Material Handling Equipment (MHE)Operator and Technician (1 years diploma)
Material Handling Equipment (MHE)Operator and Technician click here
Brief Job Description
The individual operates MHE to move, load and unload cargo in a warehouse, undertakes basic
maintenance activities for MHE and prepares performance reports.
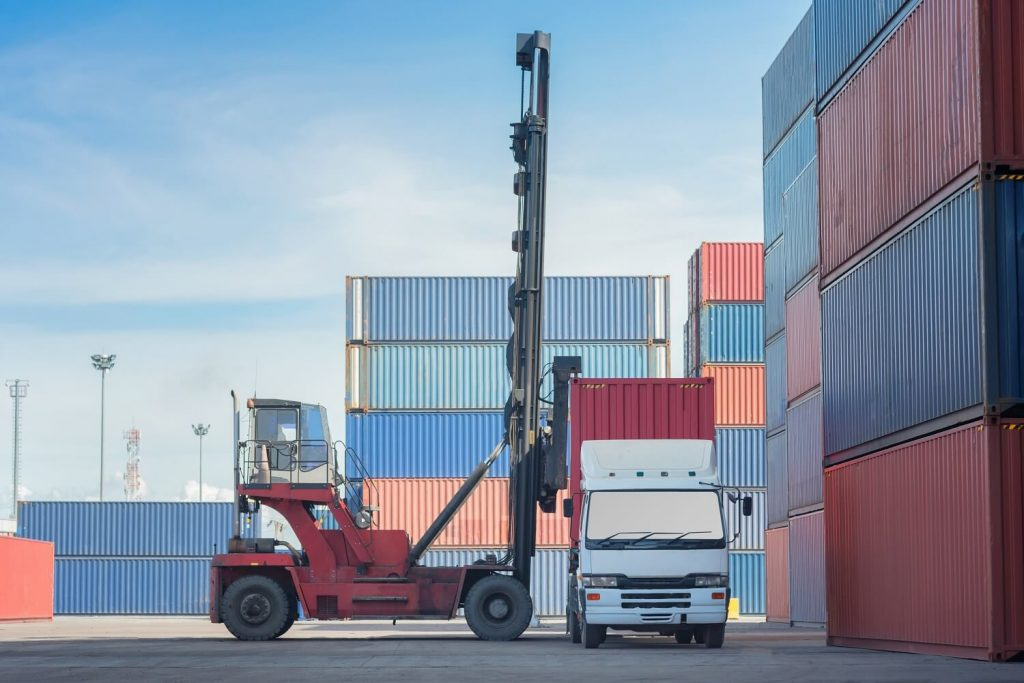
Personal Attributes
The job holder should be physically fit, judge distance and should have good eye-hand-foot coordination to drive MHE continuously for long hours. She/He must be able to prioritize and execute tasks within
scheduled time limits. She/he should have English and Vernacular language proficiency, demonstrable in
all written and oral communication.
Perform material handling activities
Description
This unit is about preparing and performing material handling activities
Scope
This unit/task covers the following:
Obtain work schedule and plan
Inspect and operate the Material Handling Equipment (MHE)
Report and document of MHE Range: Personal Protective Equipment (PPEs), Forklift, Reach stacker,
pallet truck, pallet jacks, hand trucks, side loader, order picker, walkie, stacker, etc.
Elements and Performance Criteria
Perform material handling activities
To be competent, the user/individual on the job must be able to:
PC9. assess the tooling requirement and collect the necessary tools from the tool crib/storage
racks
PC10. lift or move the pallet using the MHE and place correctly into specified location
PC11. check for damaged/spills transport goods to quarantine area and unload them for further
action
PC12. report supervisor if there are any issues such as count mismatch, breakage/ damage of
goods/ packaging during
PC13. check that movement of goods should be carried out as per standard operating procedures
(SOP)
PC14. check for safe and error free loading and unloading of the goods
PC15. park the MHE in specified location after completing the job
PC16. check for minor issues, technical issues, cleaning etc. w.r.t. MHE and inform supervisor
accordingly

PC17. report any delays, damages, accidents and other incidents to the supervisor
PC18. report on the condition of the MHE and any maintenance activity or replacement that may be
required to the supervisor
PC19. fill out forms such as damage to goods, insurance claims in accordance with company
procedures, if required
PC20. log any maintenance activity undertaken
PC1. obtain the work schedule, daily targets and priorities (if any) from the supervisor.
PC2. obtain the list of goods to be put away or picked along with the quantities and their
respective locations.
PC3. check with the supervisor the assistance required for other activities such as daily stock
counting, quality inspection etc.
PC4. plan the sequence in which the operation would be carried out so as to optimize time and
travel distance
PC5. inspect if the battery/fuel levels of the MHE is adequate for operation before moving it from
the dock
PC6. perform basic check of the vehicle condition as per the Preventive Maintenance checklist
before starting the work
PC7. Collect the necessary PPE, inspect its fitness and wear throughout the work schedule
PC8. identify goods to be moved and their location in terms of aisle number, rack number and bin
number from the putaway list during receiving and dispatch
Knowledge and Understanding (KU)
The individual on the job needs to know and understand:
KU1. types of documentation used in organization and importance of the same
KU2. risk and impact of not following defined procedures/work instructions
KU3. records to be maintained and implications of non-maintenance of the same
KU4. knowledge of security procedures e.g. secure storage of inventory
KU5. rules and regulations of shop floor as per SOP
KU6. risk and impact of not following safety procedures
KU7. escalation matrix for reporting identified problems
KU8. cost of equipment and loss for the company that results from damage of equipment
KU9. implications of delays in process to the company
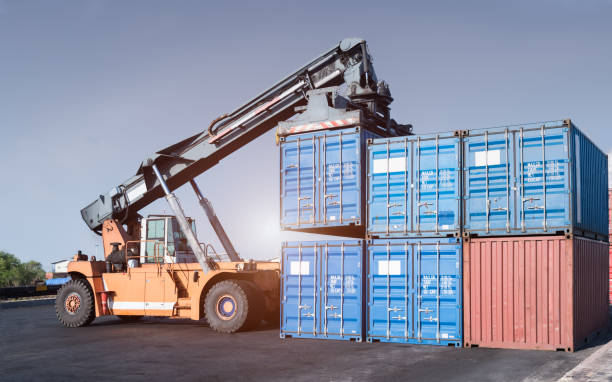
KU10. controls and switches used to operate the MHE properly
KU11. basic technicalities associated with the MHE
KU12. road signs, factory signs and other safety and emergency signals
KU13. hazardous labels for the supplies being used
KU14. correct maintenance procedures for MHE
KU15. response to emergencies e.g. fire
KU16. safety regulations while operating the MHE
KU17. optimal working condition of MHE and their components.
KU18. optimal levels of fluids and lubricants and greasing
KU19. MHE components and their functions
KU20. how to handle MHE such as forklifts, pallet trucks, cages and lifts.
KU21. how to test and safely carry out maintenance tasks on the MHE.
KU22. how to identify deviations from normal operations, diagnose and repair MHE
Generic Skills (GS)
User/individual on the job needs to know how to:
GS1. Labels and codes as per company procedures
GS2. handling instructions/company log books and records
GS3. safety manuals and safety signs on the warehouse floor
GS4. fill out checklists, maintenance logbooks detailing maintenance activities conducted
GS5. prepare detailed technical reports
GS6. note down condition of MHE and any maintenance or repair that was carried out on a daily
basis.
GS7. fill out any complaint/ insurance related forms for damaged goods
GS8. communicate clearly with supervisors and peers
GS9. regularly communicate with all employees in the chain of activities on the shop floor to
ensure activities are running smoothly
GS10. provide advice and guidance to peers and juniors
GS11. decide if a certain MHE is the best fit for the identified use
GS12. make judgment as to whether the MHE are in good condition or not.
GS13. adjust according to volume, capacity and manpower needs during peak and non-peak hours
GS14. prioritize and execute tasks within the scheduled time limits
GS15. maintain schedules and punctuality
GS16. avoid absenteeism
GS17. be a team player and achieve joint goals.
GS18. adhere to the timelines and ensure that they are met
GS19. handle the shipments with proper care so as to avoid damage while transportation
GS20. suggest ways to handle difficult material handling situations that require complex situations
GS21. resolve basic technical issues with the equipment through preventive and basic maintenance
GS22. suggest methods to streamline the maintenance process.
GS23. assess the condition of each MHE
GS24. concentrate at the task at hand and complete it without errors
Perform preventive and breakdown maintenance checks
Description
This unit is about performing preventive and breakdown maintenance checks of MHE
Scope
This unit/task covers the following:
Carry out preventive maintenance
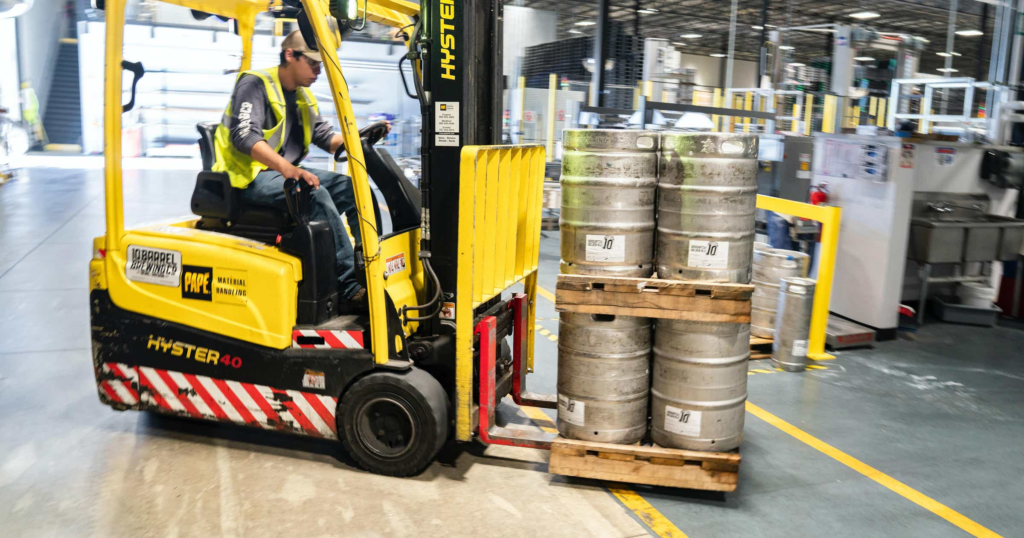
Carry out first-line repair and maintenance
Report maintenance activities Range: Personal protective equipment (PPEs), forklift, reach stacker,
reach truck, battery operated pallet truck, pallet jacks, hand trucks, order picker, tools and tackles,
maintenance kit etc.
Elements and Performance Criteria
Perform preventive and first line maintenance check
To be competent, the user/individual on the job must be able to:
PC1. collect the preventive maintenance checklist and maintenance log book for the MHE
concerned
PC2. collect necessary tools and PPE necessary for conducting the preventive maintenance
PC3. understand the complaints noted in the log book, if any
PC4. observe the overall functioning of the MHE to identify problems if any
PC5. adjust in settings or operating parameters if required
PC6. check for damage in tyres, parking break, main horn, reverse horn, warning lamp, etc.
PC7. check fluid levels of engine, transmission, differential, hydraulic, radiator coolant and brake
oil and top up any fluids as required
PC8. assess the MHE and escalate to supervisor if there is a likelihood of future problems or
replacement is required.
PC9. identify any parts that have worn out or nearing their end of life cycle as specified by the
manufacturer and put in request to obtain the required parts from the store (if available) or
inform inventory clerk to place orders.
PC10. make replacement of part and test for its safety and smooth operation
PC11. in case of a machine overhaul, plan well in advance and perform it during holidays or nonpeak hours.
PC12. test the MHE to ensure that it is fully functional and safe for use.
PC13. regularly maintain spare batteries and ensure they are fully charged
PC14. prepare and update maintenance card for every MHE
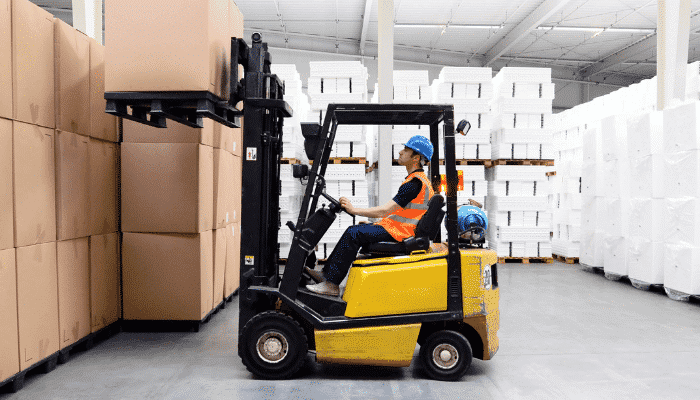
PC15. understand the type of breakdown reported/ witnessed during operation
PC16. identify and examine MHE to determine the source of the problem
PC17. determine if the problem could be resolved using existing skills or if it requires the attention
of a specialized technician from the manufacturing company
PC18. if the problem could be resolved, determine whether the part could be repaired and carry out
repairs using available spare parts/ machine shop equipment, or else put in part replacement
request
PC19. receive required parts and change the parts as per manufacturer’s guidelines.
PC20. complete and check all the line items in the first-line maintenance checklist
PC21. post first line repair, test the MHE to ensure that it is fully functional and safe for use
PC22. escalate to supervisor in case of delays or if a specialized technician from the manufacturing
company is required to solve the problem
PC23. report to supervisor for replacement of MHE parts
PC24. provide daily report to manager regarding condition of equipment, damage if any, etc.
PC25. update MHE condition in the appropriate health card and the next review dates in the
maintenance schedules
PC26. prepare a detailed report explaining the cause for the problem, solution, expected lifespan
and suggested replacement dates
Knowledge and Understanding (KU)
The individual on the job needs to know and understand:
KU1. organizational procedures
KU2. occupational health and safety standards
KU3. procedures for dealing with loss or damage to goods
KU4. value of items handled and implications of damage/loss of the same
KU5. organisation structure of the company
KU6. risk and impact of not following defined work, safety and security procedures
KU7. chain of command for reporting problems and status of work
KU8. types of documentation used in organization
KU9. records to be maintained and implications of non-maintenance of the same
KU10. security procedures e.g. secure storage of inventory
KU11. Rules and regulations of shop floor as per companys standard operating procedure (SOP)
KU12. risk and impact of not following safety procedures
KU13. escalation matrix for reporting identified problems
KU14. cost of equipment and loss for the company that results from damage of equipment
KU15. controls and switches used to operate MHE
KU16. basic technicalities associated with the MHE
KU17. road signs, factory signs and other safety and emergency signals
KU18. hazardous labels for the supplies being used.
KU19. correct maintenance procedures for MHE
KU20. response to emergencies e.g. fire
KU21. safety regulations while operating the MHE
KU22. optimal levels of fluids and lubricants.
KU23. MHE Components and particular areas that require greasing.
KU24. all the MHE components and their functions
KU25. to test and safely carry out maintenance tasks on the MHE.
KU26. to identify deviations from normal operations, diagnose and repair MHE
Generic Skills (GS)
User/individual on the job needs to know how to:
GS1. labels to identify product and its associated hazard.
GS2. instructions from checklists /company log books and records
GS3. safety manuals and safety signs on the warehouse floor
GS4. fill out checklists, maintenance logbooks detailing maintenance activities conducted
GS5. prepare detailed technical reports
GS6. communicate clearly with supervisors and peers
GS7. regularly communicate with all employees in the chain of activities on the shop floor to
ensure activities are running smoothly
GS8. provide advice and guidance to peers and juniors
GS9. make a judgment as to whether the MHE are in good condition or not
GS10. make judgment if a certain task can be best performed by the selected MHE
GS11. decide if the MHE requires any additional servicing by company technicians
GS12. decide if there is a requirement for change of parts
GS13. decide if the MHE can be put back into use or not
GS14. prioritize and execute tasks within the scheduled time limits
GS15. maintain schedules and punctuality
GS16. avoid absenteeism
GS17. look on internal customer requirements and ensure that they are met
GS18. understand the urgency and priority maintenance requests and accordingly take action
GS19. resolve basic problems of MHE based on preventive and basic maintenance
GS20. analyze and identify the estimated future life for the MHE
GS21. analyze and estimate if the problem would be recurring and estimated costs for repair in
future
GS22. assess the condition of each MHE
GS23. concentrate on task at hand and complete it without errors
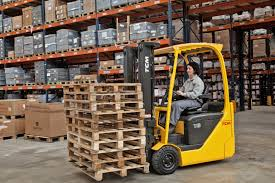
Maintain integrity and ethics in operations
Description
This unit is about maintaining integrity, ensuring data security, and professional and ethical practices
Scope
This unit/task covers the following:
Maintain integrity and ensure data security
Professional and ethical practices
Ensure regulatory compliance Range: Standard Operating Procedures (SOP), worksheets, computer,
projector, whiteboard and markets.
Elements and Performance Criteria
Maintain integrity and ethics in operation
To be competent, the user/individual on the job must be able to:
PC1. refrain from indulging in corrupt practices.
PC2. avoid using company funds, property or resources for undertaking personal activities
PC3. protect customers information and ensure it is not misused
PC4. protect data and information related to business or commercial decisions
PC5. avoid acceptance of cash or kind from vendors for support or contract negotiations
PC6. demonstrate and practice ethics in day-to-day processes and dealings with customers and
colleagues
PC7. avoid nepotism
PC8. consult supervisor or senior management when in situations that may require differentiating
between ethical and unethical
PC9. report promptly all violations of code of ethics
PC10. dress up and conduct in a professional manner
PC11. communicate with clients and stakeholders in a soft and polite manner
PC12. follow etiquettes in accordance to the place
PC13. check for regulatory documentation and compliances for the shop floor as per information
from the supervisor
PC14. perform activities considering the regulatory requirements
PC15. use Personal Protective Equipment (PPEs) in accordance to regulatory requirements
PC16. identify the different types of dangerous goods and handling methodologies
PC17. follow the SOP for handling of different types of dangerous goods
PC18. consult supervisor or senior management when in situations that may require differentiating
between ethical and unethical
PC19. promptly report all regulatory violations
Knowledge and Understanding (KU)
The individual on the job needs to know and understand:
KU1. companys policies on use of language
KU2. companys Human Resources policies
KU3. companys code of ethics
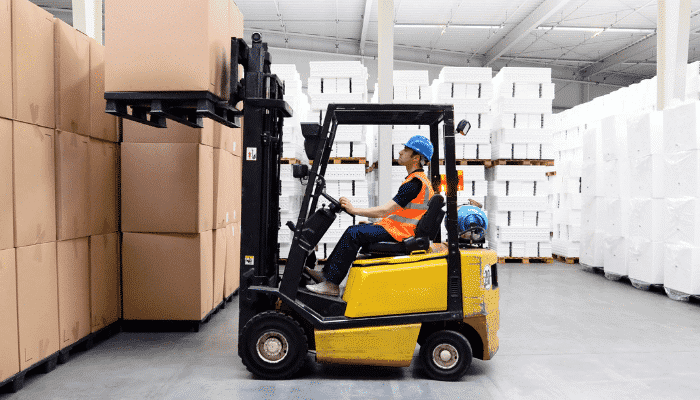
KU4. companys whistle blower policy
KU5. companys rules related to sexual harassment
KU6. companys reporting structure
KU7. companys documentation policy
KU8. principles of code of ethics and business ethics
KU9. various regulatory requirements
KU10. documentary compliance for various regulations
KU11. different dangerous shipment
KU12. regulations with regard to w.r.t dangerous shipment
Generic Skills (GS)
User/individual on the job needs to know how to:
GS1. company policy documents and work related documents
GS2. emails and written instructions
GS3. documentation pertaining to ethics and regulatory requirement
GS4. team members to work efficiently
GS5. peers and subordinates about information security and building trust
GS6. identify a shipment as dangerous goods
GS7. assess if the situation needs to be reported regarding regulations
GS8. plan and organise actions as per company guidelines
GS9. prevent company and customer information leakage
GS10. advisee colleagues regarding sensitive issues pertaining to conduct and regulations
GS11. provide professional services diligently and with integrity
GS12. avoid defaming company name by indulging into pilferage or fiddling with quality or
quantity of shipment
GS13. be fair and reasonable in profession and disclose conflict of interests
Follow health, safety and security procedures
Description
This unit is about ensuring compliance with health, safety and security procedures at the workplace
Scope
This unit/task covers the following:
Follow health, safety and security procedures
Ensure compliance to health, safety and securityRange: Personal Protective Equipment (PPE),
Material Handling Equipment (MHE), instructional material, alarms, safety guidelines, safety signs,
computer, projector etc
Elements and Performance Criteria
Follow health, safety and security procedures
To be competent, the user/individual on the job must be able to:
PC1. make note of all safety processes in different location (cargo loading area, ramp operation
area, etc.) with reference to area of operation
PC2. wear all PPE such as goggles, ear plugs, helmet, mask, shoes, etc. as applicable in the cargo
movement area
PC3. follow standard driving practice to ensure safety of life and material
PC4. follow organizational protocol to deploy action in case of signs of any emergency situation or
accident or breach of safety
PC5. undertake periodical preventive health check ups
PC6. follow necessary Standard Operating Procedure (SOP) and precautions while handling
dangerous and hazardous goods
PC7. follow security procedures like green gate in port, customs area, factory security, etc.
PC8. comply with data safety regulations of the organisation
PC9. follow standard safety procedures while handling hazardous / fragile cargo and walk only on
the designated pathway
Ensure compliance to health, safety and security
To be competent, the user/individual on the job must be able to:
PC10. recognise unsafe conditions and safety practices at the workplace and report it to concerned
authority
PC11. nspect the activity area and equipment for appropriate and safe condition
PC12. check if stacking is done at defined height and is not on the walk way
PC13. check if walk way is free from grease/ oil
PC14. check if emergency fire alarms, water sprinklers and smoke detectors are installed at all
places
PC15. participate in fire drills
PC16. check if standard material handling procedure are being followed
PC17. check if hold ladders, platforms and hand rails to be in a sound and safe condition
PC18. check if all the safety and security related tags, labels and signage are placed in the cargo
PC19. check if loading instrument is certified and operational
PC20. implement 5S at workplace
PC21. check if cargo has passed security checks and report in case of any violation
Knowledge and Understanding (KU)
The individual on the job needs to know and understand:
KU1. health, safety and security policies and procedures
KU2. special instructions for hazardous cargo handling
KU3. defined standard operating procedures
KU4. risk and impact of not following defined procedures/work instructions with reference to
health, safety and security operations
KU5. escalation matrix for reporting identified problem
KU6. basics of Occupational Safety and Health Administration (OSHA)
KU7. 5S implementation and practice
KU8. necessary security procedures for airport, customs area, etc.
KU9. tools and equipment for material handling
KU10. standard material handling procedures while handling cargo
KU11. safety and security signage and their functions

KU12. different security tags, labels and signage
KU13. handling procedure for hazardous / fragile cargo
KU14. security procedures for dangerous / hazardous shipment
KU15. different PPE, their usage and purpose
KU16. safe driving techniques
Generic Skills (GS)
User/individual on the job needs to know how to:
GS1. SOPs and safety precautions for different ground operations and handling cargo
GS2. different documents related to security and movement of cargo
GS3. fill forms related to health, safety and security procedures
GS4. communicate clearly with colleagues regarding safety procedures
GS5. share experience and guide peers
GS6. decide how to avoid any damage / accident to personal health / cargo handled, whenever
required
GS7. act objectively, rather than impulsively or emotionally when faced with difficult/stressful or
emotional situations
GS8. plan clearance of cargo in manner that it does hamper the safety of the cargo and the
loader/unloader
GS9. prioritize and execute tasks within the schedule time limits
GS10. plan and drive based on traffic and road condition using radio links/navigation aids wherever
available
GS11. ensure safe and secure movement of shipments, cargos etc.
GS12. identify any threats on personal health, safety, security, etc. and take appropriate actions
GS13. identify risks at the workplace and address them
GS14. analyse past mistakes and address them to avoid mishap in the future
GS15. check that right safety measures and procedures are in place
Employability Skills (60 Hours)
Description
This unit is about employability skills, Constitutional values, becoming a professional in the 21st Century,
digital, financial, and legal literacy, diversity and Inclusion, English and communication skills, customer
service, entrepreneurship, and apprenticeship, getting ready for jobs and career development.
Scope
The scope covers the following :
Introduction to Employability Skills
Constitutional values – Citizenship
Becoming a Professional in the 21st Century
Basic English Skills
Career Development & Goal Setting
Communication Skills
Diversity & Inclusion
Financial and Legal Literacy
Essential Digital Skills
Entrepreneurship
Customer Service
Getting ready for Apprenticeship & Jobs
Elements and Performance Criteria
Introduction to Employability Skills
To be competent, the user/individual on the job must be able to:
PC1. identify employability skills required for jobs in various industries
PC2. identify and explore learning and employability portals
Constitutional values – Citizenship
To be competent, the user/individual on the job must be able to:
PC3. recognize the significance of constitutional values, including civic rights and duties,
citizenship, responsibility towards society etc. and personal values and ethics such as
honesty, integrity, caring and respecting others, etc.
PC4. follow environmentally sustainable practices
Becoming a Professional in the 21st Century
To be competent, the user/individual on the job must be able to:
PC5. recognize the significance of 21st Century Skills for employment
PC6. practice the 21st Century Skills such as Self-Awareness, Behaviour Skills, time management,
critical and adaptive thinking, problem-solving, creative thinking, social and cultural
awareness, emotional awareness, learning to learn for continuous learning etc. in personal
and professional life
Basic English Skills
To be competent, the user/individual on the job must be able to:
PC7. use basic English for everyday conversation in different contexts, in person and over the
telephone
PC8. read and understand routine information, notes, instructions, mails, letters etc. written in
English
PC9. write short messages, notes, letters, e-mails etc. in English
Career Development & Goal Setting
To be competent, the user/individual on the job must be able to:
PC10. understand the difference between job and career
PC11. prepare a career development plan with short- and long-term goals, based on aptitude
Communication Skills
To be competent, the user/individual on the job must be able to:
PC12. follow verbal and non-verbal communication etiquette and active listening techniques in
various settings
PC13. work collaboratively with others in a team
Diversity & Inclusion
To be competent, the user/individual on the job must be able to:
PC14. communicate and behave appropriately with all genders and PwD
PC15. escalate any issues related to sexual harassment at workplace according to POSH Act
Financial and Legal Literacy
To be competent, the user/individual on the job must be able to:
PC16. select financial institutions, products and services as per requirement
PC17. carry out offline and online financial transactions, safely and securely
PC18. identify common components of salary and compute income, expenses, taxes, investments
etc
PC19. identify relevant rights and laws and use legal aids to fight against legal exploitation
Essential Digital Skills
To be competent, the user/individual on the job must be able to:
PC20. operate digital devices and carry out basic internet operations securely and safely
PC21. use e- mail and social media platforms and virtual collaboration tools to work effectively
PC22. use basic features of word processor, spreadsheets, and presentations
Entrepreneurship
To be competent, the user/individual on the job must be able to:
PC23. identify different types of Entrepreneurship and Enterprises and assess opportunities for
potential business through research
PC24. develop a business plan and a work model, considering the 4Ps of Marketing Product, Price,
Place and Promotion
PC25. identify sources of funding, anticipate, and mitigate any financial/ legal hurdles for the
potential business opportunity
Customer Service
To be competent, the user/individual on the job must be able to:
PC26. identify different types of customers
PC27. identify and respond to customer requests and needs in a professional manner.
PC28. follow appropriate hygiene and grooming standards
Getting ready for apprenticeship & Jobs
To be competent, the user/individual on the job must be able to:
PC29. create a professional Curriculum vitae (Résumé)
PC30. search for suitable jobs using reliable offline and online sources such as Employment
exchange, recruitment agencies, newspapers etc. and job portals, respectively
PC31. apply to identified job openings using offline /online methods as per requirement
PC32. answer questions politely, with clarity and confidence, during recruitment and selection
PC33. identify apprenticeship opportunities and register for it as per guidelines and requirements
Knowledge and Understanding (KU)
The individual on the job needs to know and understand:
KU1. need for employability skills and different learning and employability related portals
KU2. various constitutional and personal values
KU3. different environmentally sustainable practices and their importance
KU4. Twenty first (21st) century skills and their importance
KU5. how to use English language for effective verbal (face to face and telephonic) and written
communication in formal and informal set up
KU6. importance of career development and setting long- and short-term goals
KU7. about effective communication
KU8. POSH Act
KU9. Gender sensitivity and inclusivity
KU10. different types of financial institutes, products, and services
KU11. how to compute income and expenditure
KU12. importance of maintaining safety and security in offline and online financial transactions
KU13. different legal rights and laws
KU14. different types of digital devices and the procedure to operate them safely and securely
KU15. how to create and operate an e- mail account and use applications such as word processors,
spreadsheets etc.
KU16. how to identify business opportunities
KU17. types and needs of customers
KU18. how to apply for a job and prepare for an interview
KU19. apprenticeship scheme and the process of registering on apprenticeship portal
Generic Skills (GS)
User/individual on the job needs to know how to:
GS1. read and write different types of documents/instructions/correspondence
GS2. communicate effectively using appropriate language in formal and informal settings
GS3. behave politely and appropriately with all
GS4. how to work in a virtual mode
GS5. perform calculations efficiently
GS6. solve problems effectively
GS7. pay attention to details
GS8. manage time efficiently
GS9. maintain hygiene and sanitization to avoid infection