Vessel Operator Grade 2
Vessel Operator Grade 2 click here
Brief Job Description: The individual navigates the vessel, supervises of loading and
unloading of cargo, performs advanced preventive and corrective maintenance,
reports potential waterway hazards and manages the vessel crew
Qualifications Pack for Vessel Operator Grade 2
Electives
Elective 1: Deck Operations
The unit is about planning of deck maintenance schedule, vessel handling, storage
and inventory, and providing on-board training to deck drew

Elective 2: Engine Operations
The unit is about supervision of engine operation, overhauling of engine and related
equipment’s, undertaking preventive maintenance and undertake troubleshooting
Options
Option 1: Tug Vessel Operations
The unit is about oversea load planning, route mapping and operating within the
limitations of tug vessel
Option 2: Profit Management
The unit is about assessing the profit and loss and cost accounting of an activity or
operation
Option 3: Ship and Yard Planning
The unit is about supervising cargo handling and storage operations in the port
terminal, Inland Container Depots (ICD) or Container Freight Stations (CFS)
Personal Attributes: The job holder should have normal or corrected eyesight and
be physically fit and should have attention to details, and adaptability. The
individual should be pro-active, organised and should be able to multitask.
Description
Core Skills/Generic
Skills
Core Skills or Generic Skills are a group of skills that are key to learning and
working in today’s world. These skills are typically needed in any work
environment. In the context of the NOS, these include communication related
skills that are applicable to most job roles.
Function
Function is an activity necessary for achieving the key purpose of the sector,
occupation, or area of work, which can be carried out by a person or a group
of persons. Functions are identified through functional analysis and form the
basis of NOS.
Job role Job role defines a unique set of functions that together form a unique
employment opportunity in an organization.
Knowledge and
Understanding
Knowledge and understanding are statements which together specify the
technical, generic, professional and organizational specific knowledge that an
individual needs in order to perform to the required standard.
National Occupational
Standards (NOS) NOS are Occupational Standards which apply uniquely in the Indian context
Occupation Occupation is a set of job roles, which perform similar/related set of functions
in an industry.
Organisational Context
Organisational Context includes the way the organization is structured and
how it operates, including the extent of operative knowledge managers have
of their relevant areas of responsibility.
Performance Criteria Performance Criteria are statements that together specify the standard of
performance required when carrying out a task.
Qualifications
Pack(QP)
Qualifications Pack comprises the set of NOS, together with the educational,
training and other criteria required to perform a job role. A Qualifications
Pack is assigned a unique qualification pack code.
Electives Electives are NOS/set of NOS that are identified by the sector as contributive
to specialization in a job role. There may be multiple electives within a QP for
each specialized job role. Trainees must select at least one elective for the
successful completion of a QP with Electives.
Options Options are NOS/set of NOS that are identified by the sector as additional
skills. There may be multiple options within a QP. It is not mandatory to select
any of the options to complete a QP with Options.
Unit Code Unit code is a unique identifier for an Occupational Standard, which is
denoted by an ‘N’
Unit Title Unit title gives a clear overall statement about what the incumbent should be
able to do.
Qualifications Pack
Code
Qualifications Pack Code is a unique reference code that identifies a
qualifications pack.
Scope Scope is the set of statements specifying the range of variables that an
individual may have to deal with in carrying out the function which have a
critical impact on the quality of performance required.
Sector
Sector is a conglomeration of different business operations having similar
businesses and interests. It may also be defined as a distinct subset of the
economy whose components share similar characteristics and interests.
Sub-Sector Sub-sector is derived from a further breakdown based on the characteristics
and interests of its components.
Sub-functions Sub-functions are sub-activities essential to fulfil the achieving the objectives
of the function.
Technical Knowledge Technical Knowledge is the specific knowledge needed to accomplish specific
designated responsibilities.
Description
BP Bollard Pull
CFS Container Freight Stations
CSS Cargo Stowage and Securing
ERP Enterprise Resource Planning
ETA Expected Time of Arrival
GPS Global Positioning System
HR Human Resources
ICD Inland Container Depots
IMDG International Maritime Dangerous Goods
MHEs Material Handling Equipment
MIS Management information system
NOS National Occupational Standards
NSQC National Skills Qualifications Committee
NSQF National Skills Qualifications Framework
OS Occupational Standards
OSHA Occupational Safety and Health Administration
PMS Planned maintenance system
PPE Personal Protective Equipment
QP Qualifications Pack
RFID Radio-Frequency Identification
SOEP Shipboard oil pollution emergency plan
SOP Standard Operating Procedures
SWL Safe Working Load
VHF Very High Frequency
WWL Working Load Limit
Perform detailed navigation
Description This unit is about performing in-depth navigation
Scope This unit/task covers the following:
• Navigation planning
• Carry out navigation and maneuvering
Range: Vessel, maps & charts, navigation aids, compass, Global Positioning
System (GPS), worksheets, stationery, computer, projector etc.
Performance Criteria(PC) w.r.t. the Scope
Element Performance Criteria
Navigation
planning
To be competent, the user/individual on the job must be able to:
PC1. check map for available routes
PC2. check weather and sea condition forecasts
PC3. develop vessel’s sailing plan and direction
PC4. advise on the path and estimated time to the destination
PC5. calculate expected time of arrival (ETA)
PC6. communicate and update the port on the progress of the vessel
Carry out
navigation and
maneuvering
To be competent, the user/individual on the job must be able to:
PC7. follow the planned route
PC8. use tide tables and charts to determine tidal effects and ocean current
effects on water levels and vessel
PC9. maintain general surveillance of the ship
PC10. record vessel’s movement to avoid collision
PC11. maintain nautical charts, publications and equipment
PC12. prepare and share weather reports to stakeholders
PC13. monitor the progress of the ship against the plan
PC14. handover the required details to the reliever
PC15. assist the master in devising a plan of action based on ship’s elements
PC16. record minimum depth of water, wind’s force, tide, current and general
condition of the berth
PC17. prepare contingency plan for any change in circumstances
PC18. engage in manual steering if required
PC19. listen to the instructions as given by the pilot about the course of action
PC20. note down all navigational marks in the ship maneuvering book
Knowledge and understanding (K)
A. Organizational
context
The individual on the job needs to know and understand:
KA1. organizational procedures and policy on quality, use of Personal
Protective Equipment (PPEs), use of equipment, Material Handling
Equipment (MHEs), documentation, etc.
KA2. company’s reporting structure to support and expedite project activities
KA3. company’s policy and work instructions on quality standards
KA4. importance of the individual’s role in the workflow
KA5. occupational health and safety standards and security procedures to be
followed
KA6. procedures for dealing with loss or damage to goods
KA7. risk and impact of not following defined work, safety and security
procedures
KA8. coding system followed to label items
B. Technical
knowledge
The individual on the job needs to know and understand:
KB1. navigation terms
KB2. sea and port watch systems
KB3. mercator chart and navigational charts and their scales
KB4. meteorological instruments such as Stevenson screen, Psychrometer,
Barometer, Barograph, Anemometer, magnetic compass, GPS
KB5. international code of signal and flags
KB6. hazard identification and avoidance
KB7. warning and safety signs
KB8. emergency evacuation procedure
KB9. handling of fuel spillage
KB10. mooring and maneuvering of the vessel
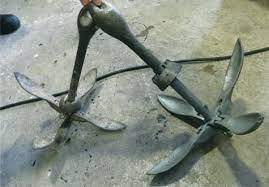
Skills (S)
A. Core skills/
generic skills
Reading skills
The user/individual on the job needs to know how to read:
SA1. written instructions over communication networks, etc.
SA2. map and navigational charts
Writing skills
The user/individual on the job needs to know how to write:
SA3. daily reports including damages and accidents
SA4. navigation and maneuvering log books
Oral communication (listening and speaking skills)
The user/individual on the job needs to know how to:
SA5. communicate in clear and concise manner with the pilot and master
B. Professional
Skills
Decision making
The user/individual on the job needs to know how to:
SB1. identify the most efficient route
SB2. decide on vessel speed and direction while navigating
SB3. identify activities or orders that need to be prioritized as per instructions
Plan and organize
The user/individual on the job needs to know how to:
SB4. plan and estimate the time for each activity
SB5. respond to the supervisor in a timely manner
SB6. prioritize and execute tasks based on instructions
Customer centricity
The user/individual on the job needs to know and understand:
SB7. importance of given timelines
SB8. urgency of priority requests as per the instructions
Problem solving
The user/individual on the job needs to know how to:
SB9. make route corrections to avoid collisions and adverse weathers
Analytical thinking
The user/individual on the job needs to know how to:
SB10. analyse obstacles and weather and devise revisions in navigation plans
Critical thinking
The user/individual on the job needs to know how to:
SB11. observe adverse weathers, bridge communications and take required
action while navigating
SB12. follow orders and SOPs while mooring, berthing and maneuvering
SB13. focus on task at hand ad complete it without errors and delays
Repair and maintenance of vessel
Description This unit is about performing advanced preventive maintenance
Scope This unit/task covers the following:
• Maintain deck equipment, winches, capstans and hatches
• Carry out maintenance
Range: Vessel and engine room equipment, tools and tackles, cranes and winches,
welding equipment, fitting tools, Standard Operating Procedures (SOP), computer,
work bench, worksheets, projector, etc
Performance Criteria(PC) w.r.t. the Scope
Element Performance Criteria
Maintain deck
equipment, winches,
and hatches
To be competent, the user/individual on the job must be able to:
PC1. perform basic check of cranes, derricks, winches and related equipment
PC2. ensure safe working load (SWL) or working load limit (WWL) of equipment
PC3. inspect the friction brake lining regularly in the capstan and replace whenever
necessary
PC4. check wire cable in case if they are broken or rust
PC5. inspect winch drums for deterioration of friction
PC6. examine hatch cover and hatch beams for corrosion, cleanliness, cracks and
material failure
PC7. lubricate the working parts and record the wear and tear
PC8. take step to prevent oil or grease from accumulating on the brake surface
PC9. replace rubber gasket immediately in case found missing or broken
PC10. report to the officer in case of any failure, damage or malfunction
PC11. move different type of cargo and loads using equipment – slings, lifts and in a
secure and safe manner
Carry out
maintenance
To be competent, the user/individual on the job must be able to:
PC12. check for the load limit on scaffolding
PC13. take necessary precautions like fix the safety harness and connect the fall
arrester device, wear Personal Protective Equipment (PPEs), have standby
emergency support personnel, secure ladder and stage for working, etc. prior
to working
PC14. setup and use scaffolding by securing the scaffolding platform using
guardrails, mid-rails and toe boards
PC15. take due precautions when climbing portable ladders
PC16. perform routine maintenance work aloft using various equipment related to
greasing, oiling or basic fitting and carpentry
PC17. perform maintenance working over-side the vessel on the working stage
rigged via ladders
PC18. keep the necessary equipment – hand-tools, drills, paint and paint brush,
chisel and hammers, etc. in a tightly rigged bucket alongside to work
PC19. use donning and breathing equipment to perform maintenance in enclosed
spaces strictly as per SOP
PC20. use chemicals and strong detergents with due precautions and PPEs for
cleaning and maintenance activities
PC21. pour chemical in water container for dilution
PC22. check that the area is well ventilated
PC23. report to master or officer in case of any accidents, injuries, damages and
malfunction of equipment
Knowledge and understanding (K)
A. Organizational
Context
The individual on the job needs to know and understand:
KA1. organizational procedures and policy on quality, use of PPEs, use of
equipment, Material Handling Equipment (MHEs), documentation, etc.
KA2. company’s reporting structure to support and expedite project activities
KA3. company’s policy and work instructions on quality standards
KA4. importance of the individual’s role in the workflow
KA5. occupational health and safety standards and security procedures to be
followed
KA6. procedures for dealing with loss or damage to goods
KA7. risk and impact of not following defined work, safety and security procedures
KA8. coding system followed to label machineries
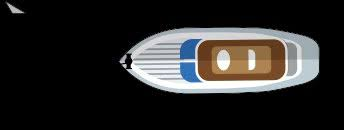
B. Technical
knowledge
The individual on the job needs to know and understand:
KB1. various hazards related to the vessel cleaning and maintenance operations in
in various parts of the ship
KB2. emergency response and basic first aid response
KB3. various types of PPEs and their usage
KB4. electrical shock and precautions to be observed to prevent shock
KB5. types of power tools and equipment for different activities – electrical checks,
carpentry, fitting, welding, painting, etc.
KB6. operation of various vessel and engine room equipment
KB7. emergency procedure of dealing with pumps and valves
KB8. functions of various kinds of equipment such as hoists, cranes and booms
KB9. various signs and signals
KB10. functions of capstan and winches
KB11. donning and using breathing apparatus
KB12. use of electrical equipment
Skills (S)
C. Core Skills/ Reading skills Generic Skills
The user/individual on the job needs to know how to read:
SA1. written instructions
SA2. read maintenance schedule
Writing skills
The user/individual on the job needs to know how to write:
SA3. daily report including damages, injuries, accidents, etc.
SA4. maintenance log book for various equipment and vessel parts
Oral communication (listening and speaking skills)
The user/individual on the job needs to know how to:
SA5. communicate with masters, officers and co-workers
SA6. collect information from masters
D. Professional Skills Decision making
The user/individual on the job needs to know how to:
SB1. idenitfy the equipment is fit for use
SB2. decide the necessary precuations for a maintenance activity
Plan and organize
The user/individual on the job needs to know how to:
SB3. maintain punctuality
SB4. should respond to the supervisor in a timely manner
SB5. prioritize and execute tasks based on instructions
Customer centricity
The user/individual on the job needs to know and understand:
SB6. importance of assigned timelines
SB7. urgency as per the instructions
Problem solving
The user/individual on the job needs to know how to:
SB8. take measures to prevent an accident while working in hazardous
environment
SB9. suggest measures for safe discharge of maintenance duties aboard the ship
Analytical thinking
The user/individual on the job needs to know how to:
SB10. identify common mistakes with regards to maintenance and safety and avoid
them
Critical thinking
The user/individual on the job needs to know how to:
SB11. recognize and report electrical hazards and unsafe equipment
SB12. take necessary precuations and strictly follow SOP when working in hazardous
environment
Perform welding, cutting and machining
Description This unit is about performing welding, cutting and machining work
Scope This unit/task covers the following:
• Perform arc welding
• Undertake basic lathe work
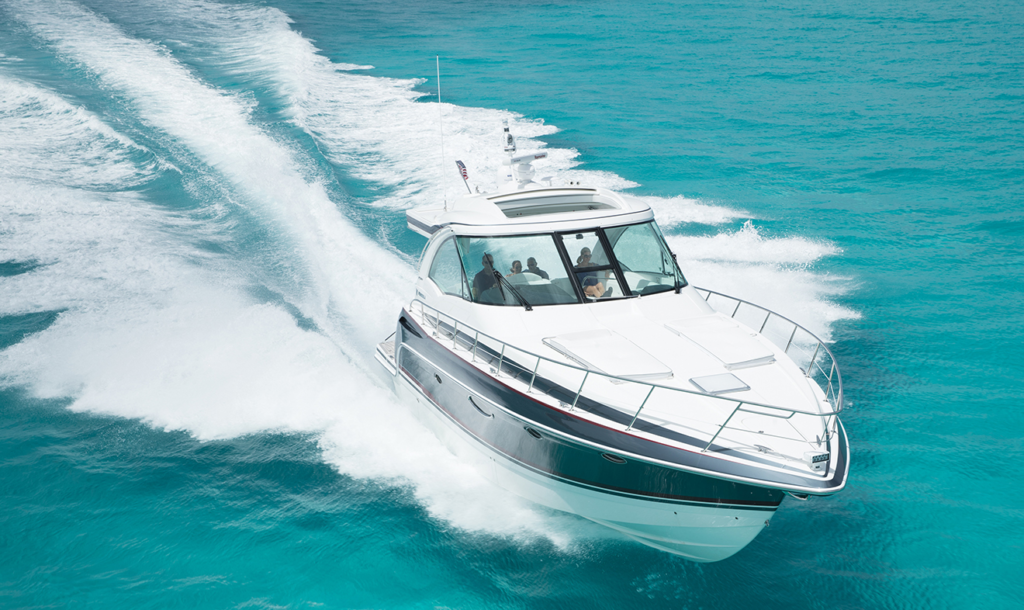
• Carry out valve operations and plumbing repairs
Range: Vessel equipment, tools and tackles, welding equipment, consumables,
work bench, cranes and winches, stationery, work sheets, Standard Operating
Procedures (SOP), computer, projector, etc.
Performance Criteria(PC) w.r.t. the Scope
Element Performance Criteria
Perform arc
welding
To be competent, the user/individual on the job must be able to:
PC1. remove dust, dirt, grease, oil, etc. from the metal piece to be weld with
the help of wire brush or power wire
PC2. insert a suitable electrode in the electrode holder at an angle of 60° to
80°
PC3. wear the necessary Personal Protective Equipment (PPE) and face shield
to protect the eyes and face from harmful ultraviolet and infrared
radiation
PC4. select proper current and polarity
PC5. contact the electrode with the metal and separate it at proper distance
to produce an arc
PC6. brush off the slag after the joint has cooled with the chipping hammer
PC7. take out the electrode holder to break arc
PC8. switch off the supply of current and shut off acetylene valve and the
oxygen
PC9. check that filled in gas cylinders and empty gas cylinders are kept
separate
Undertake basic
lathe work
To be competent, the user/individual on the job must be able to:
PC10. check lathe for any damage or missing part
PC11. wear protective eyewear and PPE
PC12. clamp the work piece tightly to the lathe
PC13. ensure that cutting of the work piece with the lathe is done as
recommended by the manufacturer
PC14. follow safety procedure while fabrication
PC15. clean the area after using lathe
Carry out valve
operations and
plumbing
repairs
To be competent, the user/individual on the job must be able to:
PC16. open and close valves as per procedure
PC17. inspect pipes at regular intervals as described in the ship’s maintenance schedule
PC18. inspect for leakages, switch off the relevant pump and investigate the
source of leakage
PC19. make temporary repair by binding or clamping
PC20. inspect the inside of the pipes looking for cause of erosion and corrosion
PC21. repair all leaks as per procedure
Knowledge and understanding (K)
A.
Organizational
Context
The individual on the job needs to know:
KA1. organizational procedures and SOPs for tasks at hand, documentation
policy and emergency responses, internal communication over network
KA2. security and safety procedures to be followed
KA3. reporting structure of the organization for escalation of issues
KA4. risk and impact of not following defined procedures/work instructions
KA5. coding system followed to communicate using flags, hand signals and
sound signals
B. Technical
knowledge
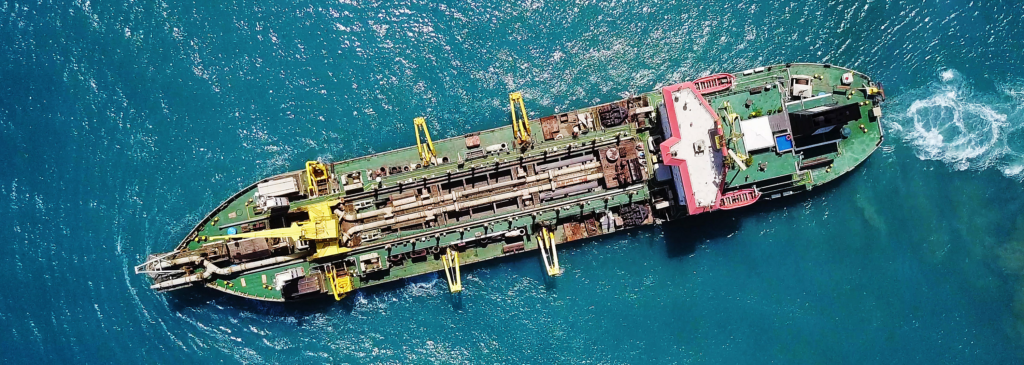
The individual on the job needs to know and understand:
KB1. hazards involved in using welding equipment
KB2. PPE used for welding, cutting and machining operations
KB3. components, tools and accessories of arc welding machine
KB4. do’s and don’ts of dealing with gas cylinders
KB5. types and colors of hose pipe
KB6. lathe and welding operation manuals and SOPs
KB7. fluid mechanics and working of pipelines
KB8. rust, corrosion and other damages to pipelines
KB9. use of hand-tools and power-tools
Skills (S)
E. Core Skills/
Generic
Skills
Reading skills
The user/individual on the job needs to know how to read:
SA1. written instructions
Writing skills
The user/individual on the job needs to know how to write:
SA2. daily reports indicating damages, accidents and injuries
SA3. maintenance and usage logs of equipments
Oral communication (listening and speaking skills)
The user/individual on the job needs to know how to:
SA4. communicate with officers, masters and co-workers
SA5. collect information from master
F. Professional
Skills
Decision making
The user/individual on the job needs to know how to:
SB1. idenitfy the welding requirement based on the view of the equipment, item
SB2. Identify the damage in the pipeline
SB3. decide if a problem can be resolved onboard the vessel
Plan and organize
The user/individual on the job needs to know how to:
SB4. plan and estimate the time for each activity
SB5. prioritize and execute tasks based on instructions
Customer centricity
The user/individual on the job needs to know and understand:
SB6. importance of assigned timelines
SB7. urgency of priorties as per the instructions
Problem solving
The user/individual on the job needs to know how to:
SB8. inform the master regarding delays, issue in equipment, safety hazards
not yet catered, etc.
Analytical thinking
The user/individual on the job needs to know how to:
SB9. analyse hazards involved in working with welding equipment
SB10. carryout risk assessment prior to starting the assignment
Critical thinking
The user/individual on the job needs to know how to:
SB11. identify leakage and damages to the pipe
SB12. Identify leakage of gas from welding cylinder
SB13. close all valves and regulators after use of welding equipment
SB14. Strictly follow SOP during storage and use of welding and lathe
Allocate resources and manage stores in a vessel
Description This unit is about allocating resources and streamlining operations in an inland
waterways vessel
Scope This unit/task covers the following:
• Prepare maintenance plan and allocate resources
• Resolve escalated issues
• Monitor daily operations
• Storage and inventory
Range: Standard Operating Procedures (SOP), route plans, communication
equipment, inventory models, computer, projector, worksheets, etc.
Performance Criteria(PC) w.r.t. the scope
Element Performance Criteria
Prepare
maintenance plan
and allocate
resources
To be competent, the user/ individual must be able to:
PC1. obtain details of vessel route and prepare tasks for workforce to
complete various maintenance activities
PC2. prepare schedule for maintenance of deck and engine room equipment
and machineries
PC3. get the work plan approved from the vessel chief officer/ master
PC4. allocate tasks to crew along with necessary equipment
Resolve escalated
issues
To be competent, the user/ individual must be able to:
PC5. identify priorities and allocate adequate resources to address various
tasks
PC6. provide guidance to assistants and workers if required and suggest ways
to resolve issues
PC7. escalate the matter to chief officer/ master for any external technical
support
PC8. liaise with officers to streamline vessel operations
Monitor daily
operations
To be competent, the user/individual on the job must be able to:
PC9. conduct inspection of vessel for safety, security of cargo and vessel,
cleanliness, marking of cargo areas, fitness of equipment and emergency
systems, etc.
PC10. prepare daily reports on task performed by crew
PC11. escalate issues with respect to operations, cargo handling, damages,
injuries, service requirements, etc. to chief officer/ master
Storage and
inventory
To be competent, the user/individual on the job must be able to:
PC12. maintain stock of inventory in the ship of different items – cargo handling
tools, food items, clothing and linen, spare parts, etc.
PC13. maintain stores under lock and key
PC14. check cleanliness and hygiene of stock including rodent prevention, waste
segregation, etc.
PC15. provide items from stores as per authorized approvals
PC16. keep a daily count of inventory and update the count register
PC17. identify the items to be quarantines or disposed and take necessary
approvals for action
PC18. inform the chief officer/ master regarding re-placements and shortages
Knowledge and understanding (K)
A. Organizational
context
(Knowledge of
the company /
organization
and its
processes)
The individual on the job needs to know:
KA1. organizational procedures and SOPs for tasks at hand, documentation
policy and emergency responses, internal communication over network
KA2. security and safety procedures to be followed
KA3. reporting structure of the organization for escalation of issues
KA4. risk and impact of not following defined procedures/work instructions
KA5. coding system followed to communicate using flags, hand signals and
sound signals
B. Technical
knowledge
The individual on the job needs to know and understand:
KB1. basics of operations in a port terminal, Container Freight Stations (CFS),
Inland Container Depots (ICD)
KB2. use of various cargo handling equipment
KB3. use of rope , flags and other manual equipment
KB4. vessel layout and loading and unloading activities
KB5. procedures of tank cleaning, cargo movement
KB6. requirements regarding handling of cargo
KB7. different type of vessels and cargo and container sizes
KB8. different type of cranes and Material Handling Equipment (MHEs) – their
capacities, constraints and usage
KB9. handling of hazardous and non-hazardous cargo – – International
Maritime Dangerous Goods (IMDG) code
KB10. marking of material and people movement areas
KB11. stuffing and de-stuffing norms with respect to different cargo
KB12. special characteristics and handling requirements of shipments, if any
Skills (S)
A. Core skills/
generic skills
Reading skills
The user/individual on the job needs to know how to read:
SA1. written instructions
SA2. shiping manifest, Bill of lading shipping bills and related documents
SA3. Enterprise Resource Planning (ERP) and computer generated reports
SA4. cargo stowage plans and vessel plans
SA5. SOPs and safety regulation manuals
Writing skills
The user/individual on the job needs to know how to write:
SA6. work-orders and instructions
SA7. daily reports
Oral communication (listening and speaking skills)
The user/individual on the job needs to know how to:
SA8. communicate with customers, fireght operators, transporters, shipping
companies, other supervisors and port authorities
SA9. guide cargo handlers for smooth operations
B. Professional
skills
Decision making
The user/individual on the job needs to know how to:
SB1. decide on required workforce and equipment for performing a particular
task
SB2. assess the environmental condition and type of cargo to assess if it is safe
for loading/ discharge operations
SB3. decide on deployment of alternate resources when required
Plan and organize
The user/individual on the job needs to know how to:
SB4. plan and estimate the co-ordination required for resolving a querry.
SB5. maintain punctuality and respond to the queries in a timely manner
SB6. prioritize and execute tasks based on client requirements
SB7. make work plans and resource allocation plans
SB8. be a team player and achieve joint goals
Customer centricity
The user/individual on the job needs to know how to:
SB9. adhere to the assigned timelines
SB10. address the urgency regarding priority requests
Problem solving
The user/individual on the job needs to know how to:
SB11. make adjustment to working requirements for difficult weathers and
hazardous goods
SB12. co-ordinate and handle major issues with different departments
SB13. identify bottlenecks and operational problems and suggest remedial
action
Analytical thinking
The user/individual on the job needs to know how to:
SB14. assess the resource requirement for a particular task at hand
SB15. assess and prepare for backup resources in case of delays
SB16. plan for cargo movement so that the resources and stroage space is
optimally utilised
Critical thinking
The user/individual on the job needs to know and understand how to:
SB17. develop work plans factoring in external weather and vessel factors
SB18. check that all security measures and safety protocals are followed at all
times
Maintain integrity and ethics in operation
Description This unit is about maintaining integrity, ensuring data security, and professional and
ethical practices
Scope This unit/task covers the following:
• Maintain integrity and ensure data security
• Professional and ethical practices
• Ensure regulatory compliance
Range: Standard Operating Procedures (SOP), worksheets, computer, projector,
stationery etc.
Performance Criteria(PC) w.r.t. the Scope
Element Performance Criteria
Maintain integrity
ensuring data
security
To be competent, the user/ individual must be able to:
PC1. refrain from indulging in corrupt practices
PC2. avoid using company’s funds, property or resources for undertaking personal
activities
PC3. protect customer’s information and ensure it is not misused
PC4. protect data and information related to business or commercial decisions
Professional and
ethical practices
To be competent, the user/ individual must be able to:
PC5. avoid acceptance of cash or kind from vendors for support or contract
negotiations
PC6. demonstrate and practice ethics in day-to-day processes and dealings with
customers and colleagues
PC7. avoid nepotism
PC8. consult supervisor or senior management when in situations that may require
differentiating between ethical and unethical
PC9. report promptly all violations of code of ethics
PC10. dress up and conduct in a professional manner
PC11. communicate with clients and stakeholders in a soft and polite manner
PC12. follow etiquettes in accordance to the place
Ensure regulatory
compliance
To be competent, the user/ individual must be able to:
PC13. check for regulatory documentation and compliances for the shop floor as
per information from the supervisor
PC14. perform activities considering the regulatory requirements
PC15. use PPEs in accordance to regulatory requirements
PC16. identify the different types of dangerous goods and handling methodologies
PC17. follow the SOP for handling of different types of dangerous goods
PC18. consult supervisor or senior management when in situations that may require
differentiating between ethical and unethical
PC19. promptly report all regulatory violations
Knowledge and understanding (K)
A. Organizational
context
(Knowledge of the
company /
organization and
its processes)
The user/individual on the job needs to know and understand:
KA1. company’s policies on use of language
KA2. company’s Human Resources policies
KA3. company’s code of ethics
KA4. company’s whistle blower policy
KA5. company’s rules related to sexual harassment
KA6. company’s reporting structure
KA7. company’s documentation policy
B. Technical
knowledge The user/individual on the job needs to know and understand:
KB1. principles of code of ethics and business ethics
KB2. various regulatory requirements
KB3. documentary compliance for various regulations
KB4. different dangerous shipment
KB5. regulations w.r.t dangerous shipment
Skills (S)
A. Core skills/
generic skills
Reading Skills
The individual on the job needs to know how to read:
SA1. company policy documents and work-related documents
SA2. emails and written instructions
Writing Skills
The individual on the job needs to know how to fill:
SA3. documentation pertaining to ethics and regulatory requirement
Oral Communication (Listening and Speaking skills)
The individual on the job needs to know how to communicate with:
SA4. team members to work efficiently
SA5. peers and subordinates about information security and building trust
B. Professional skills
Decision making
The individual on the job needs to know how to:
SB1. identify a shipment as dangerous goods
SB2. assess if the situation needs to be reported regarding regulations
Plan and Organize
The individual on the job needs to know how to:
SB3. plan and organise actions as per company’s guidelines
Customer centricity
The individual on the job needs to know how to:
SB4. prevent company and customer information leakage
Problem solving
The individual on the job needs to know how to:
SB5. advisee colleagues regarding sensitive issues pertaining to conduct and
regulations
Analytical Thinking
The individual on the job needs to know how to:
SB6. provide professional services diligently and with integrity
Critical Thinking
The individual on the job needs to know how to:
SB7. avoid defaming company’s name by indulging into pilferage or fiddling with
quality or quantity of shipment
SB8. be fair and reasonable in profession and disclose conflict of interests
Follow and monitor health, safety and security procedures on vessel
Description This unit is about ensuring compliance with health, safety and security procedures at
the workplace.
Scope This unit/task covers the following:
• Survival Techniques
• First aid
• Fire prevention and fire fighting
• Personal safety and social responsibility
• Security procedures
Range: Personal Protective Equipment (PPE), first aid kit, fire safety equipment,
Standard Operating Procedures (SOP), worksheets, computer, projector, stationery
etc.
Performance Criteria(PC) w.r.t. the scope
Element Performance Criteria
Survival
techniques
To be competent, the user/ individual must be able to:
PC1. wear a life jacket and immersion suit
PC2. safely jump from a height into the water
PC3. swim while wearing lifejacket
PC4. right an inverted life raft while wearing life jacket
PC5. board a life raft or survival vessel from the vessel or the water while wearing
life jacket
PC6. keep afloat without life jacket
PC7. operate survival craft, life raft and its equipment and communication devices
First Aid To be competent, the user/ individual must be able to:
PC8. assess the casualty and immediate medical needs and threat to own safety
PC9. position casualty and apply resuscitation techniques
PC10. apply measures to control bleeding, cover and secure burn injuries using
bandages and emergency medical kit
PC11. apply measures for basic shock management
PC12. assist in rescue and transport of the casualty
Fire prevention
and fire fighting
To be competent, the user/ individual must be able to:
PC13. take due precautions like – segregate and store, ensure proximity to
firefighting equipment, etc. while storing inflammable materials on-board
the vessel
PC14. regularly monitor the inflammable material and cargo for fire hazards
PC15. organise and maintain the firefighting equipment to make it easily accessible
and operable during emergencies
PC16. check fire and smoke alarms for functionality
PC17. keep the emergency response routes and escape routes clear
PC18. use different protective equipment and high pressure breathing equipment
PC19. use different type of firefighting equipment to extinguish a fire, when
required
PC20. participate in fire and emergency drills
Personal safety
and social
responsibilities
To be competent, the user/ individual must be able to:
PC21. inform and take appropriate action when discovering a potential emergency
PC22. recognize the emergency signal and respond as per the emergency plan
PC23. follow the designated escape routes
PC24. follow safe and environmental friendly working practices
PC25. follow precautions while entering closed areas and hazardous areas on-board
the vessel
PC26. maintain effective communications in person and while using vessel
communication devices and systems
Security
procedures
To be competent, the user/ individual must be able to:
PC27. follow vessel security plan
PC28. identify security risks and threats, communicate and initiate action as per
vessel security plan
PC29. undertake regular vessel inspection with respect to vessel and cargo security
PC30. check that all cargo containers, holds and hatches are secured
PC31. check security equipment and system for functionality and maintenance
Knowledge and understanding (K)
A. Organizational
context
(Knowledge of
the company /
organization
and its
processes)
The individual on the job needs to know:
KA1. organizational procedures and SOPs for tasks at hand, documentation policy
and emergency responses, internal communication over network
KA2. security and safety procedures to be followed
KA3. reporting structure of the organization for escalation of issues
KA4. risk and impact of not following defined procedures/work instructions
KA5. coding system followed to communicate using flags, hand signals and sound
signals
B. Technical
knowledge
The individual on the job needs to know and understand:
KB1. various nautical terms related to navigation – hulls, shipside, engine room,
etc.
KB2. various parts and components of the ship
KB3. map reading and identification of location in the globe
KB4. different type of vessels and their functions and cargo
KB5. different type of cargo and their handling requirement
KB6. basics of Occupational Safety and Health Administration (OSHA)
KB7. necessary security procedures and vessel security plan and contingency plan
KB8. layout of firefighting and first aid on the vessel
KB9. safety and security procedures for different operations and equipment
KB10. handling procedure for hazardous / fragile cargo
KB11. security procedures for dangerous / hazardous goods – International
Maritime Dangerous Goods (IMDG) cargo
KB12. different personal protective equipment (PPE), their usage and purpose
KB13. various survival techniques
Skills (S)
A. Core skills/
generic skills
Reading skills
The user/individual on the job needs to know how to read:
SA1. procedures and standards related to health, safety and security of vessel and
cargo
SA2. vessel security and emergency plan
SA3. emergency equipment layout
SA4. various documents related to security and movement of cargo
Writing skills
The user/individual on the job needs to know how to:
SA5. fill forms related to health, safety and security procedures
Oral communication (listening and speaking skills)
The user/individual on the job needs to know and understand how to:
SA6. communicate clearly with colleagues regarding safety procedures
SA7. share experience and provide guidance to peers
B. Professional
skills
Decision making
The user/individual on the job needs to know how to:
SB1. identify threats to security and emergency situations
SB2. decide the right equipment to be used in case of fire and threat emergency
SB3. decide the first aid required upon seeing casualty
Plan and organize
The user/individual on the job needs to know how to:
SB4. plan actions in case of security threat or emergency
SB5. prioritize and execute tasks as per contingency plan
Customer centricity
The user/individual on the job needs to know and understand how to:
SB6. follow instructions as per vessel contingency plan
Problem solving
The user/individual on the job needs to know and understand how to:
SB7. identify any threats on personal health, safety, security, etc. and take
appropriate actions
SB8. identify risks aboard the vessel and inform superiors
Analytical thinking
The user/individual on the job needs to know and understand how to:
SB9. analyse situations to assess threats or risks
Critical thinking
The user/individual on the job needs to know and understand how to:
SB10. ensure right safety measures and security protocols are followed at all times
Vessel handling and steering
Description This unit is about performing vessel handling and steering activities
Scope This unit/task covers the following:
• Perform vessel handling duties
• Steer the vessel
Range: Maps, charts, Global Positioning System (GPS), compass, other navigation aids,
vessel, simulator, Standard Operating Procedures (SOP), computer, projector,
worksheets, stationery etc.
Performance Criteria(PC) w.r.t. the Scope
Element Performance Criteria
Perform vessel
handling duties
To be competent, the user/ individual must be able to:
PC1. prepare vessel coastal berthing schedule based on input from officer and
port/ terminal, factoring in tides
PC2. prepare vessel route map in inland waterways and identify key landmarks and
markers for navigation
PC3. check with deck staff regarding mooring lines and cargo clearance prior to
berthing and drafting
PC4. read and report observations in gyro compass and magnetic compass
PC5. identify the cardinal, inter-cardinal points and by points
Steer the vessel To be competent, the user/ individual must be able to:
PC6. convert reading of degrees to points and vice versa
PC7. repeat helm orders and take action per the helm orders given
PC8. confirm that the helm orders are carried out
PC9. change from automatic steering to manual steering and vice versa when
required
PC10. steer a steady course with smooth alternation in course with utmost regard
for area of navigation
PC11. keep a look out for various landmarks and mile marks in the inland rivers and
estuaries to keep track of course
PC12. steer safely in bending and narrow channels factoring current, bank cushions,
bank suctions,
PC13. take precautions while steering with regarding currents when performing
staying the bend and hugging the point and heading into current
Knowledge and understanding (K)
A. Organizational context (Knowledge of the company /organization and its processes)
The individual on the job needs to know:
KA1. organizational procedures and SOPs for tasks at hand, documentation policy
and emergency responses, internal communication over network
KA2. security and safety procedures to be followed
KA3. reporting structure of the organization for escalation of issues
KA4. risk and impact of not following defined procedures/work instructions
KA5. coding system followed to communicate using flags, hand signals and sound
signals
B. Technical
knowledge
The individual on the job needs to know and understand:
KB1. nautical terms and parts of ship
KB2. capacities of various holds and cargo types for different vessels
KB3. loading and discharge procedure for cargo handling in different type of
vessels
KB4. reading various navigational devices like gyrometer, magnetic compass, GPS
KB5. navigation aids like maps, charts, instruments etc.
KB6. ocean currents and their effects on the vessel, starboard side and port side
KB7. navigation through narrow channels, shallow channels, coastal areas, etc.
KB8. basic of steering wheels, degrees and points
Skills (S)
C. Core skills/
generic skills
Reading skills
The user/individual on the job needs to know how to read:
SA1. written instructions
SA2. maps and routes
Writing skills
The user/individual on the job needs to know how to:
SA3. write instructions based on observation
SA4. daily reports indicating damages, injuries, etc.
Oral communication (listening and speaking skills)
The user/individual on the job needs to know how to:
SA5. communicate with officers, master, terminal authorites and co-workers
SA6. collect information from masters and officers
D. Professional
skills
Decision making
The user/individual on the job needs to know how to:
SB1. decide the speed and rudder requirement for a certain navigational course
SB2. decide based on observation if an obstacle can be avoided or a course
correction is required
SB3. Decide on course corrections based on visible landmarks and mile marks
Plan and organize
The user/individual on the job needs to know how to:
SB4. plan and estimate the time for each activity
SB5. maintain punctuality and should respond to the queries in a timely manner
SB6. prioritize and execute tasks based on instructions
SB7. be a team player and achieve joint goals
Customer centricity
The user/individual on the job needs to know and understand:
SB8. importance of timely circulation of information
SB9. urgency of priority requests as per the instructions
Problem solving
The user/individual on the job needs to know how to:
SB10. inform the ranking in-charge regarding course correction, adverse
observations, etc.
SB11. suggest route correction to avoid collision, based on navigational buoys, etc.
Analytical thinking
The user/individual on the job needs to know how to:
SB12. analyse the effect of currents and water levels
SB13. assess the speed and torque requirement based on navigational routes
Critical thinking
The user/individual on the job needs to know how to:
SB14. observe and make course corrections based on adverse weathers,
unfavourable currents, obstacles, dangerous operations, etc.
SB15. observe effect of environment and make speed and rudder corrections
SB16. focus on task at hand and complete it without errors and delays
Cargo facilitation during loading and discharge
Description This unit is about facilitating loading and discharge of cargo as well as monitoring of
cargo
Scope This unit/task covers the following:
• Undertake stowing of cargo
• Ensure cargo safety and security after storage
Range: Vessel, sample cargo, Material Handling Equipment (MHE), Personal
Protective Equipment (PPE), safety equipment, cargo documentation, computer,
projector, worksheets etc.
Performance Criteria(PC) w.r.t. the scope
Element Performance Criteria
Undertake
stowing of cargo
To be competent, the user/ individual must be able to:
PC1. provide details of capacities of cargo from the manifest to the chief officer
PC2. assist chief officer in preparing the loading plan, based on details of cargo to
be discharged and loaded as per cargo manifest
PC3. assist chief officer in carrying out vessel stability assessment
PC4. check that the cargo does not infringe load-line regulation while on passage
PC5. check that heavy cargo is stored beneath the light cargo
PC6. inspect the cargo space for cleanliness, damage and presence of lighting and
ventilation
PC7. check that the cargo does not touch the spar ceiling
PC8. clean the dunnage
PC9. stow the cargo with the help of rigged derrick, hoist or cranes as required
PC10. get approval on documents of specific cargoes such as hazardous, livestock,
etc. from the chief officer
PC11. stow all the cargo and securely lash it using wire ropes and chains
PC12. document details of damaged cargo and highlight to master
Ensure cargo
safety and
security after
storage
To be competent, the user/ individual must be able to:
PC13. check that all listed cargo are loaded/ discharges
PC14. do an inventory count of cargo and give a sign off to the master/ chief officer
PC15. check that all cargo are tightly secured and lashed from all sides
PC16. check that cargo containers, boxes, etc. do not move during operations
PC17. check that hazardous cargo is kept segregated with all necessary precautions
PC18. perform regular monitoring of cargo during voyage for damages,
displacements, thefts, etc.
Knowledge and understanding (K)
A. Organizational context (Knowledge of the company /organization and its processes)
The individual on the job needs to know:
KA1. organizational procedures and Standard Operating Procedures (SOPs) for
tasks at hand, documentation policy and emergency responses, internal
communication over network
KA2. security and safety procedures to be followed
KA3. reporting structure of the organization for escalation of issues
KA4. risk and impact of not following defined procedures/work instructions
KA5. coding system followed to communicate using flags, hand signals and sound
signals
B. Technical
knowledge
The individual on the job needs to know and understand:
KB1. detailed information contained in Code of Safe Practice for Cargo Stowage
and Securing (CSS Code)
KB2. basic operation of Material Handling Equipment (MHEs) in vessel and port
KB3. usage of communication equipment such as Very High Frequency (VHF) radio
etc.
KB4. blocking, lashing, shoring, chocking and tombing of cargo
KB5. use of different material handling equipment and their uses
KB6. method of securing heavy load
KB7. method of stowing vehicles and trailers
KB8. safe loading/ discharging of ro-ro cargoes
KB9. limitation of lifting gear and knowledge of limit switches
KB10. capacities of various holds and cargo types for different vessels
KB11. loading and discharge procedure for cargo handling in different type of
vessels
Skills (S)
C. Core skills/
generic skills
Reading skills
The user/individual on the job needs to know how to read:
SA1. written instructions
SA2. shipping manifest, shipping bills, cargo documentation, etc.
SA3. cargo labels and markings
SA4. maps and routes
Writing skills
The user/individual on the job needs to know how to:
SA5. write instructions
SA6. daily reports indicating damages, injuries, accidents, cargo thefts, etc.
Oral communication (listening and speaking skills)
The user/individual on the job needs to know how to:
SA7. communicate with masters, port loading authorties and co-workers
SA8. collect information from masters and officers
D. Professional Decision making
The user/individual on the job needs to know how to:
SB1. idenitfy faulty rigs, ladders, loading and unlaoding equipment
SB2. decide the loading procedure for the cargo
SB3. identify damaged cargo and containers
Plan and organize
The user/individual on the job needs to know how to:
SB4. plan and estimate the time for each activity
SB5. maintain punctuality and respond in a timely manner
SB6. prioritize and execute tasks based on instructions
SB7. be a team player and achieve joint goals
Customer centricity
The user/individual on the job needs to know and understand:
SB8. importance of timely circulation of information
SB9. urgency of priority requests as per the instructions
Problem solving
The user/individual on the job needs to know how to:
SB10. inform the ranking in-charge in case of damamged cargo
SB11. suggest methods for safe stowage and lashing of cargo
Analytical thinking
The user/individual on the job needs to know how to:
SB12. analyse common mistakes during cargo operations and take due precuations
SB13. analyse commonly carried cargo trend and make deck adjustments for easier
loading
Critical thinking
The user/individual on the job needs to know how to:
SB14. observe and communicate regarding damaged cargo
SB15. ensure safety udring cargo operations
SB16. focus on task at hand and complete it without errors and delays
On-board training of crew members for deck operations
Description This unit is about on-board training of crew members for deck operations
Scope This unit/task covers the following:
• Training for navigation
• Training for store handling
• Check cargo organization and security
Range: Navigation charts and aids, Personal Protective Equipment (PPE), Standard
Operating Procedures (SOP), Management information system (MIS) reports,
computer, projector, stationery, worksheets etc.
Performance Criteria(PC) w.r.t. the scope
Element Performance Criteria
Training for
navigation
To be competent, the user/ individual must be able to guide the deck crew to:
PC1. take watch and report from bridge
PC2. use different hand signals and flag signals
PC3. understand and comprehend navigational terms
PC4. read gyro and magnetic compass and adjust for errors
PC5. take helm orders and steer the ship using degrees and points
PC6. take necessary precautions while steering and watch regarding weathers,
obstacles, currents, landmarks, etc.
PC7. mooring and docking the vessel at terminals
Training for store
handling
To be competent, the user/ individual must be able to guide the deck crew to:
PC8. take precautions and measures to keep store rodent free
PC9. appropriately store different items – food, water, liquids, spares, equipment,
cash, etc.
PC10. inspect store, take inventory count and update
PC11. manage cold storage and store equipment
PC12. track threshold levels for raising replacement/ shortage requests
PC13. check document prior to releasing an item from store
Check cargo
organization and
security
To be competent, the user/ individual must be able to guide the deck crew to:
PC14. check that all listed cargo are loaded/ discharged and do inventory counts
PC15. check storage pattern and lashing of cargo
PC16. check that hatches and holds are secured
PC17. take precautions while handling cargo particularly hazardous cargo
PC18. check for damage to cargo during transit and loading operations
Knowledge and understanding (K)
A. Organizational context (Knowledge of the company /organization and its processes)
The individual on the job needs to know:
KA1. organizational procedures and SOPs for tasks at hand, documentation policy
and emergency responses, internal communication over network
KA2. security and safety procedures to be followed
KA3. reporting structure of the organization for escalation of issues
KA4. risk and impact of not following defined procedures/work instructions
KA5. coding system followed to communicate using flags, hand signals and sound
signals
B. Technical
knowledge
The individual on the job needs to know and understand:
KB1. detailed information contained in Code of Safe Practice for Cargo Stowage
and Securing (CSS Code)
KB2. blocking, lashing, shoring, chocking and tombing of cargo
KB3. use of different material handling equipment and their uses
KB4. method of securing heavy load
KB5. method of stowing vehicles and trailers and loading and discharge of ro-ro
cargo
KB6. performing watch duty and cargo handling on the vessel
KB7. handling and steering of vessel
KB8. maintaining of stores and inventory onboard the vessel
KB9. loading and discharge procedure for cargo handling in different type of
vessels
Skills (S)
C. Core skills/
generic skills
Reading skills
The user/individual on the job needs to know how to read:
SA1. written instructions
SA2. maps and routes
SA3. shipment manifest, shipping bills, cargo documentation, etc
SA4. inventory counts and records
Writing skills
The user/individual on the job needs to know how to:
SA5. write instructions
SA6. deliver presentations and classes
SA7. write daily reports
Oral communication (listening and speaking skills)
The user/individual on the job needs to know how to:
SA8. communicate with officers, masters and co-workers
SA9. collect information from masters
D. Professional
skills
Decision making
The user/individual on the job needs to know how to:
SB1. decide on cases and specific instances that needs to be highlighted during
training
SB2. decide basic precuations that need to be emphasized during training
SB3. identify order of acitivities for training
Plan and organize
The user/individual on the job needs to know how to:
SB4. plan and estimate the time for each activity
SB5. maintain punctuality and respond in a timely manner
SB6. prioritize and execute tasks based on instructions
SB7. be a team player and achieve joint goals
Customer centricity
The user/individual on the job needs to know and understand:
SB8. importance of timely circulation of information
SB9. catering to urgencies and priority requests as per the instructions
Problem solving
The user/individual on the job needs to know how to:
SB10. identify new and innovative ways for on job training
SB11. suggest interactive methods and tasks for enforcing learning
Analytical thinking
The user/individual on the job needs to know how to:
SB12. analyse the usual challenges in learning based on past expereince and prvide
higher focus on the same
Critical thinking
The user/individual on the job needs to know how to:
SB13. adjust based on the intellect of each deck hand to provide effective learning
SB14. explain precuations and risks of not following the same onboard the vessel
Supervise engine operation and troubleshooting
Description This unit is about engaging into basic deck operations and assistance
Scope This unit/task covers the following:
• Supervise engine room operations
• Undertake troubleshooting duties
• Perform documentation
Range: Engine equipment, simulator, tools and tackles, equipment manuals, Standard
Operating Procedures (SOP), computer, projector, stationery, worksheets etc.
Performance Criteria(PC) w.r.t. the Scope
Element Performance Criteria
Supervise engine
room operations
To be competent, the user/individual on the job must be able to:
PC1. carry out orders given by duty engineer
PC2. assign duties and manage the engine room staff
PC3. monitor the safe running of the machinery with respect to various operational
parameters
PC4. check that instruments and their reading to see functioning of the main and
auxiliary engines
PC5. prepare for hot and cold start
PC6. follow SOPs and safety precautions for operating the generator and main
engine during different weather conditions and operations
PC7. record all tank parameters for sludge and bilge system
PC8. implement Planned maintenance system (PMS)
PC9. conduct regular inspection of engine and auxiliary machinery for fitness and
maintenance needs
PC10. inspect equipment in SOEP (Shipboard oil pollution emergency plan) locker
for functionality and fitness
PC11. supervise engine crew during routine maintenance and basic repairs as
instructed by duty engineer/ master
PC12. keep the engine room bilge clean of oil and oily water
PC13. take precautions to prevent oil spills and accidents during bunkering of fuel
and oil
PC14. store all spares properly and maintain the record in the spares inventory
Undertake
troubleshooting
duties
To be competent, the user/individual on the job must be able to:
PC15. assist the crew with maintenance and repair duties bunkering of fuel and oil
PC16. check all fuel rack incase engine rpm is fluctuating
PC17. check the temperature of the airline for any leakage from air valve
PC18. overhaul and test pressure of fuel valve in case there is deviation in
temperature of fuel system
PC19. frequently clean exhaust gas boiler to avoid sparks in the main engine
PC20. use cooling to prevent overheating of engine block
PC21. replace faulty gauges, that are not working due to lose connections
PC22. fabricate engine replacement parts such as valves, stay rods, bolts using metal
and working machinery
PC23. repair engine, electric motor, pumps and other mechanical and electrical
equipment
Perform
documentation
To be competent, the user/individual on the job must be able to:
PC24. record data in the log book, bell book, weekly routine book
PC25. maintain and update inventory count of spares for the engine room like
pumps, auxiliary engine, etc. regularly
PC26. record details of quantity of oil in the tanks for machinery operation like lube
oil, fuel or diesel in the oil record book
PC27. make record of the next bunker order
PC28. update and maintain Planned Maintenance System (PMS) book
Knowledge and understanding (K)
A. Organizational
context
The individual on the job needs to know:
KA1. organizational procedures and SOPs for tasks at hand, documentation policy
and emergency responses, internal communication over network
KA2. security and safety procedures to be followed
KA3. reporting structure of the organization for escalation of issues
KA4. risk and impact of not following defined procedures/work instructions
KA5. coding system followed to communicate using flags, hand signals and sound
signals
B. Technical
knowledge
The individual on the job needs to know and understand:
KB1. various types of valves and the major components of engine and auxiliary
units
KB2. safe operating procedure for opening and closing of valve
KB3. types of pumps in engine room
KB4. precaution before starting a pump and during its operation
KB5. types of joints used for pipeline
KB6. precaution to be taken before commencing repair work
KB7. different types of oil and air filters used on board and their cleaning and
maintenance SOPs
KB8. hazards of cleaning filter on a running machinery
KB9. PPEs, safety precautions, emergency plans, escape routes, etc.
KB10. use of propelling and shafting
KB11. different type of fuel systems and engine room machineries
KB12. preservation of equipment in good condition
KB13. preparation needed for starting an auxiliary diesel engine
KB14. checks to made on an operating auxiliary engine
KB15. risk involved in working with compressed air for auxiliary purpose
C. Core skills/
generic skills
Reading skills
The user/individual on the job needs to know how to read:
SA1. written instructions
SA2. vessel layout and operating procedures
SA3. SOPs and engine operations manual and tool books
SA4. pressure gauges and level gauges
Writing skills
The user/individual on the job needs to know how to write:
SA5. daily reports including inventory, damages, repairs, maintenance, accidents,
etc.
SA6. instructions for crew
Oral communication (listening and speaking skills)
The user/individual on the job needs to know how to:
SA7. communicate with officers, masters and co-workers
SA8. collect information from officers and masters
D. Professional skills Decision making
The user/individual on the job needs to know how to:
SB1. idenitfy if there is a need for repair or servicing of engine
SB2. identify issues in operation based on reading of various parameters, listening
to noise and abrupt movements
SB3. decide if there is need for shutting down the engine and overhauling
Plan and organize
The user/individual on the job needs to know how to:
SB4. plan and estimate the time for each activity
SB5. maintain punctuality and respond to queriesin a timely manner
SB6. prioritize and execute tasks based on instructions
SB7. be a team player and achieve joint goals
Customer centricity
The user/individual on the job needs to know and understand:
SB8. importance of given timelines
SB9. urgency of priority requests as per the instructions
Problem solving
The user/individual on the job needs to know how to:
SB10. check and ensure proper functioning of various engine and auxiliary units
SB11. identify need for basic troubleshooting or engine overhauling
SB12. perform basic repairs, fitting, etc on engine components
Analytical thinking
The user/individual on the job needs to know how to:
SB13. verify the authenticity of the spare parts by conducting basic checks
SB14. analyse common issues with engine and take precautions
Critical thinking
The user/individual on the job needs to know how to:
SB15. focus on task at hand ad complete it without errors and delays
SB16. check for compliance regarding filling forms for replacement or servicing of
equipment
SB17. check and identify problems in engine functioning
SB18. identify hazardous situations and initiate appropriate action
SB19. ensure proper precautions are taken during overhauling
Assist in overhauling of engine and auxiliary equipment
Description This unit is about overhauling main engine and other auxilaryequipment
Scope This unit/task covers the following:
• Assist in overhauling of main engine
• Assist in overhauling of auxiliary equipment
Range: Engine and associated equipment, tools and tackles, maintenance equipment,
equipment manual, Standard Operating Procedures (SOP), computer, projector, stationery,
worksheets etc.
Performance Criteria(PC) w.r.t. the Scope
Element Performance Criteria
Assist in
overhauling of
main engine
To be competent, the user/individual on the job must be able to:
PC1. check for safety devices on the main engine and the auxiliary engine
PC2. check for issues with respect to noise, various measuring gauges, moving parts to
identify the need for repair and overhaul
PC3. inform the master or officer on duty regarding need for overhauling and get
permission
PC4. check that the main engine is shut off and secured from hazards with respect to fuel
leak, oil leak, heat, etc. prior to overhauling
PC5. check that the SOP and necessary precautions are followed for overhauling of engine
PC6. continually monitor the engine readings during overhauling operations by the
technical team
PC7. assist the technical team to clarify doubts
Assist in
overhauling of
auxiliary
equipment
To be competent, the user/individual on the job must be able to:
PC8. open and close valves for operation using tools like wheel spanner, etc. as per SOPs
PC9. use drain valves and drain cocks draining fluids from air bottles, oil and fuel tanks,
pipes, etc.
PC10. check tanks and level gauges
PC11. open pumps, valves and pipes as per SOP
PC12. safely open ballast system of vessel when required
PC13. perform basic pumping system cleaning and trouble shooting
PC14. open auxiliary units like filters, centrifugal separators, joints and glade packing, etc.
for cleaning and overhauling
PC15. perform basic maintenance and troubleshooting when required as per the
overhauling SOP
Knowledge and understanding (K)
A. Organizational
context
The individual on the job needs to know:
KA1. organizational procedures and SOPs for tasks at hand, documentation policy and
emergency responses, internal communication over network
KA2. security and safety procedures to be followed
KA3. reporting structure of the organization for escalation of issues
KA4. risk and impact of not following defined procedures/work instructions
KA5. coding system followed to communicate using flags, hand signals and sound signals
B. Technical
knowledge
The individual on the job needs to know and understand:
KB1. various types of valves and the major components
KB2. safe operating procedure for opening and closing of valve
KB3. identify various types of valves, pumps and cocks used for shipboard application,
their components, usage and SOP for overhauling
KB4. types of pumps in engine room
KB5. precaution before starting a pump
KB6. types of joints used for pipeline
KB7. precaution to be taken before commencing repair work
KB8. different types of oil and air filters used on board
KB9. hazards of cleaning filter on a running machinery
KB10. PPE to be worn during cleaning or repairing various equipment
KB11. checks to be made on a filter during cleaning
KB12. use of propelling and shafting
KB13. preservation of equipment in good condition
KB14. preparation needed for starting an auxiliary diesel engine
KB15. checks to made on an operating auxiliary engine
KB16. components of main engine
KB17. risk involved in working with compressed air for auxiliary purpose
Skills (S)
A. Core skills/
generic skills
Reading skills
The user/individual on the job needs to know how to read:
SA1. written instructions
SA2. vessel layout and operating procedures
SA3. SOPs and engine operations manual and tool books
SA4. pressure gauges and level gauges
Writing skills
The user/individual on the job needs to know how to write:
SA5. daily reports including inventory, damages, repairs, maintenance, accidents, etc.
SA6. instructions for crew
Oral communication (listening and speaking skills)
The user/individual on the job needs to know how to:
SA7. communicate with officers, masters and co-workers
SA8. collect information from officers and masters
B. Professional Decision making
The user/individual on the job needs to know how to:
SB1. idenitfy if there is a need for overhauling
SB2. identify the machine or system that needs to be overhauled
Plan and organize
The user/individual on the job needs to know how to:
SB3. plan and estimate the time for each activity
SB4. maintain punctuality and respond to queriesin a timely manner
SB5. prioritize and execute tasks based on instructions
SB6. be a team player and achieve joint goals
Customer centricity
The user/individual on the job needs to know and understand:
SB7. importance of given timelines
SB8. urgency of priority requests as per the instructions
Problem solving
The user/individual on the job needs to know how to:
SB9. identify need for basic troubleshooting or engine overhauling
SB10. perform basic overhauling of auxiliary units and parts as per SOP
Analytical thinking
The user/individual on the job needs to know how to:
SB11. analyse common issues with engine and take precautions while overhauling
Critical thinking
The user/individual on the job needs to know how to:
SB12. focus on task at hand ad complete it without errors and delays
SB13. identify hazardous situations and initiate appropriate action
SB14. ensure proper precautions are taken during overhauling
On-board training of crew members for engine operations
Description This unit is about on-board training of crew members for engine operations
Scope This unit/task covers the following:
• Training for engine operation supervision
• Training for engine and part overhauling
• Training for welding, cutting and machining
Range: Engine and associated equipment, tools and tackles, maintenance equipment,
equipment manual, Standard Operating Procedures (SOP), computer, projector,
stationery, worksheets etc
Performance Criteria(PC) w.r.t. the scope
Element Performance Criteria
Training for engine
operation
To be competent, the user/individual on the job must be able to guide crew to:
PC1. take precautions regarding possible risks associated with engine operations
related to chemical, thermal, oil spills, bunkering of fuel, etc.
PC2. operate and maintain lifesaving and firefighting appliance
PC3. monitor safe running of machinery and recording of tank and engine
parameters
PC4. usage of various tools, tackles and maintenance equipment
PC5. perform routine maintenance and basic troubleshooting
PC6. keep the engine room bilge clean of oil and oily water
PC7. record all tank parameters and read related instruments
Training for engine
and part overhauling
To be competent, the user/individual on the job must be able to guide crew to:
PC8. follow safety precautions and SOPs when overhauling
PC9. check for safety devices on the main engine and the auxiliary engine
PC10. check that instruments and their reading to see functioning of the main and
auxiliary engines
PC11. check tank levels and gauges and draw inferences
PC12. detailed engine dismantling, over hauling and assembling procedure
PC13. open ballast systems and trouble shoot pumping system
Training for welding,
cutting and
machining
To be competent, the user/individual on the job must be able to guide the crew to:
PC14. take necessary precautions while using tools
PC15. identify the right tool for different requirements
PC16. use the tool in the right way with all necessary precautions and SOPs
PC17. perform checklist of precautions before welding
PC18. safe stowage of maintenance equipment and disposal of maintenance wastes
Knowledge and understanding (K)
E. Organizational context (Knowledge of the company /organization and its processes)
The individual on the job needs to know:
KA1. organizational procedures and SOPs for tasks at hand, documentation policy
and emergency responses, internal communication over network
KA2. security and safety procedures to be followed
KA3. reporting structure of the organization for escalation of issues
KA4. risk and impact of not following defined procedures/work instructions
KA5. coding system followed to communicate using flags, hand signals and sound
signals
B. Technical
knowledge
The individual on the job needs to know and understand:
KB1. various types of valves and the major components
KB2. safe operating procedure for opening and closing of valve
KB3. identify various types of valves, pumps and cocks used for shipboard
application, their components, usage and SOP for overhauling
KB4. types of pumps in engine room
KB5. precaution before starting a pump
KB6. types of joints used for pipeline
KB7. precaution to be taken before commencing repair work
KB8. different types of oil and air filters used on board
KB9. hazards of cleaning filter on a running machinery
KB10. PPE to be worn during cleaning or repairing various equipment
KB11. checks to be made on a filter during cleaning
KB12. use of propelling and shafting
KB13. preservation of equipment in good condition
KB14. preparation needed for starting an auxiliary diesel engine
KB15. checks to made on an operating auxiliary engine
KB16. components of main engine
KB17. risk involved in working with compressed air for auxiliary purpose
Skills (S)
C. Core skills/
generic skills
Reading skills
The user/individual on the job needs to know how to read:
SA1. written instructions
SA2. maps and routes
SA3. operating manuals and SOPs
SA4. inventory counts and records
Writing skills
The user/individual on the job needs to know how to:
SA5. write instructions
SA6. deliver presentations and classes
SA7. write daily reports
Oral communication (listening and speaking skills)
The user/individual on the job needs to know how to:
SA8. communicate with officers, masters and co-workers
SA9. collect information from masters
D. Professional skills Decision making
The user/individual on the job needs to know how to:
SB1. decide on cases and specific instances that needs to be highlighted during
training
SB2. decide basic precuations that need to be emphasized during training
SB3. identify order of acitivities for training
Plan and organize
The user/individual on the job needs to know how to:
SB4. plan and estimate the time for each activity
SB5. maintain punctuality and respond in a timely manner
SB6. prioritize and execute tasks based on instructions
SB7. be a team player and achieve joint goals
Customer centricity
The user/individual on the job needs to know and understand:
SB8. importance of timely circulation of information
SB9. catering to urgencies and priority requests as per the instructions
Problem solving
The user/individual on the job needs to know how to:
SB10. identify new and innovative ways for on job training
SB11. suggest interactive methods and tasks for enforcing learning
Analytical thinking
The user/individual on the job needs to know how to:
SB12. analyse the usual challenges in learning based on past expereince and prvide
higher focus on the same
Critical thinking
The user/individual on the job needs to know how to:
SB13. adjust based on the intellect of each deck hand to provide effective learning
SB14. explain precuations and risks of not following the same onboard the vessel
Manage tug vessel operations
Description This unit is about performing tug vessel operations
Scope This unit/task covers the following:
• Preparing for towing operation
• Towing of vessel
Range: Tug vessel and towing equipment cum accessories, navigational aids,
simulator, computer, projector, stationery, worksheets, etc.
Performance Criteria(PC) w.r.t. the Scope
Element Performance Criteria
Preparing for towing
operation
To be competent, the user/individual on the job must be able to:
PC1. check the engine and power systems of tug boat for fitness with respect to
operations and regulatory compliance
PC2. check that the crew is certified for tug operations and have the requisite
Personal Protective Equipment (PPEs)
PC3. check that the towing gear and equipment – bollard, fairleads, sheaves, wires
and ropes, etc. are in good condition and functional
PC4. check that the towing equipment and vessel are suitable for towing the vessel
PC5. prepare tow plan identifying the route to taken and planned passage
including safe time of operation during day and night; factor in obstacles,
traffic, weather conditions, adjacent river and coastal berths, tight bends, tug
connection to be used, etc.
PC6. check for presence of sufficient fuel, water and spares on board
PC7. check for navigational information and warnings
PC8. identify the Bollard Pull (BP), the width and size of vessel to calculate the
displacement and the speed for tug operations
PC9. identify the pivot point for towing based on currents, weather, etc. for safe
and stable towing of the vessel
PC10. estimate the position of tug vessel with respect to the towed vessel factoring
in the no. of tugs, pivot point, speed of towing, etc.
PC11. estimate the number of tows required and the towing position based on the
number of vessel and barges to be towed together
Towing the vessel
PC12. check that all emergency equipment and emergency plan is in place
PC13. check that all watertight hatches and doors are closed
PC14. provide instructions to crew as per the towing plan
PC15. check for stability of both vessels prior to commencement of operation
PC16. move the tug vessel to the aft or forward point of the vessel to be towed
factoring in the speed and suction for securing the tugs
PC17. check with crew if the tug is connected and secured
PC18. carefully start the tug vessel and apply power to displace water for moving
the vessel to be towed, taking precautions against the water currents, girting,
top-sizing, capsizing, etc.
PC19. adjust for obstacles, wind speed and currents, traffic factoring the girting,
vessel speed, etc.
PC20. regularly check during operations if the towing arrangement and watertight
integrity of the tow are satisfactory
PC21. prepare for and address emergency towing scenarios as per the emergency
towing SOP in case of loss of tow wire
PC22. navigate the towed vessel to the destination and slowly brake factoring the
vessel inertia to prevent capsizing or girting
PC23. dis-engage the tow from the vessel
Knowledge and understanding (K)
A. Organizational
context
The individual on the job needs to know:
KA1. organizational procedures and SOPs for tasks at hand, documentation policy
and emergency responses, internal communication over network
KA2. security and safety procedures to be followed
KA3. reporting structure of the organization for escalation of issues
KA4. risk and impact of not following defined procedures/work instructions
KA5. coding system followed to communicate using flags, hand signals and sound
signals
B. Technical
knowledge
The individual on the job needs to know and understand:
KB1. different type of tug boats and their operations
KB2. different type of tug connections – hawser based, Integrated unit, articulated
unit, etc. and their benefits
KB3. use of different tug equipment – bollards, fairleads, sheaves, wires, tow
connections, etc. and their uses
KB4. effect of ocean and river currents, weather, suction from towed vessel and
other environmental factors that can impact towing of vessel
KB5. responsibility, manning, certification and training of tug vessel and crew
KB6. use of PPEs, making tow plans and emergency plans and SOP for
contingencies
KB7. mooring operating using tug vessels
KB8. understanding of vessel safety during tug, girting, pivot points, Bollard pull,
position for vessel towing, displacement and speed calculations, etc.
KB9. coastal and inland navigational routes for tug vessels and their limitations
Skills (S)
C. Core skills/
generic skills
Reading skills
The user/individual on the job needs to know how to read:
SA1. written instructions
SA2. maps and routes
SA3. SOPs and operating manuals
SA4. messages on various communication systems
Writing skills
The user/individual on the job needs to know how to:
SA5. write instructions
SA6. write daily reports
Oral communication (listening and speaking skills)
The user/individual on the job needs to know how to:
SA7. communicate with officers, port terminals, other vessels and co-workers
SA8. collect information from officers
D. Professional skills Decision making
The user/individual on the job needs to know how to:
SB1. decide on the navigation route and speed for vessels
SB2. decide on the work allotlment of crew on board
Plan and organize
The user/individual on the job needs to know how to:
SB3. plan and estimate the time for each activity
SB4. maintain punctuality and respond in a timely manner
SB5. prioritize and execute tasks based on instructions
SB6. be a team player and achieve joint goals
Customer centricity
The user/individual on the job needs to know and understand:
SB7. importance of timeliness for operations and circulation of information
SB8. urgency of priority requests as per the instructions
Problem solving
The user/individual on the job needs to know how to:
SB9. inform the ranking in-charge regarding adverse observations in engine,
navigation route, obstacles, etc.
SB10. suggest make shift arrangements, trouble shooting, route alterations, etc.
Analytical thinking
The user/individual on the job needs to know how to:
SB11. analyse the position of a vessel or obstacle on the map and its estimated
route
SB12. analyse the speed and torque for a certain tug operation based on vessel size
and terrain of river/ ocean bed
Critical thinking
The user/individual on the job needs to know how to:
SB13. observe obstacles and dangerous operations by other vessels and take
precautions
SB14. assess weather and environment for performing a tug operation
SB15. focus on task at hand and complete it without errors and delays
Profit and Loss Account management and cost accounting
Description This unit is about about Profit and loss account management and cost accounting
Scope This unit/task covers the following:
• Profit and loss account management and review
• Analysis of activity based costs
Range: Computers, Management information system (MIS), Enterprise Resource
Planning (ERP), performance review softwares
Performance Criteria(PC) w.r.t. the Scope
Element Performance Criteria
Profit and Loss
account
management and
review
To be competent, the user/ individual must be able to:
PC1. review department wise budgets and make amendments if required
PC2. collate and prepare annual budgets along with sales and profit targets
PC3. schedule both capital and operational expenses accordance to the budget
PC4. analyze and review the P&L performance for the unit
PC5. analyze profitability and business performance trends department wise
PC6. periodically analyze variances in the expenditure with respect to the budget
and accordingly take corrective actions
PC7. periodically analyze the physical output and performance with respect to the
budget and identify places for improvements
PC8. undertake adequate risk management so as to meet Key Performance targets
PC9. manage and control budgets of different departments on a periodic basis to
optimize financial performance
Analysis of activity
based costs
PC10. periodically review activity and department financial performance
PC11. identify the activities having high variance with respect to the budgeted costs
or the forecasted revenue
PC12. analyze the actual cost w.r.t physical output to draw inferences
PC13. identify reasons in discussion with department and take remedial and
corrective actions where-ever required
PC14. work towards rationalizing the cost of the activity wise operations to achieve
higher financial goals
Knowledge and understanding (K)
A. Organizational
context
(Knowledge of
the company /
organization
and its
processes)
The individual on the job needs to know and understand:
KA1. vision, mission and values of the company
KA2. company’s reporting structure to support and expedite project activities
KA3. company’s policy and work instructions on quality standards as well as
documentation policy
KA4. importance of the individual’s role in the workflow
KA5. company’s policy on business ethics and code of conduct
KA6. business and performance of the company
KA7. knowledge repository and various projects done by the company
KA8. occupational health and safety standards, handling of special and dangerous
goods, etc.
KA9. procedures for dealing with loss or damage to goods
KA10. value of items handled and implications of damage/loss of the same
KA11. risk and impact of not following defined work, safety and security procedures
KA12. company policy defined TATs and output metrics for daily operations
KA13. coding system followed to label items
KA14. IT system and ERP system of the organization
KA15. organizational goal for the year as well as branch/ territory targets
B. Technical
knowledge
The user/individual on the job needs to know and understand:
KB1. process flow of service operation and understanding of basic supply chain
value chain
KB2. state/country taxes and routing
KB3. local and global geographies
KB4. use of enterprise resource planning software (ERP) and the MIS
KB5. use of tools for documentation: MS excel and MS Word, etc.
KB6. basics of statistical and quantitative analysis tools
KB7. use of spreadsheets to tabulate and analyze the data
KB8. structure and implications of fees and charges involved in transportation,
warehousing, processing clearances, etc.
KB9. transit rules and regulations
KB10. working and capacities of different MHEs and other equipment used for
handling the shipment
KB11. procurement related concepts like Purchase order (PO), Invoices, procedures
etc.
KB12. significance of team coordination to achieve revenue and productivity targets
of the organization
KB13. various techniques for performance improvement and cost accounting
KB14. budgeting exercises
Skills (S)
A. Core skills/
generic skills
Reading skills
The user/individual on the job needs to know how to read:
SA1. company’s work instructions, customer requirement and quality policy
SA2. egal policies and regulations
SA3. internal communications memorandums
SA4. written instructions, standard operating procedures
SA5. SOPs and documents required for all operational activities
SA6. inferences drawn from the system reports
SA7. financial statements
Writing skills
The user/individual on the job needs to know how to:
SA8. maintain the record of as per company’s policy
SA9. make the note of instructions to team members
SA10. develop operating procedures and update them
SA11. write communications, letters, etc.
SA12. prepare daily reports, checklists
SA13. prepare reports and presentations based on data analytics and ERP reports
Oral communication (listening and speaking skills)
The user/individual on the job needs to know how to:
SA14. communicate with client, external coordinators, internal staff effectively
SA15. motivate employees
SA16. share experiences and provide guidance to juniors and peers
B. Professional
skills
Decision making
The user/ individual on the job needs to know and understand how to:
SB1. assess business performance to identify need for interventions
SB2. identify areas for improvement and accordingly suggest remedial action
SB3. identify areas for budget modifications and budget cuts
SB4. decide on ways to improve performance
Plan and organize
The user/ individual on the job needs to know how to:
SB5. plan and organise performance review sessions
SB6. make action plan for performance improvement
SB7. organise projects/ training plans for performance improvement
SB8. monitor the activities of the performance improvement plan
Customer centricity
The user/ individual on the job needs to know how to:
SB9. sensitive employees towards customer requirements
SB10. focus on customer satisfaction as a key part of the performance review
Problem solving
The user/individual on the job needs to know how to:
SB11. identify reasons for variances and resolve them in discussion with team and
management
SB12. suggest new technologies, capital purchases, operational strategies to
enhance operational and financial performance
Analytical thinking
The user/individual on the job needs to know how to:
SB13. analyze reasons for variances across departments
SB14. compare with past trends to see if it is seasonal or cyclical in nature
SB15. identify areas that are crucial for improvement and accordingly revisit
budgets
Critical thinking
The user/individual on the job needs to know how to:
SB16. assess the financial performance and make strategic decisions regarding
budgets, focus areas
SB17. motivate and ensure output so as to achieve financial goals
Perform ship and yard planning
Description This unit is about about container tracking and developing vessel berthing plans
Scope This unit/task covers the following:
• Plan yard to receive cargo
• Inspect yard to check for space utilization, segregation of cargo, cleanliness,
necessary precautions
Range: Stationery, Standard Operating Procedures (SOP), Radio-Frequency
Identification (RFID )scanner, bar code scanner, markers, Personal Protective
Equipment (PPEs), Enterprise Resource Planning (ERP), computer, display board,
printer, Material Handling Equipment (MHEs), etc
Performance Criteria(PC) w.r.t. the Scope
Element Performance Criteria
Plan yard to receive
cargo
To be competent, the user/ individual must be able to:
PC1. obtain information regarding the vessel details – docking schedule and berth,
bays and containers to be unloaded and loaded
PC2. obtain information regarding movement of containers / cargo from port
terminals to Container Freight Stations (CFS)/ Inland Container Depots (ICD)
or client
PC3. check yard’s capacity utilization and open bays and locations
PC4. assess the quantity of cargo to be moved and plan storage space for cargo
PC5. allocate resources for cargo movement
PC6. communicate the task at hand to cargo equipment handlers, manual cargo
handlers and lifting and vessel supervisors
PC7. discuss the plan for cargo movement with the operators to finalize the
container/ cargo movement plan
PC8. review that all equipment and workforce is ready for operations at the time of
vessel docking / transport arrival
PC9. review that the necessary precautions and PPEs have been taken
PC10. deploy resources for loading/ unloading as per cargo stowage plan
PC11. coordinate with cargo surveyor for safe and secured loading/ unloading
Inspect yard to check
for space utilization,
segregation of cargo,
cleanliness,
necessary
precautions
To be competent, the user/ individual must be able to:
PC12. conduct periodic inspections of the yard
PC13. check for cleanliness, adequate use of PPEs, regulations and norms for
workforce are clearly followed
PC14. check that cargo bays are clearly marked and segregated, containers and
cargo are stored as per prescribed norms
PC15. check that equipment are parked are right positions
PC16. check that all necessary precautions for storage of hazardous cargo is in place