured and
how it operates, including the extent of operative knowledge managers have
of their relevant areas of responsibility.
Technical Knowledge Technical Knowledge is the specific knowledge needed to accomplish specific
designated responsibilities.
Core Skills / Generic Skills Core Skills or Generic Skills are a group of skills that are key to learning and
working in today’s world. These skills are typically needed in any work
environment. In the context of the OS, these include communication related
skills that are applicable to most job roles.
Keywords /Terms Description
CON Construction
NSQF National Skill Qualifications Framework
QP Qualification Pack
OS Occupational Standards
TBD To Be Decided
Read drawings, specification, standards and prepare Bar Bending Schedule
Description
This unit describes the skills and knowledge required to read drawings specification,
standards and prepare Bar Bending schedule
Scope
The scope covers the following:
Read & interpret drawings, BBS , specifications and standards for bar bending
and steel fixing operations
Prepare Bar Bending Schedule
Performance Criteria (PC) w.r.t. the Scope
Element Performance Criteria

Read & interpret drawings, BBS , specifications and standards for bar bending and steel fixing operations
To be competent, the user / individual on the job must be able to:
PC1. read & interpret details from R.C.C drawing and other relevant drawings
PC2. read & interpret details from Bar bending schedule
PC3. read and understand specification and standards provided for fabrication
and fixing of reinforcement
PC4. read and understand all specification provided in the relevant drawing
PC5. read and understand schedule provided for completion of reinforcement work
PC6. read method statement for execution of reinforcement work
PC7. read, understand & follow manufactures specification for fixing of mechanical coupler
PC8. read, understand & follow manufactures specification for operation of power
tools and CNC machine for cutting and bending
PC9. carryout calculation of BOQ quantity
Prepare Bar Bending Schedule
PC10. read & co-relate R.C.C detail drawing with respect to general arrangement
drawing
PC11. prepare the BBS for cutting and bending of rebars and plan fixing of
reinforcement
PC12. ensure BBS includes all specifications of rebars for R.C.C work including
diameter, shape, cutting length, number, length of each bent and straight
portion, angle, and description of rebars
PC13. prepare schedules from given part of BBS, interpreting codes and key shapes
PC14. ensure that prepared BBS is checked and approved by respective engineer in
charge
Knowledge and Understanding (K)
A. Organizational
Context
(Knowledge of
the company /
organization and
its processes)
The user/individual on the job needs to know and understand:
KA1. standard practices for reinforcement works
KA2. safety rules and regulations for handling and storing relevant tools,
equipment and materials for reinforcement works
KA3. personal protection including the use of related safety gears & equipment
KA4. service request procedures for tools, materials and equipment
KA5. statutory compliance requirement related to workmen engagement
B. Technical Knowledge
The user/individual on the job needs to know and understand:
KB1. reading and understanding of civil structural drawings
KB2. principles involved in reading and understanding various related drawings
KB3. use of schedules including applicable code shapes and associated calculations
KB4. reading of general arrangement drawing
KB5. reading of RCC detail drawing
KB6. correlation of drawings
KB7. implementation of BBS
KB8. knowledge of basic IS/International Codes for Reinforcement
KB9. simplified sketch preparation from the drawing
KB10.how to read plan, elevation and sectional drawing
KB11.basic principal of measurement, arithmetic and geometric calculations
KB12.terminology used in reinforcement works
KB13.linear conversion of units
KB14.units of measurement
KB15. components, materials and tools used in reinforcement works
KB16.insertion and fixing procedure for various types of structure
KB17.units weight of reinforcement steel of different diameter
KB18.electrical safety of power tools for reinforcement works
KB19. computer basics, auto-cad software application for 2D drawings
Skills (S)
A. Core Skills/
Generic Skills
Writing Skills
The user/ individual on the job needs to know and understand how to:
SA1. write at least two language, preferably the local language at the site and basic
English
SA2. provide clear and simple instructions, details & sketches to sub-ordinate
SA3. record and document daily productivity report, daily labour attendance &
details regarding work done
SA4. prepare basic status updates for the superiors in the prescribed format
Reading Skills
The user/ individual on the job needs to know and understand how to:
SA5. read one or more language, preferably the local language at the site
SA6. read drawing, reinforcement specification and standards
SA7. read key documents including quality standards, standards working methods
& applicable tolerance limits
SA8. read manufacturer instruction and specification for using power tools for
reinforcement works
SA9. read various, sign boards, safety rules and safety tags , instruction related to
exit routes during emergency at the workplace
Oral Communication (Listening and Speaking skills)
The user/ individual on the job needs to know and understand how to:
SA10. speak in one or more language, preferably one of the local language at site
SA11. listen and follow instructions clearly given by the superior
SA12. provide clear instructions to subordinates for task as per work plan, time
schedule and quality
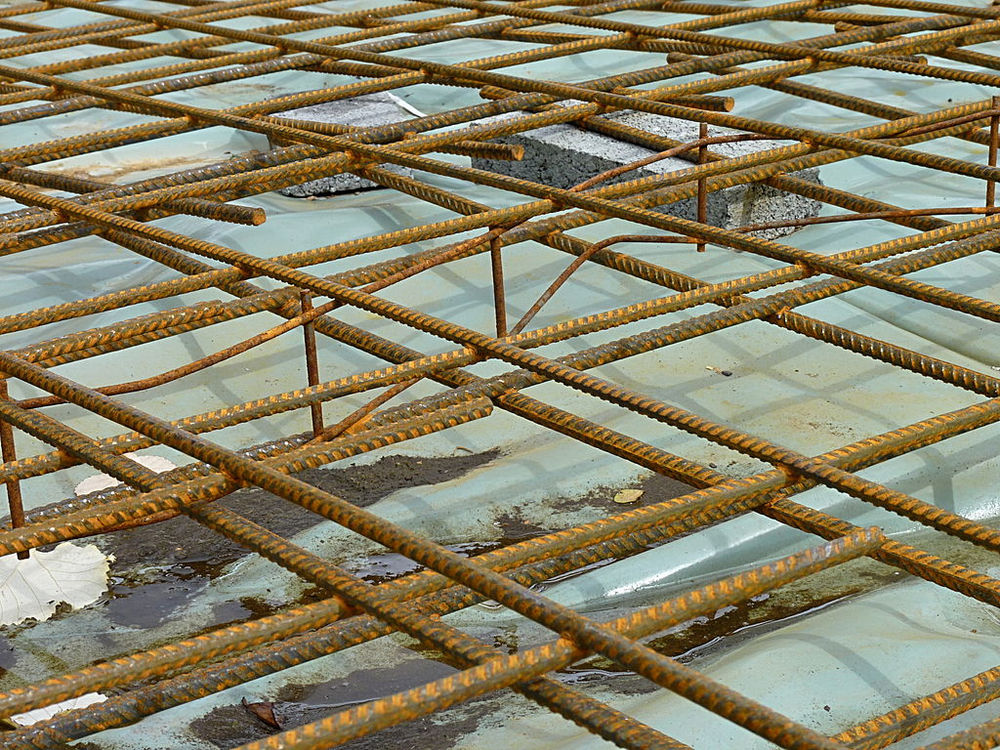
B. Professional Skills
Decision Making
The user/individual on the job needs to know and understand how to:
SB1. estimate required material and resources for work
SB2. decide on insertion and fixing of rebars
Plan and Organize
The user/individual on the job needs to know and understand how to:
SB3. plan work & organize required resource in coordination with team members
and superiors
SB4. plan work targets, allocate time schedule to subordinates and organize
complete of task within allocated time
Customer centricity
The user/individual on the job needs to know and understand how to:
SB5. ensure completion of work as per agreed time schedule and quality
Problem solving
The user/individual on the job needs to know and understand how to:
SB6. resolve any conflict within the team
SB7. resolve / clarify and clear works pending due to any hindrances
Analytical Thinking
The user/individual on the job needs to know and understand how to:
SB8. assess quantity of resources required for day work
SB9. optimize resources
SB10. minimize wastages
Critical Thinking
The user/individual on the job needs to know and understand how to:
SB11. assess complexity of the tasks, provide guidance, demonstrate corrective
action as per requirement
SB12. identify and assess how violation of any safety norms may lead to accidents
SB13. correlate the sequence of fixing reinforcement with inserts, cast in fixings etc.
Monitor reinforcement works at reinforcement yard
Description This unit describes the knowledge and the skills required to carry out monitoring
works at reinforcement yard.
Scope
The scope covers the following:
Carry out reinforcement and related monitoring works at reinforcement yard
Performance Criteria (PC) w.r.t. the Scope
Element Performance Criteria
Carry out reinforcement and related monitoring works at reinforcement yard
To be competent, the user / individual on the job must be able to:
PC1. inspect incoming / outgoing material at reinforcement yard
PC2. carry out weighing of steel reinforcement before unloading at site in
coordination with the stores
PC3. visually check for quality of reinforcement steel against rusting
PC4. ensure appropriate protection measures rebars
PC5. ensure standard practices for storing and stacking of reinforcement steel at the yard
PC6. monitor all rebars cutting and bending activity at yard
PC7. monitor threading activity ensure protection of threaded end part with plastic caps
PC8. understand manufacturer specification/instruction for use of CNC machine
PC9. understand manufacturer specification/instruction for use of power tools for cutting and bending
PC10. perform basic troubleshooting for operation of CNC machine
PC11. ensure bundling/tagging and stacking of cut & bent bars as per bar marking the BBS
PC12. ensure to prevent distortion of fabricated bars during handling
PC13. ensure proper use of slings, belts, hook for lifting of rebars using crane
PC14. ensure maximum use of cut length & minimize wastage
PC15. segregate prime length of steel rods based on diameter of bar
PC16. coordinate with seniors and stores, to ensure smooth operations of work at
reinforcement yard
PC17. coordinate with site to meet demand requirement at site on priority basis
Knowledge and Understanding (K)
A. Organizational
Context
(Knowledge of
the company /
organization and its processes)
The user/individual on the job needs to know and understand:
KA1. standard practices for reinforcement works
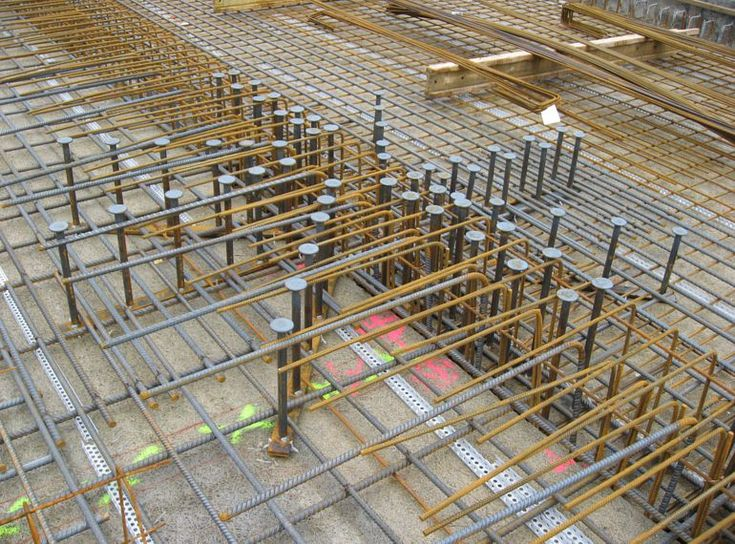
KA2. safety rules and regulations for handling and storing relevant tools,
equipment and materials for reinforcement works
KA3. personal protection including the use of related safety gears & equipments
KA4. service request procedures for tools, materials and equipments
KA5. statutory compliance requirement related to workmen engagement
B. Technical
Knowledge
The user/individual on the job needs to know and understand:
KB1. standard procedures for stacking of reinforcement
KB2. basic knowledge of various types of steel such as Mild Steel , TOR steel & TMT
steel
KB3. method to prevent reinforcement against rusting, and weathering effect
KB4. bundling and tagging of rebars
KB5. visual quality check for reinforcement
KB6. segregation of reinforcement on basis of cutting length and dia to minimize
wastage
KB7. safety rules and regulations at site
KB8. use of PPE during operations of power tools /CNC machines
KB9. service request procedures for tools, materials, equipment
KB10.schematic drawings, sketches and BBS
KB11. how to operate hand tools, power tools, CNC machine for their respective
applications in reinforcement work
KB12. types of mechanical couplers and manufacturer’s instructions for their
installations
KB13.shapes and codes provided in the BBS
KB14. computer basics auto-cad software application for 2D drawing
Skills (S)
A. Core Skills/ Generic Skills Writing Skills
The user/ individual on the job needs to know and understand how to:
SA1. write at least two language, preferably the local language at the site and basic English
SA2. provide clear and simple instructions, details & sketches to sub-ordinates
SA3. record and document daily productivity report, daily labour attendance &
details regarding work done
SA4. prepare basic status updates for the superiors in the prescribed format
Reading Skills
The user/ individual on the job needs to know and understand how to:
SA5. read one or more language, preferably the local language at the site
SA6. read drawing, Bar bending schedule, specification and standards related to
reinforcement works
SA7. read key documents including quality standards, standards working methods
& applicable tolerance limits
SA8. read manufacturer instruction and specification for using power tools for
reinforcement works
SA9. read various, sign boards, safety rules and safety tags , instruction related to
exit routes during emergency at the workplace
Oral Communication (Listening and Speaking skills)
The user/ individual on the job needs to know and understand how to:
SA10. speak in one or more language, preferably one of the local language at site
SA11. listen and follow instructions clearly given by the superior
SA12. provide clear instructions to subordinates for completion of task as per work
plan, time schedule and quality
B. Professional
Skills
Decision Making
The user/individual on the job needs to know and understand how to:
SB1. decide whether the work place is safe for working and also relevant task is not
creating hazardous condition for others
SB2. decide on manpower, tools , material and equipment for relevant work
SB3. decide alternate course of action in case of hindrance to work
SB4. decide on prioritizing activity to meet demand at site
Plan and Organize
The user/individual on the job needs to know and understand how to:
SB5. plan work & organize required resource in coordination with team members
and superior
SB6. plan work targets, schedules for subordinates for completion of task as per
work plan, time schedule and quality
Customer centricity
The user/individual on the job needs to know and understand how to:
SB7. ensure completion of work as per agreed time schedule and quality
Problem solving
The user/individual on the job needs to know and understand how to:
SB8. suggest remedial action to workers for making corrections
SB9. resolve any conflict within the team
SB10. carry out basic troubleshooting for operation of CNC machine

Analytical Thinking
The user/individual on the job needs to know and understand how to:
SB11. reconcile material consumption
SB12. assess quantity of resources required for day work
SB13. optimize resources
SB14. minimize wastages
SB15. make use of available cut piece of rebars for chairs, spacer, hanger bar to minimize wastage
SB16. segregate prime length of steel rods based on diameter of bar
Critical Thinking
The user/individual on the job needs to know and understand how to:
SB17. assess complexity of the tasks and carry out corrective action as per
requirement
SB18. identify and assess how violation of any safety norms may lead to accidents
Ensure fabrication placing and fixing of rebars as per drawing, bar bending schedule and specification
Description
This OS unit describes the skills and required to Ensure fabrication placing and fixing of
rebars as per drawing, bar bending schedule and specification.
Scope
This unit/task covers the following:
Ensure completion of surveying, marking and other preparatory arrangement
Extract work as per approved prepared BBS and drawing
Performance Criteria (PC) w.r.t. the Scope
Element Performance Criteria
Ensure completion of surveying, marking and preparatory arrangement
To be competent, the user / individual on the job must be able to:
PC1. ensure survey works are complete so as to provide required level & reference
points for reinforcement work
PC2. check and ensure that all relevant marking is complete as per drawing
PC3. check and ensure that cutting, filling, levelling and compaction of earth if
required prior to commencement of work
PC4. ensure workplace is clear of construction debris and unwanted material
PC5. ensure guard rails, kerb boards and safety nets are in place
PC6. ensure all tools, tackles, consumables, materials and equipments are available
before commencement of work
PC7. ensure scaffolding is complete as per required / specified heights /
requirements, method, load carrying capacity, etc.
PC8. ensure working platforms and access stairs are safe for working
Extract work as per approved prepared BBS and drawing
PC9. check and ensure only approved BBS is used for execution of reinforcement work
PC10. make use of already available cut steel rods to minimize wastage
PC11. plan sequence of insertion and fixing of rebars for different types of structures
PC12. correlate the sequence of reinforcement placing with fixing of inserts, sleeves,
conduits and anchors
PC13. ensure completion of work as per agreed time schedule and quality
PC14. maintain productivity report for executed work
Knowledge and Understanding (K)
A. Organizational Context (Knowledge of the company / organization and its processes)
The user/individual on the job needs to know and understand:
KA1. standard practices for reinforcement works
KA2. safety rules and regulations for handling and storing relevant tools,
equipment and materials for reinforcement works
KA3. personal protection including the use of related safety gears & equipment
KA4. service request procedures for tools, materials and equipments
KA5. statutory compliance requirement related to workmen engagement
B. Technical Knowledge
The user/individual on the job needs to know and understand:
KB1. service request procedures for tools, materials, consumables and equipments
KB2. sequence of inserting bars to fix reinforcement for various types of structures
KB3. reinforcement patterns for any special structures / patterns
KB4. lap length required for rebars based on diameter
KB5. application of anchor grouting material
KB6. allowance of hook length
KB7. how to calculate number & spacing of rebar in case of different diameter rebar used
KB8. importance about providing cover block
KB9. importance of lap length & staggering of reinforcement
KB10.types and optimum use of binding wire
KB11. common terminology used in reinforcement works
KB12. corrective measure for reinforcement
KB13.method & fixing of mechanical coupler
KB14.method to prevent reinforcement from rust
KB15.max allowable wastage of rebars
KB16.basic reconciliation of reinforcement
KB17.rolling marking of reinforcement
KB18.units of measurement
KB19. conversion of units
KB20.basic of geometry
KB21.unit weight of rebars of different diameter
KB22. computer basics auto-cad software application for 2D drawing
Skills (S)
A. Core Skills/ Generic Skills Writing Skills
The user/ individual on the job needs to know and understand how to:
SA1. write at least two language, preferably the local language at the site and basic English
SA2. provide clear and simple instructions, details & sketches to sub-ordinate
SA3. record and document daily productivity report, daily labour attendance &
details regarding work done
SA4. prepare basic status updates for the superiors in the prescribed format
Reading Skills
The user/ individual on the job needs to know and understand how to:
SA5. read one or more language, preferably the local language at the site
SA6. read drawing, Bar bending schedule, specification and standards related to reinforcement works
SA7. read key documents including quality standards, standards working methods
& applicable tolerance limits
SA8. read manufacturer instruction and specification for using power tools for
reinforcement works
SA9. read various, sign boards, safety rules and safety tags , instruction related to
exit routes during emergency at the workplace
Oral Communication (Listening and Speaking skills)
The user/ individual on the job needs to know and understand how to:
SA10. speak in one or more language, preferably one of the local language at site
SA11. listen and follow instructions clearly given by the superior
SA12. provide clear instructions to subordinates for completion of task as per work
plan, time schedule and quality
B. Professional Skills
Decision Making
The user/individual on the job needs to know and understand how to:
SB1. decide whether the work place is safe for working and also relevant task is not
creating hazardous condition for others

SB2. decide on prioritizing activity to meet site requirement
SB3. decide on completion of preceding activity for further course of action
SB4. decide on use of cut piece length of rebar for different purpose
SB5. decide on manpower, tools , material and equipment for relevant work
SB6. decide alternate course of action in case of hindrance to work
Plan and Organize
The user/individual on the job needs to know and understand how to:
SB7. plan work & organize required resource in coordination with team members and superior
SB8. plan work targets, schedules for subordinates for completion of task as per
work plan, with allocated time schedule and to quality desired
Customer centricity
The user/individual on the job needs to know and understand how to:
SB9. ensure completion of work as per agreed time schedule and quality
Problem solving
The user/individual on the job needs to know and understand how to:
SB10.suggest remedial action to workers for making corrections if required
SB11.resolve problem related to insertion & fixing process for complex structure
SB12. provide solution for replacement of one dia bar with other if required dia of
bar is not available
SB13.resolve any conflict within the team
SB14. carry out basic troubleshooting for operation of CNC machine
Analytical Thinking
The user/individual on the job needs to know and understand how to:
SB15.reconcile material consumption
SB16. assess quantity of resources required for day work
SB17. optimize resources
SB18. minimize wastages
SB19. make use of available cut piece of rebars for chairs, spacer, hanger bar to
minimize wastage
SB20. provide solution for replacement of one dia bar with other if required dia of
bar is not available
Critical Thinking
The user/individual on the job needs to know and understand how to:
SB21. assess complexity of the tasks and carry out corrective action as per
requirement
SB22. identify and assess how violation of any safety norms may lead to accidents
Inspect and check the quality of reinforcement work.
Description
This OS unit describes the skills and knowledge required to Inspect and check the
quality of reinforcement work.
Scope
This unit/task covers the following:
Inspect and check the quality of reinforcement work.
Inspect and check quality of mechanical connections of rebar.
Inspect and check the quality of pre-fabricated reinforcement cage & erection
process
Performance Criteria (PC) w.r.t. the Scope
Element Performance Criteria Inspect and check the quality of reinforcement work.
To be competent, the user / individual on the job must be able to:
PC1. check & ensure marking of rebars for spacing before commencement of work
PC2. check for bend, cutting length before fabrication & placing of reinforcement
PC3. check for visual quality & length of binding wire used for tying of
reinforcement
PC4. check reinforcement is free from rust before fabrication
PC5. describe sequence for fixing of reinforcement
PC6. ensure cutting of bars as per appropriate markings
PC7. ensure uniform spacing between the bars, stirrups, hooks, etc. as per BBS
drawing
PC8. ensure more than 50% of splicing is avoided at a location
PC9. check location and position of reinforcement and fix ties to reinforcement as
per requirement
PC10. ensure use of spacers, cover blocks, hanger bars, chairs as per specification
PC11. point out errors to workers and suggest remedial action and ensure repair
work is done as instructed
PC12. check and ensure correct ties used for tying of reinforcement
PC13. point out errors to workers, suggest & demonstrate remedial action / repair
work and ensure corrective action is taken
Inspect and check quality of mechanical connections of rebar.
PC14. ensure that appropriate type of mechanical couplers are installed while fixing reinforcement
PC15. ensure that process followed for installing mechanical coupler is as per manufacturer’s instruction manual
PC16. check that mechanical connections have been appropriately tightened and as per requirement
PC17. check that necessary protectors are in place to prevent damage to the threaded bar ends PC18. point out errors to workers, suggest & demonstrate remedial action / repair
work and ensure corrective action is taken
Inspect and check the quality of prefabricated reinforcement cage & erection process
PC19. check & ensure appropriate method is used for lifting & lowering of
reinforcement cage
PC20. check & ensure prefabricated reinforcement cage is properly aligned & positioned
PC21. ensure rebars, cast-in items, corrugated sleeve pipes, recesses, lifting hooks
and inserts are correctly positioned and properly secured, within specified tolerance levels
PC22. ensure that the joints and edges of the mould, bolts, stoppers, tie rods, side
props and rubber seal are intact and properly secured
PC23. check for stiffening of cage before lifting for stacking/erection
PC24. ensure insertion/attaching of inserts to the cage including special cover blocks
PC25. ensure preparation & usage of reference frames/jig for accurate fabrication
PC26. point out errors to workers, suggest & demonstrate remedial action / repair
work and ensure corrective action is taken
Knowledge and Understanding (K)
A. Organizational Context (Knowledge of the company / organization and its processes)
The user/individual on the job needs to know and understand:
KA1. standard practices for reinforcement works
KA2. safety rules and regulations for handling and storing relevant tools,
equipment and materials for reinforcement works
KA3. personal protection including the use of related safety gears & equipments
KA4. service request procedures for tools, materials and equipments
KA5. statutory compliance requirement related to workmen engagement
B. Technical Knowledge
The user/individual on the job needs to know and understand:
KB1. standard procedure for reinforcement works
KB2. Bar Bending Schedule, relevant drawings, sketches and BBS
KB3. precautions and measures that may be required while checking
reinforcement work
KB4. tolerance limits for various types of reinforcement works as per
Indian/International codes
KB5. importance of reinforcement in precast RCC works
KB6. types of mechanical couplers and manufacturer’s instructions for their
installations
KB7. operation of hand tools, power tools, CNC machine for their respective
applications in reinforcement work
KB8. reinforcement insertion procedures for special structures like arches, domes, etc.
KB9. safety rules and regulations at site
KB10.PPE for steel fixing and bar bending work KB11. computer basics auto-cad software application for 2D drawings
Skills (S)
A. Core Skills/ Generic Skills Writing Skills
The user/ individual on the job needs to know and understand how to:
SA1. write at least two language, preferably the local language at the site and basic English
SA2. provide clear and simple instructions, details & sketches to sub-ordinate
SA3. record and document daily productivity report, daily labour attendance &
details regarding work done
SA4. prepare basic status updates for the superiors in the prescribed format
Reading Skills
The user/ individual on the job needs to know and understand how to:
SA5. read one or more language, preferably the local language at the site
SA6. read drawing, Bar bending schedule, specification and standards related to
reinforcement works
SA7. read key documents including quality standards, standards working methods
& applicable tolerance limits
SA8. read manufacturer instruction and specification for using power tools for
reinforcement works SA9. read various, sign boards, safety rules and safety tags , instruction related to
exit routes during emergency at the workplace
Oral Communication (Listening and Speaking skills)
The user/ individual on the job needs to know and understand how to:
SA10. speak in one or more language, preferably one of the local language at site
SA11. listen and follow instructions clearly given by the superior
SA12. provide clear instructions to subordinates for completion of task as per work
plan, time schedule and quality
B. Professional Skills
Decision Making
The user/individual on the job needs to know and understand how to:
SB1. decide whether the work place is safe for working and also relevant task is
not creating hazardous condition for others
SB2. decide on acceptance criteria for the completed work
SB3. decide on prioritizing activity to meet site requirement
SB4. decide on completion of preceding activity for further course of action
Plan and Organize
The user/individual on the job needs to know and understand how to:
SB5. plan work & organize required resource in coordination with team members and superior
SB6. plan work targets, schedules for subordinates for completion of task as per work plan, time schedule and quality
Customer centricity
The user/individual on the job needs to know and understand how to:
SB7. ensure completion of work as per agreed time schedule and quality
Problem solving
The user/individual on the job needs to know and understand how to:
SB8. suggest remedial action to workers for making corrections if required
SB9. provide solution for replacement of one did bar with other if required did of
bar is not available
SB10.resolve any conflict within the team
Analytical Thinking
The user/individual on the job needs to know and understand how to:
SB11.reconcile material consumption
SB12. assess quality of extracted work for its acceptance
SB13. optimize resources
SB14. minimize wastages
SB15. provide solution for replacement of one did bar with other if required did of
bar is not available
Critical Thinking
The user/individual on the job needs to know and understand how to:
SB16. assess complexity of the tasks and carry out corrective action as per requirement
SB17. identify and assess how violation of any safety norms may lead to accidents
Plan, arrange and manage resources for execution of relevant work
Description
This unit describes the skills and knowledge required to plan, arrange and manage
resources for execution of relevant work
Scope
The scope covers the following:
Arrange and manage manpower
Arrange allocate and mange tools, material and equipment
Performance Criteria (PC) w.r.t. the Scope
Element Performance Criteria Arrange and manage manpower
To be competent, the user / individual on the job must be able to:
PC1. determine quantum and nature of work under assigned activity
PC2. calculate requirement of manpower for assigned activities
PC3. submit manpower requirement to superiors
PC4. allocate and extract work as per plan
PC5. provide clear instructions to workmen for execution of work
PC6. ensure optimum utilization of manpower resources
PC7. record the daily labor attendance
PC8. record the daily productivity report
Arrange allocate and mange tools, material and equipment
PC9. estimate quantity of assigned work
PC10. estimate requirement for material, components and fixtures
PC11. estimate equipment, tools and accessories required
PC12.submit material, equipment and tool requirement to superiors
PC13. allocate material , equipment and tools to workmen and extract the work as per plan
PC14.provide clear instructions for optimized use of resources
Knowledge and Understanding (K)
A. Organizational Context (Knowledge of the company / organization and its processes)
The user/individual on the job needs to know and understand:
KA1. standard practices for execution of relevant work
KA2. safety rules and regulations for handling and storing required tools,
equipment and materials
KA3. personal protection including the use of related safety gears & equipment
KA4. service request procedures for tools, materials and equipment
KA5. statutory compliance requirement related to workmen engagement
B. Technical Knowledge
The user/individual on the job needs to know and understand:
KB1. construction drawing of relevant work
KB2. manpower requirement on the basis of quantum of work and productivity
KB3. sequence and priority of activities
KB4. how to identify priority and critical activity of relevant task
KB5. method and technique on briefing team members about relevant work
KB6. different check to evaluate progress and quality of relevant works
KB7. importance of daily productivity report
KB8. importance of daily attendance register
KB9. standard working practices for relevant works
KB10. principles of measurements
KB11. conversion of units
KB12. arithmetic and geometric calculation
KB13. how to calculate quantum of relevant work
KB14. calculation of tools and material requirement
KB15. optimize use of available resources
KB16. computer basics auto-cad software application for 2D drawing
Skills (S)
A. Core Skills/
Generic Skills
Writing Skills
The user/ individual on the job needs to know and understand how to:
SA1. write at least two language, preferably the local language at the site and basic
English
SA2. provide clear and simple instructions, details & sketches to sub-ordinate
SA3. record and document daily productivity report, daily labour attendance &
details regarding work done
SA4. prepare basic status updates for the superiors in the prescribed format
Reading Skills
The user/ individual on the job needs to know and understand how to:
SA5. read one or more language, preferably the local language at the site
SA6. read relevant drawing, specification and standards
SA7. read key documents including quality standards, standards working methods
& applicable tolerance limits
SA8. read manufacturer instruction and specification for relevant work
SA9. read various, sign boards, safety rules and safety tags , instruction related to
exit routes during emergency at the workplace
Oral Communication (Listening and Speaking skills)
The user/ individual on the job needs to know and understand how to:
SA10. speak in one or more language, preferably one of the local language at site
SA11. listen and follow instructions clearly given by the superior
SA12. provide clear instructions to subordinates for completion of task as per work
plan, time schedule and quality
B. Professional
Skills
Decision Making
The user/individual on the job needs to know and understand how to:
SB1. decide whether workplace is safe for working and also his work is not creating
hazardous conditions for other

SB2. decide on manpower, tools , material and equipment for relevant work
SB3. decide alternate course of action in case of hindrance to work
Plan and Organize
The user/individual on the job needs to know and understand how to:
SB4. plan work & organize required resource in coordination with team members
and superior
SB5. plan work targets, schedules for subordinates for completion of task as per
work plan, time schedule and quality
Customer centricity
The user/individual on the job needs to know and understand how to:
SB6. ensure completion of work as per agreed time schedule and quality
Problem solving
The user/individual on the job needs to know and understand how to:
SB7. suggest remedial action to workers for making corrections
SB8. resolve and solve any conflict within the team
Analytical Thinking
The user/individual on the job needs to know and understand how to:
SB9. reconcile material consumption
SB10. assess quantity of resources required for day work
SB11. optimize resources
SB12. minimize wastages
Critical Thinking
The user/individual on the job needs to know and understand how to:
SB13. assess complexity of the tasks and carry out corrective action as per
requirement
SB14. identify and assess how violation of any safety norms may lead to accidents
Work effectively in a team to deliver desired results at the workplace
Description
This unit describes the skills and knowledge required to work effectively within a
team to achieve the desired results.
Scope
The scope covers the following:
Interact and communicate effectively with co-workers, superiors and subordinates across different teams
Support co-workers, superiors and sub-ordinates within the team and across
interfacing teams to ensure effective execution of assigned task
Performance Criteria (PC) w.r.t. the Scope
Element Performance Criteria
Interact and
communicate in
effective and
conclusive manner
To be competent, the user / individual on the job must be able to:
PC1. pass on work related information/ requirement clearly to the team members
PC2. inform co-workers and superiors about any kind of deviations from work
PC3. address the problems effectively and report if required to immediate
supervisor appropriately
PC4. receive instructions clearly from superiors and respond effectively on same
PC5. communicate to team members/subordinates for appropriate work
technique and method
PC6. seek clarification and advice as per requirement and applicability
Support co-workers
to execute project
requirements
PC7. hand over the required material, tools tackles, equipment and work fronts
timely to interfacing teams
PC8. work together with co-workers in a synchronized manner
Knowledge and Understanding (K)
A. Organizational
Context
(Knowledge of
the company /
organization and
its processes)
The user/individual on the job needs to know and understand:
KA1. own roles and responsibilities
KA2. importance of effective communication and establishing strong working
relationships with co-workers
KA3. risks of a failure in teamwork in terms of effects on project outcomes,
timelines, safety at the construction site, etc.
KA4. different modes of communication, and its appropriate usage
KA5. importance of creating healthy and cooperative work environment among
the gangs of workers
B. Technical
Knowledge
The user/individual on the job needs to know and understand:
KB1. different activities within his work area where an interaction with other workers is required
KB2. applicable techniques of work, properties of materials used, tools and tackles
used, safety standards that co- workers might need as per the requirement
KB3. importance of proper and effective communication and the expected
adverse effects in case of failure relating to quality, timelines, safety, risks at
the construction project site
KB4. importance and need of supporting co-workers facing problems for smooth
functioning of work
Skills (S)
A. Core Skills/
Generic Skills
Writing Skills
The user/ individual on the job needs to know and understand how to:
SA1. write in one or more languages, preferably the local language at the site
Reading Skills
The user/ individual on the job needs to know and understand how to:
SA2. read in one or more languages, preferably the local language at the site
SA3. read communication from team members regarding work completed,
materials used, tools and tackles used, support required
Oral Communication (Listening and Speaking skills)
The user/ individual on the job needs to know and understand how to:
SA4. speak in one or more languages, preferably one of the local language at the site
SA5. listen and follow instructions / communication shared by superiors/ co-
workers regarding team requirements or interfaces during work processes
SA6. orally communicate with co-workers regarding support required to complete
the respective work
B. Professional
Skills
Decision Making
The user/individual on the job needs to know and understand how to:
SB1. decide on what information is to be shared with co-workers within the team
or from interfacing gang of workers
Plan and Organize
The user/individual on the job needs to know and understand how to:
SB2. plan work and organize required resources in coordination with team
members
Customer centricity
The user/individual on the job needs to know and understand how to:
SB3. complete all assigned task in coordination with team members
Problem solving
The user/individual on the job needs to know and understand how to:
SB4. take initiative in resolving issues among co-workers or report the same to
superiors
Analytical Thinking
The user/individual on the job needs to know and understand how to:
SB5. ensure best ways of coordination among team members
SB6. communicate with co-workers considering their educational / social
background
Critical Thinking
The user/individual on the job needs to know and understand how to:
SB7. evaluate the complexity of task and determine if any guidance is required
from superiors
Plan and organize work to meet expected outcomes
Description
This unit describes the knowledge and the skills required for an individual to plan and
organize own work in order to meet expected outcome.
Scope
This scope covers the following:
Prioritize work activities to achieve desired results
Organize desired resources prior to commencement of work
Performance Criteria (PC) w.r.t. the Scope
Element Performance Criteria
Prioritize work
activities to achieve
desired results
To be competent, the user / individual on the job must be able to:
PC1. understand clearly the targets and timelines set by superiors
PC2. plan activities as per schedule and sequence
PC3. provide guidance to the subordinates to obtain desired outcome
PC4. plan housekeeping activities prior to and post completion of work
Organize desired resources prior to commencement of work
PC5. list and arrange required resources prior to commencement of work
PC6. select and employ correct tools, tackles and equipment for completion of
desired work
PC7. complete the work with allocated resources
PC8. engage allocated manpower in an appropriate manner
PC9. use resources in an optimum manner to avoid any unnecessary wastage
PC10. employ tools, tackles and equipment with care to avoid damage to the same
PC11. organize work output, materials used, tools and tackles deployed,
PC12. processes adopted to be in line with the specified standards and instructions
Knowledge and Understanding (K)
A. Organizational
Context
(Knowledge of
the company /
organization and
its processes)
The user/individual on the job needs to know and understand:
KA1. importance of proper housekeeping
KA2. policies, procedures and work targets set by superiors
KA3. roles and responsibilities in executing the work for subordinates and self
B. Technical Knowledge
The user/individual on the job needs to know and understand:
KB1. standard practices of work to be adopted for assigned task
KB2. how to use available resources in a judicious and appropriate manner to
minimize wastages or damage
Plan and organize work to meet expected outcomes
Description
This unit describes the knowledge and the skills required for an individual to plan and
organize own work in order to meet expected outcome.
Scope
This scope covers the following:
Prioritize work activities to achieve desired results
Organize desired resources prior to commencement of work
Performance Criteria (PC) w.r.t. the Scope
Element Performance Criteria
Prioritize work
activities to achieve
desired results
To be competent, the user / individual on the job must be able to:
PC1. understand clearly the targets and timelines set by superiors
PC2. plan activities as per schedule and sequence
PC3. provide guidance to the subordinates to obtain desired outcome
PC4. plan housekeeping activities prior to and post completion of work
Organize desired
resources prior to
commencement of
work
PC5. list and arrange required resources prior to commencement of work
PC6. select and employ correct tools, tackles and equipment for completion of
desired work
PC7. complete the work with allocated resources
PC8. engage allocated manpower in an appropriate manner
PC9. use resources in an optimum manner to avoid any unnecessary wastage
PC10. employ tools, tackles and equipment with care to avoid damage to the same
PC11. organize work output, materials used, tools and tackles deployed,
PC12. processes adopted to be in line with the specified standards and instructions
Knowledge and Understanding (K)
A. Organizational
Context
(Knowledge of
the company /
organization and
its processes)
The user/individual on the job needs to know and understand:
KA1. importance of proper housekeeping
KA2. policies, procedures and work targets set by superiors
KA3. roles and responsibilities in executing the work for subordinates and self
B. Technical
Knowledge
The user/individual on the job needs to know and understand:
KB1. standard practices of work to be adopted for assigned task
KB2. how to use available resources in a judicious and appropriate manner to
minimize wastages or damage
The user/individual on the job needs to know and understand how to:
SB6. evaluate potential solutions to minimize avoidable delays and wastages at
the construction site
Supervise, monitor and evaluate performance of subordinates at workplace
Description
This OS covers the skills and knowledge required by an individual to supervise,
monitor and evaluate performance of subordinates at work place
Scope
The scope covers the following:
Monitor all construction work activities performed by subordinates and evaluate
their performance and ensure strict adherence to quality instructions &
timelines as per organizational policies and procedures
Performance Criteria (PC) w.r.t. the Scope
Element Performance Criteria
Supervise, monitor and evaluate performance of all subordinates and ensure adherence to organizational policies and procedures
To be competent, the user/individual on the job must be able to:
PC1. fix expected targets for the respective gang as per site requirements
and allocate work to subordinates
PC2. establish expected performance standards and expectations for the
respective gang of workers to meet the desired outcomes
PC3. inspect assigned work to the respected gang of workers through progressive checking
PC4. observe and verify the work activities performed by the subordinates at the
construction site
PC5. monitor overall performance of subordinates on the designed measures to
ensure quality requirements set by the concerned authority
PC6. ensure adherence to the organizational policies and procedures for all
relevant construction activities by the workmen subordinations
Knowledge and Understanding (K)
A. Organizational Context (Knowledge of the company / organization and its processes)
The user/individual on the job needs to know and understand:
KA1. policies, procedures and work targets for performance evaluation and appraisals
KA2. organizational policies, procedures and protocol for smooth completion of
work at the respective workplace
B. Technical Knowledge
The user/individual on the job needs to know and understand:
KB1. complete work/task accurately by following standard specifications and
procedures by optimized and correct used of materials , tools, tackles and
equipment