Loader/Unloader (1 years diploma)
Loader/Unloader click here
Brief Job Description
Loader/ Unloader in the Logistics industry is also known as Loader, Transport Associate. Individuals in this
role need to identify goods based on the product code, unload them from the truck onto the inbound area and move them to the staging area. A similar sequence is done for loading. Their responsibilities include identifying damaged goods and moving goods safely.

Personal Attributes
This job requires the individual to concentrate on the job at hand and complete it without any errors. The
individual should also be skilled in identifying goods based on their labels and in arranging goods in the
truck. The individual must be able to follow instructions provided by supervisor.
Preparing to unload
Description
This OS unit is about preparing to unload inbound items.
Elements and Performance Criteria
Obtaining information required for unloading
To be competent, the user/individual on the job must be able to:
PC1. obtain count sheet of inbound items from supervisor
PC2. understand the daily schedule, number of trucks to be unloaded and unloading targets from
the supervisor.
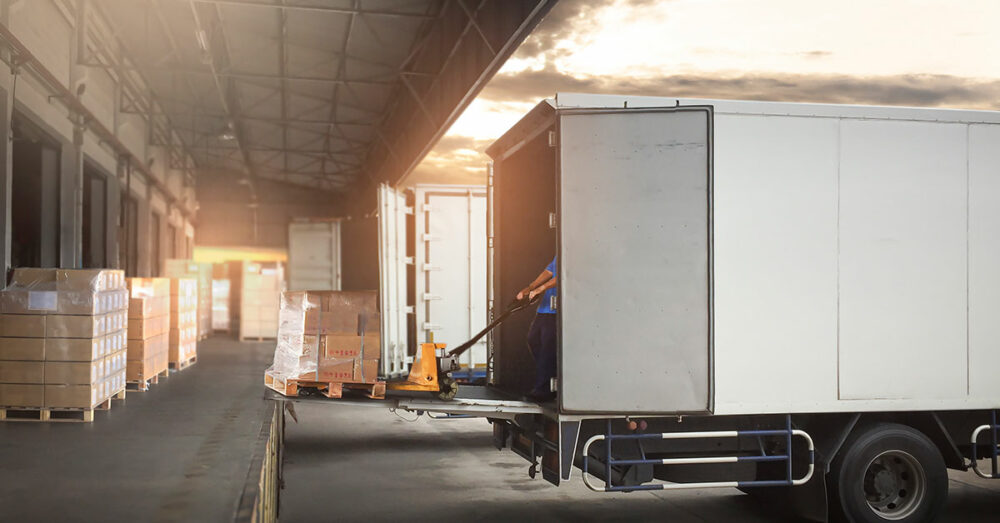
PC3. find out when the trucks are expected to come in.
PC4. determine which gate or dock the required truck to unload from is to be parked at
Gather required equipment, make space for unloading, inspection.
To be competent, the user/individual on the job must be able to:
PC5. assess Material Handling Equipment (MHE) needed for unloading
PC6. assess Personal Protective Equipment (PPE) required based on the goods being unloaded and
the environment
PC7. collect and wear all the necessary PPE
PC8. move any remaining inbound items into the staging area to make space for incoming
shipment in the inbound area.
PC9. move aside any goods yet to be loaded to make space for incoming goods in the inbound
area
PC10. get any MHE required for unloading and keep it ready
PC11. perform a basic safety inspection of areas and MHE
PC12. ensure that the staging and inbound areas are clean. clean up any spills or breakages
Knowledge and Understanding (KU)
The individual on the job needs to know and understand:
KU1. knowledge of organizational procedures
KU2. role and responsibilities of colleagues on the shop floor
KU3. procedures for dealing with loss or damage to goods
KU4. risk and impact of not following defined procedures/work instructions
KU5. nature and characteristics of goods being loaded
KU6. knowledge of client and products handled
KU7. knowledge of all relevant safety and security procedures
KU8. knowledge of transport logistics service providers used by the company
KU9. knowledge of entire shop floor activities and persons in charge of each function
KU10. knowledge of coding system followed to label goods.
KU11. knowledge of types of goods being handled
KU12. knowledge of loading methods that can be used for different types of goods
KU13. ability to read labels and understand special handling requirements of goods.
KU14. types of workplace hazards that one can encounter on the job and safe operating practices.
KU15. knowledge of MHE used to load larger and heavier items.
KU16. arranging goods to maximize truck space.
Generic Skills (GS)
User/individual on the job needs to know how to:
GS1. write down notes about goods unloaded, methods used and special handling characteristics.
GS2. ability to read and understand product labels
GS3. ability to read and understand what is required from count sheet.
GS4. ability to read instructions/training directions in english
GS5. communicate clearly in local language or english with supervisors and peers
GS6. provide advice and guidance to peers & juniors
GS7. communicate with team members for sharing work, delays in loading/unloading.
GS8. balance loading and unloading work
GS9. ability to prioritize and execute tasks in an efficient manner.
GS10. flexibility to stretch and meet unloading targets.
GS11. coordinate work with team and supervisor
GS12. understand the customer timelines and ensure that they are met.
GS13. rapid identification and rectification of errors
GS14. ability to identify type of equipment required for unloading and moving goods.
GS15. ability to identify and group items based on product code.
GS16. ability to cross check items against count sheet
GS17. ability to concentrate on task at hand and complete it without errors
Perform Unloading
Description
This OS unit is about performing unloading of inbound items.
Elements and Performance Criteria
Select, unload goods and segregate them.
To be competent, the user/individual on the job must be able to:
PC1. have the dispatcher check the driver’s papers to confirm it is the right truck to unload
PC2. read labels and identify goods in the truck based on product codes.
PC3. unload goods of the same category carefully onto inbound area
PC4. check the condition of goods unloaded.
PC5. keep damaged goods aside
Tally, verify and deliver goods
To be competent, the user/individual on the job must be able to:
PC6. tally segregated with the numbers of each item in the count sheet
PC7. have the goods unloaded verified and any forms required by driver to be filled out by
dispatcher
PC8. load goods onto MHE.
PC9. move goods into the staging area specified by supervisor
PC10. unload goods from the MHE onto the staging area.
PC11. keep similar goods together for easy GRN and put away.
Knowledge and Understanding (KU)
The individual on the job needs to know and understand:
KU1. knowledge of organizational procedures
KU2. role and responsibilities of colleagues on the shop floor
KU3. procedures for dealing with loss or damage to goods
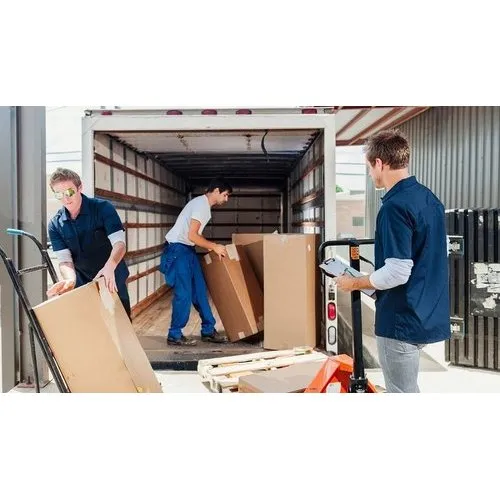
KU4. risk and impact of not following defined procedures/work instructions
KU5. nature and characteristics of goods being loaded
KU6. knowledge of client and products handled
KU7. knowledge of all relevant safety and security procedures
KU8. knowledge of transport logistics service providers used by the company
KU9. knowledge of entire shop floor activities and persons in charge of each function
KU10. knowledge of coding system followed to label goods.
KU11. knowledge of types of goods being handled
KU12. knowledge of loading methods that can be used for different types of goods
KU13. ability to read labels and understand special handling requirements of goods.
KU14. types of workplace hazards that one can encounter on the job and safe operating practices
KU15. MHE used to load larger and heavier items
KU16. arranging goods to maximize truck space.
Generic Skills (GS)
User/individual on the job needs to know how to:
GS1. write down notes about goods unloaded, methods used and special handling characteristics.
GS2. ability to read and understand product labels.
GS3. ability to read and understand what is required from count sheet.
GS4. ability to read instructions/training directions in english.
GS5. communicate clearly in local language or english with supervisors and peers.
GS6. provide advice and guidance to peers & juniors.
GS7. communicate with team members for sharing work, delays in loading/unloading
GS8. balance loading and unloading work
GS9. ability to prioritize and execute tasks in an efficient manner.
GS10. flexibility to stretch and meet unloading targets.
GS11. coordinate work with team and supervisor
GS12. understand the customer timelines and ensure that they are met.
GS13. rapid identification and rectification of errors.
GS14. ability to identify type of equipment required for unloading and moving goods.
GS15. ability to identify and group items based on product code.
GS16. ability to cross check items against count sheet
GS17. ability to concentrate on task at hand and complete it without errors
Perform Post unloading activities
Description
This OS unit is about post unloading activities for inbound items
Elements and Performance Criteria
Carrying out Housekeeping
To be competent, the user/individual on the job must be able to:
PC1. move all the damaged goods to the quarantine area.
PC2. perform a quick safety inspection of the staging and inbound areas
PC3. clean up any spillage to ensure that the staging and inbound areas are clean
PC4. return any PPE used to the storage rack
PC5. store any MHE used in storage area.
Reporting to Management
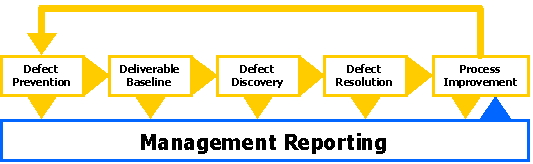
To be competent, the user/individual on the job must be able to:
PC6. notify supervisor on the number of quarantined items and the number of replacement items
required.
PC7. report on the condition of PPE and MHE
PC8. provide feedback regarding damage if any, delays in inbound, orders which hadn’t arrived, etc
PC9. complete any forms as required by management
Knowledge and Understanding (KU)
The individual on the job needs to know and understand:
KU1. knowledge of organizational procedures
KU2. role and responsibilities of colleagues on the shop floor
KU3. procedures for dealing with loss or damage to goods
KU4. risk and impact of not following defined procedures/work instructions
KU5. nature and characteristics of goods being loaded
KU6. knowledge of client and products handled
KU7. knowledge of all relevant safety and security procedures
KU8. knowledge of transport logistics service providers used by the company
KU9. knowledge of entire shop floor activities and persons in charge of each function
KU10. knowledge of coding system followed to label goods
KU11. knowledge of types of goods being handled
KU12. knowledge of loading methods that can be used for different types of goods
KU13. ability to read labels and understand special handling requirements of goods
KU14. types of workplace hazards that one can encounter on the job and safe operating practices
KU15. MHE used to load larger and heavier items
KU16. arranging goods to maximize truck space.
Generic Skills (GS)
User/individual on the job needs to know how to:
GS1. write down notes about goods unloaded, methods used and special handling characteristics
GS2. ability to read and understand product labels
GS3. ability to read and understand what is required from the count sheet
GS4. ability to read instructions/training directions in English.
GS5. communicate clearly in local language or English with supervisors and peers
GS6. provide advice and guidance to peers & juniors
GS7. communicate with team members for sharing work, delays in loading/unloading
GS8. balance loading and unloading work
GS9. ability to prioritize and execute tasks in an efficient manner.
GS10. flexibility to stretch and meet unloading targets.
GS11. coordinate work with team and supervisor.
GS12. understand the customer timelines and ensure that they are met
GS13. rapid identification and rectification of errors.
GS14. ability to identify type of equipment required for unloading and moving goods.
GS15. ability to identify and group items based on product code.
GS16. ability to cross check items against count sheet.
GS17. ability to concentrate on task at hand and complete it without errors
Preparing to load
Description
This OS unit is about preparing to load outbound items.
Elements and Performance Criteria
Obtain information required for loading
To be competent, the user/individual on the job must be able to:
PC1. obtain pick list and order sheet for outbound items from supervisor.
PC2. understand the schedule and number of trucks to be loaded and loading targets from the
supervisor.
PC3. find out when the trucks are expected to come in.
PC4. determine which gate or dock the required truck to load into is parked at.
Gather equipment, make space for loading, inspection.
To be competent, the user/individual on the job must be able to:
PC5. assess Material Handling Equipment (MHE) needed for loading
PC6. assess Personal Protective Equipment (PPE) required based on the goods being loaded and
the environment.
PC7. collect and wear all the necessary PPE
PC8. complete loading of any goods remaining in the outbound area.
PC9. move any delayed goods aside to make space for outgoing goods.
PC10. get any MHE required for loading and keep it ready.
PC11. perform a basic safety inspection of the areas and loading equipment
PC12. ensure that the staging and outbound areas are clean. clean up any spills or breakages.
Knowledge and Understanding (KU)
The individual on the job needs to know and understand:
KU1. knowledge of organizational procedures
KU2. role and responsibilities of colleagues on the shop floor
KU3. procedures for dealing with loss or damage to goods
KU4. risk and impact of not following defined procedures/work instructions
KU5. nature and characteristics of goods being loaded
KU6. knowledge of client and products handled
KU7. knowledge of all relevant safety and security procedures
KU8. knowledge of transport logistics service providers used by the company.
KU9. knowledge of entire shop floor activities and persons in charge of each function
KU10. knowledge of coding system followed to label goods
KU11. knowledge of types of goods being handled
KU12. knowledge of loading methods that can be used for different types of goods
KU13. ability to read labels and understand special handling requirements of goods
KU14. types of workplace hazards that one can encounter on the job and safe operating practices
KU15. MHE used to load larger and heavier items
KU16. arranging goods to maximize truck space.
Generic Skills (GS)
User/individual on the job needs to know how to:
GS1. write down notes about goods loaded, methods used and special handling characteristics
GS2. ability to read and understand product labels
GS3. ability to read and understand what is required from the pick list and order sheet
GS4. ability to read instructions/training directions in english
GS5. communicate clearly in local language or english with supervisors and peers
GS6. provide advice and guidance to peers & juniors
GS7. communicate with team members for sharing work, delays in loading/unloading.
GS8. balance loading and unloading work
GS9. ability to prioritize and execute tasks in an efficient manner.
GS10. flexibility to stretch and meet unloading targets.
GS11. coordinate work with team and supervisor.
GS12. understand the customer timelines and ensure that they are met
GS13. rapid identification and rectification of errors.
GS14. ability to identify type of equipment required for unloading and moving goods.
GS15. ability to identify and group items based on product code.
GS16. ability to cross check items against count sheet.
GS17. ability to concentrate on task at hand and complete it without errors
Moving Goods
Description
This OS unit is about inspecting, grouping, verifying and loading outbound items.
Elements and Performance Criteria
Perform primary inspection
To be competent, the user/individual on the job must be able to:
PC1. check the condition of goods and tally items present with the numbers of each item in the
pick list.
PC2. report to supervisor on damages, excess or shortage of required numbers.
PC3. receive replacement or missing goods and keep extra goods aside.
Group, Move and verify Items
To be competent, the user/individual on the job must be able to:
PC4. group items into orders based on order sheet
PC5. get supervisor’s sign off on quantity and condition to move goods
PC6. load items onto MHE.
PC7. move goods from staging area to outbound area near the truck.
PC8. unload goods from MHE.
PC9. have goods verified by dispatcher.
PC10. have the driver’s papers checked by the dispatcher and confirm that it is the right truck to
load into.
Sort, load truck, arrange and perform final count
To be competent, the user/individual on the job must be able to:
PC11. sort all items based on size of packing case.
PC12. load goods into truck as per the shift schedule specified by management.
PC13. arrange goods in the truck to maximize truck space
PC14. perform final count with driver and get his signature, acknowledging receipt of goods.
Knowledge and Understanding (KU)
The individual on the job needs to know and understand:
KU1. knowledge of organizational procedures
KU2. role and responsibilities of colleagues on the shop floor
KU3. procedures for dealing with loss or damage to goods
KU4. risk and impact of not following defined procedures/work instructions
KU5. nature and characteristics of goods being loaded
KU6. knowledge of client and products handled
KU7. knowledge of all relevant safety and security procedures
KU8. knowledge of transport logistics service providers used by the company
KU9. knowledge of entire shop floor activities and persons in charge of each function
KU10. knowledge of coding system followed to label goods.
KU11. knowledge of types of goods being handled
KU12. knowledge of loading methods that can be used for different types of goods
KU13. ability to read labels and understand special handling requirements of goods.
KU14. types of workplace hazards that one can encounter on the job and safe operating practices.
KU15. MHE used to load larger and heavier items
KU16. arranging goods to maximize truck space.
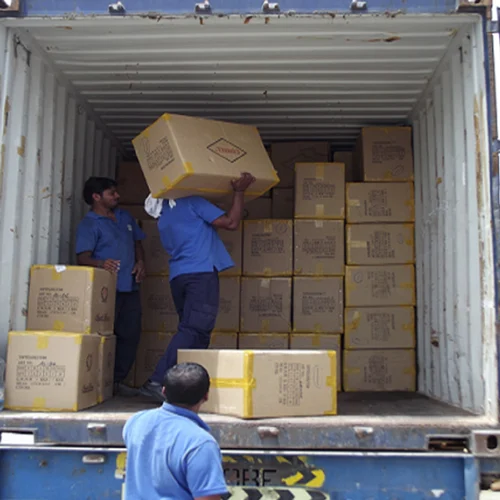
Generic Skills (GS)
User/individual on the job needs to know how to:
GS1. write down notes about goods loaded, methods used and special handling characteristics
GS2. ability to read and understand product labels
GS3. ability to read and understand what is required from pick list and order sheet
GS4. ability to read instructions/training directions in english
GS5. communicate clearly in local language or english with supervisors and peers
GS6. provide advice and guidance to peers & juniors
GS7. communicate with team members for sharing work, delays in loading/unloading
GS8. balance loading and unloading work
GS9. ability to prioritize and execute tasks in an efficient manner.
GS10. flexibility to stretch and meet unloading targets.
GS11. coordinate work with team and supervisor.
GS12. understand the customer timelines and ensure that they are met
GS13. rapid identification and rectification of errors.
GS14. ability to identify type of equipment required for unloading and moving goods.
GS15. ability to identify and group items based on product code.
GS16. ability to cross check items against count sheet.
GS17. ability to concentrate on task at hand and complete it without errors
Perform Post loading activities
Description
This OS unit is about post loading activities for outbound items.
Elements and Performance Criteria
Carrying out Housekeeping
To be competent, the user/individual on the job must be able to:
PC1. move items to quarantine area or staging area based on condition of remaining goods
PC2. perform a quick safety inspection of the staging and outbound areas
PC3. clean up any spillage or breakage to ensure staging and outbound areas are clean
PC4. return any PPE used to the storage rack.
PC5. store any MHE used in storage area.
Reporting to management
To be competent, the user/individual on the job must be able to:
PC6. notify supervisor on the number of quarantined items and the number of replacement items
required.
PC7. provide feedback regarding damage if any, delays in outbound, inability to meet an order, etc.
PC8. complete any forms as required by management.
PC9. report on the condition of PPE and MHE
Knowledge and Understanding (KU)
The individual on the job needs to know and understand:
KU1. knowledge of organizational procedures
KU2. role and responsibilities of colleagues on the shop floor
KU3. procedures for dealing with loss or damage to goods
KU4. risk and impact of not following defined procedures/work instructions
KU5. nature and characteristics of goods being loaded
KU6. knowledge of client and products handled
KU7. knowledge of all relevant safety and security procedures
KU8. knowledge of transport logistics service providers used by the company
KU9. knowledge of entire shop floor activities and persons in charge of each function
KU10. knowledge of coding system followed to label goods.
KU11. knowledge of types of goods being handled including weight limits, truck capacit
KU12. knowledge of loading methods that can be used for different types of goods
KU13. ability to read labels and understand special handling requirements of goods.
KU14. types of workplace hazards that one can encounter on the job and safe operating practices
KU15. MHE used to load larger and heavier items.
KU16. arranging goods to maximize truck space
KU17. knowledge of products and labels for different types of products
Generic Skills (GS)
User/individual on the job needs to know how to:
GS1. write down notes about goods loaded, methods used and special handling characteristics.
GS2. ability to read and understand product labels
GS3. ability to read and understand what is required from pick list and order sheet
GS4. ability to read instructions/training directions in english
GS5. communicate clearly in local language or english with supervisors and peers
GS6. provide advice and guidance to peers & juniors
GS7. communicate with team members for sharing work, delays in loading/unloading
GS8. balance loading and unloading work
GS9. ability to prioritize and execute tasks in an efficient manner.
GS10. flexibility to stretch and meet unloading targets.
GS11. coordinate work with team and supervisor.
GS12. understand the customer timelines and ensure that they are met
GS13. rapid identification and rectification of errors.
GS14. ability to identify type of equipment required for unloading and moving goods.
GS15. ability to identify and group items based on product code.
GS16. ability to cross check items against count sheet.
GS17. ability to concentrate on task at hand and complete it without errors
GS18. Ability to crosscheck items loaded against order sheet
GS19. Ability to concentrate on task at hand and complete it without errors
Employability Skills (30 Hours)
Description
This unit is about employability skills, Constitutional values, becoming a professional in the 21st Century,
digital, financial, and legal literacy, diversity and Inclusion, English and communication skills, customer
service, entrepreneurship, and apprenticeship, getting ready for jobs and career development.
Scope
The scope covers the following :
Introduction to Employability Skills
Constitutional values – Citizenship
Becoming a Professional in the 21st Century
Basic English Skills
Communication Skills
Diversity & Inclusion
Financial and Legal Literacy
Essential Digital Skills
Entrepreneurship
Customer Service
Getting ready for Apprenticeship & Jobs
Elements and Performance Criteria
Introduction to Employability Skills
To be competent, the user/individual on the job must be able to:
PC1. understand the significance of employability skills in meeting the job requirements
Constitutional values – Citizenship
To be competent, the user/individual on the job must be able to:
PC2. identify constitutional values, civic rights, duties, personal values and ethics and
environmentally sustainable practices
Becoming a Professional in the 21st Century
To be competent, the user/individual on the job must be able to:
PC3. explain 21st Century Skills such as Self-Awareness, Behavior Skills, Positive attitude, selfmotivation, problem-solving, creative thinking, time management, social and cultural
awareness, emotional awareness, continuous learning mindset etc.
Basic English Skills
To be competent, the user/individual on the job must be able to:
PC4. speak with others using some basic English phrases or sentences
Communication Skills
To be competent, the user/individual on the job must be able to:
PC5. follow good manners while communicating with others
PC6. work with others in a team
To be competent, the user/individual on the job must be able to:
PC7. communicate and behave appropriately with all genders and PwD
PC8. report any issues related to sexual harassment
Financial and Legal Literacy
To be competent, the user/individual on the job must be able to:
PC9. use various financial products and services safely and securely
PC10. calculate income, expenses, savings etc.
PC11. approach the concerned authorities for any exploitation as per legal rights and laws
Essential Digital Skills
To be competent, the user/individual on the job must be able to:
PC12. operate digital devices and use its features and applications securely and safely
PC13. use internet and social media platforms securely and safely
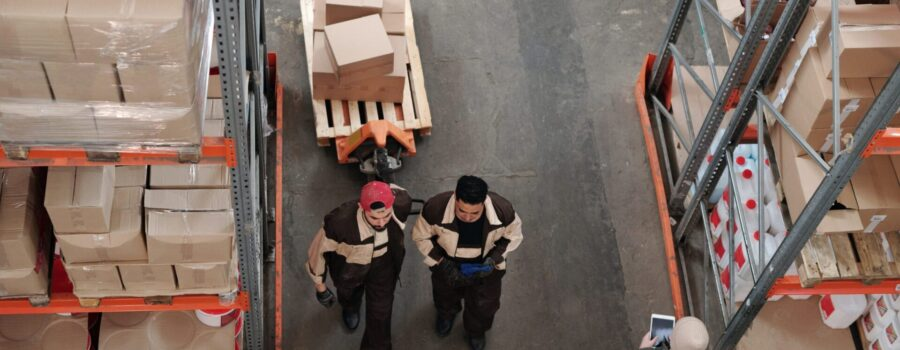
Entrepreneurship
To be competent, the user/individual on the job must be able to:
PC14. identify and assess opportunities for potential business
PC15. identify sources for arranging money and associated financial and legal challenges
Customer Service
To be competent, the user/individual on the job must be able to:
PC16. identify different types of customers
PC17. identify customer needs and address them appropriately
PC18. follow appropriate hygiene and grooming standards
Getting ready for apprenticeship & Jobs
To be competent, the user/individual on the job must be able to:
PC19. create a basic biodata
PC20. search for suitable jobs and apply
PC21. identify and register apprenticeship opportunities as per requirement
Knowledge and Understanding (KU)
The individual on the job needs to know and understand:
KU1. need for employability skills
KU2. various constitutional and personal values
KU3. different environmentally sustainable practices and their importance
KU4. Twenty first (21st) century skills and their importance
KU5. how to use basic spoken English language
KU6. Do and dont of effective communication
KU7. inclusivity and its importance
KU8. different types of disabilities and appropriate communication and behaviour towards PwD
KU9. different types of financial products and services
KU10. how to compute income and expenses
KU11. importance of maintaining safety and security in financial transactions
KU12. different legal rights and laws
KU13. how to operate digital devices and applications safely and securely
KU14. ways to identify business opportunities
KU15. types of customers and their needs
KU16. how to apply for a job and prepare for an interview
KU17. apprenticeship scheme and the process of registering on apprenticeship portal
Generic Skills (GS)
User/individual on the job needs to know how to:
GS1. communicate effectively using appropriate language
GS2. behave politely and appropriately with all
GS3. perform basic calculations
GS4. solve problems effectively
GS5. be careful and attentive at work
GS6. use time effectively
GS7. maintain hygiene and sanitisation to avoid infection